Introduction: 3D Printed Water Rocket Launcher (old)
August 2023 Update New, Updated Instructable Here!
The new version (v1.4) is simpler, universal, glue-less, pipe-optional, and has been known to make your breakfast and walk your dog. Well, maybe not the last part.
The below instructions reflect Version 1.2 from May 2022. Please see the updated instructions linked above.
This is a water rocket launcher system that is:
- Built from 3D printed parts, PVC pipe, and readily-available off-the-shelf components
- Easy for a novice to assemble and set-up, but is modular and expandable for advanced tinkering
- Portable
- Adaptable to parts found worldwide
- Low cost: Total cost per launcher < $5 USD
This project's goal is to make water rocket projects universally accessible. I welcome your help!
3D models live at Printables.
DESIGN CONCEPT
Launching a soda bottle requires water, pressurized air, and a triggering mechanism. 3D-printed parts can interface with cheap off-the-shelf parts to do this reliably and with a minimum of assembly complexity.
The assembly may look daunting at first, but almost all of it simply involves snapping together 3D printed parts. The hard work of holding high pressure is isolated to a Core assembly. Choose a configuration that matches your locally-available parts and design priorities and away you go!
To reduce clutter, additional instructions and design discussions are at https://www.marimolabs.com/water-rocket-launcher
SAFETY DISCLAIMER
Pressurized systems are inherently dangerous. No warranty, expressed or implied, is made regarding the safety, performance, or suitability of any designs, models, or analyses presented. I am not an expert and hold no formal qualifications in this field. Do not attempt without appropriate experience, protective equipment, and tools.
Updated to Version 1.21 on 18 May 2022
This project was designed with Fusion 360 by Autodesk using the free hobby license. Autodesk also owns/publishes Instructables ad-free. In our micro-commoditized world, I find these to be amazing investments in the Maker Movement. Thanks Autodesk!
Supplies
THE SIMPLE VERSION
This modular design has many combinations of parts for different regions, bottles, and assembly complexities. If you are looking for the very simplest version, and you live in North America, this is what you need to get started:
- Print: Base 21.4mm, Clamp 17h 33d x6, Collar Universal, Launch Pin Universal, Foot US x3, Peg US x3, Carrier 21.4mm, Core TypeB Universal.
- Obtain:
- Schedule 40 1/2"-nominal PVC pipe, 3 sections of equal length for legs, 6-8" long
- Rubber bands, any, but silicone #33 (3 1/2" x 1/8") are nice
- String to tie to Launch Pin
- TR414 Tire valve stem
- O-ring 15mm ID x 3.5mm thickness x 22mm OD
- Bike pump/car tire hose extension 15-20cm
- Reusable straw, 7.6-8mm OD
- Bike pump with Schrader valve (the wider one, found on mountain bikes)
- A soda or seltzer bottle
- 5 minutes to snap it all together with Steps 1, 2, and 5 below.
- Then go launch!
THE ADVANCED VERSION
If you want more options, see below to choose your Pipe Size, Cores, and Clamps.
A) PIPE SIZE
PVC pipe is used as Legs for the base (required) and for launch tubes that interface with the bottle (optional).
This launcher is currently compatible with these pipe sizes:
- North America: ASTM Schedule 40 1/2" nominal PVC pipe (OD 21.4mm, ID 15.6mm). Compatible with 3D models marked “US” or “21.4mm”, Cores Type A and C
- UK: 21.5mm overflow pipe (OD 21.5mm, ID 18.7-18.9mm). Compatible with "UK" and “21.4mm”
- Australia/New Zealand: AS/NZS 1477 DN15 PN18 PVC-U pipe (OD 21.1-21.5mm, ID 17.8mm). Compatible with "AUS-NZ" and “21.4mm”
B) CORE SELECTION
The launcher Base accepts different “Cores”, which are the central interface to the bottle. Type A and B are mature designs; other designs are in beta testing (see Step 7).
Core Type A: Strongest with the longest test record. Launch tube configuration, with stainless-steel bolt reinforcement; currently requires ASTM Schedule 40 1/2"-nominal PVC pipe and PVC cement. Takes a while to build.
Core Type B: Easiest to assemble and universally compatible as it needs no PVC pipe. Uses a “bottle stopper" configuration. No adhesives required.
C) CLAMP SELECTION
Clamps are available for different common bottle dimensions. Measure in millimeters the height from the opening of the bottle to the far-side of the flange (this is “height”, or “h”) and the flange diameter ("d"). Select your clamp accordingly.
- 15h 29to33d: For GME30.37 bottles common in UK/Europe
- 17h 33d: For PCO-1881 bottles common in the US
- 21h 33d: For PCO-1810 bottles common in many parts of the world including Australia/New Zealand
PRINTED PARTS LIST
Based on your configuration chosen above, make your Printed Part List. 3D models and print settings are available for free at Printables.com (https://www.printables.com/model/86434-water-rocket-launcher).
All launchers will need:
- Base 21.4mm
- Clamp x6: Choose based on your bottle. Holds bottle onto the Base.
- Collar (universal): Holds Clamps together until launch.
- Launch Pin (universal): Holds the Collar in place until launch.
- Foot x3: Foot for end of PVC pipe Legs that have a retaining ring for Pegs and a bevel to lock into the Base for transport. US, UK, and AUS/NZ versions available.
- Peg x3: Ground pegs to anchor the Launcher into grass. US, UK, and AUS/NZ versions available.
- Carrier 21.4mm
Print parts for your chosen Core:
- Type A: Core TypeA Center (note 100% infill with supports touching buildplate for only this part), Core TypeA Valve Retainer, Core TypeA Valve Backstop
- Type B: Core TypeB Universal
NON-PRINTED PARTS LIST
All launchers will need:
- PVC pipe sections, 15-20cm long, 3x, for Legs (see notes above on sizing)
- Rubber bands, any, but silicone #33 (3 1/2" x 1/8") are nice
- String to tie to Launch Pin; braided polyethylene 36″-long suggested
- Air pressure source with pressure gauge and Schrader valve (e.g. bike pump)
- Long extension hose with pressure release valve, 4-6 ft (suggested)
For Core Type A, you will need:
- TR414 Tire valve stem
- O-ring 15mm ID x 3.5mm thickness x 22mm OD
- ASTM Schedule 40 PVC pipe, 7.0cm (lower) and 15-20cm (upper)
- 1/4"-20 stainless steel hex-head bolt, 2.5" long
- 1/4"-20 stainless-steel nylon-inlay locknut
- Car tire hose extension 15-20cm, heavy duty (recommended). Recommend REMOVING the internal spring valve from the extension hose (allows for safer depressurizations on launch abort)
For Core Type B, you will need:
- TR414 Tire valve stem
- O-ring 15mm ID x 3.5mm thickness x 22mm OD
- Reusable straw, 7.6-8mm OD
- Car tire hose extension 15-20cm, heavy duty (required). Recommend REMOVING the internal spring valve from the extension hose.
TOOLS
If building Core Type A, you will need:
- Disposable gloves
- Permanent marker
- Cotton-tipped swabs
- 100-120-grit sandpaper
- PVC primer/cement
- Paper towels
- PVC pipe cutter that makes straight edge cuts (two options shown above)
- Ruler
- Utility knife
- Slip-joint pliers (optional, but occasionally useful)
If building Core Type B, you will need:
- PVC pipe cutter (to make the Legs)
- Utility knife (to cut the TR414 valve for Core Type C)
- Kitchen shears (to trim reusable straw)
GETTING STARTED
Whew! Let's get started. Some of the Steps below will not apply to your build, depending on which configuration you chose. Note that pictured parts may differ from yours due to updates.
Step 1: Assemble Base
The Base holds the Core in position and uses Clamps to keep the bottle on the launcher until the Launch Pin is pulled.
- Put Clamps in place; hold temporarily with a rubber band.
- Slide the Collar over the Clamps partially, lining up the "PIN" notations on the Collar and Base, remove the rubber band, then press the Collar all the way down
- Loop rubber bands around each leg support and over the hooks on the Collar (3x)
Step 2: Assemble Legs and Stow Parts With Carrier
ASSEMBLE EACH LEG x3
- Collect your Leg pipe sections. They should all be the same length, but the exact length does not matter. 15-20cm (6-8") works well. If prioritizing portability, use 15cm. If prioritizing stability and planning to use larger bottles, use 20cm. Be cautious with pipes longer than 20cm; the longer the pipe, the greater the torque force on the Base. Ground anchors provide important stability; Pegs or sandbags will give you more stability than longer Legs.
- Insert the Foot into one end of the PVC pipe. Insert a Peg in the other end.
STOW PARTS IN THE CARRIER
- You will assemble a Core in upcoming steps. Take a note from the pictures of where this will go.
- Hold the Legs vertically, sliding each Foot behind a cross-brace and fitting into the groove in the Collar
- Put the Carrier over the end of the Pegs, lining up the "PIN" notation with the Base
- Slide the Carrier downward into place
- Stow the Launch Pin and wrap the cord around the cleats
- Stow an optional Hose Extension
- Add an optional clip
Step 3: Assemble Your Core
Each Core has different build instructions. Find the applicable Steps below for your Core.
Core Type A: Step 4
Core Type B: Step 5
Step 4: Core Type_A Assembly
Core Type A is the strongest Core with the longest test record. It uses a launch tube (tube that goes in the neck of the bottle) which preserves reaction mass (i.e. water) in the initial phases of launch. Core Type A uses a stainless-steel bolt as reinforcement to overcome the weakness to shear of 3D-printed parts. It requires ASTM Schedule 40 1/2"-nominal PVC pipe commonly found in North America.
It also requires use of PVC cement, so intermediate tinkering experience is suggested.
PREPARE PARTS FOR ASSEMBLY
- Prepare PVC pipe. You need two sections. Ensure ends are cut square and deburred.
- Lower pipe: 7.0cm (aim for +/- 2mm)
- Upper pipe: 15-20cm. Exact length not critical. Use the longest that will fit in your bottles to maximize benefit of launch tube.
- Assemble the Core Center by inserting the bolt and attaching the nut as shown with the 3D printed hex wrenches. Carefully note that the nut goes on the "bottom" side which has the bevel in the center.
- Cut the TR414 tire valve as shown to remove the rounded "mushroom" side.
CEMENT PARTS TOGETHER
Gather the pictured materials in preparation for the bonding steps. I recommend reviewing the detailed instructions.
- Bond #1: Lower PVC pipe to bottom (beveled side) of Core Center
- Bond #2: Upper PVC pipe to top (flat side) of Core Center
- Apply extra cement to the Core Center to allow wicking action to fill gaps in the print
- Wipe away excess cement
- Insert the Valve Backstop in the Lower PVC pipe
- Partially insert the tire valve
- Apply primer using a cotton swab
- Bond #3: Valve Retainer to the PVC pipe to hold in the tire valve
- Compress the entire assembly for 1 minute
- Allow 45 minutes to cure
- Install the O-ring in the groove
Whew! Consider making several Type A Cores at once to make the most of your setup/cleanup time. Assemble any other Core types you want, then proceed to Step 6.
Step 5: Core Type B Assembly
Core Type B is the easiest to assemble and universally compatible as it needs no PVC pipe. It uses a “bottle stopper" configuration, which is inherently lower-performing than a launch tube configuration but still pretty great. No PVC pipe or adhesives required.
A reusable straw acts as a snorkel to prevent water backflow into the pump. It also enables a cleaner launch abort - it will drain the air while leaving water in place. It's preferred to use an air hose extension WITHOUT a valve so that the bottle will depressurize if the pump is detached. Tools are available to remove the valves.
You will need:
- 3D printed Core Type B
- O-ring
- Air hose extension, preferably WITHOUT a valve
- Reusable drinking straw, approximately 7.6mm (0.30") outer diameter, cut so it extends above the bottle water level
CORE TYPE B ASSEMBLY INSTRUCTIONS
- STEP 5A: Put O-ring on TR414 tire valve
- STEP 5B: Insert tire valve into Core Type B printed part
- STEP 5C: Securely attach the air hose extension
- STEP 5D: Seat the tire valve in the 3D printed part with a combination of pushing and gentle tug on the extension collet (spinny part). Don't pull too hard on the extension hose - it may pull apart depending on the strength of the crimp.
- STEP 5E: Insert the reusable straw
Assemble any other Core types you want, then proceed to Step 6.
Step 6: Set Up Launch Site and Launch!
Find an open and flat grassy space away from trees and traffic.
Set up the Launcher
- Insert the Legs into the Base
- Position the Base on a level surface
- Stabilize with Pegs (in grass) or heavy objects (on hard surfaces)
Load the Rocket
- Insert a Core into a bottle. You can either detach the Core from the pump hose and put it in a right-side-up bottle (upside-down rocket), or use the slack in the hose extension to pull the Core up and turn it sideways to load the bottle.
- Load the bottle + Core onto the Base
- Lock the bottle in place by raising the Collar and inserting the Launch Pin
Prepare for Launch
- Ensure the launch site is clear and that no one is near the launcher
- Pump up the Rocket. Some slow leak is possible (and safer!) and not a problem.
Launch!
- Pull the cord to the Launch Pin. Blast off!
NOTES ON LAUNCH ABORT
Note: if a launch abort is needed, the best thing is to depressurize the system with a pressure release valve. Some pumps have these. You can also purchase hose extensions that have release valves. You can use a thin object (the Carrier's cord cleats work well) to press the Schrader valve's center pin to release the pressure. If you use a hose extension without a valve, you can disconnect the pump to open a path for depressurization.
Step 7: More Ideas
The above is a brief overview of assembly and use of the Launcher. Several modifications and additions are in beta testing, with files available at the parts repository on Printables.com.
These include:
- Core Type C (glueless launch tube-style Core designed with US, UK, AUS/NZ versions)
- Fin tests (snap-on fins)
- Payload/parachute tests
Further instructions and discussions can be found at https://www.marimolabs.com/water-rocket-launcher
Feel free to ask questions below and I will do my best to answer. Let me know if you need a model adapted to your local parts. And please share your makes!
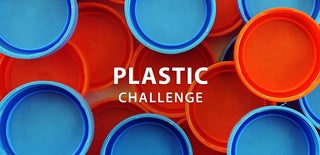
Second Prize in the
Plastic Challenge