Introduction: 3D Printed and Laser Cut Model of Gas Laws
For a chemistry project at my high school, I decided to create this model to demonstrate the following basic properties of different states of matter.
Gases are composed of fast moving particles that are spread far apart. These particles also attempt to diffuse from areas of high pressure to areas of low pressure.
Avogadro's Law states that the amount of moles and the pressure of a gas are directly proportional. This means that as the amount of particles in a gas increase, the pressure will increase as well.
Gay-Lussac’s Law states that temperature and pressure are also directly proportional -- meaning that as the temperature of a gas increases, the pressure will also increase.
An increase in the pressure of a gas will result in an increased number of collisions.
An increase in the number of particle collisions within a gas will lead to a faster reaction rate -- the time it takes for a chemical reaction to occur.
In my model, the fan underneath the chamber is symbolic of the temperature of the gas. As the “temperature” increases (the motor spins faster), the particles (pom-poms) will move more quickly and collide more often. Also, adding more pom-poms are added to the machine will also produce more collisions and an increase in “pressure.” Lastly, you may notice that occasionally a “particle” will exit the chamber all together. This is a representation of how gas particles will often disperse and diffuse throughout their surrounding environment to reach the zone of lowest pressure. The zone of lowest pressure is, in this case, outside of the wooden box. To make this project possible, I used Fusion 360 to design several 3D printed parts, and I used it to create the .dxf files for laser cutting!
Let's get started!
Step 1: Materials and Tools
Properly completing this project will necessitate various tools and materials. Let's get started!
Materials:
- 400cm^3 of plywood 1/8 inch thick
- 200cm^3 of clear acrylic 1/8 inch thick
- Spool of 3D Printing filament (I used blue.)
- 5V DC Motor
- Classic 3 blade propeller
- 15mm*15mm*20mm Rocker Switch (Other dimensions will require altering the 3D model I designed.)
- Acrylic Paint (This is optional but highly recommended. I ended up with many epoxy stains after glueing the box together, and painting over them fixed the problem.)
- Alligator clips and jumper wires
- Variable Power Supply (This project can be done with a simply AA battery, but then the "temperature" becomes constant, and Gay Lussac's Law can no longer be adequately tested.)
- Bag of Pom Poms
Tools:
- 3D Printer (I used a Printrbot Simple Metal.)
- Laser Cutter
- Soldering Iron
- Masking Tape
- Strong Adhesive (I used a combination of Hot Glue and Loctite Epoxy.)
- Vinegar (This is for when you cover your hands in epoxy and find it won't come off with soap and water.)
Step 2: Laser Cut and Assemble the Box
Laser Cutting
If you want to design your own box, I would recommend using Fusion 360. I modeled the entire box with 3D rectangles, and then I simply selected each sketch and exported it as a .dxf file. If you're using my pre-made designs, simply download all six of the files I have uploaded below -- each file is a different side. When laser cutting the box, both "side1.dxf" and "side2.dxf" should be cut out of acrylic, transparent plastic. These pieces will be the windows through which the view can observe the "particles" colliding inside. I cut all of the other sides out of the 1/8inch plywood although another material with the same dimensions could probably be used. After the job is finished, make sure not to remove the protective, outer layer on the acrylic. We will take this off in a later step when the epoxy has already dried, ensuring a much cleaner finished product.
Assembly
Securing this box together is not an simple task. Before permanently attaching the wood, fumble around with the design of the cube so you are clear on how it comes together. I found it was easiest two adhere two different sides at a time, and then glue those larger sections together -- see the pictures above. I used Loctite Epoxy as an adhesive, but I am sure anything like Gorilla Glue would work as well. Lastly, after everything is set to dry, if you're like me your hands will be covered in sticky epoxy. To my dismay, I discovered it did not wash off with soap and water. After some quick internet research, I settled upon soaking my hands with a vinegar infused towel. This immediately worked!
Step 3: Finish the Box: Paint It and 3D Print the Legs
Painting the Cube
After the central cube had dried, I sadly noticed that it was covered in cured epoxy stains, and it simply did not look good. One of the acrylic windows was stained as well! To solve this problem and improve the overall aesthetic of the project, I decided to paint over all of the wooden areas on the box and one of the transparent sides. To assure a clean painting job around the functional acrylic side, I lined its borders in blue painter's tape. Next, I simply started painting away! After the first coat of dark blue paint, I was not satisfied with the color and did a second layer. Finally, it was done and looked great!
Designing and 3D Printing the Legs
In order for the box to be properly attached to the main platform, it must have legs of an appropriate length and width. Based on the height of the 3D model of a motor housing which I had already designed (see step 4), I 3D modeled four rudimentary legs with Fusion 360. Each one took around thirty minutes to fabricate on my desktop 3D printer, the Printrbot Simple Metal. At this point, I had run out of my Loctite Epoxy, so I used hot glue to attach the four legs to each corner of the bottom of the box (the bottom is the side with the hole cut out).
Attachments
Step 4: 3d Print the Electronics Housing
At the center of the gas properties model, there is a fast-moving fan propelling the "particles" around the container. It is controlled by a switch and a variable power supply. To make the final product as professional as possible, I 3D modeled a custom enclosure in Fusion 360 to fit my motor and switch. If you are using different electrical components, you will definitely need to modify my design or create a new one from scratch. Once, my file was complete, I 3d printed it -- it was close to two hour print. Now follow these steps:
1. Remove the supports in the rectangular hole for the switch and the supports in the smaller wire hole at the bottom of the motor cavity.
2. Set the motor in its corresponding hole -- feeding the wires through their exit hole at the bottom first. This may be difficult, but don't give up. It took me a couple tries to actually get them through all the way.
3. Place the rocker switch in its proper location.
4. Use either hot glue or epoxy to adhere the motor and the switch to the central 3D printed piece.
Don't worry about wiring right now. I will cover that in a later step.
Attachments
Step 5: Attach Both Pieces to a Rigid Base
Before I decided to mount everything to a base, I tested out the machine with a AA battery. However, it was difficult to keep everything in place so I would recommend permanently securing all of the elements. Grab a friend because I would highly recommend using two people to complete this step.
1. First, place the motor housing and the laser cut enclosure on a square piece of cardboard around 13cm*13cm.
2. Grab a spare battery, turn the fan on, and adjust the electronics housing so that it is in the center of the base, and move the wooden container so that the propellers are not brushing up against the edges of the circular hole.
3. Once you have found the optimal positions for these elements, tell a friend to trace around the legs of the enclosure and the plastic housing in an erasable pencil while you hold them down.
4. Apply your choice adhesive to the housing and glue it down on the location measured previously,
5. Now comes the tricky part. Have a friend hold the motor leads together so that the machine is constantly running. Administer the glue to each of the plastic legs of the wooden enclosure, pick it up, and set it down over the fan onto the marked points. While the glue is still drying, make slight adjustments to ensure a clatter-free model. I ran into a small problem on this step. When I lifted the container over the motor, a little hot glue was transferred to a propeller. Thankfully, I was able to pick it off after everything had dried.
Step 6: Wire the Electronics and Prepare the Power Supply
This project is very simple to electrically wire. Solder or adhere the positive lead of the motor to one of the leads on the rocker switch. Then connect the switch and the negative motor lead to their corresponding terminals on the variable power supply. I used various alligator clips to hold everything in place. The project is complete and now you're ready to test it out!
Step 7: Add the Pom-Poms and Experiment With the Model!
Once everything is connected, switch the machine on, and dial the voltage from the power source up to around five volts. Then add the "particles" one-by-one through the hole in the top. When I first reached this step, I was worried about the particles being shot out of the hole in the top. Therefore, I 3D modeled and 3D printed a latch to be glued on over it (see the above picture.) However, this print ended up not sticking very well, and I realized that the likely-hood of a particle managing to fly out there was very slim; in fact it has still never happened throughout all of my testing!
Experimenting with different voltages on this machine can provide true insight into the structure of gases and molecules. I hope you find this contraption as explanatory and helpful as I did. If you have any comments, questions, or concerns I would love to hear from you in the comment section below! Also, I would appreciate a vote in the science and untouchables contests! Thanks!
Lastly, I'd like to give a shoutout to my friend and fellow maker, Ziven. He allowed me to use his laser cutter while making this project. Thanks a lot Ziven!
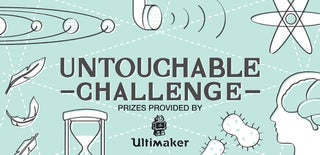
Participated in the
Untouchable Challenge
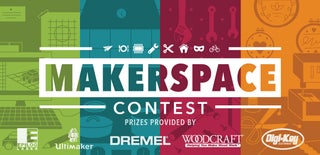
Participated in the
Makerspace Contest 2017
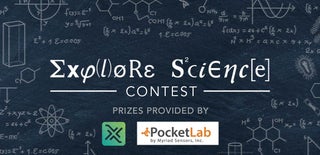
Participated in the
Explore Science Contest 2017