Introduction: 3D Printed and Resin Cast Shrink Ray From the Outer Worlds
- We have flown through Outer Worlds twice since it releasing and were instantly drawn to all the Science Weapons. After seeing the Shrink Ray we knew instantly that it was a potential project. We found a 3d model of it on Thingiverse and went to work!
We used our Glowforge to make both the sign and the stand for the Shrink Ray. If anybody is interested in purchasing a glowforge you can use my referral code to get: $500 off a pro, $250 off a plus, or $100 off a basic. I’ll get credit too! Use the link below. We love our Glowforge. Feel free to message us with any questions!
https://glowforge.us/r/DSKCNJZL
FOLLOW:
Head over to https://whengeekscraft.com for more of what we do!
INSTAGRAM: https://www.instagram.com/whengeekscraft
FACEBOOK: https://www.instagram.com/whengeekscraft
If you like what we do here, Support our crafting habits on PATREON - https://www.instagram.com/whengeekscraft
Supplies
Below are Amazon Affiliate Links to tools used in this build. Using these links don't cost you any extra, they just help us feed the cats and leave the lights on:
- CR - 10 3d Printer - https://amzn.to/37ZrQ6u
- Hatchbox PLA Filament - https://amzn.to/32oaUFy
- Rust-Oleum, Gray, Filler Primer Spray Paint, 11 oz - https://amzn.to/32oaUFy
- UV Resin - https://amzn.to/32oaUFy
- UV Lamp - https://amzn.to/32oaUFy
- Vallejo Basic USA Colors Paint Set, 17ml - https://amzn.to/32oaUFy
- paint brushes - https://amzn.to/32oaUFy
- xacto blades - https://amzn.to/32oaUFy
- MIFFLIN Cast Plexiglass Sheet (Transparent Clear, 1 Piece, 12x12 Inch, 0.118" (1/8 in) Thick) - https://amzn.to/32oaUFy
- Source One LLC 1/8 th Inch Thick Acrylic Plexiglass Sheet (12" x 12", Black) - https://amzn.to/32oaUFy
- Testors Red spray lacquer- https://amzn.to/32oaUFy
- 3D Printing STL file - https://www.thingiverse.com/thing:3927987
- Filler Primer Spray Paint - https://amzn.to/38YEfc2
- UV Resin - https://amzn.to/2HW4C6w
- UV Resin curing lamp - https://amzn.to/37RGAUR
- Sanding materials (Sticks, sheets, wet/dry high grit papers...We used almost all of them) - https://amzn.to/32lJ0tW
- Silver Spray Paint
- Vallejo Model Paints for Distressing - https://amzn.to/2SYmVyC
- Tamiya 6mm Masking Tape- https://amzn.to/2PqS7nS
- Alumilite Casting Resin (or whatever you want to use as a dome alternative) - https://amzn.to/2vYuYCu
- Pressure Pot
- Smooth-On Oomoo 30 - https://amzn.to/390jsVy
Step 1: Find and Print the 3D Model
Head over to Thingiverse and download the 3d printing files for the Shrink Ray.
https://www.thingiverse.com/thing:3927987
In Cura, we did the following Settings:
- Infill - 10%
- Shell - 2 layer Shell
- Detail - Fine detail for the CR-10
- Filiment - HATCHBOX PLA WHITE
Step 2: Sand the 3D Printed Pieces and Apply UV Resin to the Surface
- Start basic sanding at 120 grit to knock back a lot of the harsh layer lines. Be careful not to hit any small detail sections.
- Use some sanding sticks (Pictured second) to get in some of the nooks and crannies where it's too difficult with the paper.
- End sanding on the PLA at 220 Grit. You're not looking for the model to be perfectly smooth, you just want a slightly smoother surface.
- Dust the model off and brush on UV resin (Picture 3).
- Do small sections at a time and don'tlet large amounts pool.
- Let cure under UV lamp until hard and not sticky.
- Tip- Keep the bottle of resin, the cap, and the brush away from UV light while on.
- The goal of the resin is to fill in the layer lines. It will leave a smooth painting surface.
Step 3: Prime and Sand Again
- Using Rust-oleum Gray Filler Primer, spray multiple LIGHT coats onto the models.
- Sand back any high spots or areas that paint pooled using sanding sticks.
Step 4: Glue the Pieces Together and Sand Some More
- Using 5-minute epoxy, Attach the two pieces together and clamp the model shut with rubber bands.
- After the pieces are dry, start to sand and fill the seam lines.
- Follow the same methods as previously stated. I personally filled the seams with UV resin and sanded back the seams with sanding sticks.
Step 5: Spray Paint and Mask
- Spray the entire model with a few LIGHT coats of Silver Spray Paint.
- After the silver paint is dry, use Tamiya 6mm Masking Tape to prepare for the Testors Extreme Laquer Red Model spray paint.
- Mask off any areas that need to stay silver and apply a few coats of the red paint.
- After everything is dry, remove the masking tape.
Step 6: Dry Brush to Distress the Model
- Using gunmetal model paints (a mixture of Vallejo metal paints and Army painter model paints were used)
- Dip the brush in the paint and wipe off most on a paper towel.
- You want to dry brush the paint onto the model.
- Check out some youtube videos for dry brushing if you have never done this before but too much paint will look wrong. Dry brushing is the way to go.
Step 7: Add the UV Pigment Powder Effects
- In a cup, mix the UV Resin and the UV Pigment powder together.
- Stir with a popsicle stick.
- Working slowly and using the light often to set, pour the UV resin into the sections where the Shrink Ray glows.
- Make sure to remove any seepage before applying the light.
Step 8: Make the 'Glass Dome'
This gets tricky and we could have done this so much better so listen to all of our tips or check out other YouTube Videos for two-part mold making.
- Process the dome to a smooth surface BEFORE MOLDING. Sand, UV Resin, Sand, Filler primer, Sand again
- When the model is smooth, then make the mold!
Mold making process - Part 1
- Create a form for the mold to sit in.
- Put a clay damn about halfway up the model itself.
- Add registration marks into the clay.
- Mix up Smooth-On oomoo 30 and put in into the form. Follow the directions on the box and use mold release.
- If you have access to a vacuum chamber, remove the bubbles from the oomoo before pouring into the mold.
- If you don't, then pour the mixture in from higher up.
- Tap the walls of the mold to pop any bubbles
Mold making process - Part 2
- Remove the half-done model from the form.
- Remove the clay and clean up and extra clay pieces.
- Create a new form, add two pipes for pouring the resin, and bush on some baby powder before pouring in the next layer of oomoo.
- We hot glued two sticks to the model to act as pipes.
- Mix up Smooth-On oomoo 30 and put in into the form. Follow the directions on the box.
- If you have access to a vacuum chamber, remove the bubbles from the oomoo before pouring into the mold.
- If you don't, then pour the mixture in from higher up.
- Tap the walls of the mold to pop any bubbles.
Separate the mold
- If you did the model right then it will pull apart properly.
- If you goofed up like us, then you will have to cut it out.
- Regardless, mark your sides and use rubber bands to clamp the mold together.
Resin Casting
- Mix up Alumilite Clear (Slow) by following the directions on the container and pour the resin into the container
- Put the mixture in a pressure pot for a perfect clear result.
- If you don't have access to a pressure pot, it will still work, it may just have some bubbles.
Sanding and Polishing - IF YOU NEED TO SAND AT ALL:
- Start sanding through the grits and clear often.
- As a good rule of thumb, each layer of sanding is to remove the scratches from the previous.
Follow the grits:
- Dry sandpaper: 60,120, 220, 400
- Wet/Dry sand paper: 600, 800, 1000, 1500, 2000
- Polish: Novus 3,2,1 polish
Step 9: Attach All the Pieces Together
- Sand each attachment point so there is a place for the resin to adhere.
- Put UV Resin on the nose and attach it to the clear dome.
- Clean out any seepage and use the UV light to cure.
- Repeat the process with the Shrink Ray Side and cure with the UV light.
Step 10: Laser Cut the Sign and Stand
For file: ShrinkrayStand.svg
- Cut the pink pieces on 1/8th-inch material
- Cut the blue pieces on 1/4th-inch material
- glue the pieces together
- Spray paint the pieces Gold
For File ShrinkrayStand2.svg
- Engrave the text, Cut the shape of the text block and cut the stand feet on 1/8th-inch clear acrylic
- Cut the frame out of black 1/8th-inch acrylic
Gluing the sign together
- Stack the pieces together and clamp the with sewing clips(pictured above) so they are lined up for gluing.
- Take out the clear acrylic text panel, put a small amount of UV Resin on the border of the clear acrylic panel, and place back into place.
- Clean up anyglue that rose to the top of the panel and turn on UV light. This will glue all the layers together.
- Using superglue (CA Glue) on acrylic will cause the acrylic to fog.
Step 11: Display It Somewhere!
Stay Crafty my friends!
Nicole C - WhenGeeksCraft
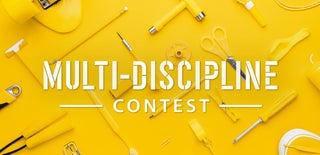
Participated in the
Multi-Discipline Contest