Introduction: PoWeR Your 3D Printer Wire Reinforcement for CR-10, Tevo Tornado, Anet Like
With the great popularity of affordable large volumen printers (CR-10, Tornado, Anet...), we are all learning how to handle tall objects avoiding the frustration of a print failure on the upper part, after many hours of "noisy" patient. The cause is that all this aluminium extrusion based printers has a week structure in the vertical axis, no matter if is 2020 or 2040 extrusions, and the situation get worse as printing so far from the heatedbed depends on how well is attached the plastic to the base, and that the hotend apply a lateral force to the last layer due to the melted plastic glue effect.
This is a very simple instructable (10' work and 3 or 4 hour printing test), but at least to me, has been one of the most rewarding mod to my 3D printer, in term of rquality esults and "zero cost".
We have seen some examples of very profesional metal bars & printer adaptors structures, like https://www.thingiverse.com/thing:2123233, but, I live in a island, getting extra bars implies another month of delivery, and also.. I am a kind of lazy.
So. I designed what I call PWR (pronounced "power") or Printer Wire Reinforcement for tall extrusion based 3D printers. If you like to replicate on your... stay tuned.
Step 1: First, the Results
An image worth more than thousand words. This picture is the difference of the upper part segment (from 20 to 30cm) of two 30cmx30mm single wall hollow cylinders printed before and after the wire structure was installed. To me was.. "wow" factor... Hope it bring you interest to follow this instructable..
Step 2: Get the Material
The BOM list is quite short, affordable, and available everywhere:
- 6 wood 4x20mm screws
- 2 washers, as larger as better
- 10m of kevlar based Fishing line, or similar
The most important choice is the wire, should be strong to support weight, but more important, should be almost zero strain. What is this? That means that the wire should not present any elasticity, so nylon wire should be discarded. If you are not a fisher, get to a speciallize shop and ask for a line that present high stress resistance (100-200 MPa) combined with a very low strain (lower than 0.005). If they look at you with a weird face, just ask for a line with kevlar core for fishing swordfish (they will relax and attend you as a rich man with luxury hobby).
I did not test other material, but kevlar core is being used everywhere for fishing, crates and climbing ropes,as its light and strong, without elasticity. In my case, I used Nylon Dyneema line with kevlar core (see picture). It is not the cheapest, (around $6 10m) but you will not break your balance.
Do you have everything already like me? Go ahead with building the wire frame...
Step 3:
This is very simple. Pick the 15mm screws and Insert them in the center holes of every x axis extrusion. Three on each side of the printer. Ensure that at least, half of its lenght is inside the hole. You may need to use an electric screw driver to really drive force and fix them stiff.
Step 4: Tide the Wire to the Screws
Again, very simple step, Tide the wire to the left side botton back hanging screw with a lace. Deploy the wire over the top extrusion side screw and follow until the front side, but at this point, get the wire through one of the washers.
Round the line through it and bring it back toward the back screw, passing again through the washer, but in the contrary direction (see the picture). We need that the washer get crossed by each wire on counter directions to get sufficient friction that will allow to strech the cable and sustain the strength at the end.
After crossing the second time the washer, follow again over the upper screw, and repeat the path through the back screw and again back. You may decide to simplify or extend the number of laps over the three screws with adventages and disadventages. A simple lap, will be easier to strech, but will provide less stiffness. Too many laps (more than 2), will provide extra stifnnes, but will be very difficult to strech.
Paid attention streching allways the wire before bending it over each screw, as kevlar wire use to deformate a bit and later will be more difficult to strech.
At the end of the lace, tide the wire end to the washer with your preferred knot.
Now you can strech the whole lace by pully carefully the washer. It will be not easy, depending the wire envelope texture. Take your time.
There is a trick to further strech the wire by inserting a wood or plastic piece among the laces and or twisting them several turn.
Take into account that after placement of this wired structure, you should level the heatedbed again, as the vertical extrusion may have different strength from one side than the other and has been bended a bit toward back or front of the printer.
You are done... let follow with the tests.
Step 5: Test Quality Result With Calibration Cylinder
Now we use a calibration model consisting in a single walled cylinder, 30cm in height, with a little brim (or raft if you prefer...). I use Openscad por this, as it is parametric an quick (see attached code). We create an stl file as usual and slice with you preferred program. I used here Simplify3D to verify that the wall is just a single pass. This is important as printing at 0.4mm layers will take a couple of hours. No infill of course and no support needed, as we are printing a very weak and tall tower on purpose to detect minimum printing layer shift or similar effect.
The intention is that if you print this challenging object and achieve quality, then yiu can feel safe to invest 10's of hours on your huge wished model.
I am quite happy with this upgrade and will recommend it to everyone with same extrusion base structure printer, that dont want to bother with a more professional metal triangular structure reinforcement.
Please comment your experience and spread the word, "PWR on" your 3D printer.
Have fun!
@agnuca
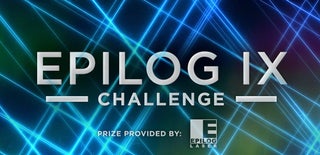
Participated in the
Epilog Challenge 9