Introduction: 4-20 MA CURRENT LOOP SIMULATOR USING AN RTD PT100 TEMPERATURE TRANSMITTER
4-20 mA SIMULATORS
Analog signal transmission ( also digital sometimes ) using 4-20mA current loops is broadly used in industrial environments. Some of its greatest advantages are: high noise immunity, cheap twisted pair (not shielding necessary) and the possibility of transmitting over very long runs of cable without appreciable signal loss.
Sometimes, for testing PLC analog inputs, checking the travel of 4-20 mA controlled valves or verifying an industrial process display, some kind of tool is desired to generate ( and sustain ) current signals to variable resistive loads (well, under some limits!). These instruments are known as "4-20 mA loop simulators" or "4-20 mA signal calibrators", etc.
Some of the parts needed to build this project:
RTD PT100 4-20mA temperature transmitter: ( http://s.click.aliexpress.com/e/niqvBmA )
Right angle removable screw terminal:( http://s.click.aliexpress.com/e/7ubAiMb )
Plastic project box: ( http://s.click.aliexpress.com/e/mQVFMfU )
500 Ohm single turn potentiometer: ( http://s.click.aliexpress.com/e/6Q33rJ2 )
500 Ohm multiturn potentiometer: ( http://s.click.aliexpress.com/e/jyVvZZZ )
3 position switch: ( http://s.click.aliexpress.com/e/Y7AEAEI )
Temporary push button switch: ( http://s.click.aliexpress.com/e/BAe6UbI )
1 Ohm resistor: ( http://s.click.aliexpress.com/e/RZBqVf2 )
10 Ohm resistor: ( http://s.click.aliexpress.com/e/YByZnaa )
47 Ohm resistor: ( http://s.click.aliexpress.com/e/7QZbmU7 )
-----------------------------------------------------------------------------------
For more info, please visit:Absolutelyautomation.com
-----------------------------------------------------------------------------------
Step 1: CURRENT REGULATION CIRCUITS
CURRENT REGULATION CIRCUITS
To set ( and keep ) a fixed current in a loop with a variable resistance load, two things are needed: The ability to increase or decrease the loop current with some sort of controlled resistor, and a way to measure the actual loop current to make adjustments in such component.
A "crude" loop current control can be made with a variable resistor (potentiometer) and a multitester connected in series in milliamps mode. In this particular case a human being act as a control loop reading the meter and increasing or decreasing the resistance to keep the current near the desired value.
The aforementioned example, was very simple but highly dependent on the person who operates the potentiometer to correct any current fluctuation caused by a change in the loop resistance or a variation in the power source voltage.
To improve things, there are alternatives like using an LM317 voltage regulator in current regulation mode!. In this configuration the current adjustment is made with the feedback resistor, so the current will stay stable even with variations in the loop resistance or in the voltage source. In some other projects, a specialized XTR101 chip was used. All depends on budget, required precision and electronics building skills!
Step 2: LOW COST AND READY TO USE 4-20 MA TRANSMITTER
LOW COST AND READY TO USE 4-20 mA TRANSMITTER
This project born to be a solution for the recurrent need for the people working in areas like industrial control and instrumentation, for a low cost tools to make simple quick checks on devices with 4-20 mA inputs
This instrument is no means neither a replacement for 4-20 mA simulators with digital displays, nor instruments used for signal calibration&certification.The idea is to have a low cost, easy to build (with common elements found in a technician's toolbox), portable and that doesn't require too many skills (soldering, PCB, breadboard, etc.)
The brain of this instrument is an RTD PT100 4-20 mA temperature transmitter (also used in an early project), with some other components like resistors (as possible low values like 1 ohm, 10 ohm and 47 ohm) and a 3 position switch. This kind of transmitter "translates" a resistance value into a current value according to a PT100 to ohm conversion table. Depending on the elements nearly available, this simulator could exhibit different characteristics:
Continuous linear current adjustment, using a low value potentiometer.
Current preset values "temporary", (while pressed) using push buttons and a resistor array.
Current preset values "latched", using a 3 position (or more) sliding switch and a resistor arra
The circuit shown is pretty simple. A resistor array made of multiple resistor (parallel and series) to make 3 equivalent resistors for the chosen RTD transmitter lower, mid, and max current points. in this example the transmitter range was from -50 C to 150 C (mid value 50 C). The resistance values of those points according to RTD table are: 80 ohm, 119 ohm and 157 ohm. The 3 position switch, "shorts" some portions of the resistor array to obtain the aforementioned resistor values to get currents of 4 mA, 12 mA and 20 mA.
Instead of the resistor array, a low value potentiometer (e.g. 500 ohm) could be used to have a fine current adjustment, however such low value single-turn pots are less common to find in stores than 1k pots and above. If a multiturn pot is used, there is no easy way to make physical marks for predefined values, so an ammeter has to be used to set the desired current.
The lack of a multi position switch is not an obstacle!. Instead, temporary push button switches could be used. Every push button must "short" some part of the resistor array to give a current preset. The only disadvantage of this implementation is there is no "automatic latching" of a current preset.
Step 3: TESTS AND CONCLUSIONS
TESTS AND CONCLUSIONS
The circuit could be built neither with soldering nor PCB nor enclosure, just twisting resistor terminals to make connections and wire wrapping cables to switches. However, to increase stability and mechanical protection the circuit was built on top of a very simple PCB (copper clad & sharpie method) and was enclosed in a little plastic box. To ease connection/disconnection of the loop's wires removable right angle terminals were used.
As seen in the video and pictures, current presets are not linearly ordered (20 mA, 12 mA and 4mA). The real order is 12 mA, 20 mA and 4mA. The reason for this was the switch used: 3 positions, but only 2 contacts!. So the middle position does not "short" any part of the resistor array, leaving the biggest value of resistance and consequently the biggest current preset(20 mA).
Two 12V (A23) batteries were embedded and connected in series to make an internal 24V power source for tests when there is no external power. The 2 position switch makes possible to choose between internal 24V power or external source for the loop.
The RTD PT100 to 4-20 mA transmitter used requires around 11 volts to work, so the maximum voltage drop on the loop using a 24V power source is around 13 volts. For a max current of 20 mA the biggest loop resistance is around 650 ohms.
The solder joints, connections and wires between resistors, the transmitter and switches should be made with the best quality possible, because their own resistance modifies the resistor array, so probably some of the resistors should be "trimmed" for better precision.
The internal 24V power supply (2 x A23) is recommended only for occasional and short tests when there is definitely no other power source for the loop, because these batteries have very low capacity and discharges very quickly if used for long times.
--------------------------------------------------------------------------
For more info, please visit:Absolutelyautomation.com
--------------------------------------------------------------------------
Attachments
170412_4_20_MA_CURRENT_LOOP_SIMULATOR_USING_A_PT100_RTD_TEMPERATURE_TRANSMITTER.pdf
170412_4_20_MA_CURRENT_LOOP_SIMULATOR_USING_A_PT100_RTD_TEMPERATURE_TRANSMITTER_KICAD.zip
170412_4_20_MA_CURRENT_LOOP_SIMULATOR_USING_A_PT100_RTD_TEMPERATURE_TRANSMITTER_PCB.zip
170412_4_20_MA_CURRENT_LOOP_SIMULATOR_USING_A_PT100_RTD_TEMPERATURE_TRANSMITTER_SCHEMATIC.pdf
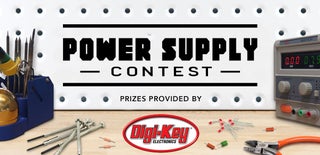
Participated in the
Power Supply Contest