Introduction: A Dust Splitter for a Dust Collection System
This time I will show you how one shop vac could efficiently collect all dust from various workshop power tools.
I have a small workshop with few basic woodworking tools, and till now all of them are dependent on a single shop vac. When I’m switching between tools for different operations I need to follow with a dust hose too. This drives me crazy, so let’s change that with a clever homemade device.
How I did it - you can check by looking DIY video or you can follow up instructions below.
For this project you will need:
Materials:
Neodymium magnets 23N, 10mm in diameter and 5mm height, 16pcs
15mm plywood sheet
PCV pipe 50mm in diameter (approx 50cm)
5min epoxy glue
Dust hose 50mm in diameter
Hose clamps 5pcs
Wood glue
Tools:
Table saw
Mitter saw
Drill press or regular drill
Forsner bits in diameters of 50mm and 10mm
Router with a chamfering bit
Deburring tool
Sandpaper 120 grit
Clamps for glue up
Ruler, square, pencil and other small bits and bobs that are usually found in every work area.
Step 1: Preparing Plywood Pieces
I started by cutting 130, 20, and 25-millimeters wide strips out of 15 millimeters of plywood. Marked a few reference points for upcoming holes.
Step 2: Drilling Some Holes
In the middle of the board, I drilled 5 50mm holes by using a forsner bit. After that, I changed the bit to 10mm and drilled evenly spaced holes with 5mm depth.
Step 3: Preparing PVC Pipe
I took a regular 50mm PVC pipe and sliced off 6 equal pieces.
Inside burrs were cleaned with deburr tool. This small and cheap tool will make life way easier. If you do not have one - you should get it. One pass leaves a nice and clean edge. Outer burrs I sanded with sandpaper. Not as effective - but done the job too.
Step 4: Glue Pipes in Place
Mixed some 5 minutes epoxy and glued PVC pieces in prepared holes.
Step 5: The Magnets
Next, I used really strong neodymium magnets. They are rated for 23N of holding power which is a lot considering the size - 10mm in diameter and 5mm in height. They are sitting pretty snugly in drilled holes, but I fix them permanently with the same 5 min epoxy.
Step 6: Glue Up of Splitter Base
While the epoxy was curing I moved to the narrow plywood pieces and glue them together. 30min later I glued that L shape sliders onto the main piece. I placed a scrap plywood piece in the middle to get a perfect parallel alignment. I was very careful and tried to avoid any wood glue squeezeouts towards the inside, because I won’t be able to remove that insert later. The insert did its job and successfully was removed.
Step 7: Making Splitter Slider
Now I will make a second dust splitter part by cutting a small piece of this plywood insert.
As with the base - I marked and drilled the holes for the PVC pipe and for the magnets. One more time came back to the drill press and drilled 10mm holes in the corners and 50mm hole in the middle.
With the same fast querying epoxy glued magnets and PVC pipe pieces in place.
Step 8: Last Details and First Test
I gave the last touch-up on the dust splitter base with a palm router and a chamfer bit.
First test. My used magnets are in the sweet spot of holding power. I could use only one finger to move the slider, but at the same time, it snaps and centers itself in the next place immediately.
Drilled and countersink a pair of holes at an angle which will be used to attach the dust splitter under the workbench.
Step 9: Preparing Dust Hoses
To connect each power tool I bought this 50mm of diameter technical hose. Cut 4 pieces in the needed length and secured them on the PVC pipe outlets with hose clamps. Later you will see why one outled was left open.
Step 10: Installing Dust Splitter and Connecting Tools
I found that the perfect place for the dust splitter will be under the workbench from where I could reach each tool by using the short as possible dust hose.
Routed all hoses to tools and connected with the 3D printed adapters. They were designed so that will be no need to use any hose clamps. They simply just turn in the hose like a screw.
Step 11: Connecting Shop Vacuum / Cyclone
The last piece in the dust collection system is this - my homemade cyclone which I build a few years ago. From day one till now it works perfectly. If you are interested here's the video of how it was built - https://youtu.be/uiN17AZKBao.
Placed cyclone in place and disconnect the previous intake hose. I will connect it to the first dust splitter port and will use it as a free dust hose to clean the mess all around or will connect it to the orbital sander or another power tool.
The last piece of the hose was used to connect the cyclone inlet port with the dust splitter outlet port. Even with the hose attached, I could use one finger to switch the slider place between different ports.
Step 12: The Preview
My dust splitter is designed for 5 tools. Going from left to right, dust hose, belt sander, miter saw, table saw and band saw.
Step 13: Testing in Real Application
My shop vac is starting automatically after the power tool is turned on. All I need is to change the dust splitter port before turning the tool.
To use the dust hose I need to turn the show vac manually, but that not an issue at all.
Step 14: Final Thougts and Potential
I made a dust splitter for 5 tools, but it could be made with your preferred number of ports and sizes. This is a general idea of how the very simple device could be made depending on each workshop’s needs. And yes, this is one of those builds that I’m questioning myself - “why I didn’t build it years ago”.
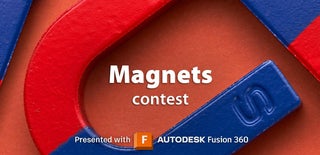
Second Prize in the
Magnets Contest