Introduction: A-Frame Garden Shed From Reused Wood
In early summer of 2020 we finally got a (rented) garden after beeing on the waiting list for almost two years. For those not familiar with the german "Schrebergarten", head over to this article or over here to get to know this very german concept. It might be interesting... ;-)
So we finally had the garden especially my wife was longing for. I agreed under the condition, that I could build a bigger shed on the plot, as the existing one was only a little toolshed and I wanted something to make the stay in the garden relaxing and also possible under worse weather conditions. She agreed under the term that it shouldn't be too big.
As this is Germany, there are obviously a lot of rules you have to follow when renting a Schrebergarten, even more so, when you intend to build a shed on it. The main important ones for me where:
- 24 sqm built over area tops (this includes a terrace or similar)
- when building a classic roof maximum height over floor 3,5 m
- maximum distance floor to ground 0,25 m
- you have to hand in building plans that need to be approved before you are allowed to build
- you have to seek final approval when you are done building
So I thought a lot about what I wanted to build. First decision was, that I didn't want a "classic" prefabbed shed. Too expensive and too ugly. So as a big fan of the tiny house movement I went digging in the interwebs and at one point I stumbled over the concept of the A-frame-house, I even remember having seen some on instructable (in fact, I now found four: here, here, here and here). Especially the concept, that you could swing up a part of the roof and create a large open space and transform the closed room into a covered terrace within seconds was very intriguing.
I discussed the concept with my wife and she gave me green light, if I stayed under 4x4 meters. During my research I watched a lot of youtube videos from other builders and also found these great plans from relaxshacks that I bought and downloaded. If you want to build a standard A-frame I can recommend these.
After a lot of research, I came up with my own idea of the shed:
- a smaller part as tool shed
- a larger part as "living room"
- a (very) little terrace
- a sleeping den
- a little cellar/fridge
- all built upon 3,5 x 3,5 x 3,5 m
- all built of reclaimed/reused wood (wood prices at the start of this build were sky high)
As I started drawing and did my first rough calculations, I realized that with new wood this thing would cost me an arm and a leg, so I decided to mainly use reclaimed materials (only the wood would have cost me almost 2500 - 3000 Euros).
Then I went at the final (?) plans. I used sketchup to do this. It's free to use and I'm familiar with it, so I got results pretty fast and the plans I got with it were accurate enough to hand in for my building permit...
To get the final go from my wife I even added the 3D model into a garden picture.
I started this build in October 2021, most of it was done until November 2022 and I got the official approval in December 2022, but some things are still in progress.
I tried do split up this instructable into steps that make sense, but you will recognize by looking at the pictures and videos, that it wasn't built in that order. I switched from one part to the other as necessary and sometimes I had to wait with one thing until materials got available (for a reasonable price or even better for free). Sometimes I even had no clue how to continue, so I did something else until I got the right idea. As you may realize, I'm no carpenter, just a woodworm willing to learn and there was a lot of learning involved in this build!
It's necessary to have the big picture in mind, the problems will be solved, when they appear.
A lot of times I had a second smartphone propped up somewhere on a pole or tripod, taking pictures every 30 seconds. During the build I published this short stop motion videos (most of them without sound) and others in the bike forum, where I documented the chronological progress of this build. Later on I intend to put them all together in one video with some nice music. But for now the short ones will have to do...
So after this long intro, I invite you to come with me onto my journey, but be warned, it will be picture heavy!
Supplies
Picture heavy he said, and then in the next step one single picture....
Here you see most of the tools I used. Mostly classic handtools, but also a few selected powertools. Missing on this picture are a few more clamps, a little powersander, a milling tool and two different circular saws I could borrow from a friend, but that's about it...
I did a lot of work with handtools as they obviously need no external power. There is no electricity directly in our garden. When I wanted to work with powertools I had to pull an extension cord from the main house (where the shared toilets and electricity are) to our garden. If I take the straight route through the back of our neighbors garden (he's ok with that) my 40 m cord is just long enough...
The other reason for using handtools is, that they make less noise, and as the german Schrebergarten has very strict rules about quiettimes it's better to work with your hands power... for the sake of peace!
Step 1: Collect Materials
Before I could start building I had to collect materials. Soon after I got my building permit I started to look out for materials. The first score I made was a batch of wooden beams that had been a terrace before: about 10x20x400 cm This gave me my base. Soon after that I scored several batches of 10x10 cm beams. One batch around 2 m and another 2 batches with 4-6m long beams (the ones pictured above on car and trailer).
I also collected a lot of pallets, stone plates, bricks and gravel and even a nice large green wooden door. One really lucky find was a complete IKEA bed (Kura) for free. Then I also got a lot of flooring boards for free, even some really nice ones that still had scraps of a newspaper from 1959 on it. Another free load of flooring I had to tear out myself and carry it down about one hundred stairs.
I found corrugated roofing for a very fair price and even some fitting corrugated polyester material just because I was telling the seller of the roofing what I was looking for and guess what, he had some standing in his barn...
The first hunt for materials took almost the full two weeks of my autumn break, but it really was worth it. I got to know a lot of very friendly people and some nice corners of Berlin I've never been before. As I got a lot of the stuff for free or for a very fair price, I also saved a lot of money.
After those initial two weeks I had enough materials to start building. But there was still a lot missing. Throughout the whole build I was constantly monitoring "ebay Kleinanzeigen" (it's probably very similar to craigslist) for potential building materials. Usually if something interesting pops up for free you have to be very fast and ready to pick it up the same day. The IKEA bed for example landed in the trunk of my car only about 3-4 hours after it popped up...
I also found three cheap large sheets of thick ply, painted in a similar green as the door, another batch of corrugated roofing for a good price (lighter than the first ones) and I got a nice little yellow kitchen cabinet for free.
Step 2: Prepping the Building Site
When most of the materials were in the garden it became obvious that I had to start organising the place. The building materials were already stacked nicely, the wood was covered and the area, where the new shed would be built was empty...not.
There was still the old shed. I had to get rid of it first, but before doing that, I had to empty it and store all the tools and other stuff somewhere else. For that reason I had a little material tent set up (it was a gift from a fellow camper), arranged some pallets in it to be able to hang or lean against all the tools.
After that I could get rid of the shed and dig out the old foundations.
The roof of the shed became then the surface of my improvised table. It turns out, that together with four pallets they made a sturdy table with an almost perfect height to work upon.
Step 3: Plans and Sketches
Before and during the build I did several sketches. You can also see pictures of my calendar in the week of October 2021, where I did most of my tours to collect materials.
Sketching and sometimes even ripping and folding a piece of paper helps me a lot. Even if my sketches are very rough, it visualizes my ideas and keeps them save.
The plans to hand in with the other papers to get my official building permit I did with SketchUp. I redid them after the build was done (the last 3 pictures), as I mirrored the build right after I started as it fit better into the rest of the garden.
Step 4: Foundation
For a solid shed, you need a solid foundation. When I had decided on the final position of the shed, I built a grid of slats around it, putting all the horizontal slats leveled in the corners on the exact same height with the help of a "tube level" (basically a clear tube with water in it). Then I pulled strings along the edges of my planned shed and marked their positions on the slats.
Like this I could easyly recreate the position of each edge or corner of the shed if necessary.
Then I dug 9 foundation holes down to the layer of very hard clay that lays underneath the loose dirt. To dig the right size holes I marked the size of the stone plates with two slats screwed together.
The depth of every hole was different. To level them out, I filled them all to the same hight with fine gravel (some needed an extra filling with bricks to not spend to much gravel on this) on the gravel I then placed the stone plates (measured as often as possible against the strings) and stacked 6 bricks on each plate.
To check if all the stacks are level I used one of the wooden beams I had on site... ;-)
Step 5: Floor Platform
After the foundation was laid and levelled, it was time to build the base. For this I used the 20x8 beams I purchased early on in the project. They were about 4 meters long and gave me the perfect base for the shed: heavy and sturdy!
I slotted all the joints by cutting them with my circular saw first and chiseling them out after (I also used the handsaw on some of them).
When I was sure that I wouldn't change the position anymore, I nailed together all the joining slots with loooong nails.
Step 6: A-frame Beams
To build the 4,5 A-frames, I used the base platform as a large jig, so that I easily could mark and cut all the beams to the right size and angles.
First I marked and cut the sides (top first, then bottom), then I added in the horizontal beam. Again all joints where cut in with handsaw/circular saw first and then chisled out. After I had the first frame done, I temporarily put it up to get a basic idea of the complete size of the shed.
After I had done all the A's I layed out all rear and later the front beams, to fit the horizontal connecting beams in. I had to be very carefull here to get the spacing right on both sides!
With all that prep work done it was time to errect the basic construction. I did all this alone, so it was important to come up with temporary support structures to keep the frames upright once they were up. Putting the horizontal beams in required some "convincing" with hammer and spanners, as either the wood had "worked" due to humidity inbetween doing the cutouts and piecing it together (about two weeks of humid autumn days inbetween) or my measuring was of a bit. But finally I managed to put it all up and together!
Step 7: Roof Cladding
With the structure of all the A-frames up it was time to cover the roof.
As material for covering I used the large batch of flooring I got out of the attic of that 6 story building in Berlin Kreuzberg. It was about 30 sqm of good dry tongue and groove. It was more than enough to cover the complete roof and save something for other parts of the build.
To start off aligned with the rest of the construction, I nailed on some short slat leftovers to the base frame, so that I could rest the first board on it leveled before nailing it on. From there on I made my way up onto the top of the roof. While at it, I learned pretty quick, that it was best to only hammer in the lower nails on the new board and only after that the upper nails of the board mounted before. Like this there is still some possible movement of the upper edge of the fixed board, when slotting in the next one, thus making it easier to really slotting it over the complete length. It's also crucial to use a leftover piece of tongue an groove board as an in-between while hammering the new board down into its final position.
I finished the edges with some simple slats, mounted upright to create a slightly raised edge. In retrospect I wouldn't do that again, as it created unexpected problems when mounting the corrugated roofing and I had to change it later in the build.
So if you want to get clean edges you can use slats, but use ones that have the same thickness as your roofing boards!
After I was done with the boards I covered the complete roof surface with a vapor barrier to protect against rain while there was no roofing on it and against moist coming in when the roofing will be on later. It took longer than expected to get the final roofing done, so the wind had time to work and during a very stormy night it ripped the top half of the covering off. So be sure here to use long enough staples and get it down thight along the edges so the wind has nothing to grab onto!
Step 8: Corrugated Roofing
Putting on the roofing was very straight forward, or at least it seemed to be in the beginning. As I worked alone (as most of the times in this build) I had to come up with solutions to hold the roofing sheets in the desired position while setting the first few screws. I started in the back and for the first row I wedged a long plank just underneath the lower edge of the wooden cladding. This gave the roofing sheets something to rest on and me a possibility to get the placement and overlaps right.
First thing I realized was, that I had to lay flat the upright slats I nailed onto the edges of the cladding, as the waves of the roofing wouldn't fit over it. I did this only on one side (left) as the upright edge on the right (non weather) side provided a good starting point.
Next thing I learned was, that the roofing material didn't care about the selfdrilling screws, so I hade to drill the holes first with a "real" drill.
After the first row of roofing was on, I had to wait a few weeks due to bad weather, with the result that one of the storms tore off the top row of the vapor barrier. I had to reattach it and it didn't look nice anymore, but it will still do its job (I hope).
To mount the top row, I built a very improvised scaffold. It was stable enough to mount the roofing, so the rear was finished off quickly after that.
The rear was covered with 8 sheets of 1x2m. For the front I needed different sizes. I had two more 1x2m sheets and 4 1x2,5m sheets. The 1x2,5m sheets I used on the right lower half, for the top half I needed to cut down the other 4 sheets to about 1,6m. So I stacked all 4 on top of each other, marked the cut line and went at it with my jigsaw... First I used short sawblades just to realize that they were too short after breaking the two I had, so I went shopping for longer ones. They worked much better, but I still managed to break some more... But a few sawblades and several swearing words later all four sheets had the right length.
To mount the front roofing, I decided to build a little more solid scaffold and set the upper board a bit higher than on the rear side. Like this it was very easy to mount the upper boards (after predrilling all the holes).
As rooftopper I used two pieces of old GDR raingutters, both 2m long. As I had to stay within the building limits (3,5m above floor) I had to make the rooftopper really flat, as the top beam was already at 3,4 m. To achieve that I bent flat all the folded and curled edges of the gutters with flat nose pliers and a hammer. Like that I could cover the top with a very flat curve and still had enough material to screw the edges through the corrugated roofing into the top beam (just had to buy longer screws, as the roofing screws turned out to be to short for that).
As you can see in the pictures, this step cost the life of a few sawblades and drillbits...
Later in the game I got my hands on another set of corrugated roofing and was able to extend the roofing on all sides. Like this the protruding beams and also the sidewalls get a bit more protection from the weather.
Step 9: Kneewall
I'm also documenting this build in a subforum of a bikebuilders forum. Early on in the build, someone asked me, if I intended to build a kneewall. Not knowing what this meant (english isn't my first language) I had to do a websearch first to find out what he meant. But as soon as I knew, I realized that he just pointed me to the solution of a long lasting problem. Until then I couldn't figure out a good way to store those two long tables and four benches (all around 2,2m long) that we have in the garden for the ocasional party with a bigger number of guests. But this was it: a kneewall compartment over the total length of the shed!
The floor I made from four scaffolding planks (~4 m each) I had scored together with some 10x10 cm beams early on. The first plank had to be slotted in along the A-frame beams obviously. Another one of the planks I fitted in right above the horizontal beam, supported by several upright 3x6 cm logs. This gave me exactly the room I needed for the tables and benches!
The wall was then cladded with the remaining planks from the same flooring, I had used for the roof. Later on I added triangular doors to both ends of the kneewall space. They are made from slats from the old shed and a sheet of ply coming from a wooden transportbox I got for free. The tricky part on this was the hinging process, as I had to take into account that the outside of the shed will get cladded later on, so I had to let the hinges stick out far enough to allow the door to open fully later on. I resolved this by clamping two of the cladding boards inbetween beams and door when I screwed on the hinges. Also the edge opposite to the hinges needed some angle to completely swing into the frame. When all that was done I screwed another slat onto the A-beam as an inner frame to stop the door from swinging to far in. As intermediary "lock" I used a theatre hinge. And I obviously did this on the other side as well...
Step 10: Tool Shed Door and Outer Wall (right Side)
For the right side wall, aka the tool shed side, I almost exclusively used materials coming from the old shed. After putting the two upright beams for the doorframe up, I mounted the old shed door. To hinge it, I used the same method as with the two triangular doors. Like this the hinges are in no way accessible as soon as the door is closed, so no one can just unscrew them to get into the shed.
After the door was hinged in, I cladded the outside with the boards from the old shed. This was really straight forward as in: hold the board on, mark and cut. Ok, around the ends of the horizontal beams it was a bit trickier, but still... I had good luck with the triangular door, as the edge of the board below it had the perfect hight, so I only needed to cut of the tongue for allowing the door to open.
After all the cladding was done I mounted some latches to be able to lock the shed.
While I was continuing to build the rest of the shed, the door stayed like this for several months. When I was done with the rest of the outside, I "revisited" this door and added some wide trim, made from pallet slats, to cover the gap between door and the surrounding wall.
Step 11: Tool Shed Floor
To prep for the tool shed flooring and the separating wall I added several smaller beams to the subfloor grid. I needed something to rest the inner edges of flooring on (pictures 1-3). For this I used beams coming from the old shed. I also added an upright post in the middle to later fix the wall to and another post along the kneewall for the same purpose.
Then I took apart some of the pallets I had left. For this I enlisted some help from the kids to tear out as many nails from the pallet planks as possible. The did a very good job on that and so I got a good stack of nice planks (and a heap of leftover parts).
Throughout the build I got better at this and the amount of leftover per pallet got less.
After laying down a vapor barrier I placed the planks and cut them to size, so that they ended about 1cm before the intended separating wall, to allow some movement later when humidity hits in winter. I layed them out completly before I nailed them down, as I quickly realized, that I had to "play" a little bit with the placement of the slats to get a floor with no big gaps due to uneven or bent planks.
To finish it off I ran a kickboard along the edges. I intentionally left out the side of the kneewall, as I intend to install a composting toilet on that side later on, so there's no need for a kickboard yet.
Step 12: Separating Wall
For the wall between shed and "living room" I used the thick flooring with the newspaper scraps (from 1959). I had to lay them out first on my worktable, as I tried to put them up in the right order as good as possible and I wanted to keep as much of the newspaper scraps as possible, as I really like them. It's a little piece of history that I want to preserve as good as possible. So the challenge here was more of an artsy one than a construction one.
The latter was pretty straight forward: measuring/test mounting, marking, measuring again, cutting, mounting, nailing...
Later when the full wall was up I glued the lose parts of the scraps back onto the wood and gave the complete wall several coats of clear satin PU coating.
For the ceiling over the shed I also used parts of the same flooring but only the ones without paper scraps (see also step 20)
Step 13: Tool Shed - Shelfs and Tool Storage
With the roofing on, right outer wall, separating wall and rear portion of the sleeping den (see step 20) done, it was time to retire the material tent and to get all the tools and other stuff into it's new place. But first I had to build some shelfs.
Before starting with the shelfs, I mounted a long slat along the edge between beam and outside wall, to close off the little gaps that showed especially in the area of the horizontal beams. I did the same in the edge towards the inner wall.
the I simply screwed leveled slats to the walls on the hight I wanted to have shelfs. For the shelfs itself, I use pallet slats and flooring boards. They filled up pretty fast with all the little things...
In the old shed most of the longer tools were only leaned against the wall or hung up with a simple screw or nail. I wanted something a little more sophisticated and orderly. I took a few cues from Ana Whites site and came up with a nice hanging system. The first version with all the tools on one level didn't work, but when I arranged the shorter tools into a lower section, it became very clean, but still rustic due to the raw slats I used.
I then added in a few single screws and some more slats and the storage part was done. The right side is still used as a wood storage until the composting toilet will be built in. And when the "living room" has got it's own shelfs and cupboards, some of the stuff now stored here will then move over.
Step 14: Swing Up Roof
The core part of this build is the swing up roof. It opens up the rather small inside space towards the garden and creates a covered terrace of sorts. When closed, it still lets light through and creates a very nice atmosphere inside the shed.
I built the whole frame out of parts from an IKEA kura bed. They have a nice finish and the longer slats had almost the perfect size for my plans. Here again I had a general idea, had the materials and went on from there.
First I built the frame. For the horizontals I could use the slats as they were, I even had to cut them shorter to fit. For the verticals I needed to elongate the slats. You can see how I did this in the first picture. I added in diagonals in the corners for stability and a crossbrace for the same purpose. Later, with the corrugated poly already on I added another vertical brace to facilitate the pushing up and lowering down of the roof. As stoppers to define the "parked" position I added short pieces of the slats to the A-frames on both sides. They also were very helpfull in holding the roof in place while adding the bolts for the axles (first I used standard screws and replaced them later on with thicker bolts).
With the frame in place I could add the poly roofing. First I had to shorten it down a bit. The scraps then came in handy when adressing the main problem: As the axle was under the roof the top part hinged inside underneath the metall roofing, but the edges had to be outside to create an overlap to avoid water leaking in. So there was a "conflict of interest" in both upper corners that had to be solved. I used the scraps to come up with the cut pattern that allowed a max opening, but still keeping the gap/hole as small as possible.
Both (necessary) holes/gaps were then covered with pieces of a rubbermat (maybe replaced very soon) to avoid leakage. That's also the reason why I didn't screw in the lower row of screws in that part of the roof until after the rubbermats were in place.
Next problem to adress was how to hold up the roof when opened. In my research I had seen several solutions, none of them was really to my liking. I didn't want a complicated rig or a separate pole I somehow had to put in place while holding up the roof. So I developed a foldout system. For it to work, I had to recess the hinges so that the two parts of the folding pole could be folded flat onto each other and against the roof frame. The lower pivot point was also done with a thicker bolt and I added latches to the main folding joint to stabilize it in the stretched position. The same latch could also hold the pole in the "parked" position. Two very simple latches were added at the lower inside to secure the roof in the closed position against beeing opened from the outside.
The latches I bought, that should stabilize the fold didn't hold up very long, so I made my own from metall tubing and some lashes.
Step 15: Left Wall
After the doorframe was in place, it was time to get the left wall done. For this wall I used classic Berlin flooring boards. Classic in the sense that the colours oxred and the green you see were really common in Berlin at the beginning of the last century up to after WW2. The tones differ slightly, sometimes even from room to room, but it was the most used colour to paint floors. I used the coloured side inwards an the raw underside of the boards as outside wall. I used the same pattern as on the floor, two red one green. I started with a rather large batch of flooring (or so I thought), that I had gotten for free and used it for the floor and the wall. I started with the first half of the floor and then with the wall, after I put aside enough boards to finish the floor.
After I was half way up, right above the door opening, I suddenly realized, that I in theory I had enough boards to cover the wall, but practically all the boards that were left had damaged groove edges and were unusable for my purpose... I asked the lady that I got the boards from, as when I left, there were many more boards, but she had them already given away to someone else. It took me almost a month to get my hands on another decent batch of flooring for a reasonable price. I had to dig them out of a huge pile of ripped out boards, but it gave me enough to finish up the wall up to the top and still have a lot of boards left.
After a very wet first winter I discovered something on the boards that looks like mold. I'm not really sure about it, but maybe be I need to add a layer of protection onto the wall. We will see about that...
Step 16: Left Door
Very early in my hunt for materials I got my hands on this really heavy door. It used to be a door to a garage/shed in the outskirts of Berlin in it first life. It was in a poor state when I got it. The area around the doorhandle and the bottom edge were very rotted and needed some serious attention and drastic measures. Also the glass of the little window was missing. And the green paint was way beyond saving...
First I took care of the bottom edge by simply cutting it off. The door was to high anyway so this was the solution for two problems in one cut. The area around the outside doorhandle I simply milled and chiseled out and fitted in a piece of pallet board. I intend to cover this part with a sheet of brass later on. I also filled up the gap/indent that led around the edge of the outside. The door originally opened to the inside, but I want it to open to the outside, so I needed to fill this gap and add trim later on.
Then it was time to get rid of the old paint. For the outside I used a nylon brush with the drill. I used up two brushes until I called the front side done. There was still a lot of green, but most of the ugly paintchips were gone and a lot of the structure of the wood was visible.
On to the inside. I started off again with the nylon brush and mainly took care of the edges. The nylon wore off pretty fast and I had only a metal brush left, so I used that one, only to realize that It wore off as fast as the nylon. So I needed to go shopping another nylon brush to finish of the edges.
When I had the edges done, I tried the brush on the flat surfaces only to realize that it kind of melted the paint and then all the bristles got clogged with the heated up paint. So I took out my little powersander and went at the flat areas with 40 grit first and finished it off with some 120 grit sandpaper. Also on the inside I reached the point with most of the dark green paintchips gone, but enough green left to get a nice patina. Or like a fellow bike builder (and instructables member) used to say: "Stop before you think you are done"
Then it was time to get the door in place. I screwed some slat pieces where I intend to put a door sill later and marked the final top cutout to cut it with the jigsaw. Then I screwed a slat to the outside of the doorframe and clamped the door against it in its intended position. Then I carefully screwed on the hinges using a lot of measuring and a water level. I finally had a working door!
After the door was hinged I took care of the little window. I took the framing slats out and transferred the size and form directly onto some acrylic glass. I love working with this material as it is very easy to cut to size. You only need a ruler, a knife and a straight edge. Go over the desired cut several times with the sharp knife, then place the line along a sharpe edge and hold down the acrylic with another sturdy flat object (slat or similar) and you can just snap it off with a fast and firm downward push on the overhang.
After the window I fitted in the door lock, handle and lock plate. The lock and handle was very straight forward, as the necessary recess was already there and I only had to drill the new holes on the outside. With the locking mechanism in place I located the right spot for the lock plate on the doorframe. This was a lot of trial and error because I made a wrong assumption in the beginning instead of taking mesurements (stupid me!). But finally I could make it work and now I have a real locking door.
Now it was time to take care of the inner doorframe. At this stage there was still a visible gap inbetween door and frame and the door had nothing to stop it swinging towards the inside. So I cut some pallet slats to the right width and screwed them to the inside of the doorframe.
In this state the door stayed for a long time. After I had added trim to the door on the right wall it was time to do the same here. So I repositioned the hinges and added a wide trim made out of pallet slats to the edge of the door, covering the gap around the door.
Step 17: Under Floor Storage
When mounting the smaller beams inbetween the large first grid, I intentionally left out a part in the rear. I wanted to build a little cellar to keep stuff cool during the summer and above zero during winter. I dug a hole about 60 cm deep below floor level and then filled the lowest part with gravel to create a flat surface. On this I placed four of the same stone plates I had used for the foundation. Then I built a solid base frame (from leftovers from the old shed) and a hinged frame for the trap door.
With the base in place and the top end defined, it was time to build the wall. I still had a lot of bricks left from the foundation, so I layed them out and came up with a wall that I had enough bricks left for. I installed a sort of scaffold from old slats and layed down the first row of bricks. Then I enlisted some family help again. My kids go to a waldorf school and in third grade they usually build something on the schoolyard (benches, brickwalls, pizza oven, ...). My older ones class missed that important part due to the pandemic. So I decided to give him the possibility to build something on his own. That's why he layed down the bricks to build the wall of our little cellar.
After the kid was done, the only thing that was left to do for me was closing the gap inbetween the top row of bricks and the wooden frame. That was quickly done with some more mortar. Now the contents are protected against mice and rats.
Step 18: Flooring
For the flooring I needed to add a few more smaller beams. As well as in other parts of this build, I used parts from the old shed for that. The material was to perfect not to use. As stated in the last step, I left a large gap for the under floor storage in the back.
To build the floor I used some original 30ies flooring I got for free. It came in oxred and shades of green. I decided to go two red one green, same as on the left outside wall. I layed out the boards first to be shure I had enough. Then I layed down vapor barrier and started to cut and nail the boards. It was a little bit tricky on the trp door, as I had to mill out some space for the hinges. I also messed up a bit the gap on the hinged edge inbetween trap door and solid floor due to lack of experience and practice with the milling machine. But after all said edge wont be really visible, as I intend to build a kind of counter along the rear wall.
I really like how the floor came out and I think after some good cleaning, it will look really nice.
Step 19: Front Porch
First I covered the front and the right side of the beams (left was already done when I covered the left wall) and added two more short beams as reinforcement.
Then I cut off tongue and grove of 5 flooring boards with the table saw, rounded the edges with the router, cut them to the right length and rounded the short edges as well.
When I screwed the deck down I left little gaps inbetween the planks, so that the rainwater can run off the deck.
Step 20: Sleeping Den
To take good use ot the ceiling hight, I built a little sleeping den into the top of the shed. The part in the back (over the tool shed) is acting as the roof of the tool shed. During the building time I used it to store extra flooring boards.
But with most of the outside work done I cut down one of the long thick planks and alos built the front part of the den that covers the seating/sleeping area of the "living room". After the boards were up, I covered the floor area with cork to make it comfortable to be up there. I used doublesided tape to hold down the cork, but during the winter I realized that the humidity made it warp. So I probably have to redo this part sometime.
With the cork down I finished off the edges with some angled wood, left over from the old shed and srewes two boards to the left and right just over the horizontal beam to create some storage space.
To access the den I modded a folding attic ladder I got for free. I had to switch over one of the hinges and come up with a simple string and pulley system to hoist the ladder up or lower it.
The kids already love it to be up there. But in summer it probably needs some ventilation to make their stay bearable...
Step 21: Bulleye Windows
I wanted to have some more light in the shed. As there were no suitable windows in a standard shape available, I thought: round!
So I searched for round windows and found someone selling the glass part of washing machine doors. For 10 € I got 6 washing machine doors.
First I want to make the upper windows and only if they do not provide enough light add the lower ones, at least on the left side. On the right side the lower window is set, as behind it will be the composting toilet so some natural light will be very helpful there...
First I needed to do some carefull measuring to get the size of the hole in the wall right and also the inner and outer diameters of the wooden rings that make the window frames and hold the bulleyes in place. Especially the ring that holds the wider part of the glass needs a lip to hold the glass in place and still sit flush to the wall. I also quickly realized that I needed to tweak the circle tool from my router to allow for smaller circles.
When all the measuring and tweaking was done, I screwed the plywood designated to become the window frame to my worksurface and went at it. Make sure to work from the outside inwards! I made the inside ring (wider part of the window) first. Then I mocked up the thickness of the wall and measured the right size for the inner edge of the outside ring (the outer edge has the same diameter as the other ring). I made a mistake there, but more on that later. When I had routed the rings, I rounded the outside edges and sanded down most of the bold green colour to get a similar green as on the door. The outside rings then got a thick clear coat to protect the ply against the weather.
I first mounted the window on the tool shed side. While cleaning out the future sleeping den to get acces to the wall I realized that the planks had seriously shrunken during the hot summer and a lot of gaps showed. So I decided to cover the inside of the wall with some ply I still had laying around. Then I decided on the position of the window, marked the circle and got the jigsaw out.
When the hole was cut, I placed the window and inside ring. When checking outside, I realized that I had not taken into account the thickness of the plywood. Because of this the space inbetween wall, glass and the rings was to big. I adressed the problem by filling this gap with strips ripped of some black used t-shirts I didn't need anymore. The gap inbetween outside ring and glass was then filled and sealed off with silicone. The whole process (minus the ply and the additional filling) was then repeated on the other side.
Step 22: Awning Roofs
To add some protection to the door openings, I added little awning roofs over them. I made them up from leftovers. I had two pieces of corrugated roofing of about 100x50 cm that were the perfect size for this, plus some plank and beam leftovers.
The plank leftovers had about the same size. I marked the diagonal as cut line and cut off the top of the beams at the same angle. Together with some pallet wood this gave me a sturdy base for the roofing and more than enough slope. I had to plan the whole construction in a way that it fitted inbetween the protruding roof beams and kept the door still accessible. I then screwed it to the wall, making sure to hit the inner horizontal beam with at least some of the screws.
I also had to cut off some of the roofing in the upper corners to allow room for trimming off the beams later (see next step).
To finish it off I added some trim were the roof meets the wall. I made it from a piece of roof topping I got together with the last batch of corrugated roofing.
Step 23: Trimming Edges and Corners
To close off all the little gaps on the outside and inside edges, where boards meet beams and other walls, I cut down several pallet boards into 3 cm wide strips. These strips were then used to cover up all those little gaps.
The inside rooftop didn't look too nice as well, as there were still visible gaps between the top beam and the roof cladding. To cover those up I cut some pallet boards at an angle to cover the side gaps and used a third board to finish off the middle. Like this I conveniently created a little channel that I will later use when putting LED lights up there.
Step 24: Furniture: Kitchenette
Originally I planned to build a counter along the separating wall, but then I liked the look of the wall that much, that I didn't want to cover it up. And on the other side, the kneewall didn't look that nice so I decided to build the counter in front of the kneewall.
I got that little yellowish kitchen cupboard for free. I raised it with two boards to get a decent counterheight. For the countertop I used some more of the flooring boards with the newspaper scraps and reduced the counter depth on the right side to get more seating space. Then I rounded all the front edges with a router. The surface was finally sealed with several coats of a clear semi gloss PU coat (same as the separating wall).
The kneewall above the counter I covered up and topped with some more flooring boards. The counter very quickly proved it's practical value at my son's birthday party acting as a buffet.
Later I added some more shelves above to store cups and other small stuff. With that much storage ready I brought some decent tableware in so I don't need to use those paper plates anymore...
Finally I added my two flame gas stove (from my outdoor kitchen from this instructable). Now I can make myself a coffee or a tea while at work or cook a quick meal.
Step 25: Furniture: Foldout Bench
Along the separating wall I added a bench with storage underneath, that folds out to a bed, large enough for two adults.
The seat and backrest are created from the same batch of ply as the frames for the round windows. After a few sketches and a lot of measuring I cut it into one wider strip for the seat (50 cm) and two smaller ones for the backrest (30 cm). Then I screwed a short beam to the kneewall at the desired seating height an d built a little frame for the front. With that fixed it was time to focus on the pull out part.
From my outdoor kitchen I still had left the coaster wheels (IKEA) and I had several angles and hinges on stock from other projects and from the old shed. First I cut one of the OSB roof boards from the old shed to size and put it on wheels with the help of some pallet slats. With the floor height of the box set, I could build the rest of the frame of the pull out so that it sat about 2-3 mm higher than the support frame in front and the beam on the kneewall. Like this it pulls out easy and when the backrest is down the full surface sits flat.
To try it out I fixed the front edge to the box frame with some theatre hinges. To attache the seat to the backrest I used the door hinges from the old shed. The other hinges I bought new. The trickiest part was to attach the hinges that fix the seat to the box, because when the seat is opened the backrest moves slightly forward (geometry and lever movement is tricky sometimes) and I had also to find a position for the seat so that the backrest is angled backwards. This all took a lot of trial and error.
With all that geometry figured out I added some angles as stops to the outside corners of the pull out box and cladded everything with flooring boards. I also rounded all the exposed edges of seat and backrest and sanded the green surface to make it look similar to the faded door.
Step 26: Furniture: Small Bench
To add some more seating possibilities and additional storage, I built a little bench on the small wall between left door and porch. I used what I had on scraps from pallets and flooring boards.
Step 27: Landscaping
To stay within the building rules the shed floor has to be 25 cm or less above the floor level. I acheived that on the tool shed side, but as the ground wasn't level I had to do some landscaping on almost all the other sides of the shed to bring the ground up.
Then, with most of the outside done, I used some of the dirt I dug out for foundations and cellar to even out the ground around the shed again, especially in front of the doors. I also had some gravel and several stone plates left from my foundation work.
So a layed down some gravel first to even out the ground, put the plates on top, so that they sit flush with the edge of the wall and then filled up with dirt around the plates.
Step 28: Composting Toilet
Not started yet...
I plan to build a composting toilet into the right side of the tool shed compartment. But this will get it's own instructable sometime.
Step 29: Solar Power
Not started yet...
When all the other project parts are done I'm planning to put solar panels on the roof to produce enough electricity to have light in the evening/night and to occasionally charge a laptop or mobile. But this will be in another instructable as well...
Step 30: The Little Things - Side Stories
A lot of things happend during or alongside building this shed, that do not fit into one of the above steps.
Documentation: I documented a lot of this build through a smartphone running Stop Motion Studio Pro. I really can recommend the Android App. My experience with the PC-App on the other hand was very dissapointing at the beginning as it didn't work and immediately crashed every time I tried to use it. But then I realized that this only happened, when I tried to import a full project from my phone. When I just imported all the pictures, it worked.
During this build I went through several sets of working gloves. At the moment I'm using set number 5.
To lock the shed, I mounted several latches. Also to hold the doors open when working in the garden, as it is often a bit windy.
Wearing masks sometimes was really a plus and carrying 30 squaremeters of flooring down 100 hundred steps gave me a good workout without using a gym.
As the garden is not far from our home I used the bike and trailer a lot instead of the car to transport tools and materials to the garden.
The half finished shed provided good shelter when we were celebrating our little ones birthdays in 2021/22. We did most of them outside to not make anyone worry about covid.
The newspaper flooring boards was another special. It came from a building close to ours. They had a big water damage and had to pull out the floor of several rooms on two floors. When I saw their ad only a few boards from one room were left, as nobody wanted them because of the paper scraps. The owners were really happy that I took them as they also saw the worth of the boards WITH the scraps.
In the beginning I intended to cover the outer walls with planks from pallet wood, but then shifted toward flooring boards. So I had a lot of pallets and even more leftovers from the pallets I actually had used. So I decided to build a little woodshed from pallets to store all that scrap pallet wood... :-)
Some of the scraps I immediately took to good use to make a fire (several times) and roast some corn or sausages or the occasional banana for desert.
Speeking of fruit: All over the build we always had some garden work to do, but also had good results, especially for making marmelade (apple zucchini for example).
And I several times had little visitors coming by. The occasional mouse, a hedgehog and of course our local fox which is pretty courious and not very shy.
At some point the heap of scrap wood just got too big, so I had to get rid of some. I think I compressed the rear suspension of my car almost to it's limits, when I hauled all that (wet) wood to the local recycling center. But even after that, there is more then enough material left to build other stuff in/for the garden...
And as our plots number is 1A, the shed got its number, made from old licence plates.
Lately my younger son had to build a little house for school and we took good use of some of the scrap wood from the shed.
And in the meantime me and the boys also had our first sleepover in the shed.
Cheers and thank you for reading along until here!
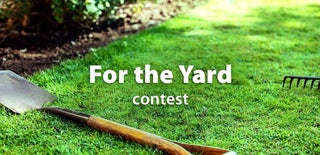
Grand Prize in the
For the Yard