Introduction: A Modular Desk From Steel and Cypress Wood
The Story Behind the Desk:
Because it's my first Instructable, I'd like to give a brief explanation of who I am as a self-proclaimed "maker." I grew up working on whatever projects either of my grandfathers or dad could dream up. One grandfather, "Gramps," is meticulous, a retired orthodontist. His tools are old, yet immaculate. It may take a day to do a project with him, but when you're done, you're done with it for good--or at least until he decides it's time for a little preventative maintenance. The other, "Dude," is constantly busy with projects. His tools are worn and plentiful. I've spent many summers building birdhouses with him or fixing a sprinkler system that always seemed to leak. We spend the time necessary to finish a project and usually finish a few in a day. My dad is remarkably efficient in his work; he always has the right tools and a plan well before the project starts. He's not afraid to google the correct way to fix anything around the house. His habits most resemble my own. While his workshop is more limited, partially because of all of his tools I've lost or ruined over the years, he's ingenious in his solutions and always like to talk through his ideas with me.
After that digression about my support team, it should be no surprise that when I decided that I wanted to learn how to weld the Spring of my freshman year of college, they were on board. While I was itching to try out what the equivalence of a few hours of how-to videos on YouTube could do for me, Dude was reaching out to the consortium of old men, or his friends and neighbors, for tips and an old welder. My dad was reasonably more worried about the engineering classes I was procrastinating from.
The project actually began as a bike frame that I imagined riding around campus. I'd possibly beat my chest and win a few races I had never trained for, you know how it goes. However, a little bit of feasibility calculations proved that building a bike wouldn't be very economical or really that safe for a first time welder. Furthermore, my little brother refused to be the test rider. Eventually, I decided that a desk would be more useful in my future, unfurnished apartment than a bike: practicality is a dream killer sometimes.
Step 1: The Design
I should make a preliminary disclaimer that I don't talk too much about dimensions in this instructable. I apologize, but my design went through so many minor changes that almost all of the measurements changed. I didn't keep up with them at all. Maybe in future instructables I'll be better at writing detailed dimensions; but for right now, the best I can do is accurately describe my process and reasoning.
The design had to be simple in concept because I wanted to finish it over the summer and I honestly really didn't know what I was doing. I knew that I wanted a desk that could be pushed into a table when a few people were over to study and could be used for single use as well. There was not much other criteria. Ideas were thrown around when my friends and I studied together until I'm sure they were sick of hearing about it. After hearing updates on the most minuscule aspects of the design for over two months, I'm sure my girlfriend was about to kill me. Ask her to list the pros and cons of Formica tops, cabinet grade plywood, laminated pallet wood, and jointed wood; she'll be able to tell you more random facts than you want to know (and I'm sure she doesn't love knowing them either).
I began to make a base model on SolidWorks so that I could update the design easier. Ahhh technology. I started with the main desk and built from there. I decided the desk top should be thirty inches from the ground based on table tops and desks I found around my dorm. Oh yeah. I was that weird kid discretely measuring tabletops where I studied. All in the name of research. Then I decided the desk top should be about 40" long from proportions I visually tested on the SolidWorks model. I knew I wanted the desk assembly to push together as a square, so the desk top then had to be 20" wide. I threw in a few drawers and a few pieces of steel here and there, and I was done. I did a few calculations on stress from torque, that I never ended up using, and called it a sound design.
Next came the side desk. It was comparatively simpler to design. The top dimensions had to be 20"x20". My desk in my dorm had a pull-out desk top that extended from the front of the desk to double the writing area I made sure I added one of those to my model. Who wouldn't want more desk space? The answer is me when I am trying to figure out how to attach the sliding desk top to metal. I figured one drawer would be fine in this case.
The cart was admittedly a last resort. The top also had to be 20"x20", and everything kind of fit together from there. The design called for a three-tiered cart with the middle shelf's top equidistant from the tops of the top and bottom shelf. I wanted a file cabinet, but lack of know how and time to consider my options kind of killed that idea.
So I spent some time on SolidWorks when I could afford it until the design changes began to come more slowly. I threw together a few drawings and Bill of Materials for the desk assembly, and I set out starry eyed for my new project.
Step 2: Materials
STEEL:
.75"x.75"x.125"x20' Angle Iron (3)
1"x1"x16 GAx20' Square Tubing (2)
1.5"x1.5"x 14 GA x20' Square Tubing (2)
.75"x.125"x20' Flat Bar
The steel supplier I used only sold the steel in 20' sections, so I spent time making a cut list to ensure that I would use the steel as efficiently as possible. With that being said, I still spent $160 on all of the steel, including the cost of the supplier cutting the steel into sections to fit my car. I was thrilled with my purchase; my wallet was not.
WOOD:
In short, I used two 7"x13'x.75" planks, a 7"x6'x.75" plank, and a 6"x4'x.75" plank of Cypress for the desk. Approximately 8"x10'x5/8" of cedar paneling was used for the drawers.
Along came Dude to the rescue. His friend Mr. Dave, had old Cypress baseboards that he had found stored in his mother-in-law's house. He "traded" Dude for some of the cedar fence board scraps that Dude had and he called it even. All in all he gave me two 7"x13'x.75" planks of wood and a 7"x6'x.75" plank of wood. He also found some cedar paneling that we resawed and planed for the drawers. He was a huge help.
The 6"x4'x.75" plank of cypress actually came from a random workshop I stopped at on my way home from work one afternoon. The man was very nice and even planed the wood for me.
Step 3: Tools
SAFETY:
I'm going to start by saying that I am by no means an expert in safety equipment. However, I wore whatever I could find to be safe and tried to abide by the warnings of the tools themselves. Therefore, use your head and knowledge of PPE to protect yourself. Take a break and read the safety literature that comes with your tools. Losing a finger or eye isn't the cool thing to do just yet.
METAL WORKING:
Chicago Electric 90 Amp Flux Cored Welder with 0.035" flux cored welding wire
Ryobi 4.5" Angle Grinder
Chicago Electric Welding Helmet
Leather Welding Gloves
Cut off wheel
Grinding wheel
Flap disk (sandpaper disk)
Drill with lots of drill bits
Wood:
Clamps. Lots of Clamps.
Table Saw
Circular Saw
Router
Orbital Sander with a few different grits of sandpaper
Miscellaneous:
Tape Measures
Squares of all shapes and sizes
Marking tools (soapstone, pencils)
Wood Glue (Get the good stuff. Titebond III)
Screw Drivers, if you can find one that is bent at a 90 degree angle, it will help later on)
Step 4: Cutting the Metal: Where the Fun Starts
I had way more trouble with this than I needed to. At first, I used a cut off saw that my girlfriend's uncle let me use, but I burnt through a blade fairly quickly and didn't have time to run and get another one. The replacement blade is still in the back of my car (Sorry Mr Johnny!).
Then I tried a hacksaw. I was probably going to finish the project in a few summers at that rate.
So I finally caved: I bought the 4.5" Ryobi Angle Grinder. It was one of the smarter purchases I made during the entire process. I bought a few extra cut off wheels and grinding wheels and set off to work.
I grabbed my cut list and started cutting. Around this point, I took the welding class and realized that the tolerance of my cuts had to include the gap distance for welding. With this in mind, I ground the ends a little less; they did not have to be the perfect miters I was accustomed to with woodworking. However, the better the cut, the less headaches later on, so don't get too careless with the measuring. I measured twice and cut once, the whole shebang. For the angle iron and square tubing, I found that if I used a carpenter's square to mark all sides of the steel and turned the metal each time I cut a side, the cuts were within a reasonable tolerance for welding.
It would probably be a good idea at this point to go ahead and sand the mill scale off the metal before its all put together. I did not. I also spent a lot of time alter on trying to fit a round angle grinder in square holes to clean up rust that so effortlessly avoided me. I did, however, grind the surfaces of the steel pieces about four inches into each side so that the welds would be stronger.
Step 5: Welding: Cue the Disney Music
"A whole new world..."
Welding was like working with wood that you could mess up over and over again and still get a good result. I probably broke tacks to redo sections tens of times. I had to completely cut welded joints apart a few times too. The beautiful thing was that I could just patch areas where the cut off disk wandered with the welder. Sure, the engineering student in me whines about weakening the metal with the stress of heating and reheating, but I can ignore him.
So I sat in my backyard during my off time and set things to square and tacked. Checked square and tacked. Chased off the neighbor's dog so I wouldn't blind her, and then checked square again. And after a few iterations, I finally did my best to lay a bead. They weren't pretty, but they were functional.
I welded the angle iron on the top together first, then welded the legs to the top, then the remaining pieces to the assembly.The angle iron on the top had to be square and the legs attached square to the top. The angle iron for the shelves were a last minute solution to the drawers. This angle iron was mounted so that the drawer bottoms would slide on the top of the angle iron. therefore the top of the angle iron was flush with the steel parallel to the top pieces (that would frame the drawers on the bottom).
As a side note, I did have to set my welder to the highest amperage setting. The beads looked fine at the lower setting, but the angle iron on the cart became dislodged when I subjected it to my weight. Of course this happened when I was standing on it to show off the weld strength. Then, I played the fun game of tracking where on the desk assembly I used the lower setting so I could regrind and re-weld if necessary. One of these places was the top of the main desk. I found it after trying to lift the desk up when I was about to apply the blackening agent.
If I learned one thing about welding that I could pass on, it's to use clamps. The magnets I bought were not nearly big enough to keep the metal square. I typically only clamped one piece of metal down, and checked square constantly, but I still ended up with some pieces that somehow were a little off. That's life (without using clamps).
Step 6: The Wood: Back to Basics
THE TOPS:
Dude's friend Mr. Doug and his jointer/tablesaw combo come into play. It's an awesome piece of machinery that makes the cart it's sitting on look like it will break well before the tool itself.
At this point, there were a few old men in the garage making sure I was doing the wood side of the project right. While working under their watchful eyes was nerve wracking at times, it ultimately proved very beneficial. Each contributed valuable ideas about lining up the cuts and clamping the wood. Plus, it was nice to hang out and talk tools every once in a while.
The baseboards were cut to size before handled further. Three 40" segments and twelve 20" segments were cut after carefully balancing areas where the wood was too rotten and areas that gave the wood character. Another hint here is to not cut the wood exactly to size. I knew better, I really did, I just got blinded by excitement. I had to make adjustment cuts on most of the pieces once they were glued up anyway, so no harm no foul.
The goal was to cut the quarter round off the baseboards and then joint the edges. It mainly just took time; time that no one was really ready to spend on the project. But hey, we stuck it out and all of the boards glued together (for the most part) without gaps.
Clamping was another story. I mistakenly went right for the kill shot. The top of the main desk buckled not once, but thrice under the pressure of the clamps before I clamped two boards perpendicular to the grain. After I removed the clamps, the ends were not lined up exactly and there were a few gaps. I've written it off as character. The two remaining tops and two shelves glued together without a hitch.
THE DRAWERS:
I was pretty worried about the drawers. Despite my best efforts, some areas on the desk were not as square as they could be. So I took measurements of the distance between angle iron at the front and back of the drawer slots and built the drawers a quarter inch smaller than the smaller distance.
The drawers were built from cedar paneling that was ripped to the correct width (the height of the space provided minus an inch) and then planed to expose the grain and limit sanding time. Because any thing that can limit sanding is a wonderful thing. Dude and I broke out his new router table, which had a quarter inch bit set to rout a three eighth inch from the bottom of the drawer, and ran all four sides of each drawer through. Then, quarter inch plywood was cut to size and slipped into the routes on the side for a test fit. Next, glue was added to the joints, and brads were shot in by nail gun to hold the drawers together. Perhaps, this wasn't the most elegant of solutions to the drawers, but dovetails were out of the question at this point due to time constraints.
Once everything dried, I test fit the drawers, and used a Dremel tool with a grinding bit to knock down any welds that got in the way of the sliding action. Then, I cut the remaining piece of cypress to fit each drawer front. After some glue between the fronts and the drawer bodies and some clamping, the drawers were finished.
Step 7: Finishing Things Up
THE METAL:
Oh yes, I was forgetting something--or remaining blissfully ignorant, the jury is still out. The caster wheels. The wonderful things that would stop the question, "Isn't that desk a little low?" The bane of my web research.
I spent my nights this summer looking up caster wheels. My criteria was a three inch wheel with brakes and a threaded stem. The threaded stem was solely because I knew finding a plate caster that fit well on my 1.5" square tubing legs was going to be too big of a headache. For whatever reason, I could not find wheels that I liked. Then, after one last Hail-Mary-type look on homedepot.com, I found black rubber and Nickle plated casters for only $4 each. They would work just fine.
Once they came in, I ran to the hardware store and picked up the nuts that corresponded to the threaded stem. I burnt up a drill bit or two drilling holes through plates that would weld on the open face of the legs and then I welded the galvanized (yikes) nuts onto the plates. There are two huge things wrong with that statement for those of you who may try this project or adapt it in some way. One, welding galvanized metal is a big sin. It releases toxic, yellow green gas that you really don't want to inhale. Two, I mixed two different types of steel. From a materials standpoint, galvanized steel and mild steel corrode when mixed.
Once the final welds were made, I put the grinding disk on my angle grinder and attempted to take down the more obnoxious, ugly welds. Then, I loaded on the flap disks and sanded the mill scale off of all of the steel the angle grinder could reach. Everything the angle grinder couldn't reach, like the angle iron on the tops of the desks, was sprayed with a rust inhibitor.
I bought JAX Blackening Agent because I didn't want my metal to look shiny compared to the wood that had so much "character." I decided I would try it out on a piece of scrap to see what it would do and was more then satisfied with the result. Plus it was easy: wipe on, rinse off.
Then I wiped all of the steel down with the JAX Blackening Agent and hosed it off after about ten minutes.The Louisiana sun stepped in and dried off the metal once I set it in the driveway. After a brief panic attack at the orange rust that covered my previously shiny metal, I attached a wire brush to the angle grinder and the metal looked great.
Then came the really fun part. I began putting the caster wheels on and one snapped off at the stem. It snapped off at the stem in the desk. I had to order a new caster, cut the nut off, take a break before I broke something else, ground the area down, and re-weld a new nut on. Then I redid the finishing process for that area. It was great. The rest of the casters went back on without a problem.
Once the desk was cleaned up by the wire brush, I wiped it down with acetone and sprayed it with Rustoleum Crystal Clear Spray Enamel. Save yourself the time, Satin means Satan. I mean, frosted. I sprayed the entire cart with the satin stuff (I obviously had abandoned the careful testing I did with the blackening agent at this point) because I didn't want a shiny finish on the metal. After waiting a few days in vain for the paint to dry clear, I used the wire brush on the cart again and then sprayed it with the good, crystal clear, stuff. The shine ironically didn't bother me.
THE WOOD:
Cypress wood is soft. It's probably not the best wood to make a desk out of, but being the loyal Louisiana boy that I am, I was committed to cypress as soon as the decision was made to use a solid wood top. My solution to the softness was polyurethane. Coats on coats of poly.
First, I measure the inside of the angle iron of the desk to make sure the wood would fit. For the most part, it didn't. I clamped straight pieces of scrap wood onto the desk tops so that my circular saw cuts would be straight. Then, I sanded the tops with an orbital sander. My main focus was to eliminate sharp edges and areas where glue seeped past the joints. Polyurethane over glue looks much different than polyurethane over wood. I also tried to leave as much "character" in the wood as I could--partially to cover up my other mistakes.
Then, all of the tops and drawers were coated with polyurethane. The desktops got a quick coat of poly on the bottoms and about five or six coats on the tops and sides. I lost track. However, the surface did not show any writing when tested. I waited about a day and lightly sanded the surface between each coat. The drawers got about four coats of polyurethane on the sides and three on the fronts. I was impatient and painted the sides before I had attached the fronts.
Step 8: The Final, Finishing Touches
The time had come to join the metal and wood in some dramatic fusion. I burnt through two more drill bits drilling holes for the 5/8" brass screws through the steel. I spaced out about three or four holes for each side in an effort to curb any warping or movement due to external forces that might occur. Then, I drilled shallow pilot holes in the cypress. Now would not be a good time to put an extra hole through the wood. The screws were actually screws used to install curtains, for those of you who have hundreds of those lying around like Dude does.
Screwing the screws in was one of the tougher parts of the project. Everything seemed to get in the way of the drill or whatever driver I was using. The bottoms of the drawer frames really limited any action I wanted to do to the tops. Luckily, Dude found a screw driver whose head was perpendicular to the rest of the tool, so I was able to hand screw the screws in the more difficult areas.
My mom found the drawer knobs in a furniture store in New Orleans. They were pretty perfect for the job. They were all cast iron and each was a different style than the others. Dude rummaged through his collection of bolts to find matching bolts for each knob. I drilled holes equidistant from either of the sides and 1.325" from the tops of the drawers for the bolts and countersunk the inside holes. I ended up having to break out the angle grinder one more time to trim the bolts so they would fit in length.
And that was it. The desk and summer was done. Sure, I would have loved to put in bolts as drawer stops and maybe put another coat of polyurethane on everything, but that's ok. The desk is not without flaws. There are actually quite a few. Yeah I grumbled, got frustrated, and dealt with a few rude retailers, but I also enjoyed small victories, learned a new building technique (although I'm nowhere near mastering it), and spent a ton of time with my family. And, I did all of this because of some random desk project. I really could not have topped this summer.
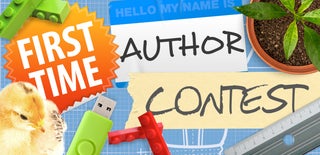
Participated in the
First Time Author Contest