Introduction: A Wide-Body Quadrotor - Designs and Ideas to Build Your Own.
A quadrotor is a type of multirotor aircraft. These aircraft are easier than ever to build. You can start with this machine and increase its capability (and complexity) as you learn more. Your experience, knowledge, and respect for the capability of this technology will increase as you complete this project. Compare the center body of the quadrotor you can build with this Instructable to the other photo of my first scratch-built quadrotor (the wire showing is only the battery connection and would be tucked away for flight).
With the latest electronics installed, calibrated, and configured, this quadrotor is capable of flying a mission defined by you. At this point, some would consider the aircraft a 'drone'. Most flights are from 9 to 15 minutes. The variation in flight time is due to several factors, the greatest of which is the total weight of the aircraft. (Note: To simplify this initial build project, I did not include the GPS option for my vehicle control electronics because it adds complexity that a newcomer can avoid for now) I plan to follow up with another Instructable that will add this feature.
This aircraft, even if equipped with mission-programmable electronics, is still a radio controlled (RC) aircraft. RC aircraft pose certain risks that must be considered. Follow safety practices to reduce risks to a minimum. The two greatest risks are blade/propeller strikes and Lithium Polymer (LiPo) battery ignition (fire!). The largest reported injuries are blade cuts to the hands and arms.
The design of this aircraft attempts to control the risk of a LiPo battery fire by enclosing the battery (or two in this design) in a battery box for protection. The actual implementation of your battery box will depend on the battery you use. I only provide general information regarding the construction of the box. With the design sketch and my photos, you should be able to implement one if you desire.
Blade/propeller strikes can only be completely prevented by mechanical enclosures and fencing methods. This DIY design does not use a protection method for blade/propeller strikes. The operator is responsible for following safe practices including being aware of what is happening in the surrounding areas.
One of the pleasures of a project like this is learning and using creative skills. Creating/making uses cognitive processes and develops/enhances motor skills. Build on!
SKILLS that may be required for this project:
Soldering the connectors of brushless motor and/or electronic speed controllers (ESCs) connectors to wire or to printed circuit boards (PCBs).
Cutting sections of thin plywood
Cutting lengths of thin-wall square aluminum tubing
Drilling and tapping holes in thin-wall square aluminum tubing
Assembling with small screws, nuts, washers, etc.
Possibly cutting screws to a shorter length (if you cannot find items that are short enough)
Painting the parts you have made (optional - not shown in this build)
Step 1: Tools You Need
Who can make anything without tools? If you are an active builder and DIY person, you may have everything (and more) listed below.
The following tools are needed (optional tools can enhance or replace the needed tools):
Screwdrivers: Philips #1 (or another type depending on the fastener you use)
Hacksaw and blades to cut aluminum or plywood
Files: a Rectangular Smooth Bastard, a Round
Hand power-drill and twist drill bits
Drill and tap to make 6-32 threaded holes
Utility knife and extra blades
Metal 'speed square' or other metal 90 degree square
Metal straight edge
Clamps (bar type, C type, spring type)
Optional tools: (can be used with or take the place of some tools above)
Bench vise
Coping saw and blades
Drill press
CNC router
Servo tester (buy one or make your own as discussed later)
Step 2: Buy/locate the Materials (raw)
The materials here are considered "raw" or raw stock; they can do nothing without your effort and skill.
They are stock you will use to make the parts seen in other areas of the build.
Choose the material carefully. Be picky. The better the quality of material you choose, the better your build should turn out.
Plywood should be a flat as possible with no bows or large defects in the surface.
Aluminum tubing should be straight and not dented.
Here is a list of the materials you need to build this aircraft:
Materials (and supplies)
1/8 Birch model plywood -- for the body plates, stack plates, landing gear mount
3/4 square aluminum tubing -- for the motor mount arms (HERE is an Instructable question regarding this material)
1/32 or 1/16 scrap fiberglass sheet approximately 4 inches square (alternate is scrap pcb material) -- for plate reinforcement under screw heads
Sandpaper -- 100 to 150 grit -- for smoothing cut edges
Wood glue -- (optional) for assembling the battery box
CyA glue -- regular or gel type (alternate - 5 minute expoxy) - for securing the plate reinforcement
Nylon wire ties -- 3 to 5 inches -- wiring management and component mounting
Metal 6-32 Philips head machine screws x 25 each; 1/4 inch long. (No need for stainless steel but they look nice )
Optional - paint or clear coat as desired.
Optional - vibration dampening foam rubber
Step 3: Buy/locate the Components (purchased)
Components you will probably purchase:
Quadrotor Components - (see links below for examples)
4 X Brushless motors -- 2820, 2816, etc -- should include wiring connectors and prop adapters
4 X Brushless motor ESC -- 18 to 30 A -- should include wiring and connectors
1 X Power Distribution Board -- should include wiring and connectors
4 x Propellors -- Slow Flyer type, 10x4.7, 2 x CW, 2 x CCW) -- should include hub adapters
1 X LiPo Battery -- 3S 2200 mAh or better capacity -- power connector dependent on PDB connector
1 X Flight Control Electronics -- Builder must choose the type of control electronics they desire.
1 X TRex 700 RC Helicopter landing skids (as used in this build)
Optional: 1 X LiPo Battery -- 3S with 2200 mAh or better capacity -- same as above. This build can use two batteries in parallel
Radio Control Components
1 X Radio Transmitter (TX) -- 6 Channel is recommended minimum; 5 Channel absolute minimum
1 X Radio Receiver (RX) -- match the number of receiver channels to the number of transmitter channels
Links to Example Components (most used in this build)
Link to Flight Control Electronics
Link to PDB
Link to ESC
Link to Motor
Link to Propellors (note you need 2 each, CW and CCW props)
NOTE: The TX will require some type of battery, which may not be included in the price of the TX.
Step 4: Parts You Will Make
Quadrotors have been built from many different kinds of raw material and from adaptations of other items. I classify this type of construction as 'Tube/Bar and Plate' construction (I have identified 8 types of small multirotor frame/body construction).
The parts you will make from raw materials are:
Plate 1 x 1
Plate 2 x 1
Receiver Deck x 1
Stack-up Plates x 1(or more as needed)
Motor Arms x 4
Additional recommended parts (dimensions are provided in the sketch)
Battery box sides x 3
Battery box end x 1
Battery box top x 1
Step 5: The Wood Parts
Use the drawing to mark cut lines on the plywood. Before cutting, use a metal square or other geometric device to confirm your corners are 90 degree angles.
The hobby plywood used in this project can be cut with a heavy duty utility knife. If you use this method, make several cuts using metal straight edge to guide the blade. Cut on a hard surface. Use a cutting mat or cardboard under the wood to keep the blade from cutting into the table or bench.
TIPS that may help you
-- Do not try to complete a single part before moving to the next part but rather get all the parts rough cut to dimension. If you plan your parts carefully you can make fewer cuts and get through the rough stage faster.
Optional Idea - Use a CNC Router
I developed G-code to use with my DIY CNC router to make my parts. The setup and troubleshooting to make a good part was probably longer than it would take me to manually cut the parts, but I learned a great deal in the process.
Step 6: The Aluminum Parts
Take your time. Measure twice for each hole and cut line. Aluminum is more expensive than the plywood, so use the attitude of 'measure twice and cut once'.
-- Cut the tubing to length
-- Cut the motor mount area
-- Mark and drill the motor mount holes
-- Mark and drill the motor lead holes
-- Mark and drill and tap the body mounting holes
TIPS that may help you
- Use a black permanent marker to mark over the area where you will be making a cut or hole.
- To scribe a cut line, use a utility knife. The bright aluminum under the marked area will clearly show through after you scribe the cut line.
- To mark a hole to drill, measure two dimensions as indicated and used the previous scribe method to show the hole location. Then use a center punch (or a large nail if you don't have a punch) to mark the hole describe by the intersection of the scribe lines. As with the cut line example, the hole mark will clearly show through the black paint.
-I made a jig of some scrap flat aluminum pieces and a brushless motor plate. The size of the jig will depend on the plate that comes with your motor. The drawing notes discuss mounting the motor at an angle to the center line of the arm to allow the wiring to exit in line with the center line. This cleans up the build nicely. One issue that can result is getting too much angle and causing the screw heads to foul the sides of the arm. I made relief cuts in the arm sides for screw head clearance. If you think this will happen, just don't angle the motor holes as much.
Step 7: First Test Fit
Mount and align the other two arms the same way. Notice that with only one plate, the assembly is somewhat floppy. Take care to not over-stress the assembly and crack Plate 2. Note: The photo in this step shows the battery box assembled and integrated into Plate 2.
Now mount Plate1 onto the four arms with eight machine screws. You should have something that looks like the picture in this step.
Problems? -- At this stage you will discover how well your holes line up. If everything was well measured and fabricated, all the screws will drop into the motor arms holes properly. If you have a misaligned hole use a small round file to remove plate material as needed. Remove just enough plate to allow the screw to enter the hole without binding.
Step 8: Battery Box -- a Good Option (landing Gear Too!)
Remove Plate 2 from the trial assembly when you are satisfied everything is the best you can make it. You will have to cut slots into Plate 2 if you choose to use the tabs indicated on the sketch. Another option is to leave out the tabs and slots and simply butt glue the box onto the bottom of Plate 2
Begin assembling the battery box onto Plate 2 by reviewing the parts sketch and the photo for this step. It may be easier to place Plate2 on a flat surface and find items to support the walls of the battery box as they are glued onto Plate2. Make extra effort to ensure that the walls are perpendicular to Plate 2.
After the glue for each wall section has dried/cured, you can install the Back plate and Top. The Battery Box adds much rigidity to Plate 2, and the entire quadrotor.
After all the sections have dried/cured, test fit your battery(ies) into the box. The battery will become warm as it discharges while flying. I add a bit of self adhesive foam to the battery to act a cushion and spacer. It is generally not a problem if the battery moves a little in the box.
The landing gear is attached to the bottom of the battery box. A simple rectangle plate is made from the same hobby plywood. The TRex 700 helicopter legs are mounted on the plate with 6-32 screws and nylon inserted nuts (you don't want the legs to fall off in flight). The entire leg-plate assembly is then mounted centrally on the battery box with double-stick foam tape.
Step 9: Mount the Motors, ESCs, and PDB
The goal is to secure the motor to each arm with at least two screws OR secure the motor plate to the arm with at least two screws (the motor plate has been attached to the motor).
Some multirotor builds have you simply use a wire-tie to secure the motor wires to the arm. However, this build hides the wiring inside the aluminum tubing. From a flying perspective, either method will work. I like hiding the wiring to prevent damage in the event of a crash. The drawings and pictures show the entrance hole for the motors wires.
With the arms mounted and the motors mounted on the arms, route the motor wiring through the tubing from the outside to the center of the frame. Now add a tape marker to indicate the motor number. It helps to add an identical marker to the arm. 'M1', 'M2', 'M3', and 'M4' is a good scheme to use. Refer to the documentation for your flight control electronics to determine which motor is M1, M2, etc.
Now mount the PDB onto Plate 2. Make sure the wiring for the battery(ies) can be connected without straining the connections.
The ESCs are mounted between Plate 2 and Plate 1 with nylon wire-ties as shown in the picture. If your drive signals are routed through the board, make sure you have the correct ESC connected to the correct place on your PDB . Marking the ESC and wiring is a good idea. This might seem a silly practice but after many discussions on DIY Drones where I tried to assist builders with multirotor problems, many of the initial failures have been because the ESC and motor connections were mixed up. Take a little time now and make your life easier later.
Step 10: Power Wiring -- Motors, ESCs, and PDB
Your battery is the source of these amps. When combined with volts (the potential energy) of the battery, the result of consuming electrical energy is power (measured in watts). A result of using watts is heat. The same physics is in play when you notice a light bulb is hot to the touch. Your motors, ESCs, battery, and associated wiring will become warmer or even hot with use while flying. This power will find the weakest, poorest electrical connection in your system and cause it to fail eventually or immediately if you do a poor job. If soldering is not in your skill set yet, ask around for a friend with experience to assist you.
Testing the Power Electronics -- DO NOT DO THIS WITH PROPELLERS ATTACHED!
There are two ways to test your power electronics:
1) Use a servo tester to provide a drive signal to the ESC. MAKE Magazine Issue 31 had an article on building your own -- as seen in the photo in this step.
2) Use the Throttle ouput of your RC receiver to drive the ESC.
Either method will allow you to check that you have the ESCs you expect to drive, connected to the motors you intend to drive.
Step 11: Electronics Mounting -- Stack It Up!
Because this section is a general guide, do not consider my design lines to be hard and fast.
When creating these plates, consider the following ideas:
-- More plate area allows you to cut cable paths and other access points.
-- Mount switches and interlocks at higher points on the larger plates.
-- Position components that have indicator LEDs so that you can see them.
-- GPS antennnas are best placed at the highest point on the aircraft, with clear views of the sky (the GPS satellites).
-- Add stiffening elements to the plate if your material seems too flexible. This can help reduce harmonic vibrations.
-- Add vibration dampening materials to components that contain the MEMs hardware (note the foam rubber).
All of the plates are attached by using the four screw holes around the center of Plate 1. I used threaded spacers to separate each plate. This provides easier wiring routing and component access.
Step 12: Signal and Control Wiring -- What's This APM Thing?
This step will completely depend on the type of electronics you purchase. For this Instructable build, I am using the APM2.5 vehicle control electronics (autopilot) from 3D Robotics, 3DR power distribution board (PDB), Spektrum AR6210 6 channel RC receiver, and assorted wiring to form a system.
The APM2.5 uses Open Source software, and is a well-supported flight controller. It will function as a controller for fixed wing, traditional helicopter, multirotor, and 4 wheel (or more) rovers. This product is not the cheapest way to get your quadrotor into the air, but it provides capabilities you can initially use and more capabilities you can use later. APM 2.5 software can function in several modes. The most important for a beginner is 'Stabilized' mode.
HERE is a connection diagram utilizing the 3DR PDB, APM2.5, and a RC receiver. If you are unfamiliar with the wiring and connection types, you might ask for help at a local hobby shop (LHS), from an experienced RC flyer/builder, or by posting a question on one of the discussion forums on the DIY Drones website. People in this hobby are often happy to assist.
In this step it is very important to carefully check and review the electrical connections. READ and understand the connection and other instructions that were provided with your electronics components.
Note -- Preventing Interference:
I prefer to mount my RC receiver(s) in a mid-level area of the electronics stack. This positions my vehicle control electronics farther from the power components. Power components radiate energy, magnetic and electrical, that can interfere with the sensor electronics in the APM. Putting distance between the suspected source and the unintended receiver (the APM) is the easiest solution. Doing this exploits The Inverse Square Law to reduce the risk of interference with the control electronics.
Common mistakes to look for (avoid at all costs!)
Swapping the +V and -V(ground) -- This mistake could cost you the price of the entire control electronics. With most electronics the color of the power wiring is (traditionally) red for the positive power connection, black for the negative (return) connection. Manufacturers *sometime* take the potential for an accidental miswiring into consideration by installing a fuse or another sacrificial component to mitigate this error.
Confusing the Signal (S) wiring -- This mistake usually does not destroy components but rather leaves you puzzled as to why a command with your TX does not have the expected response. Pre-made servo cables have 3 wires. +V, -V, S (sometimes referred to as S+). Pay attention to how your control electronics use these types of connectors.
Step 13: Initial Tests -- the Real Fun Begins
You have worked hard on this build. Now is the time to start seeing some action.
This step will vary totally from builder to builder depending on the electronics that were used. In my case, a Spektrum DX6i TX and an AR6210 receiver were used. The binding process will depend on the brand of TX and RX.
The RC system must work correctly before you setup your control electronics. The control electronics depend on inputs from the receiver of your RC system.
An extensive website is dedicated to the use and application of the APM product -- Do It Yourself Drones.
You will want to look for the Wiki for ArduPilot, found by selecting the path seen in the second photo. You don't have to be a member of the DIYD community, but I encourage you to join. That is where I hang out and help other enthusiasts with getting their tri's, quads, hexes, octos into the air.
Follow the guides under Arducopter (located HERE for the new guides) to learn more about getting your labor of love and interest into the air.
Closing Remarks
It is time to draw this Instructable to a close and thank you for reading it this far. I hope you will consider building a quadrotor and if you get a new idea from this, my second scratch-build, let me know about it.
My next builds will employ two of the popular plastic injection mold arm aiframes: A DJI F550 Flamewheel Hexacopter, and an HJ450 quad. If you are a total beginner and do not have the shop space and tools to build from scratch as seen in this article, I highly recommend this type of airframe. They are tough with a low cost to get into this fantastic hobby.
I want to acknowledge the effort and thank my good friend John Githens for supplying editorial assistance with this Instructable. John and I collaborate on a civilian drone language website DroneSpeak. Thanks John! (Any errors in this article are my responsibility in spite of the efforts of my friends)
-=Doug
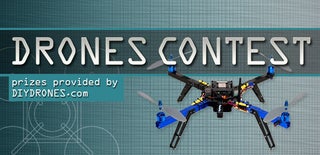
First Prize in the
Drones Contest
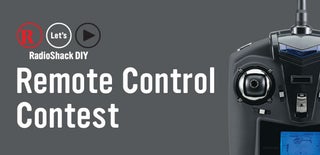
Participated in the
Remote Control Contest