Introduction: Acoustic Panels
I hope this tutorial would be a good reference for those of you wanting to craft your own acoustic panels.
Step 1: Materials & Tools
- Wooden Planks
2 Short (55cm x 5cm x 2.5cm)
2 Long (120cm x 5cm x 2.5cm) - Rigid Fibreglass
1 Slab (120cm x 60cm x 10cm)OR 2 Slabs (120cm x 60cm x 5cm)
There's a lot of literature about what is the "best" density.
Do a little Googling and you'll find most sources quote around 64kg/m3 for panels of this size. - Back Fabric
1 piece (120cm x 60cm)
Make sure it is "breathable" (more acoustically transparent). - Front Fabric
1 piece (155cm x 95cm)
Make sure it is "breathable" AND pleasing to your eyes. - Nails
4 pieces (at lease 5cm long each) - Gloves
A pair - Power Drill
- Wood Glue
- Spray Adhesive
Step 2: Pre-drill Holes
Pilot a shallow hole on each end of the 2 long planks. Be sure to leave a ~1cm gap from the edge. There is no need to drill through. The holes are simply guides for your screws later.
Step 3: Form the Frame
Place the nail in the pilot hole and drill it through, connecting it with the short plank as shown.
Optionally, you may apply wood glue for extra strength.
Work on one corner at a time.
When you're down with all 4 corners, you should get a stable rectangular frame.
Step 4: Staple Back Cloth to Frame
Staple back fabric onto wooden frame. Make sure the fabric is taut.
Step 5: Glue Fibreglass
If you have 1 slab of 10cm thick fibreglass, hooray you can skip this step.
If, like me, you can only get access to 5cm slabs, you can simply glue the 2 slabs together using a layer of spray adhesive.
Step 6: Lay Out Cloth + Fibreglass + Back Frame
Lay the front fabric on a flat, open surface. Position the fibreglass in the center of the front fabric (try to be as precise as possible here to reduce adjustments required later on).
Place wooden frame you made earlier (with the back fabric stapled on) on top. Ensure that the back fabric is laid against the fibreglass.
Step 7: Wrap & Staple
Work on the sides first (highlighted in green) and leave the corners alone for now. This will help you tuck in the corners neatly later.
Ensure you pull the front fabric taut as you staple. This will help prevent ugly looking creases.
Step 8: Staple the Corners
Staple the fabric to the back of the wooden frame.
Step 9: Trim Off Excess Cloth
You may also staple loose ends onto the wooden frame to keep the back side neat, although there's really no need to do so as nobody's gonna see the back view if you put it against the wall.
Step 10: Hammer Flat and Done!
Run your fingers gently along the stapled surfaces, and you may realise that your staples are not flat all the way in. Hammer in any protruding staples for safety during handling.
You are done!
Further work:
To hang it up on the wall, you can drill a few screweyes into the inner side of the wooden frame, and attach steel wires to them. Simply hang it up like a picture frame.
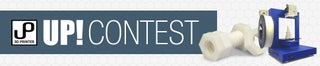
Participated in the
UP! Contest