Introduction: Double Wall Curved Bookshelf
The main instructions are in BOLD - for those of you who just like to get a direction and go for it.
For those of you who like a little bit more detail, look to the fine print.
Alright, so in this instructable we are going to learn the skills needed to create the bookshelf pictured above. It is made of curved acrylic pieces joined together, and supported by metal rods embedded in the wall.This is obviously specifically designed to fit my room, but you can use these same ideas to create a shelf in any form you like. This shape is just one of many ideas that I had for this project, and I may post another instructable in the future (if and when I get around to realizing one of those other ideas).
There are a few different techniques that will be covered in this instructable; we will be learning about:
• Bending Acrylic
• Welding Acrylic with a solvent
• Flame Polishing Acrylic
Once you get these skills down, creating this bookshelf and more complex shapes will be relatively simple.
For those of you who like a little bit more detail, look to the fine print.
Alright, so in this instructable we are going to learn the skills needed to create the bookshelf pictured above. It is made of curved acrylic pieces joined together, and supported by metal rods embedded in the wall.This is obviously specifically designed to fit my room, but you can use these same ideas to create a shelf in any form you like. This shape is just one of many ideas that I had for this project, and I may post another instructable in the future (if and when I get around to realizing one of those other ideas).
There are a few different techniques that will be covered in this instructable; we will be learning about:
• Bending Acrylic
• Welding Acrylic with a solvent
• Flame Polishing Acrylic
Once you get these skills down, creating this bookshelf and more complex shapes will be relatively simple.
Step 1: Materials and Tools
I used 3/8” clear acrylic for my project, which cost me about $200 for a 48”x96” sheet. The plastics store was nice enough to cut it down into the 12” widths that I wanted. I chose clear acrylic because it was the cheapest, and I knew that I could spray paint it whatever color I wanted. ¼” acrylic could have done the job with some bending, but I have some heavy books, and one of my walls had studs on 24” centers, while the other wall had 16” centers. (Hooray for old construction!) The tools that I used were a laser level, studfinder, heat gun (not pictured), tablesaw, and a jigsaw. As you use these tools please use proper safety procedure and equipment, eye protection,breathing mask, etc. The supports are the 3/8“ galvanized rods that you see pictured above.
Step 2: Planning
Planning is key if you want this project to work out correctly. First, I designed my shelf in a 3D modeling program. I used Rhino, but any number of programs can do the same thing. After that, I used the stud finder to locate where I could put my supports. Then I used the laser level to make sure everything was going to be nice and flat. I outlined the layout in pencil on my wall. Once everything was all marked and planned out, it was time to move on to construction.
Step 3: Forms for Bending
For my shelf, I wanted to have two semicircular curves, one with a 14” diameter and one with a 8” diameter. In order to get the acrylic to bend well, you will need to build a form. It doesn’t need to be anything fancy; I just built mine out of some oriented strand board (OSB) I had lying around. Mark out the curve using a ruler and protractor, or any other means that you have available to you, and then cut it out with a jigsaw. Use proper safety procedures with the jigsaw, don't put your hand near the blade as you are following the curve. (I have seen a lot of people do this.) You’ll notice from the pictures that I only cut out 4 of the curved pieces, and the rest are just spacers. The acrylic is stiff enough during bending that you don’t need to support it at all points, so using spacers instead of all curved pieces saves time and materials. Align all the pieces and put them together, and then you will be ready to start bending.
Step 4: Bending
Alright, now it’s time for the fun part, bending! Measure carefully so you know exactly where to place the acrylic. In other words, you need to decide how much acrylic you want above and below the curve and plan accordingly. You may need to remember back to geometry class to find out how much of your acrylic the bend is going to take up. Pi*radius of the curve will give you the length of the curve in this case. Just to give an example, the small curve that I designed was 8” tall, giving it a radius of 4”. Pi times 4 is approximately 12.6 inches, so of my 48 inch long piece, I had 35.4 inches to work with. I chose to have 25” on top and 10” on the bottom, so I positioned the acrylic on the form accordingly. Take off the masking on one side of the acrylic and clamp it firmly to the form, allowing as much room to bend it around as possible. I used gloves to protect the acrylic; it does scratch somewhat easily – a towel or something similar will work as well. Make sure the form is also clamped to a table, very firmly, because you are going to be putting a lot of force on the assembly. Now we are ready to use the heat gun to start bending. In order to heat the acrylic enough to bend, I used the high setting on my heat gun. While the heat gun is not very dangerous, it does get pretty hot, so please use protective gloves and always be aware of what you are doing. Be sure to use the horizontal sweeping motion shown in the video. It heats up the bending area evenly and prevents the material from bending too sharply, like you see in the picture above. We want sexy curves and not ugly bends, as seen in the last picture. As you are heating the acrylic, push on the unclamped end of the acrylic to help it to mold to the form.Be prepared to spend a lot of time on this step; bending the large curve took me about an hour. Once you get it bent far enough, clamp it on the far side and leave it to cool.
Step 5: Refine the Bend
The bend will not be perfect at this point; you can see how the two planes in the top picture are not perfectly parallel. It doesn’t have to be exact, but the closer you can get it, the better. If you feel it needs more bending, put a weight on the top and use the heat gun on the outside of the curve. It involves a little bit of guesswork: heat and bend until it looks good, let it cool and then take the weight off. If it is close enough, move onto the next step; otherwise, just keep trying until you get it right.
Step 6: Cutting the Corner
Your design may involve a corner, like mine. There are many ways to tackle this, but I tried to keep things simple by using a simple curve like you see above. Cutting the corner out is simpler than it looks. Again, use a protractor and a ruler to correctly mark the curve, and then use a jigsaw to cut it out. Use a saw blade that is somewhat thick, otherwise the acrylic will fuse together from the heat of the saw. The jigsaw works well for the curve, just be careful and go slow. However, as you are cutting the long, straight pieces to size, I found that a table saw works best for getting clean edges. With either the jigsaw or the table saw, go slow and be careful. Once you have the corner and the straight pieces cut, you can start joining all the pieces together.
Step 7: Joining the Acrylic With Solvent
When you join the acrylic with solvent, be sure to use proper safety precautions, eye protection and a breathing mask, because the solvent you will be using is hazardous. I used Weld-On 3, and it performed perfectly. Make sure that the edges are sanded down and line them up with each other, ensuring that they are level. I’ve found that elevating the pieces off of the surface below them, as seen in the video, helps keep the underside of the acrylic clean as the solvent doesn’t build up on the bottom. Clean the area around the joint. Slowly dispense the solvent across the joint. The dropper that you see me using is usually available anywhere that sells the solvent and is very helpful. Be sure that it penetrates the joint fully; you can actually see in the video the difference between the parts that have been contacted with the solvent and those that have not. Wipe off the excess and don’t touch it for at least 10 hours, until it has gained enough strength to be moved. Before you join all the pieces together, make sure that you will be able to move the completed shelf to its desired location. I wasn’t going to be able to do this, so what I did was join the pieces into two halves, painted those halves (except for the final joint), and moved them into my basement, where I did the final joining and painting. Be sure you support the shelf properly using cardboard boxes or other means. Acrylic is pretty strong, and so is the joint created by the solvent, but it would not be fun to have something break after putting this much time and money into it. In the picture above, I marked the joints so that you can see the individual pieces that make up the whole.
Step 8: Flame Polishing
If you aren’t painting your shelf, and you want the edges to be clear just like the rest of the acrylic or you just want really smooth edges, you can do something called flame polishing, which is essentially just melting the edge a little bit until it is clear. I used a handheld butane torch for this. (You will want something that reaches 2500 degrees or above.) Sand the edges down until they are very smooth, and I mean very smooth. You should be able to run your finger along it without feeling much variation or texture. You can see this from the video, but then you take the torch and run the flame across the edge quickly, until you see it clear up. Don’t leave it there too long or you will melt and round the edges. Be very careful as you do this and make sure the area is clear of anything that could ignite. I would strongly suggest practicing first with the scrap pieces left over from your cuts. The video is just of a little piece, because I didn’t end up doing this on the shelf. I just sanded the edges until they were nice and smooth.
Step 9: Painting
I wanted my shelf to be somewhat monolithic looking, so I went with a black semi-gloss spray paint. I got both gloss and flat spray paints as well and tested those out on the acrylic to see what each would look like. In the picture above, the semi-gloss is on the left, flat black in the middle and gloss on the right. I would suggest doing test paints to get a feel for both the color and technique. In order to make the color look smooth, hold the spray paint away from the cleaned surface at least 12 inches, this enables you to get an even surface. Allow it enough time to dry.
Step 10: Placing the Supports
Now that we have a shelf, we need a way to keep it up. I decided to be a minimalist and just use galvanized rods to support it. They are small and sleek and, at the right angle, you oftentimes can’t even see them supporting the shelf, creating the illusion that it is floating. I got the rods from Home Depot, pretty cheap, just a few bucks per 3' rod if I remember right. The I used a metal band saw at a local metal shop to cut them down to size, but you can use a cut off saw, or even a hacksaw, and that will get you the same result. I used a portable drill press because I didn’t trust myself to drill the holes perfectly straight into the stud. Drill a small guide hole first, then an intermediate-sized hole, and finally use a 3/8” bit to drill the final hole. I drilled in 2”, which left 10” of my 12” rods exposed, and has plenty of strength for my needs. Go slow and be careful, the drill can jump around if you're not holding it steady. After that, I used a mallet to get the rods into the stud, and believe me they are not going anywhere. If I ever decide to get rid of this, I am not sure how I am going to get these out, they are that tight.
Step 11: Installation
Once you have all the supports in, it is finally time to move your shelf into place. Get some friends to help out, more than you think are necessary – you never know when you are going to need an extra hand somewhere. After the (hopefully) painless process of moving it, you are the proud new owner of a cool curved acrylic bookshelf. Load it up with your favorite reads and enjoy!
I’m really interested to see any designs of yours that come out of this idea. Please let me know and send pictures if you try something along these lines or if you have any questions!
I’m really interested to see any designs of yours that come out of this idea. Please let me know and send pictures if you try something along these lines or if you have any questions!
Step 12: Final Images
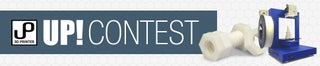
Participated in the
UP! Contest