Introduction: Building a Backyard Rocket Fort
If there is one thing I'm really bad at...it's acting my age. While I could be content to build normal things and do your typical home-improvement projects -- I constantly find myself taking on projects that my inner child assures me are much more important than those boring options anyway. So that explains how, about a year ago, I found myself pitching the idea of a 14ft tall, rocket-themed fort for our backyard to my wife. I'm convinced I only succeeded in that endeavor because of my frequent assertions that it was "all for the kids" (I just left out the part where I may have been including myself as one of those kids).
Somehow I got the green light and since then it's been a fun learning process as I took on the biggest build I've ever attempted. There was a lot of learning, a lot of geeking out on build details, and a lot of long hours in the backyard...but HEY I got there in the end!
I'm no expert. I'm an aerospace geek who refuses to grow up and has a collection of power tools to play around with. As such, in this instructable I am going to talk about what I did, share my 20-20 hindsight, and walk you through the journey I took building this. For those visual learners, I've created several YT videos which I will link along the way that focus on the different parts of the build. Here I've included a fun overview that gives a quick glimpse at the project and the final result.
Thanks for taking the time to read along and share this adventure in building a backyard rocket with me!
Supplies
Ok, so here's the deal. I had to buy a LOT of materials for this build. While I can't promise a perfect accounting, I believe I was able to capture the bulk of these purchases in an excel sheet I used to plan the builds and follow my budget. Along the way, I will include direct links to the things (hardware, special fittings, tools etc) I purchased so you co have that as a reference.
Here's a fun little game, first take a glance at the cost estimate I wrote when I originally pitched the project to my wife (and how I estimated $1000 of wood) and then look at the purchase tracker where I go on to spend $2100 on the build. Now admittedly, much of that is stuff besides wood...but it is also WELL beyond the first estimate I put at $1400 total for the build.
As it turns out, starting a massive woodworking project RIGHT as lumber prices spiked doesn't bode well for your budget. oh well. I'll comfort myself regarding the overrun as I'm sitting in my ...er ...the kids' sweet new fort!
Tools used:
post-hole diggers
levels/rulers/squares
hammer
power drill
nail gun
circular saw
miter saw
paint rollers
table saw
caulking guns
jig saw
spindle sander
router
clamps
When buying wood, I used pressure treated wood that was rated for ground contact on everything except for the outer walls, which I protected from the elements using exterior paints.
Step 1: Design Overview
The first few months of this project were spent developing a design and creating a 3D model of the fort in Fusion 360. That allowed me to think through some of the challenges I'd have to solve as I went through the build process and also allowed me to get a more accurate cut list when it came time to purchase lumber. So I figure it makes sense to take a little time at the beginning to show a design overview and talk about my thoughts as I developed the CAD model.
So I had seen some play sets around my neighborhood that had castle turrets and towers and that is what got me thinking about doing a rocket in the first place. I wanted it to be tall enough for the kids to have 2 levels, but not so tall that the complexity of the build would get out of hand (or require build permits). I also wanted to pick a shape that implied the cylindrical shape of a rocket body, without having to actually build a cylinder. With that in mind, I eventually settled on a hexagon body and 2 levels that were each around 5 feet tall. As I am 6 ft tall (and need to be able to ...er... INSPECT the rocket on a regular basis) I decided to make the top level into a loft that only went half-way across the rocket body interior. That way, I would still be able to open the door and stand upright in the front area before climbing up into the loft or crouching under it if needed. The overall height of the rocket from ground to tip of the nosecone (roof) was to be 14 feet.
As a level of protection for my kids, I planned on adding a cargo net that would attach from the edge of the loft to the rafters of the roof. This would serve as some fall protection should they get too rowdy on the loft level and slip off (side note: that addition came in handy within a DAY of letting the kids loose on the rocket).
Another thing I had to think about was overall size. I didn't want the inside of the rocket to feel cramped, but letting it get too big would run the lumber prices way out of control (you know, on TOP of a pandemic causing them to spike already). For simplicity, I decided that the walls needed to be no wider than a 4x8 sheet of plywood. I figured trying to splice plywood sheets together to make a wall would be a pain and also invite tons of issues when trying to seal this against the elements
oh yeah, that.... I live in a state that sees an average of nearly 58" of rainfall annually. That is just about twice the national average for the USA. This thing NEEDS to be able to handle rain. As much as I joke about making this rocket for myself...I wanted to make a place where the kids could still be outside playing during those rainstorms and not have to feel so trapped indoors. (my son takes it particularly hard when he isn't able to spend a lot of time outside)
A final thing to think about for me was the door. I played with getting fancy hinges that slid the door over to the side so it was more like a hatch opening, but I decided to keep things simple and go with the tried and tested (and more robust) option of fence gate hinges. I designed the door to swing outwards because I didn't want a door infringing on the limited space within the rocket.
Ok so that was more of less the thought process I used when starting this build. Now lets get on to the first step.
Step 2: Grounding the Rocket -- an Overview of the Process for Setting the Posts
Before anything could be done to build UP the rocket, I needed to ensure the fort would have an adequately secure foundation...so that meant digging DOWN. 3 feet in fact. To build the "backbone" of the fort's frame, I used six 4x4 posts, each positioned at the corner of a hexagon. I cemented each of these posts 3 ft into the ground by digging a hole, positioning the post, and filling the remaining space with quickset cement.
While the general idea was pretty simple, I found the execution of these steps to be rather challenging. I tried to do all I could to be consistent and careful about where the posts were placed and how I controlled how straight they were. As it turns out, I still ended up running into issues with things not quite lining up perfectly. This was due to only using a couple of bubble levels and some simple angle measurements rather than laser levels or more precise tools. Overall though, I was able to make things come together ok. I just point this out now because these little issues had a ripple effect throughout the build. What starts off as a little error in straightness or position ends up being magnified with each piece added to the frame. This caused me to make carefully customized cuts in places rather than being able to batch out cuts to the dimensions the 3D model had called for. So basically, being very careful early on pays dividends as you go forward.
Also, a general note: All wood that is (1) intended to be in close proximity to the ground, (2) will be getting wet repeatedly, or (3) will be otherwise exposed to the elements should be pressure-treated. Failing to get ground-contact rated posts and 2x4's for the frame will cause them to deteriorate and fail prematurely
Anyway, read on to see what I did. For those visual leaners, I have a YT video that more or less shows the basic steps I will be describing.
Step 3: Digging a Hole
The first part of setting the posts was to dig a hole. A 3 ft deep hole that was around a foot in diameter.
For the first hole I used a shovel to dig and, well...there is a reason post-hole diggers exist. The shovel made a hole that was far too big in diameter (because of the size of the shovel head and how hard it was to leverage dirt out of a deep hole with a shovel). This would later result in a good amount of extra cement being needed to fill the space back in. The other holes were dug with a post hole digger (lessoned learned!). Despite the hole being oversized, we at least got the opportunity to take fun pictures with the kids! ;) ( silver linings!)
Step 4: Prepping a Post
Each post was cut from a 12' long 4x4 piece of lumber. 3 feet were to be buried in the ground while 8 feet were to extend above it (thereby allowing a full 4'x8' plywood sheet to be used as a wall later on). A bit of extra length on top of each post was used to create an angled cut that would define the roof angle. The total cut length for each post was set at 138.625" (I've included a more zoomed-in shot of the top of a post from my CAD model). The angle on the top of the posts was cut at 40 deg.
As part of the prepping steps, I marked the "ground level" point (where the post should just come flush with the ground assuming a 3ft deep hole). I also marked each of the 3 other places where horizontal 2x4 pieces would be connected between adjacent posts (in order to tie them all together). The position of each of these marks (marking where the bottom face of a 2x4 would be relative to the bottom of the post) were as follows:
1) 36" (ground level 2x4)
2) 80.75" (bottom of 2x4 that defines the fin height)
3) 95.5" (bottom of loft support beam)
4) 125.5" (bottom of 2x4 used for securing top of plywood wall)
(for a bit more clarity, consult the image of the CAD model I included showing each of the cross-beams highlighted in blue)
Step 5: Prepping Cross-beams and Another Post
I cut four 2x4 cross-beams to be 35.3" long each. These were then each attached to the first post with the use of a nail plate and nails. I made sure that the cross beams were (1) in the correct position along the post's length, (2) horizontal, and (3) at a 60 deg angle to the post. (60 deg because hexagons have 120 deg corners and we're bisecting that with each post).
Once I had attached the cross beams to one post, a second similarly-prepped post was attached to the other end of the cross beams. I had effectively created a "wall unit". This unit would be repeated until all the posts and cross beams were installed.
Step 6: Installing Two Posts, and Continuing the Process...
Once assembled, I moved the "wall unit" over the first hole, laid it on the ground, and used it to determine the position of the 2nd hole to be dug.
Then I dug.
Once ready, I raised the wall and each of the post ends into these holes. I used bubble levels to get the posts to a point where they appeared straight and the cross beams were horizontal -- then I started pouring cement. My daughter even joined in and we had a blast!
Next, I positioned (and dug) the next holes for the remaining posts. From this point, things get a little redundant... dig, set post and continue... until all posts are in. The trick was knowing WHERE to dig the holes. I did this by using a pre-cut 2x4 cross beam and holding it against the base of a previously-installed post. Then, after ensuring it was being held at a 60 deg angle, I would mark the spot on the ground where the 2x4 ended -- indicating where the hole needed to be dug. Later, when installing the new post, I would have all the cross beams already attached to the post going in and then I would lower the post into the ground and ensure the the cross beams connected into the nail plates on the previously installed post. By checking that the new post was vertical and the cross beams were horizontal to both it and the adjacent post I could verify that the posts were not leaning. Then it was cement-mixing time again!
After all 6 posts were in it was time to celebrate, and my poor back and arms were very ready to take a LOOOONNNGGG break from digging (somehow I never broke down and rented an auger)
Step 7: Framing the Rocket Body -- an Overview of the Process
With the posts cemented in place and the cross-beams installed to connect them, I continued on to wrap up the framing of the rocket body.
The steps involved in doing this were:
1) Framing the loft support
2) Framing the floor supports
3) Installing the floor and loft deck
4) Framing the door
I'd say the critical part of this section of the build was making sure to adequately support the loft, as I knew for a FACT that my high-energy kids would be bouncing all over that thing. Also, I had to be careful when framing the door to ensure that the 2x4's were all straight and true... that would ensure the the door wouldn't bind up as it swung back and forth.
Again, I have another YT video that covers the steps in this section of the build for those who want visuals to pair with my ramblings.
Step 8: Installing the Loft Support
When I framed the support for the loft; I designed a single, load-bearing beam that would span across the middle of the rocket body and create the front edge of the loft's deck. I created this beam by nailing 2x4's into either side of a post. The front 2x4 was cut to a maximum length of 76.625" and had a 60 deg angle on each end (so the corners wouldn't stick out into where the plywood walls would eventually go). The back 2x4 was cut shorter, to avoid interfering with the cross beams previously installed. I cut it to a length of 73.2". The top of each of these 2x4's were positioned at a height of 59.5" above the top of the bottom-most cross beams (the ones installed at ground-level on each of the posts). This also placed them at the same height of the cross-beams connected to each of the posts earlier.
In order to get the two 2x4's to act more like a single beam, I cut sections of a 4x4 (roughly 6" in length) and nailed them between the 2x4's along the length of the beam. Then, to spread the load from the loft on to the other 2 posts, I hung 2 more 2x4's to connect to the front beam and posts (as shown in the images). These additional 2x4's were cut with a 60 deg angle on one end, and a 90 cut on the other. The max length of each 2x4 was 31.5". Using a 2x4 hanger bracket, I connected the 90 deg end of each 2x4 into its respective post. I then nailed the angled end into the main loft support beam. The two angled 2x4's join the loft beam near mid-span on its rear 2x4. As you can see in the images, I made sure that one of the 4x4 sections was attached where they all joined up.
Step 9: Framing the Floor Supports
After framing the loft, I framed out floor supports. I used a very similar process as I did on the loft. First, I cut two long 2x4's that ran between two opposing posts. Then, I cut a few shorter 2x4's that branched out from the center beams to each of the other posts. This time, however, there was no need to use 2x4 hanger brackets -- I just attached all the 2x4's into the side of each post. The lengths I cut each 2x4 to were:
-- 73.2" (the two long ones)
-- 31.8" (each of the short angled ones)
All of the 2x4's were cut with 60 deg angles on their ends
As I installed the 2x4's, I was careful to keep them all on the same level (no single one protruding above the rest). This would keep the floor flat and smooth when I went to install it later
Then, after I was done attaching all the 2x4's, I filled in all the area between them with dirt. Why did I do this? Well I was hoping for uniform support on the floor so it wouldn't sag or move as people walked over it. As I look back on it, I wonder if I'm not being a little TOO optimistic about the "ground-contact" treatment of each of these 2x4's... I guess time will tell.
Step 10: Installing the Floor and Loft Deck
This next step was really more like installing puzzle pieces. It came down to cutting some plywood sheets so that they could fit tightly between all the posts. To pull that off, I took all the measurements around the perimeter of the loft and floor, and traced those dimensions and angles onto plywood to make the final shapes. When I cut the recesses for the posts, I had to account for the direction in which the plywood would be installed. As I needed the recesses to allow me to slide the plywood into place, in some areas that meant making the cutouts for the posts slightly larger to allow this movement. After cutting out the plywood pieces it was simply a matter of placing them and diving a bunch of deck screws to secure them.
Floor:
Deck:
Step 11: Framing the Door
Framing the door was another pretty straight-forward step, I just needed to be careful that the sides were parallel and perpendicular to the floor.
The sides of the door frame were cut to fit snugly between the top cross beam and the floor. To do this, 2x4's were cut to be 85.25" long. Before screwing them into place, I had to ensure that the sides were equi-distant from the center of the opening. Once I'd done that, I cut two more 2x4's which would serve as a means to set the door width.
In my design I set the door width to be 24", so that was the length that I cut one of the 2x4's to. That shorter section was screwed to the second one I cut; a 2x4 that had 60 deg cuts on both ends and measured a maximum length of 33.5". I made sure the 24" 2x4 was centered on the longer one before screwing them together. This left me with a 24" long piece that was 3" thick, with 4.75" long extensions on either side. (See the CAD image of the piece that I included for more clarity). I stuck this between the 2 vertical sides of the door frame, screwing it into place. I set the top of the door to be 60" from the floor.
Finally, I cut six small 2x4 sections to help connect the sides of the door frame into the posts. Each section was 4.75" long (with a 60 deg angle cut on one end). I used construction screws to attach these sections into the door frame's sides and then into the posts. The top 2 sections were connected into the top cross beam as well.
With that, the door frame was complete! The kids and I celebrated a bit (tho i was a little too tall to really join the party)
Step 12: Framing the Fins
Framing the fins was the last step before moving on to the roof. I created three fins, and attached them to every other wall (there are 6 total walls on the hexagon rocket frame). Obviously you need to position the fins so that none of them end up where you want the door to be.
The fin frames were built using a clipped delta fin shape. The fins were framed to have a max height of 37.3" and max width of 15.75". The angled edge of the clipped delta was (again) 60deg. [hey, when I find an angle I like, I stick with it, ok? ;) ]
As you can see from the images, the fin itself consisted of a vertical 2x4 -- with a 60deg cut on one end and another end that extended beyond the termination of the fin shape (so it could be cemented into the ground). I figured that I could count on my kids to try and climb on the fins at some point so I decided to build them so they would be prepared for that eventuality. This long, vertical, 2x4 was cut to a maximum length of: 38.5"
The 2x4 that ran at an angle along the top of the fin was cut with opposing 60deg cuts on each end and had a maximum length of 20".
I finished the framing with a short horizontal piece that defined the bottom of the fin shape and a middle support piece. The bottom piece was 14.25" and would but up between the vertical edge of the fin and the wall of the rocket body (so no angle cuts on either end). The middle support piece was cut to a length of 29.5" (with a 60deg cut on the top end).
I purchased several small angle brackets to help secure the pieces together. I only found ones that were 90deg angles, so I had to bend a few of them them a bit to get them to the right angle. Additionally, as an on-the-fly change to the design, I added sections from a 4x4 to the bottom of the fin so they would make contact with the ground and add additional support.
In preparation for attaching the fins to the rest of the rocket frame, I had to attach two vertical 2x4's that would serve as anchoring points for the fins. These 2x4's are set between the rocket's floor and lower cross beams, centered between the posts with a 3.5" gap between them (see images). I cut each of the six 2x4's (2 for each of the 3 faces where the fins will be mounted) to a length of 40.5". I secured them with some flat brackets at the top and angle brackets at the base.
The next thing I did was to put each fin in place. This required first digging post holes (only a foot deep this time!) to cement them and then putting the fin between the two upright supports previously installed. I used a flat bracket to tie the bottom of the fins in to the floor of the rocket while I placed screws at an angle through the top of the fin and into the vertical support pieces. This support was increased later with the addition of a 2x4 (32.375" long) that went horizontally across the point where the top of the fin met the cross-beam. This 2x4 connected to the vertical supports, top of the fin, and the posts. (see CAD image with the transparent representation of the cross-piece being installed)
For the fins on either side of the door, I installed additional horizontal 2x4's, each 32.375" long, to create a simple ladder to help the kids climb up to the loft. I set the spacing between each "rung" at roughly 7.5" (width of gap between each).
One last on-the-fly adjustment I made was to include another vertical 2x4 on the wall-side edge of the fin frame. This isn't a structural addition, I just realized that unless I closed up the void that was there my kids would probably use it as their wastebasket and I really didn't want to deal with that. I cut the 2x4 to 31.25" max length (with a 60 deg cut on the top) and slid it into place.
With all that taken care of, I poured cement into the holes I'd previously dug to finish securing the fins.
-------------------------------------------------------------------------------------------------------------------------------
Now, as a special prize for hanging in with me so far, here is a dad joke for you!
hey...where is everybody going?!?!
Step 13: The Blind Leading the Blind -- Framing the Nosecone
OK folks, I'm gonna be straight with you.
While for the most part, my engineering background and past build experience kept me pretty confident on what to do during this build -- that was simply NEVER the case for the roof work I did. While I had some experience shingling a roof, I'd never framed one -- and certainly never a roof on top of a hexagon frame.
I certainly benefited from the fact that nobody was ever going to need to get on top of this roof, and also that the span lengths were all pretty small. I KNOW that the methods I used wouldn't hold up at scale for a real roof. Often times I felt like I was just throwing stuff at a wall and seeing what stuck so I will apologize in advance:
1) Sorry to all those tradesmen and actual roofers who are about to be ABSOLUTELY AFFRONTED by my descriptions of what I did framing this roof.
2) Sorry to those reading along who will be exposed to my crazy thought-process as I try to explain why I did what I did at each step along the way.
3) Sorry to neighbors, who got to see me climbing around 10 feet in the air on this EYESORE of a framing job for a few months while I tried to work out all the kinks. At least I've hidden it away under some shingling now.
So, while for the sake of painting the full story for you I will continue to outline the steps I took to make this roof, PLEASE take it with a grain of salt. In fact, take it with the entire 26oz container of Morton Salt (you can decide whether it be iodized or not)
If you'd like to make an itemized list of my roofing sins and share them with me in the comments, then at the very least I can get some instruction and do better the next time I take on the challenge of framing a roof.
Anyway, let's press on. For those interested in seeing the train wreck happen in full sound and technicolor -- I've created a YT video that goes more into depth on the roof build for your entertainment:
Step 14: Framing the Nosecone
The first step of framing the roof was to attach a 2x4 to the top of each post, which would become the beams that defined the shape of the roof (or in this case: NOSECONE).
I toyed with how to do this for some time before finally deciding on a plan.
I started off with attaching a tie plate to the top of each post. I positioned it to sit flush with the cut face of the 2x4 beam (without protruding above it). I then found some adjustable hanger brackets that I could attach to either side of the posts and adjust their angle to line up with the installed roof beam. I then inserted a 2x4, that had been cut with a 40 deg angle on the end next to the post and a 50 deg cut on the top end. Each 2x4 beam was roughly 55" long --- though to be totally honest, it was at this point I had to start doing a lot of custom cuts to make things work. It turns out that the steps I'd taken to install the posts vertically and evenly spaced had been insufficient and that became painfully obvious at this stage. None of the roof beams ended up being the same and it took a fair amount of tweaking with each one to overcome the inconsistency brought on by my errors with the post installations.
Anyway, as a final step to secure the roof beams to the posts, I drilled a 5/16 hole through the top of the roof beam and through the top of the post. I then inserted a 5/16 carriage bolt in the hole and cinched the two pieces of wood together as I tightened a nut onto the bolt.
After this had been done for each roof beam, I had to create a cap piece to connect the beams together. Looking at the CAD images you can tell I intended this to be a roughly circular piece, but the reality was not that way. For transparency I've included a shot of a carboard piece I had to create as a template to make the VERY MUCH NOT CIRCULAR shape that was needed to connect all these roof beams. (I've also included the reaction shot of any competent roofer after seeing that)
Anyway, let's continue on shall we?
So I made an improvised "adapter" from 1/2" plywood and then centered a circular cut on the adapter, through which I put several construction screws (2 per each beam) to secure it in place. These plywood pieces are more to close up the top of the roof, and not so much for structure. The structure came from the addition of several 2x4 "rafters" I placed near the top of each roof beam. The rafters connected opposing beams to each other so as to create an alternative load path for the roof (instead of passing load through the cap pieces previously installed)
When installing the rafters, I would take a 2x4, clamp it into place on the roof beams being connected, and (after ensuring it was level) trace the edges of the roof beams on to the rafter to indicate where it would need to be cut. I would then cut the rafter pieces and re-position them before screwing them into both sides of the roof beams. I started with the top-most rafters and worked my way down. In that way, I ensured adequate access room for my tools as I worked. To give more room to drive screws through the rafters and into the roof beams, I added sections of 4x4's onto the underside of the beams in the region where the attachment would be made and screwed the rafters into those as well. I repeated this process until I had attached all 6 rafters (installed in 3 sets of 2) between each of the 3 sets of roof beams. I made sure the lowest rafter was still 59" above the deck surface -- this meant that even my oldest could stand comfortably on the loft without hitting her head on the rafters.
Next, I had to add a bracing piece of wood to the corner between each of the roof beams and posts. This was done with 4x4 pieces cut to roughly 40" in length. These braces were cut to match the angle between post and roof beam ( requiring roughly 20 deg cuts on each end). I then used 5" long, 1/4" diameter lag screws to connect the braces to the posts (4 each) and then construction screws to attach the brace to the roof beams (4 each).
Finally, I had to add in some 2x4 pieces between each of the roof beams. This is kind of a play-it-by-ear part of the build and was necessary so that I'd be able to add the OSB sheathing in the next step. The actual placement of these connection pieces, however, wasn't totally critical. If you look at the roof, you'll see that it is split into 6 triangular sections -- I wanted to make sure to get at least three 2x4 connection pieces, evenly spaced, in each triangular region of the roof. I got the measurements for each cut by holding the 2x4 in place, tracing the edge of the roof beams onto it, and then cutting them to shape. One tricky thing about the cut is that, in order to fit between the roof beams I also needed to bevel the edges of each piece at a 25deg angle -- otherwise the 2x4 would protrude above the top of each roof beam. Once I got all the cuts right (and it did take a few tries), I connected them all in place using some more tie plates.
Step 15: Sealing Up the Nosecone
The next task was to use some OSB sheathing to close up the roof.
To do this, I traced the triangular shape between roof beams onto some pieces of cardboard and then transferred that geometry onto the OSB sheets (I had six 4'x8' sheets -- each 1/2" thick). Each triangle was cut so that it came flush with the edges of each roof beam, met the center piece at the top of the roof, and then extended a few inches past the edge of the roof. Extending the edges of the roof slightly beyond the rocket body helps to keep some water off the walls and does a little better job at keeping the water from leaking into the rocket.
Once all 6 OSB pieces were cut, I installed them on the roof frame by driving nails through the OSB and into the 2x4's running horizontally across each of the triangular sections of the roof frame. Once secured, I still had recesses between each triangular section over where each of the roof beams were (see image). To make the outer surface smooth, I cut six 3.5" wide strips from some 1/2" plywood and nailed them to the top of each of the roof beams -- being sure to trim them in length at the point where they came even with the outer edge of the OSB sections previously placed.
While I had closed up the openings in the roof with OSB, at this point there were still plenty of leak paths for water to get into the rocket. As a defense against this, I went around using silicone caulking to fill all the gaps and cracks between the center piece at the top of the roof, the triangular sections of OSB, and the plywood strips over each roof beam. I was careful to ensure that I filled each crack and gave sufficient time for the silicone to dry. I double-checked each seam before moving on to ensure I hadn't missed any gaps.
Step 16: Attaching the Heat-Shielding (shingles)
As an additional layer of protection against the elements, I used roofing shingles on the rocket roof.
For the most part I was already familiar with the process, having done some shingling projects in the past, but even still there were some details that were a bit foggy for me. I'm not totally confident I did it entirely right, but so far it seems to be working -- so there is at least that. Anyway, I'm sure you could point me straight if any of this is way off course:
The first thing I did was to apply a good helping of roll roofing adhesive; a tar-like glue that serves as weather proofing and bonding agent for the asphalt-infused felt roll sheets to be used. I then used the cardboard templates I created for the OSB sections to size and cut out triangular sections of the felt (being sure to cut them over-sized for extra overlap). I placed each of these pieces of felt, going one at a time and securing them with plastic-cap roofing nails. For the top center piece, I cut a large circle with several slits so it could wrap down over the edge and on to the triangular panel sections of the roof.
Once the entire roof was wrapped in felt, it was time for the shingles. Each shingle is marked with a strip to drive the roofing nails into, and an area that is intended to be covered up my adjacent shingles. So starting at the bottom edge, I placed singles all the way up each triangular section -- overlapping them as indicated. I trimmed each as I got nearer to the top and ensured that, at least for now, no shingles wrapped over the corner of the triangular sections. I used ridge-line shingles to cover the gaps at each triangle sections' edges. These ridge pieces have a smaller shape and are designed to be folded over ridges at the top of a typical roof. These worked really well in this application. You can see them installed in the final picture I included.
The very top section of the roof was pretty tricky for me. The flat, circular surface being joined by angled, faceted faces proved difficult to get the shingles to conform to quite the way I wanted (at least without looking like they'd be too prone to getting blown off). In the end I used a tape-like flashing with a metalized backing (flashband) to solve the problem and help secure the shingles. I will admit, it wasn't the prettiest solution...but it has been working very well so far. Since installing the tape the roof has seen heavy rains and tornado-level winds without losing any shingles or leaking. SOOOOO... at least there's that.
Step 17: Deploying the Solar Arrays
A final modification I made to the nosecone of the rocket was to install an external solar array. This array would serve to power the internal lights of the rocket!
The basic idea was to create a method for the kids to turn on the lights in the rocket should they decide to play there past sun-down. The problem was that I knew from experience that the kids would eventually leave the lights on and let the batteries drain with whatever I put in there. So the lighting system I would use needed to be able to charge itself. So I decided to look into outdoor security lights.
I searched around the internet until I found the solar-powered security light I was looking for. For it to work for my application I needed the following features:
1) A solar panel that was not connected directly to the lights (there was a power cable between the solar cell and actual lights)
2) The lights needed to be motion activated
3) The lights needed the OPTION of being switched to a "constant on" mode for more extended periods of use
4) The light needed a sufficiently large battery, so that it could remain on for a good amount of time without losing charge.
5) The lights needed to be bright. I ended up selecting a security light that had a 1500 lumen rating
I finally settled on this exterior security light
To install the light, I first attached the solar cell to a 2x4, angled upwards. I then drilled a hole through the 2x4 and put a washer on the underside. The idea was to attach the 2x4 to the roof in only one spot so that it could still pivot, and the washer would hep facilitate that. I am not sure yet how well this will work, because the trees around the rocket haven't grown enough leaves back to require it: but the idea was that I wanted to be able to adjust the position of the solar cell throughout the year. I figured if it was getting shaded out consistently, I could rotate the solar panel about the roof's center to a better spot. We'll see how that works once I actually have to do it.
Anyway, the next step was to drill a hole through the top of the roof (shingles and all) so that I could pass the power cord of the solar cell through the roof and into the rocket interior. I was then sure to seal that leak path up really well with silicone. Once the 2x4 with the solar panel was secured to the roof, I just had to mount the security light to the rafters inside the rocket and connect to the power cable.
A note on attaching the 2x4 with the solar panel to the roof: that screw acts as a leak path as it penetrates the shingles. So what I did was to coat the screw with silicone, as well as fill the ID of the washer so that any penetration made by the screw would be sealed by the silicone. Will that actually work that way? I dunno. I also imagine that it'll require some touch up with the silicone every time I reposition the solar cell.... time will tell I suppose.
----------------------------------------------------------
At this point, I was 6 months into the build and Christmas was days away. I could often be heard singing:
"I want to build a rocket fort for Christmas, only a giant rocket fort will do..."
or:
"All I want for Christmas is this rocket built, this rocket built, this rocket built..."
and at times:
"I'll blast-off for Christmas. Just count down from three. I'll blast-off for Christmas....it only in my [nerd] dreams... "
Anyway, in that spirit: please enjoy the Christmas-themed update shot of the rocket
...we're getting to the end soon now. :D
Step 18: Buttoning-Up the Rocket Body
With the roof sealed up, now it's time to close up the rocket body.
The process is pretty similar as what was done for the roof: 1/2" plywood was cut to size and nailed to the frame to hold it in place. This time around, the cutting of the plywood sheets for the the walls is much simpler than what was done for the roof. The wall framing was sized so that a full-length 4'x8' plywood sheet could be used with only a slight reduction in width needed. Each plywood panel was cut to 39.5" wide.
When cutting the plywood, I found the Kreg Jig Rip Cut to be an invaluable tool. It helps to get the straight cuts you expect from a table saw but without needing to awkwardly to feed a huge plywood sheet through the tablesaw. As a plus, this jig (that attaches to any circular saw) is much more versatile. I used the jig to cut a 60 deg angle on each of the edges of the plywood sheets (see images)
The only other cut necessary to make on the walls was a groove in 3 of the 6 plywood sheets being used. These grooves were needed so that the plywood sheet could fit around the framing for the fins. I took the measurements from each fin and traced them on to the middle of each of the three walls.
Once I had nailed all the plywood pieces into place, I went around using tie plates to secure the corners. These tie plates come flat, so I had to bend them a bit before they could be used. I installed 3 or 4 on each corner seam--whatever was needed to make sure the seams wouldn't open up.
Ok now let's talk about the door.
Creating the opening for the door was actually rather simple. I simply let the frame to the work for me. I placed a piece of plywood over the wall with the door frame, just the same as if it had been one of the other walls. Then, after securing it into the frame, I used a router and a panel trim bit. This bit has a drill-like tip that allows it to penetrate plywood, and then a cutting edge with a collar above and below it. This allows the panel bit to cut through plywood until it reaches something on the back side that is thicker than the length of the tool. It will then use that object as a guide as it continues the cut. So basically, I was literally using the inside of the door frame as a cutting guide to get a perfectly flush cut-out of the door opening. Here, check out a sped -up version of the process:
Nice and easy eh?
The only things left to do before moving to the next step were to attach a 6" wide section of plywood to the right side of the door opening. This will serve as a mounting point for the door hinges. I size it to be a little taller than the door opening (~ 1.5"). The last thing is to seal up the cracks in the wall corner seams and interior seams where the fins and frame meet with silicone as added assurance that the rocket would remain leak-tight.
After all that, the rocket was really starting to take shape -- and that shape was PRETTY AWESOME! I mean, check out my daughter's reaction to getting to knock down the cut-out section for the door!
Ok, one last thing. I pulled out the left-overs of the flashband sealing tape and applied it to the bottom edge of each wall, I figured that the added protection around the edges of the plywood that would be in direct contact with the soil would be a good thing.
Step 19: Building the Hatch
With a spot for the door cut out, the next step was to build the door.
The door began with a piece of 1/2" plywood, cut to be 28" x 64". Next, I used 2x4's to reinforce the plywood. The lengths of the 2x4 sections were:
58" (x2)
16" (x3)
I placed the two long pieces parallel to the vertical edges, attaching them by driving nails through the plywood and into the 2x4's
Next I attached the shorter 2x4 sections across the top, bottom, and middle of the door. I attached each to the plywood as before, then drove screws at an angle in each corner -- so as to tie the horizontal pieces into the vertical ones.
It can be seen from the images that the the rectangle created by the 2x4 reinforcements was not centered on the plywood sheet that created the outer surface of the door. The rectangular frame was sized to just fit inside the 24x60" opening previously cut out. The extending bits of plywood served as a stop to catch the door as it swung shut. Due to the hinges I planned to use, the rectangular reinforcement frame had to be shifted towards the side where the hinges would mount to to the door (yet still centered vertically on the door). The outermost edge of the reinforcement was placed .5" from the edge where the hinges would mount.
Once all the pieces were mounted, I painted everything with a couple coats of white exterior paint.
Next, let's talk about the porthole.
The porthole was created by first tracing and then using my jigsaw to cut out a circle in a piece of 1/2" plywood. I used a spindle sander to smooth the cut before moving to the next step.
Once I had the circle the way I wanted, I trimmed the plywood so that it would JUST fit inside the reinforcement frame of the door and screwed it into place above the middle support. Then, I used my router with a trim bit to follow the curvature of the circle as I cut that shape into the outer plywood layer of the door. (A trim bit is a bit that has a bearing or some other feature that causes it to follow a surface without cutting it -- while cutting that same shape into another, thinner, piece of wood)
Once I had cut a circle for the porthole, I removed the plywood I had just used as a cut guide and moved on to installing a window. The first step was to paint the outer surface of the door with a red exterior paint and then I painted the cut guide black. I then set to work turning the cut guide into a window frame.
The plan was to use .25" thick acrylic to act as a window. To attach it, I needed to make a recess in the back of the window frame (formerly the cut guide) -- which I did by setting my router bit depth to .25" and routing out the recess. I left a 1" wide border around the square pocket I created (see images). Once done with that, I evenly spaced several holes for screws around the perimeter of the porthole opening.
Next, I cut an acrylic sheet to fit nicely into the recess in the frame (in the images I included you can see the acrylic in place with the blue protective film still attached). Then I clamped the acrylic in place and used the pre-drilled holes in the window frame to drill matching holes in the acrylic (you can't drive screws into acrylic without splitting it)
Finally, I removed all protective film from the plastic and covered the recessed area of the frame with silicone to seal and hold the plastic in place. I also applied silicone around the circumference of the hole cut in it--to keep from letting water get into the space. Once that all looked good, I pressed the frame, plastic, and door "sandwich" together and secured the window frame with screws. I wiped up any excess silicone that squeezed out and let the remaining silicone set.
And there you have it, a hatch with a porthole ... ready for install.
Step 20: Painting the Rocket and Installing the Hatch
Before installing the rocket hatch, it was time to paint the outer surfaces of the rocket. Applying multiple layers of a good exterior paint will add an extra level of weathering resistance to the plywood walls.
There really isn't a whole lot to be said here about HOW to paint so I am gonna take a second to explain WHY I painted the rocket the way I did. One might question my decision to use white paint on a structure that will be a play-fort for kids -- and I see that argument. Yes the white paint is gonna show dirt a lot faster, but the rocket nerd in me just couldn't bring myself to use another color. Launch vehicles are almost exclusively white, and it all comes down to the cryogenic fuel they use. When the fuel you are using boils away at -260 F, you don't want your rocket body absorbing any more heat than necessary. Therefore, white is used due to it's resistance to absorbing thermal energy. Despite that, there is still quite a bit of boil-off that occurs with a white rocket. Here is a clip from a SpaceX launch where you can see a bunch of propellant boiling away.
They must continually top-off the tanks to replace what is lost right up to launch, which can get really expensive...so it's in their interest to minimize that loss.
Anyways, all this to say that rockets are supposed to be white. Let's continue on!
Once I'd painted the rocket body, it was time to mount the door. There really isn't a huge trick to hanging the door, just be careful to mount the hinges into the 2x4 frame of the door and not just the plywood. If you need, additional 2x4's can be added as needed to the door frame to accommodate the placement of the hinges. I used ordinary gate hinges, but went with a design that looked kind of cool.
Once I verified that the door was attached and swinging smoothly, I decided to add a latch.
This part was a bit tricky.
I used a typical gate latch, and attached the latch part to the inside of the door. I installed the metal thing it latches onto to the door frame.
A word of advice, any tweaking and positioning of the latch that you do at this point should be done from INSIDE the rocket. If, for example, you had the latch fully installed and, let's say, the door got swung shut and latched on you while you were outside it... well then you couldn't just reach over the door and open the latch like you can on a backyard gate. In fact, there would be NO way to open the latch from the outside unless you popped the pins out of the hinges, shimmied them lose and then opened the door just enough to slide your arm in and grab the latch that way.
Ask me how I know.
So once the latch was installed, and BEFORE I allowed it to get shut on me while standing outside the rocket (again) I installed one of those wire cables (the ones that allow someone to open a gate latch from the side opposite where the latch itself is installed by pulling a cord). This is done by drilling a hole through the door, passing the wire into the hole and attaching it to the latch. I found that the wire connection clip looked a little flimsy, so I went ahead and tied the wire cable through the hole in the top of the latch to ensure it wouldn't work itself free.
Now the rocket fort is nearly complete! Only a few more steps remain :D
Step 21: Finishing the Fins
Ok, with with the walls finished, the only part of the frame left to cover is the fins. First I had to get the pieces I needed from some 1/2" plywood. To do this I traced out the shape of the fin frame onto a piece of plywood. After cutting out the traced shape, I then repeated the process to make a second. Then, in order to cover the front and top edges of the fin frame, I needed some rectangular strips of plywood. Each strip was cut to a width of 4.5" (3.5" is the width of the 2x4 being covered, plus the width of the 1/2 plywood being added on each side of the frame adds up to 4.5"). I cut one plywood strip, intended to cover the front edge, to an overall length of 27 3/8" (with a 60 deg cut on the top edge). The top plywood strip was cut to a length of 17 3/8" with opposing 60 deg cuts on each side.
After applying several layers of exterior paint to each piece of plywood, the assembly process was pretty straight-forward. To mount the plywood I simply used a nail gun to attach the outer pieces first, followed by the front piece, and finally the top one. As an added measure of weather-proofing, I applied silicone to the edges of the plywood pieces where they joined up -- in order to keep water from getting between them and into the inside of the fin's frame.
I repeated the process for each of the remaining 2 fins.
Step 22: Adding More Viewports
Ok walls are up, the door is installed, the fins are done.... at this point the rocket has really taken shape. However, the rocket was really dark inside at this point as well. While I had a light, that was really intended as a supplement, not the main light source -- the rocket needed more windows.
I designed some additional windows based off the command deck of an imperial star destroyer. These windows were placed on the top level of the rocket, on either side of the back fin (the one opposite the wall where the door is installed).
Let's talk about how I made them:
First, I started off with 1" plywood that I cut to a 27" x 20" rectangle.
Next, I traced out my design to the plywood; clearly marking the areas to cut out and which ones would stay. I've included a dimensioned sketch of my design for reference.
After I had the design sketched on the plywood, I used a jigsaw to cut out the triangular windows and a spindle sander to smooth the cuts.
Next, I used double-sided tape to stick the plywood I'd just cut onto another 27" x 20" piece of plywood, being sure to line them both up. Then I use a plunge router with a trim bit to cut out the triangular windows in the new piece of plywood -- using the cuts of the first piece as a guide. I then was left with 2 identical pieces.
Just as I'd done with the window frame for the porthole in the door, I use a router to create a recessed pocket in each of these pieces of plywood. This recess was .25" deep and would make room for another piece of acrylic to sit flush in that space. I sized the recess so as to maintain a 1.5" wide border all the way around the frame.
After spray painting each window frame black, I was ready to begin installation of the windows. This began by screwing the window frames in position on the interior walls of the rocket. Once screwed in place, I used a router with a trim bit to cut along the interior edges of the window frame to copy that same shape into the walls.
After cutting the windows into the rocket walls, and painting the exposed wood edges white to match the rest of the wall, I was ready to install the window frames and acrylic window. The process was the same as with the porthole: I applied silicone to the recess in the frames as well as on the wood of the rocket wall around the window -- then installed the acrylic. The window frame held and clamped the acyclic while screws were installed to hold the frame and window ( which had previously been pre-drilled with matching screw-holes) and outer wall together. Afterwards I cleaned up any excess silicone and ensured there weren't any un-sealed gaps.
-------------------------------------------------------------------------------------------------------------------------------
Now, you may have noted in my first image here that I added a little more than just windows. I mean, how was I supposed to build a rocket fort in my back yard and NOT deck out the inside? So now that the fort is built ...it's time to make it a ROCKET
Step 23: Let's Geek Out
Ok, so at this point the rocket structure itself is done. Now I could really geek out. Here are the things I added to the rocket to make it feel a little more on-theme:
Cargo Nets
The first thing I did was add a cargo net between the loft and the rafters. Now admittedly, this was also a safety feature as I mentioned before but I thought it would be a fun thing for the kids to hang and swing on. I also added a cargo net on one of the side walls next to door. This, with the ladder rungs I'd added when I framed the fins helped make climbing into the loft just a little easier for my kids. As far as mounting the cargo nets go, I used carabiners and eye bolts to create connection points into the wood frame. In some places I was able to pass the netting directly though the carabiner, but when that wasn't possible, I used paracord to lash the netting to the carabiner. The netting going between the loft and rafters was secured at both the top (to the frame and roof beams) and the bottom (at the back of the main deck beam). In this way that cargo net was able to hold some one up who decided to sit or lean on it.
A Captain's Chair
You simply can't have a rocket without a captain, and you can't expect a captain to fly a rocket without doing it in style can you? So I set out to get a chair that would work for the kids. I wanted something that wouldn't take up all the room in the loft (could be stowed away when not in use), didn't run the risk of getting pushed off the top deck, and allowed the kids to pivot around like a real command chair would. I came to the perfect solution by getting one of those hanging hammock chairs. Since the one I found came with hardware already, all I needed to do was wrap the provided leash around the rafters and secure it with their provided carabiner. When selecting the chair, I needed to make sure the minimum hanging height of the chair wasn't more than 59" (distance from loft to rafter), I also wanted one with a decent max weight (the one I got was rated at 400 lbs)
I let the kids pick out the colors :D
A Sleeping Hammock
For those deep-space explorations, the brave crew would need sleeping arrangements. For that, I decided to get a children's hammock. That way our intrepid explorers could settle in for some shut-eye between each of their adventures. With this hammock (since I wasn't able to wrap around the posts as you would a tree) I couldn't use their hardware. Instead I had to put in my own eye screws in opposing posts on the rocket's lower level and then clip into them with the hammock's carabiners. I oriented the hammock so it stretched across the bottom of the rocket, parallel to the front edge of the loft. I also added an additional eye screw in an adjacent post under the rocket loft so the hammock could be connected to it and converted from a bed to extra seating.
As you've caught a glimpse in these videos, I included a few other things as well but they take a little more explaining so I will dedicate their own page to that. The upgrades left to discuss are:
(1) the engine room
and
(2) the nav controls
Then at the end, just so I can brag about my creative little girl, I show you an upgrade she made for the rocket herself!
Step 24: The Engine Room
In the lower section of the rocket, I decided to add a little something extra and put together an "engine room" from some odds and ends I had lying around.
I had a broken dishwasher taking up room in my shop, so I took the plastic face-plate off of it and used that as the housing for the controls. I re-painted the plastic and buttons to make it look a little more like it belonged. After I had found the face plate I wanted to use, I just had to find a way to mount it. I did that with a piece of 2x4 that I cut so the plastic slid over the top of it nice and tight. I had to trim out some plastic features from the injection molding process so I had a better fit, but after a little tweaking I had something that worked. Adding a few of those command strips along the 2x4, at locations where the plastic housing made contact with it, helped to secure it in place.
Before that tho, I took advantage of my access to aerospace equipment and got some junked pressure gauges from work. I figured these pieces could be the engine "power gauges". I measured each of their stems and drilled holes to match in the top of the 2x4. I then epoxied the gauges into place.
Scrounging around a bit more, I found an old solar-powered lawn light. I stripped the solar panel and connected the wires from it to some AA batteries using one of those battery holder things. I also re-wired the switch on the lawn light to one of the re-purposed dishwasher buttons. In that way, the light could be turned on by pressing a button on the "engine controls".
When mounting the engine controls, I first screwed the 2x4 to the wall of the rocket, then attached the plastic housing and secured the light in place -- I did that in much the same way I had attached the pressure gauges.
As one last fun little addition, I found some cool switches that I could 3D print and mount on the wall. I simply looked up switches on thingiverse and picked one that I liked best. I've included the STL files.
Step 25: The Nav Controls
The rocket wasn't going anywhere without a proper nav computer and flight controls, so I set to work putting something together.
The design of these controls was actually something I asked my daughter to help me come up with. She put together a sketch of some controls and I did my best to bring it to life. It was pretty fun getting her involved in the design process!
Once again I scrounged parts from a broken appliance for this. I used the selector dial and start button from a broken dryer, as well as a metal backplate. I mounted all of these on to a piece of wood that I'd painted black. Getting the control layout took a little figuring. I cut out pieces of paper, taped them in place, and moved them around until I found something I liked. Next, I used a vinyl-cutting machine to cut out the words and graphics I was going to use and began placing them as planned. You can see the step-by-step process in the clip below:
The idea for the nav computer was that one had only to use the top dash to select the destination (I restricted it to locations within the solar system so the kids could still be back in time for dinner), then hit the launch button. Once in flight, the captain could select different speeds as well as use the instrument panel to select from a collection of offensive and defensive tech.
I built the frame for the nav computer with some boards that I connected to a couple of wooden braces. These braces were roughly 30 deg from vertical and after attaching some brackets to either side, I was able to mount the assembly to the wall.
Because a Nav system isn't complete without flight controls, I 3D printed a yoke that I found on thingiverse. I linked the files below. After painting some extra details and decorations on it, I had to mount the yoke to the nav controls. I did this by using a retractable key ring to connect the yoke to the control board. The first step was to remove the belt clip, then very carefully remove the key ring. When I removed the key ring I tied some thin wire through the chain so that I could retrieve the end of the chain in case it got pulled into the housing. Next, I glued the key ring on to the back of the yoke. While that dried, I drilled a hole through the face of the control board. Very carefully, and with the help of the attached wire, I fed the chain of the retractable key chain holder though the hole. I then removed the wire from the chain and re-attached the chain to the key-ring ion the yoke (once the glue was dry). And there you go!
When needed, the yoke can be pulled forward towards the captain's chair. When stowed, the yoke retracts back to its spot in the corner of the nav controls board.
Step 26: Bonus: Even the Kids Are Getting Into It
Ok, so if you would allow me to indulge in a little side-tangent...
This little project doesn't directly connect to the rocket build, but it did come about because of it.
I know that I'm probably investing too much money into what some might deem a waste of time...but I have always done these big, fun projects so that my kids can get inspired about taking on projects themselves. If they see me just letting my imagination guide, I hope they will learn to do the same. And then, when they see me pull together some out-there project... I hope they will see that just cuz something sounds odd doesn't mean it can't be done.
This little project my daughter did is a small realization of that hope for me.
So one day we were out walking and my oldest saw a piece of discarded plastic: a broken tray from a printer. She immediately commented that she thought it belonged in the rocket. Curious, I asked her what she thought she could do with it. What she saw was a tablet/control panel for the rocket where I had only seen plastic. She brought it home and set to work designing it. She grabbed some paint and made a "screen" and filled in the circular depressions on the plastic with various colors to make the tablet's buttons. Finally she decided to draw an image of the rocket in flight on the screen. She practiced a few times and then drew it on with some paint markers she has.
The final result is 100% her creativity: taking a discarded scrap of plastic to being a command tablet for the rocket fort! It was so great to see her at work, and I'm looking forward to seeing more such projects from the kids over the years with regards to the rocket fort (and whatever crazy thing I take on next!)
Step 27: Final Touches and Final Thoughts
Well, After a year of designing, building, figuring, and sometime just blind guessing.... I got my way to the finish line!
To celebrate the occasion, it is time to christen the rocket:
My sister, a talented graphic artist, created decals for the rocket and issued its identification number:
Behold! the ILS-24601 (Imagination Launch System). Fabricated and flown by the WILCOX Space Agency.
She's a modest ship, but she's got it where it counts!
Now that the project is over, and I have time to look back over it.... I had an absolute BLAST! I learned a lot along the way. I think the only things I'd want another shot at are: managing the placement of the posts as well as the framing of the roof. I think it all would have been much smoother had I dropped the money on real laser levels so I could better check the positioning of the posts. Also, I feel like I was probably cheating my way through with a small roof, I probably should dig into more research on how roof trusses and posts are joined in real construction. Only having 5ft spans on any of the beams I put in meant I had a LOT more forgiveness to get away with some of the things I did that weren't exactly "correct". Is there anything gnawing at you about what I did? Anything I didn't touch on that you're wondering about? Let me know! I'm interested to learn too so feel free to drop some tips.
Thanks so much for reading through this and hopefully I see you in the next instructable I put together. Who KNOWS what it'll be next time. lol
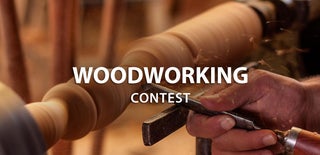
Grand Prize in the
Woodworking Contest