Introduction: Aeroponic Microgravity Planting System
This is a Professional entry in the NASA Growing Beyond Earth contest by Sophie Bandurski, Molecular Biologist and Daniel Sarafconn, Robotics Engineer.
When plants are exposed to microgravity there is a myriad of stresses, such as hypoxia and oxidation, that negatively affect growth and development. While other space agriculture systems like Veggie and Advanced Plant Habitat have grown lettuce aboard the International Space Station (ISS), these systems do not adequately account for such stresses and therefore need to be improved upon. With this in mind, we have designed an aeroponic growth chamber that considers how plants respond on a physiological and molecular level to microgravity compared to Earth to successfully grow plentiful, robust crops aboard the ISS. Because we have built our machine with solid astrobiological research in mind, combined with simple yet innovative engineering, it prototypes the necessary modifications that future growth chambers could include to successfully cultivate lettuce and other produce in space.
Why aeroponics? In the 1990s aeroponics was utilized to grow Asian beans in space in order to evaluate its feasibility in providing life support for long-term space missions. While hydroponic technology has boomed, especially as an alternative method for growing compared to soil in space, the benefits of aeroponics over hydroponics and classic soil method are greatly overlooked. Issues with soil, for example, include improper root aeration, meaning that the plant has less oxygen than is required for mitochondrial respiration which ultimately corresponds with the aforementioned oxidative stress response. Oxidative stress is especially crucial to consider because Reactive Oxygen Species (ROS), while a normal part of cellular metabolism, have been shown in both proteomic and transcriptomic studies to compromise cell wall integrity and attenuate root flexibility, leading to cellular and physiological damage. Secondly, soil lacks sterility and harbors both aerobic and anaerobic bacteria that create a gradient, altering how much oxygen the soil is receiving. Finally, soil provides uneven water distribution. These negative cumulative effects support the decision to use aeroponics which utilizes a sterile, nutrient-rich mist and gives the plants plenty of room to breathe and thus optimally proliferate.
While hydroponics can be beneficial for ground-based systems, it is not the best option for growing plants in microgravity because plants are still grounded in media that also does not allow for proper aeration. Soil and hydroponic growing share many of the same problems, with one characteristic especially unfavorable: disease. In a 2002 NASA article, professor Cheryl Nickerson states that: “When humans are in space, there appears to be some compromise to their immune systems. This suggests a higher risk of infection could occur in flight.” Because we know that microgravity weakens plants, it can be deduced that any microbe that goes into virulence overdrive could propagate and easily kill plants. However, aeroponics is a sterile alternative, reducing the impact of disease while in microgravity.
If you have any questions regarding supplies, construction, 3D files, sources, etc. please feel free to contact us.
Supplies
- 25mm Sq Extruded Aluminum Profiles
- 25mm Quarter Round Extruded Profiles
- Arduino Nano
- Small Compressor
- 0-100psi Pneumatic Regulator with Pressure Gauge
- Pneumatic Solenoid Valve
- Tubing
- Various Pneumatic Fittings
- 12V Power Supply
- MOSFET Modules
- Various Lengths of Wire
- 1 Liter Soda Bottle
- 3 Liter Water Bladder
- 0.3psi Relief Valves
- Rockwool
- Aluminum Foil
- 1/16" Thick Plastic Sheets
- 2" sq x 1/16" Thick Aluminum Tubing
- 2" sq Vinyl Tube Caps
- Full Spectrum Adhesive-Backed LED Strips
- Fertilizer
Step 1: Frame Construction
Per the spatial constraints of the contest, the frame was constructed as a 50cm cube consisting of two squares of 25mm square profiles (the "front" and "back") connected by four quarter round profiles with the rounded sides facing inwards. The rounded surfaces serve as the mounts for the lights. The front and back squares each have a centered vertical column supporting the planting manifold. The front column is also removable, allowing the planting manifold to be removed accordingly from the frame for planting and harvesting.
The lights are adhesive-backed waterproof full-spectrum 12V LED strips with each strip affixed to one of the quarter round profiles that are all wired together. The wires are routed along the frame to the side which becomes the electronics panel, and zip ties were used to secure the wires. While much information can be found touting the use of only red and blue light to grow plants, current literature suggests that plants do in fact grow better in full-spectrum lighting. Despite the fact that red and blue wavelengths match the peaks in the absorption spectrum of chlorophyll, additional wavelengths affect accessory pigments within different absorption spectra also and are therefore essential to plant health.
Step 2: Planting Manifold
The heart of the design is the planting manifold that was constructed from a 2" square x 1/16" wall aluminum tube. This tube is located in the center of the cube where it is supported by 3D printed brackets mounted on extruded aluminum profiles on each end. Since the longest dimension of a square is its diagonal, it was determined that the most effective use of space in microgravity would be for the plants to grow outward from a central manifold towards the corners of the square. Since there is no "up" or "down" in microgravity, it does not matter that the plants will be growing in four different orientations. By growing outward from the center as opposed to inwards towards the center, the plants have room to get wider as they grow taller without becoming overcrowded.
Based on the average size of fully grown "Outredgeous" Red Romaine Lettuce, it was determined that three evenly spaced plant pots would be in each side of the manifold. These plant pots consist of 3D printed baskets filled with rockwool mineral fibers embedded in the manifold. Holes were drilled in the manifold and the 3D printed pots were designed to snap in for easy installation and removal. Rockwool mineral fiber was chosen because it is an established alternative growth medium that is used in aeroponic systems. This material is low weight in comparison to soil-based systems and allows for proper support from seedling to maturity.
Each end of the manifold is sealed with a vinyl cap. The end of the manifold that is considered the front has holes in its cap through which the atomizer nozzle is inserted. The opposite end of the manifold has holes drilled in it for 0.3psi relief valves. These valves separate the atmosphere of the interior of the manifold, or "Root Zone," from the exterior "Leaf Zone" between mist cycles while allowing venting into the Leaf Zone during mist cycles. By venting into the Leaf Zone on all four sides, mist cycles not only refresh the atmosphere of the Root Zone, but also refresh the atmosphere of the Leaf Zone and ensure adequate humidity is maintained in the Leaf Zone. By positioning the nozzle at one end of the tube and the relief valves at the opposite end, the air-water mist flows from end-to-end completely refreshing the atmosphere of the Root Zone during each mist cycle.
It proved difficult to locate an appropriate COTS atomizer nozzle; therefore, a custom nozzle was designed and 3D printed. A test of the nozzle can be seen below. Modern aeroponics falls into two categories: low pressure and high pressure. Low pressure systems are primarily used by hobbyists and home-growers for their simplicity and ease of construction. High pressure systems are considered more effective due to their ability to create a mist with a finer particle size. High pressure aeroponics was developed by NASA and works by forcing high pressure water through an orifice to create a mist with an average particle size of 5 to 50 microns, which was found by NASA to be the optimal size for aeroponics. Given the unique problem of inadequate root aeration in microgravity, a new approach to high pressure aeroponics was attempted which would not only create water mist, but create an air-mist mixture that simultaneously waters and aerates the roots. Rather than pressurizing the water and forcing it through an orifice, pressurized air is fed into a dual fluid nozzle such as those used in a paint sprayer. While the nozzle itself is not a new invention, there is little to no literature indicating its application to aeroponics. This is most likely because air circulation is less of a problem in Earth-based aeroponics. This type of nozzle capitalizes on the Venturi effect whereby as the nozzle constricts the flow of air, its velocity increases and its pressure decreases. The pressure drop is enough to siphon water from the bladder into the nozzle without the need for an additional water pump.
When the water is introduced to the high velocity air stream, it is atomized. While it is difficult to measure or estimate particle size without advanced equipment, flow calculations show that air velocities of Mach 0.5 (or half the speed of sound) can be easily achieved in a nozzle this size. Research into this type of nozzle indicates that these velocities would be sufficient to create a mist particle size within the 5 to 50 microns discovered by NASA to be optimal for aeroponics.
Step 3: Utility Panels
With the plants growing outward from the central manifold towards the corners of the cube, the triangular spaces between the plants on each side of the cube are utilized for the controls and mechanical components of the aeroponics system. Each of the four sides of the cube is dedicated to one part of the aeroponics system. These four panels are: Electronics, Water, Primary Pneumatic, and Ancillary Pneumatic. Pictures of the panels, as well as a circuit diagram and pneumatic diagram can be seen above.
Electronics Panel
This panel contains both the power and control systems. For power, a 12V power supply is used. For the prototype, the power supply operates on US standard 120V 60Hz AC. On the space station, the power supply would be a DC-DC converter to supply 12V from the Station's internal DC power. Since cooling by air convection does not work in microgravity, a power supply with a temperature-controlled fan was used. For safety, the power supply also has built-in over-current protection, over-voltage protection, and over-temperature protection. Additionally, even though the electronics are in an isolated compartment, they will necessarily be in close proximity to the water mist and therefore a GFCI outlet is used as yet another failsafe.
Control is achieved with an Arduino Nano. Really, just about any microcontroller can be used, but the popularity and simplicity of the Arduino platform makes it a convenient prototyping tool. While the Arduino Nano is capable of running directly off 12V, its internal linear regulator would be dissipating a lot of power to regulate the 12V down to 5V and therefore would generate a lot of heat. To avoid this, a more efficient method is used. A buck converter reduces the 12V to 5V at high efficiency and creates minimal heat. Since the outputs of the Arduino are designed for 5V logic, not high-current switching, external MOSFET modules will be used to control the lights and solenoid. These modules allow the 5V low-current outputs of the Arduino to switch to the 12V high-current of the lights and solenoid. Relays can be used instead of MOSFETs, but there are several benefits to using MOSFETs. Unlike relays, MOSFETs do not require continuous current to remain on, meaning lower power usage and therefore less heat generation. MOSFETs are also capable of fast switching which means a PWM can be used to control the intensity of the lights. The purely solid-state nature of MOSFETs as opposed to the mechanical nature of relays means there are no moving parts to experience mechanical wear. While a small transistor such as those found in a modern computer processor may be susceptible to radiation, the relatively large size of the power MOSFET's gate means that even if radiation knocks loose a few electrons, the charge will be much too small to affect the state of the MOSFET.
This simple yet effective control design leaves plenty of room for further development. In fact, several vacant IC sockets connected to the Arduino's I2C bus and GPIO which were used during development can be seen in the picture below. The extensibility of the Arduino platform allows for the easy incorporation of a wide variety of sensors and user interface devices.
Water Panel
This panel contains the refillable 3L water bladder. Given the reduced water requirements of aeroponics, 3L of water will allow for extremely long periods of unmonitored operation before refilling becomes necessary. The drinking nozzle of the water bladder is replaced with a push-to-connect tube fitting for connection to the atomizer nozzle. The use of a soft-sided bladder rather than a rigid sided container is critical due to the unique challenges of microgravity. On Earth, the higher density of water compared to air means that water will always situate in the bottom of a rigid container, so placing the outlet at the bottom of the container is sufficient to ensure that you will always get water out of the container before the air pocket is reached. In microgravity, there is no "bottom" so the water and air will indiscriminately float around the container, making it impossible to reliably get only water from the container. By using a soft bladder, the container collapses as it drains so there is never an air pocket inside the container.
Primary Pneumatic Panel
This panel contains the equipment for creating the compressed air supply for the atomizer nozzle. This system consists of a compressor, an accumulator, a regulator, and a solenoid valve. Since both the compressor and accumulator take up a significant amount of space, the accumulator is located on a second, ancillary pneumatic panel.
Finding a compressor small enough to fit in the cube presents a unique challenge. Initially, a portable tire inflator was used. This had the benefits of a small size, 100psi capability, and met the 12V power requirements; however, this device proved much too loud to operate indoors. Experimentation with this compressor did show that pressures as low as 30-40psi would be sufficient to operate the atomizer nozzle. The compressor used in the final design is an airbrush compressor that is significantly larger than the tire inflator, has a maximum pressure of 60psi, and is significantly quieter so it can be run indoors. While sufficient for a prototype, this compressor is still not ideal. The seemingly perfect technology does however exist. It is possible to make a compressor that is simultaneously small, quiet, and capable of creating high pressure using a conical screw design such as the Vert04 developed by Olly Dmitriev. According to press releases for the Scottish company Vert Technologies, this technology is in fact at this time being developed for use in satellite cooling system compressors for the European Space Agency and the British Ministry of Defense.
The compressor connects to a T fitting. One branch goes to the accumulator and the other branch connects to the regulator. The compressor is capable of reaching 60psi. The regulator reduces the 60psi from the compressor to the 30-40psi required for the atomizer nozzle. Standard pneumatic tubing and push-to-connect fittings were used.
Airflow to the atomizer nozzle is controlled by a 12V solenoid valve. When the valve is closed, pressure builds in the accumulator until it reaches 60psi. When the valve opens, this stored air is released through the nozzle. Wiring for the solenoid is routed back along the frame to the electronics panel.
Ancillary Pneumatic Panel
As stated in the primary pneumatic panel section, this panel contains the accumulator portion of the pneumatic system. The accumulator itself is simply a 1L soda bottle. These bottles, designed for holding pressurized liquid, are capable of holding upwards of 100psi. At the 60psi output by the compressor, a compression ratio of approximately 5 is achieved and therefore the bottle holds roughly 5L of compressed air. A vented manual shutoff valve is connected to the accumulator to allow venting of the compressed air in the event of system maintenance.
Step 4: Dividers and Exterior Reflective Sheathing
Each of the four segments of the Leaf Zone are enclosed by reflective dividers. These dividers separate the light sources of the segments so that each plant only sees light from "above." The spaces between these dividers are where the Utility Panels are located. These areas, which are otherwise unused as growing area, are therefore utilized for the systems sustaining the plants. This results in maximum usage of the allotted space.
The exterior of the cube is also covered in reflective sheathing. This effectively separates the interior lighting from the lighting of the surrounding environment, allowing an isolated growing environment in which light intensity, length of day, percentage of daylight. These factors and other growing parameters can be tailored to the optimal growing conditions of the plants inside regardless of the light cycle of the spacecraft in which the cube resides. This sheathing can be made from aluminum foil which is inexpensive, widely available, lightweight, and opaque. A more high-tech version would be aluminized kapton/mylar film like that used on the Lunar Lander.
Step 5: Programming
A timer interrupt was utilized to update the light and check the mist conditions at a rate of 1Hz. While much faster speeds are possible, there is no benefit in checking on the plants a million times a second versus once a second or less. While the Arduino framework provides convenient delay() and millis() commands, these were avoided since they are based on a timer which overflows after approximately one month. Since the growing period of the plants exceeds one month, this could result in an undesired condition at the time of overflow.
The solenoid is controlled by a function which, using the aforementioned timer interrupt, turns it on for two seconds every five minutes. This timing is based on Earth-based aeroponics systems and is fully adjustable.
The lights, also updated by the 1Hz timer, can be programmed with length of day, percentage daylight, minimum intensity, and maximum intensity. This allows for the design of an optimal light schedule including adjustable day/night period and fading on and off to simulate dawn and dusk.
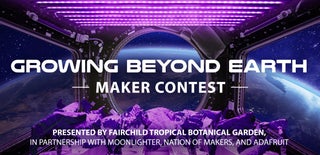
Runner Up in the
Growing Beyond Earth Maker Contest