Introduction: Affordable 2 Way Speaker Cabinet
The idea behind this project was to build a pair of speakers to use as monitors in my mini home studio, the cost should be less than comparable monitor speakers.
It started with the selection of low cost and relatively good performing woofers and tweeters. I chose a pair of MCM Electronics part number 55-2971 (8" Woofer) http://www.mcmelectronics.com/product/55-2971 for $27.77 including shipping, and a pair of Pyramid Tweeters (TW-12) that I bought in ebay for $6.99 shipping included.
The woofer specifications are: Operating Bandwidth: 50Hz ~ 6KHz, Power Handling Capacity of 70W, and RMSSensitivity (1W/M): 89 dB. The tweeters specs: Operating Bandwidth: 3.5kHz ~ 30kHz, Power Handling Capacity of 200W and RMSSensitivity: 92dB (1W/M). They match up well, having to decrease the response of the tweeter by 3db for a flatter frequency response of the speaker as a whole.
Other chosen design specs:
- Volume of the box: .55 ft3, based on the recommendations of one reviewer of the speakers. Small enough that makes sense for my application, while keeping an acceptable low freq response.
- Sealed Cabinet: Easier construction. More forgiving in terms of dimensions. Up to a 10% of error in size would not affect the box freq response as bad as in a ported cabinet would.
- Construction material: MDF. It is Low cost, sturdy, easy to work with, and neutral in terms of frequency response.
- Impedance: 8 Ohms
Tools:
- 1/4 In. 2.4 Amp Trim Router
- Jigsaw
- 3/8 Reversible Drill
- Set of screwdrivers
- Pliers
- Utility knife
- Scissors
- Clamps and Corner Clamps
- Drill bits, straight router bits (1/4 in., 1/2 in.), flush router bit 1/2 in.
- Portable Work Bench
- Soldering iron
- Ruler
- Pencil
Materials (for 1 speaker):
- 2 shelves 3/4 in. x 12 in. x 4 ft MDF
- 2 sheets Wood Veneer. 14.5 in. x 40.5 in.
- 5/8 in. Wood Square Dowel
- Sand Paper different grits (80, 120, 150, 220)
- 0000 Steel Wool
- Wood Stain, Wood Polyurethane finish
- Paint brushes, cotton rugs
- Wood glue
Electronics:
- 8" Woofer - MCM Part #55-2971
- Piezoelectric Tweeter - Pyramid TW-12
- 1 uF non-polarized capacitor
- 1 x 100 Ohm resistor 2 Watt
- 1 x 50 Ohm resistor 2 Watt
- Terminal Strip (for the high pass filter)
- Speaker connector
- Speaker cable 4 ft
Miscelaneous:
- Wood screws
Let's get started
Step 1: External Dimensions Given the Internal Volume
To calculate the dimensions I used a free online application called Speaker Box Volume calculator http://www.diyaudioandvideo.com/Calculator/Speaker... ). The external dimensions I came up with for a .55 ft3 box are:
- Width: 11.5 inches
- Height: 16.5 inches
- Depth: 8 inches
- Wood Thickness: 3/4 inch
- Battens: 1/2 inch
Note: Other ratios between the 3 parameters will also provide the same volume.
Final dimensions for the sides, front, back, top and bottom follow:
Material: 3/4 inch MDF
- Sides: 2 16.5 x 8 inches
- Front and back: 2 16.5 x 10 inches
- Top and Bottom: 2 10 x 6.5 inches
Step 2: Buying the MDF - Cutting Layout
With the dimensions calculated in Step 2, a 3/4 in. x 24 in. x 4 ft MDF board is enough for 1 speaker.
The price for a 2 x 4 board at Home Depot is $12.48, but I noticed that a 3/4 in. x 12 in. x 4 ft. bullnose MDF shelving board is only $2 per shelf. Compare http://www.homedepot.com/p/Medium-Density-Fiberboa... with http://www.homedepot.com/p/3-4-in-x-12-in-x-4-ft-B...
The bullnose edge do not bother here because the widest boards are only 10 inches, that edge will be discarded after the cuts.
I bought 4 shelves for $8 instead of 2 boards for $24.98 for my 2 speakers. Besides saving almost 17 bucks, the amount of cuts needed using the shelves is less than using the boards (less work). Photo 1 is the layout in paper, Photo 2 is the transferred layout to the MDF. When tracing the parts in the MDF, you should leave about 3/8 of an inch between parts for the cuts.
Step 3: Cutting the Front, Back, Top and Bottom Parts
Cut the front, back, top, and bottom boards with the jigsaw, staying between 1/16 and 1/8 of an inch outside the marks. Side boards will be cut later.
Photo 4 detail of the parts and the discarded bullnose edge.
Step 4: Getting the Parts to Size
To get the parts to the right size you can use a file to get the boards to size. I decided to use the trim router with the 1/4 in. straight bit and the base plate attached (Photo 1). The photo shows that there are 42 mm (millimeters) from the edge of the base plate to the cutting edge of the router bit.
In each board I draw a line at 42 mm from the outside edge (Photo 2, Photo 3), parallel with it.
Although you can make a router jig for cutting (or buy one), I used a piece of straight wood 3/4 in. x 1.5 in. as a fence. I attached the piece of stock with clamps to the part, with one side touching the 42 mm line (Photo 4). This is the fence against which the edge of the router base plate will rest for the cut.
Holding the router against the fence, cut the part to size (Photo 5).
Photo 6 is the detail of the completed cut, the board is now of the correct size.
Total elapsed time for all the cuts including getting the parts to size: 45 min.
Step 5: Speakers Placement and Cutouts
One of the 16.5 in. x 10 in. boards will have the cutouts for the speakers. For simplicity I decided to have the speakers centered from the sides, and equally spaced from top to bottom.
The good thing about this approach (for my particular configuration) is that the tweeter is 2 1/2 in. and the woofer is 8 in., which allows an equal spacing of 2 in. between parts. The distribution is shown in Photo 1, Photo 2 is the actual drawing in the front speaker board.
Photo 3 is a take of the back of the tweeter. It shows the difference between the external size of the tweeter and the cutout needed. The actual cutout is 45 mm (roughly 1.75 in.) by 95 mm (3.75 in.). Also a bigger slot should be cut for the screws holding the horn with and the transducer.
Photo 4 shows the cutouts for the tweeter and the woofer. The required diameter for the woofer cutout is 182 mm (7.17 in.)
Photo 5 is the correction of the tweeter cutout so the transducer and its associated screws can go through it.
Step 6: Making the Tweeter Cutout
Photo 1 and 2: To make the tweeter cutout starts with a couple of through holes big enough to allow the jigsaw blade to fit.
Once the rough cut is made I used the trimmer router to get the hole to the right size. I used a combination of the fence at 42 mm and the accessory that came with the router (photos 3 to 7) to get the cut to the correct shape.
As I want the tweeter and the woofer to be flush with the front face of the baffle I need to cut a recess for them. Starting with the tweeter, photo 8
Step 7: Woofer Cutout
For the woofer cutout I used the trim router and a jig that I made out of a piece of plastic board. I made several holes in the plastic board and just "eyeball" the holes that will give me the radius I needed. Photo 1
I disassembled the base that came with the router and mounted 1/2 of the base on the plastic jig. Photos 2 and 3.
I made the recess of the woofer at 4 inches radius with the 1/2" straight router bit Pic 4 and 5.
Photo 6 shows how I attached a piece of stock (from under the face I am working) to the center of the cut so the center of the cut will still be attached to the whole face when I have completed the cut and will not break the router or bit or wood I am working on.
I made the complete cutout for the woofer with the same jig, in 1/8 deep intervals (8 passes) Photos 7, 8
Photo 9 is a fit test of the 2 speakers. PERFECT.
Step 8: Gluing Front - Back - Top and Bottom
As previously discussed my idea is to cut the sides last, once I have the Front - Back - Top and Bottom already glued together. In this way I am sure that the sides will fit snugly.
Photo 1 is a dry test making sure that the 2 parts fit together tight at the joint. I used the corner clamps to hold the parts square. I only have 2 clamps so I glued 2 pieces at the time.
I used the small workmate table to put pressure at the joint (Photos 5 and 6). Photos 7, 8 show that with care parts can be glued square even with this few tools.
Step 9: Cutting the Sides
Once the front - back - top - bottom are glued it is time to measure and cut the sides.
1) Flush trim the joints Photos 1 and 2
2) Mark the body of the speaker and the board that will become one of the sides to glue the side in that place and not mix the parts up. Photo 3
3) Mark the side. Photos 4 - 5 - 6
4) Cut the part with the jigsaw making sure of keeping the blade a couple milliliters outside the outline. We will trim the part to side once everything is glued.
Step 10: Gluing the Battens - Attaching the Sides - Flush Trim the Attached Sides
Before gluing the sides to the baffle I decided to add battens to the front and back to not only glue the sides but also keep then in place with screws. I used 5/8 square hard wood battens.
I glue them and screw them to the front and back using 1 inch wood screws. I made a through hole with a 2 mm bit to avoid breaking the the parts and battens and 3/8 inch holes 2 mm deep in the front and back so the head of the screws will be below the face of the parts. Later I cover the screws with wood filler Photo 4.
Glue the sides and use the same technique to screw the sides to the battens as previously discussed. Photos 5 - 6
The sides were cut a little larger than the correct size. This assures that when flush trimmed the baffle is perfectly flat in every surface even if it is a little off square in some joints. Photos 7 - 8 - 9 and 10
Step 11: Sealing the Interior
Using any sealant (i.e. used in for sinks and kitchen counter-tops) seal every joint of the baffle from inside. See photos.
Step 12: Veneering
I decided to veneer the box. I used wood glue, Titebond, you can also use contact adhesive (I suggest 3M spray).
Photo 1 and 2 show how the glue is applied, I cut the veneer a little bit larger than the face to cover and glue it. phto 3 shows the weight I put in the face using an auxiliary piece of wood to distribute the pressure.
Phots 4 and 5 show part of the veneer applied to the front face.
Photo 6 is the speaker completely veneered.
After that I applied gel stain and polyurethane finish following the instructions given by the makers.
Step 13: Finishing It Up
Only left is to complete the electronics.
The circuit is a basic high pass filter and the 2 resistors will lower the gain of the tweeter about 3 db. I had 10 watts resistors, but 1 watt resistors for a 20 watt speaker will work as well. The filter goes in the tweeter line, the woofer is connected directly to the audio connector.
Solder the circuit. I used a terminal strip for the serial connector of the capacitor and the 50 Ohm resistor and the terminal connector on the tweeter to solder the 100 Ohms resistor that goes in parallel with it. This resistor will protect the tweeter of any unwanted low freq. Photos 2 and 3.
I painted the interior of the speaker cutouts black for a better finish as depicted in photos 2 and 3.
Attach the speakers.
The total cost per speaker in my case was less than 30 dollars. I wanted them affordable a reasonable good quality.
Voila.
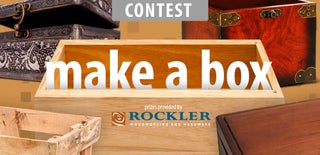
Participated in the
Make a Box Contest
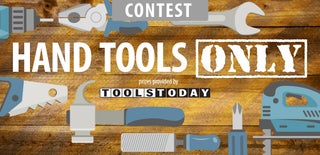
Participated in the
Hand Tools Only Contest 2016