Introduction: Air Hose Reel From Plywood / 360° Swivel
In today's woodworking project, I will show you how I built my 360° swivel air hose reel from plywood.
I made this hose reel for my workshop, it currently hold a 50' 3/8 air hose and it also work with a 100' hose.
The reel can swivel 360° so it's easier to go different ways in my shop, also easier when reeling the hose.
My lock system can lock the air hose reel in 5 different positions.
It is not perfect, but I'm really happy for the V1. I already have some ideas for a Version 2 in the future, but for now I want to build more tools and more storage for my workshop, so make sure you follow my Youtube channel for more content and more videos like this one. Thanks for following along, I really appreciate all the support!
Supplies
- 5/8 plywood ( 2'x4' sheet if more than enough )
- 3/4 Wooden Dowel ( 6' long )
- Trim Screws ( 1"5/8 trim screws and 1" trim screws )
- Dewalt 50' Air Hose or Any air Hose Up to 100'
- 1/4 Female to 1/4 Female NPT Fitting
- 1/4 Male to 1/4 Male NPT Fitting
Disclaimer : As an Amazon Associate I earn from qualifying purchases you make using my affiliate links. It really help me continue to bring you more free content when you purchase using my affiliate link and it doesn't cost you more so it's a win/win situation.
Step 1: Plywood Cutting List
Here's the list of all the plywood pieces you will need to cut for this build.
Step 2: Drawing and Marking Holes Locations
First, before we can even cut both plywood circles, we need to draw and mark the location of the five 3/4 holes that will received the 3/4 dowel, this step is very important because we need to find the center of our circle and that cannot be done after we enlarge the center hole for the axle.
Step 3: Cutting the Plywood Circle
At this part, you will need to cut 2 circles out of plywood. In this case, 5/8 thick plywood. I do this using a circle cutting jig i made from a lexan sheet. I also made a video tutorial on my jig if you want to see it click here :
Alright so to cut that circle, you will need to drill a center hole so you can turn your router jig arond. I drilled a 1/8 hole ( same size as jig holes ) and then i insert a dremel bit (1/8) inside the jig and the hole. Why a dremel bit? Just because it's easier to remove it, you can grab that stone and pull on it easily, not the case with a drill bit. The diameter of a circle is 2 times its radius so i set up my drill bit at 6" from the router bit, and i cut my both plywood circles.
Step 4: Making Holes in Both Plywood Circles
Now that our circles are cut, time to make the 5 holes for the 5 dowels that will joint both circles together to make a spool for our reel.
Once these 5 holes are made with a drill press, I drill the center holes on both pieces. One of them is 5/8 and the other one is 3/4. Center holes can't be made with my drill press because they are 6" from the edge and my drill press can take 5" max.
Step 5: Assembling the Spool
After cutting [5x] 3/4 x 9"¾ dowels, I assemble my spool. I only put some wood glue on each end of the dowels and I insert them in my plywood circles.
You can see in the picture, I already added a 2¼x2¼ piece of plywood with a 3/4 center hole in it. This is for added stability later with the center dowel that will also act as an axle so it was easier to glue this piece before adding the 5 dowels in the plywood circles.
Step 6: Making the Spool Support
We need to assemble the support that will hold the spool. I do this using some wood glue and 4 trim screw on each side to make sure it's really strong.
Step 7: Installing the Fitting ( It's Also the Axle )
Ok so the spool will spin around an axle made from a female to female fitting on one side, and from a 3/4 dowel on the other side. Let's start with the fitting side.
I first screw my 90° air fitting elbow to the female/female fitting, and I sandwich between these 2 fitting the main support of the spool aka the 2¼ x 9" plywood with a 5/8 hole.
Once it's done, I need to secure the fitting in place so it doesn't move around. A couple pieces of scrap wood later, everything is secure with two screw.
At this step, I was putting the elbow fitting upward, but it's a good thing i only used 2 screw for that little plywood bracket because I have to reverse it so the air fitting exit point downward. It's a must so the intake hose can swivel 360 around and don't get stuck in the wall mount support.
Step 8: Handle and 3/4 Dowel for the Other Axle
So we just installer our fitting on one side to make our axle. Now for the other side, I use a 3/4 wood dowel that will be screw from the spool to the handle. So before inserting this axel dowel, I assemble the handle.
Handle is made from a piece of plywood with a 3/4 hole at each end, paired with a 3 5/8 dowel to make the handle.
Once it's done, let's move to the next step that is assembling the spool on the support! :)
Step 9: Mounting the Spool on the Support
I mount the spool on the support, then I secure everything using a 3/4 wooden dowel. I place 2 metal washers on this dowel, one between the spool and the support, and one between the support and the handle.
I secure the 3/4 dowel inside the spool with a screw, and I do the same for the handle. I can remove the spool if I have to.
On the fitting side, I screw a male/male fitting with a quick connect fitting to secure the spool on the support.
Step 10: Making the Wall Bracket
I made a wall bracket for my hose reel with some plywood. I assemble all the pieces together then I attach the bracket to the hose reel using a 1/4 x 2"½ bolt. I put 2 washers between the wall bracket and the reel support.
Step 11: Locking System
I made a locking system to lock the spool and reel at certain positions. It's a simple mechanism but need to be improved, maybe in a V2. Watch the video for more details :)
Step 12: Wall Installation
I mount my air hose reel on a plywood plate because I have no studs in the middle on that wall. That way, it will be strong enough to hold up to 100' of air hose. Otherwise, I would have screw the bracket right into a wall stud.
Step 13: Installing the Hose
First, I connect the air intake, this is the hose that will run to the compressor. Second, I reel my 50' air hose onto my reel. I make sure there is no air leak, and our air hose reel is done! :)
Step 14: Thanks for Watching My Instructables
Thanks you so much for watching my instructable, make sure you watch my build video on my youtube channel.
I love to make stuff and I have several projects for my workshop, be sure you're subscribe so you don't miss anything.
Thanks to everyone for the support, this project has taken more than 40 hours ( design, making, filming, editing, english voice over when it's not my native language, making the instructables, publishing to youtube etc etc ) and I try to keep my build free for everyone and give my plans/measure to everyone so if you want to help me continue my mission, make sure your subscribe to my channel and keep sharing my projects. Thanks all! :)
Step 15: Air Fittings
Updated this Instructables with a diagram of all the fittings used in this build. Sorry should have included this earlier. The 90° air swivel is the model MP1038 from campbell hausfeld, unfortunately it's the old version but you can find the exact same model on amazon. Check the links in the supplies section of this instructables.
If you have any questions ask me below!
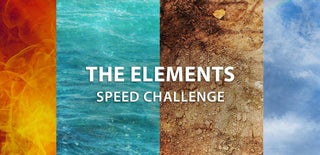
First Prize in the
The Elements Speed Challenge