Introduction: Air Powered Bicycle - Pneumatic Bike!
This instructable is an overview of my Pneumatic Bicycle - an air-powered bike.
When you pedal, the chain drives a 3D printed pulley, which drives an air compressor and fills the 3 gallon tank with air.
On the tank is a regulator which controls airflow to the motor, mounted at the rear.
The air motor is basically a train-style piston motor - the pistons are controlled by pneumatic valves, the understanding of which is largely the point of this project.
By rough calculation, I put the efficiency of this bicycle at 3% - a regular bicycle is over 90% efficient!
However, it is a really sweet kinetic sculpture, and taught me a lot about pneumatic power; that was the main point of the project, and to drum up interest in our team for the Baltimore Kinetic Sculpture Race!
Supplies
Air Compressor Bits
- Harbor Freight compressor - I used this one: https://www.harborfreight.com/1-3-hp-3-gallon-100...
- U-Bolts to hold it on
- 12v Air Compressor - just need the motor - I got a cheap car-powered compressor and cut it up.
- Sprag Bearing - one way drive on the air compressor motor shaft
- Bronze Bushings to mount the pulley
- one-way-sprocket, 12 tooth - I used one on the motor, and one on the pedal input; wanted to make sure the motor didn't pull my legs off.
- Bike Chain!
- 12mm steel shaft to mount the big pulley on
- Various printed parts - pulley mount, pulley, tank mounts, motor mount
Air Motor misc. parts
- two 300mm 2020 aluminum profile, and two shorter ones to tie them together
- Old bike rear rack - use the legs to mount the rear of the motor
- rod-ends: https://smile.amazon.com/gp/product/B07HNKVVYG/ref...
- Misc. screws, more 12mm brass bushings (from McMaster)
Pneumatic Components
- Piston - 17/16" bore, 3" stroke, double-acting rear pivot mount: https://www.automationdirect.com/pn/A17030DP
- Pilot Valve - 5 port, 2-position, single air pilot spring return: https://www.automationdirect.com/pn/AVS-5242
- This is directly connected to the piston. When the pilot has air pressure, it pressurizes the back end of the cylinder and exhausts the front. When the pilot is unpressured, the valve pressurizes the front of the cylinder and exhausts the back!
- Roller-type valve, 2 position 3 port: https://smile.amazon.com/gp/product/B01JIIJU64/re...
- 1/4" and 1/8" pneumatic tube
- Various press-fit fittings, all from automationdirect
Electric Components
- Big ol' battery: https://smile.amazon.com/gp/product/B07DWSYYZR/ref...
- You can justify this purchase cuz you can also use it to start your car.
- Big switch - the battery sends a lot of amps. My little switch died, use the biggest you can find. The one on there now is rated for 50 amps.
- Pressure Cutoff Switch: https://smile.amazon.com/gp/product/B00NXIXR60/ref.
- I wanted to make sure I didn't overfill the tank and blow up. Feel like that's important. I keep it set to 60PSI, although the tank is rated to 120.
- 5v Fans - keep the compressor cooler, for higher efficiency. Run them off the USB output.
- You can justify this purchase cuz you can also use it to start your car.
- I wanted to make sure I didn't overfill the tank and blow up. Feel like that's important. I keep it set to 60PSI, although the tank is rated to 120.
Step 1: Putting Air In
Mechanical
The compressor tank gets all of its bits removed, except for the drain plug and the regulator.
The compressor input is replaced by a one-way valve to make sure air only flows into the tank; the pressure cutoff part is replaced by our adjustable one. In theory, you could simply use the one on there - but it will pressurize the tank to 90PSI at all times and cannot be adjusted. I didn't feel comfy with 90PSI, and also it's really hard to pedal more air in at that pressure!
The big pulley is mounted on the rear bike stem, using a large printed clamp and brass bushings on a 12mm rod. This is comically oversized to give a decent speed increase - and I mounted a one-way sprocket so that you can backpedal without reversing the compressor - possibly not worth doing, but hey.
Mounting the compressor uses a 3D printed part and a hose clamp; make your belt first, and then you can pull the motor forwards to tension it.
I cut the sides of the motor off, and dismantled it to slip a sprag clutch on the shaft - that's another kind of one-way-bearing. Over this is a 3D printed pulley. If you don't use the clutch... the motor will spin the pedals and you will have a bad day.
Electrical
The electrical side is even easier.
The battery is mounted with a printed strap and some Velcro cable ties, so that it's easily removable; the switch is mounted just like the motor, printed housing + hose clamp.
I used purple wire because I had some, and it's awesome - 16 guage, which is overkill but whatevs.
From the battery, the positive wire just goes straight to the motor - but don't permanently affix it yet.
The negative lead goes first through the switch and then through the pressure valve on the tank, then to the motor.
So. If the switch is on and the tank is low pressure, pump. If either of those things aren't true, chill.
If you test the motor and it is driving the pedals, swap the leads. YAY dc motors. The compressor just needs oscillation, so nothing else cares which direction it runs in.
Finally, the cooling fans. I mounted mine inline with a bimetallic switch glued to the compressor cylinder - so that they turn on when it gets over 40C - and plugged straight into the 5v USB port on the battery. I like simple, it's reliable.
Step 2: Getting Air Out
The compressor tank outputs to a regulator - which I generally keep at 10PSI so that the bike can go farther. It does provide more power with more PSI, but not much more speed - it does have to accelerate itself AND you, after all.
Pneumatic (and hydraulic) Valves
So, how do you control the pistons!? Valves. How do you know what they do? Valve diagrams. I've annotated the one for this valve - check the photo.
The outsides of the valve diagram are how it is operated, or piloted. In this case, one side is a spring return, and the other is an air pilot.
The inside of the diagram consists of two or more squares, known as positions. It's quite common to have a 3-position valve - pressure one side, pressure nothing, pressure the other side - but this valve is only two-position. When ports A and B are hooked to a cylinder, one position of the valve pressurizes the front of the piston while exhausting the rear, and the other valve position pressurizes the rear while exhausting the front.
The other valve I have on there is linked to the pilot, and controlled via the big blue cam. As it rotates, it alternately pressurizes the piston, which then rotates the cam, which then rotates the bike tire.
The air plumbing looks intricate, but about half of that is because I pipe the exhaust back up front to a single valve - manually operated - that I can use to safe the system before getting off the bike.
Step 3: Air Compressor Overview
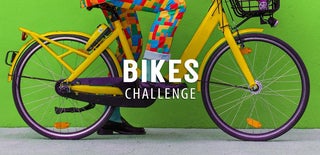
Participated in the
Bikes Challenge