Introduction: Air Umbrella 2.0 DIY! a Second Wind!
Have you ever had your parade rained on? I am not talking metaphorically even though I do enjoy metaphors. This is a literal question and to make it more relevant lets remove the parade requirement and ask if you have ever been rained on? When these sky tears beset you maybe you had a rain jacket or an umbrella, but what if there was an option that took the same amount of space as a traditional umbrella but was more expensive, needed batteries, made noise, prone to breaking, and it gets people around you wet and likely will still let you get wet? I can practically hear the chorus, "Shut up and take my money!"
This instructable is not here to solve a problem of building a better umbrella because lets be honest a regular umbrella is quiet, keeps you dry, does not get others wet, takes no batteries, and costs only a few dollars. My first project on Youtube was to make a cardboard impeller to try and build a successful air umbrella motivated by a failed kickstarter and a similar project by The Action Lab. This Kickstarter was light on details and then even lighter (they were non-existent) on the final product and while Action Lab tried to give it a fighting chance by using a leaf blower the extra piping and air constriction really suffocated his design.
If you just watched the cardboard air umbrella video you will know that those dreams wilted just like the wet cardboard of the umbrella. However as the simulated rain hid my tears I vowed that I would try again with a better design. Well today is the day we see if those clouds have a silver lining by proving that an air umbrella is possible even if it is not practical. That said many new innovations when they were first demonstrated were far from practical but I digress.
Alright here is what ya need!
FTC Disclaimer: I earn a percentage of the sales through the affiliate links provided through Amazon.
If you click on the link it helps fund future projects but bear in mind it might not be the best price for this materials.
Supplies
Materials
- Brushless DC Motor & Electronic Speed Controller
- 3S LiPo Battery
- Battery to ESC Adapter (XT60 to Deans)
- 3D Printing Filament
- 3/4" Black Iron Pipe 12" Section
- 3/4" Floor Flange
- #10 Machine Screws & Nuts
- Wire
- MCU
- Heat Shrink Tube
- Super Glue
- Duct Tape
Tools
- 3D Printer
- Soldering Iron
- Phillips Screw Driver
- Pliers
- Small File
- Safety Glasses
- Ear Protection
Monsoon Umbrella
Step 1: How It Works?
The way a regular umbrella works is simple, place a piece of waterproof material over your body and head and let the rain hit that material instead of you. Once the rain hits that material is runs down it until it falls off the edge of the material and falls to the ground missing you.
An Air Umbrella uses a similar concept but instead of the rain hitting a piece of material it hits a jet of fast moving air. This jet of air is moving sideways out from the umbrella. When the rain hits this jet of air it gets caught and if there is enough air moving fast enough it will carry the rain drop sideways as it continues to fall. This sideways movement of the raindrop is exactly what happens with a regular umbrella but in the case of the air umbrella it is accomplished using air to push the rain drops away from you while a regular umbrella uses fabric.
Sometimes a video is the best way to capture a concept so I would encourage you to watch the video that I made for this project to understand how it works and to see the project in action.
Step 2: Finding a Motor (Going Brushless)
My first attempt at an air umbrella used brushed DC motors which have been around for a very long time. They are very robust but they are not the champion of torque or speed that I needed. This is where a different type of motor that we are seeing more and more frequently gets its day in the sun... I mean rain.
A brushless DC motor is an interesting tool but what is it? What is the difference between a brushless and a brushed DC motor well the simple answer is the brushes, but you deserve a better explanation than that. The way a brushed DC motor works is that it has a stationary ring of magnets on the outside body along the length of the motor. These magnets sit in one place creating a fixed magnetic field. Inside this ring of magnets are specially designed coils of wire. These wires carry the through the motor generating a magnetic field that interacts with the magnets in the ring around them. However if these coils were connected to our power source directly two things would happen.
- When the motor spins it would twist the wires connecting the coils to the power supple until they break.
- After only a partial rotation the field from the magnets and the coils would align and it would stop spinning.
So how does a brushed DC motor get past these problems? Well it just "brushes" them off...
The coils in a brushed DC motor are attached to curved plates on the shaft of the motor. This plates have brushes sliding over them making electrical contact as the motor spins. This solves the problem of not twisting the wires and it also solves the second problem by changing the magnetic fields in the coils. Using these brushes as the coils spin the brush that they are in contact with changes which then changes its magnetic field so that it is attracted to a different set of magnets which pulls the coil around until it hits the next brush and the process repeats.
Now that I have spent so much time on brushed DC motors why am I using brushless and how do those work?
Interestingly enough the brushless DC motor drive signals are not DC at all. Let me explain why by digging into how the motor works. If we took that brushed DC motor that I described above and turned it inside out where the magnets moved while the coils remained still which is the opposite of a brushed DC motor. How do we drive this motor because if we just apply DC power we will end up having a locked up motor just like the second problem we would have with a brushed DC motor without the brushes. Well this is where brushless DC motors get really interesting because they effectively have digital brushes! We does that mean?
Using a piece of circuitry called an Electronic Speed Controller (ESC) a collection of digital circuitry and power electronic switches turn the power to the different coils on and off just like the mechanical brushes do in a brushed DC motor. This changes the magnetic field in the coils which pulls the magnets forward
The benefits we reap from the brushless design are numerous.
- No Brushes means that this source of friction and point of failure is gone
- Using digital control instead of mechanical brushes to transfer power is more accurate and more efficient
- More compact design allows for more coils of wire and more magnetic material allowing these motor to handle a lot more power.
So I started my brushless DC Motor search looking for enough power but not going overboard and spending too much or having the over build the system.
With the explosion of drones on the market there are all sorts of brushless DC motors to choose from. I landed on a motor that seemed suitable for my prototype due to its high speed and sufficient torque while still being compact. I really did not want to have to walk around with car battery strapped to my back.
With the motor selected most of the rest of the project really began to fall into place as I fit the design to accommodate the motor I had purchased.
Step 3: Impeller Design
Impeller design was a process to optimize a number of factors:
- Large intake opening to allow copious amount of air to be drawn into the system
- I would prefer to not have this system be pulling a golf ball through a straw
- Large diameter exit port to increase the speed of the ejected air as fast as possible
- Larger exit port diameter increase the air's angular moment as the radius increases
- Stable motor mount to allow for high RPMs
- Light weight to not waste power spinning the impeller
- Strong enough to move all that air
The intact and output openings determine the general size of the design while the later points are important characteristics but they can be adapted afterwards.
One thing that I really wanted was to have the intake area to be as big or bigger than the exit port. The reason being that I did not want to starve the system for air so by having the intake be bigger than the output the incoming air could be moving slower than the out going air. This created some challenges because while the intake has an area the size of a circle which is (Pi * Radius^2) the exit port has the surface area of the side of a cylinder which is (2 * Pi * Radius * Height).
I created a simple Excel spreadsheet to get an idea for how to get a better sense of more dimensions. The left column is radius while the numbers on the top row are the height of the outlet port. This helped me settle on a inlet radius of ~30mm and an outlet radius of 45mm. The result is an inlet port size of ~2827mm^2 while giving me the flexibility to set the outlet port height between 7mm -10mm tall while still meeting my design objectives. (Fun realization is that if I use a 10mm tall outlet port my inlet and outlet ports should be the exact same areas minus the blades and motor shaft)
With the top and bottom impeller radii selected next I had to decide on the total impeller height. It was important to have the impeller be tall enough to accommodate the outlet port height with enough space inside the impeller to still accelerate the air. This did not narrow down things down too much so I looked at my motor dimensions to try and achieve a compact and efficient design. This is what guided me to make the impeller height 40mm. This allows the impeller to take up nearly the entire height of the motor.
The dimensions of the motor will a little bit of a challenge to find so I have included the diagram that I found elsewhere on the internet. This meant the the motor body would need a cavity that was a little bit larger than 28mm accounting for filament width. The impeller mounting hardware had three sections two it the top and the bottom that is designed to sandwich the impeller had need about 12.6mm diameter cylinders while the center of this sandwich only needed a 5.4mm hole to allow the shaft to pass through. I have added the STL files for the impeller and the motor cavity into this step.
With the dimensions for the impeller laid out it was time to make the blades and for that I want to take a full step to discuss the process.
Step 4: Impeller Blade Design
I had a fun time making the blades for the Take Your Breath Away Mask but there was a lot that I learned in that process and I wanted to make these blades even better. This meant that I was going to be using backwards inclined blades again since they are quieter, more efficient, and capable of higher air pressure.
How I made these in TinkerCAD was an interesting process.
- Starting with 1mmx1mmx90mm boxes I stacked 65 of these boxes on top of each other to create a 1mmx60mmx 90mm structure.
- Next I progressively offset the boxes by 1 degree along the 90mm axis with each box to make a spiral staircase shape.
- Then to smooth the surface I rotated each box 40 degrees on its 1mmx1mm side to slope it backward to match the angle of the blade face.
- The result of this is actually only a single 45mm blade because the other end all choppy because of the 40 degree rotation. So I chopped the blade at 45mm in width and 40mm in height.
The result was a great looking backwards sloped blade. This process even gave a nice curve to the inlet.
The final step was to introduce the taper in the blade edge to match the conical shape of the impeller housing. With that blades all set I copied and pasted 8 of these blades to finish up the impeller.
Step 5: Impeller Enclosure and Air Guide
This turned out to be pretty simple since I just needed a hollow cone that was slightly larger than the impeller to protected it while it spun while leaving a large enough path for the air the enter the impeller and a shaped path for the air to exit.
The larger challenge came from ensuring that the floor flange would mount properly to the enclosure and that I could mount the motor while accounting for the leads coming out of the motor, mounting holes, and that protruding shaft out of the back. This shaft protrusion was something that I figured out after I had printed the project and so I just used a drill to save myself time and filament instead of reprinting the whole project.
I also realized that if I printed this file just like how it looks in TinkerCAD it would be mostly support wasting a lot of filament and there would be no way to get the impeller inside. The motivated me to cut the file in half printing the tow separate pieces that you see in the pictures. I was then able to easily installed the impeller and then rough up the contact points between the two parts using a file before I glued and clamped the pieces together to give me the final prodcut.
Note: In my video for this project I tested a larger output port. The stl file for that is also attached to this step.
Step 6: Motor Control
The motor control for this brushless DC motor is handled almost entirely by the Electronic Speed Controller (ESC). This circuit translates a simple single channel PWM into the multi-phase signal that the brushless DC motor needs and at considerably higher power.
The code was very simple to implement on the microcontroller. Controll signal that it is looking for is a simple very low speed pulse. This pulse has a frequency of ~400Hz and the speed of the motor is determined by how much of the pulse is on versus off.
Using the two buttons that are on the MSP430 development board the pulse that is used to control the motor can be turned up or down.
Attachments
Step 7: Handle
I have been on an black iron pipe kick for a few other projects I have coming up so it seemed fitting to use the same material here.
I settled on a 3/4" not because I needed the strength but because it let me use a few fun 3D printed parts that I have prepared from a future project to give the handle a unique Thor-like feel. Follow me to stay updated on this project teaser and other projects for when they post. (OK I am too excited it is a Thor's hammer with a unique worthiness test that I have never seen done before!)
The handle is simple in that it is a 3/4" standard black iron nipple that it 12" long. I adapted the handle prints from this post on Thiniverse to fit the pipe dimensions for my Thor hammer project that I have coming up but it is my handle and I needed it now so I am also using it hear on the Air Umbrella.
https://www.thingiverse.com/thing:2626313
Step 8: Testing!
I had thought about recording the testing with progressively larger droplets following a progression from a humidifier, to spray bottle, to garden hose sprayer but I changed my mind shortly after starting that. The humidifier and spray bottle mists are just not representative of real rain and they are really hard to see on camera.
This had me pivoting to using my shower because the drops are larger and I also have about 10 inches or snow on the ground in my backyard making garden hose testing really unappealing.
I was still able to define a reasonable testing progression even with the shower.
- Testing with the shower turned on very low with the umbrella right next to the shower head
- This allowed me to get some initial confirmation that the air stream can deflect water at all because if you watched my cardboard air umbrella it was barely able to deflect the water at all.
- The goal is to achieve complete deflection of the water droplets as far below the shower head as possible.
- Testing with the shower on full stream with the umbrella a few feet below the head
- This is a real power test since a shower head turned on fully will put out a considerable amount of water much more than a typical rain storm.
The design that I have outlined up to this point uses the 3S1P LiPO battery and is likely consuming between 50-100 watts and it is spinning the impeller at above 10,000 RPM.
One thing I am learning about is what the internet likes. One of those things are memes and there is one that fits perfect. "RyanMake you Bojo! Air Umbrellas don't work on water! Unless you got POWER!!!" Well that is what I have in the next step that I am calling the Monsoon Umbrella. How that version was made is covered lightly in the next step.
Step 9: Monsoon Umbrella
I had so much fun taking my Take You Breath Away Mask to a ridiculous level that I called the hurricane mask for its strong winds and it just so happens that these projects are similar enough that I can use the same 70mm ducted fan to do the same. I am calling this one the Monsoon Umbrella because this solution is so overpowered that if it does not work even in a torrential down pour then the whole goal of an air umbrella is lost. (The reality is that the idea is lost but I am hoping that is a completely overpowered silver lining.)
Using the same general housing that I had from the Hurricane mask I simply flipped the ducted fan the other direction and slide the mounting plate onto the bottom slotted channel and the air guide into the top slotted channel.
The results were wild and again terrifying to have so much power that close to my head again.
Attached are the larger intake and output files and the main body that holds the ducted fan.
Step 10: Summary Thoughts
There are so many interesting things that can be done with air and while the develop process was not a breeze it was a lot of fun to continue to develop and learn more about 3D modeling and printing while getting to begin exploring brushless DC motors!
This project has me thinking more about air curtains and where they can be used in interesting ways so stick around and follow me here on instructables and on Youtube to stay updated when those projects hit.
One other idea that has crossed my mind in building this project is another rain oriented phenomenon that I have wanted to explore and that is Lord Kelvin's discharge. Is it possible to make and electric umbrella?
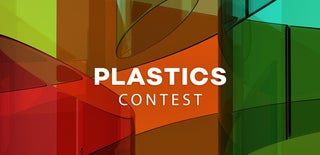
Participated in the
Plastic Contest