Introduction: Airsoft M41a Pulse Rifle
Ever since I’ve watched Aliens as a kid for the first time, I have been totally in love with Colonial Marines’ gear. I could not afford (and lacked some skills) constructing Dropship or a transporter, but making a rifle seemed more promising.
Once there was a Thompson-M41a conversion set produced by Tokio Marui and G&P. Sadly, when I started to plan my own conversion, it already hasn’t been available for some time. Funny thing is that when I was finishing it, Snow Wolf and Matrix model was entering the market.
My plan was to make a pretty affordable rifle that would be as faithful in looks to the original and as durable/heavy duty as possible, so that it didn’t break on a random close counter with a wall, pole or a tree.
Step 1: Items and Products Needed:
- 1x Thompson Airsoft Replica
- 1x cheap shotgun Airsoft Replica (similar to Remington 870)
- 1x cheap SPAS Airsoft Replica
- 2x aluminium sheet (1mm 0,5mx0,5m)
1x aluminium sheet (2mm 0,5mx0,5m)
1x Novol Professional Glass Fiber Putty 0,6kg http://professional.novol.pl/en/product/113/fiber...
1x Novol Professional Finishing Putty 0,6kg http://professional.novol.pl/en/product/109/finis...
2x Fosco Industrial Spray http://www.army-paint.com/products/spraycans-400ml
epoxy glue http://www.ebay.com/itm/POXIPOL-10min-Epoxy-Glue-A...
1x copper pipe 0,4m x 15mm
1x copper pipe 0,4m x 12mm
1x PCB Etching Kit http://www.ebay.com/itm/Printed-Circuit-Board-Etch...
sanding papers of various thickness
Tools
- cordless drill
- hacksaw files,
- hammers,
- pliers, vice,
- screw, clamps
- soldering iron
- gas jet/burner
- 2x brazing rods to solder aluminium
- riveting machine
Step 2: First Model and the Project
Before buying Thompson’s replica, I found its original production blueprint. I used it as a basis for first drafts of my conversion elements and it also helped me in completing the list of materials that I was going to need.
I considered using aluminium or steel sheets and eventually favored the first option. I don’t really remember why, but I guess it must have been that I didn’t have any welder to use and that aluminium could be soldered (or so I hoped, but it turned out I was partially wrong). My project included several stiff connections. Additionally, aluminium is somewhat bending- and blacksmithing-friendly.
I think every M41a amateur constructor starts from papercraft, which is actually a good starting point for everyone who attempts to construct a bigger model. I based my model on a plan from a webpage that sadly does not work anymore - www.usmcblackwatch.feeserve.co.uk.
To be honest, my paper model was quite rough and quickly done (true and accurate models need a few days of making). All I needed was just a scale and something to look up to just in case.
Next, basing on my model (and on a load of web images) I made tech plans and a template that was later used for cutting from aluminium sheets.
I used Solid Edge 2D, a free and user friendly program. I needed to draw a flat plan and the program served the need perfectly.
I based my plans on milimeters. I know that there are a lot of measurements on the project, but this is how many of them I really needed when I was transferring the plan into the sheet.
Step 3: Body
Being a poor blacksmith who works in a delicate home environment, I used a hacksaw and metal shears. Sheet bending at home is really hard.
It was important to make even and parallel bends. Sheets had to be bent on an entire length, so I couldn’t use a hammer and an anvil. Instead, I used a carpenter vice and a couple of flat bars and screw clamps.
I wanted my rifle to be easy to dismantle just in case, so I made one of the magazine covers moveable.
It was easier then to work on the display.
After much of a struggle, I managed to solder the second part to replica’s main part. It turned out that aluminium can be soldered, but only in small parts. Bigger parts cool down quickly and you need high temperature to solder anything.
I strongly recommend reading this How-to beforehand:
https://www.instructables.com/id/How-to-Weld-Alumin...
I had to stiffen the magazine’s cover inside, so that it didn’t bend when pressed. I assembled H profile out of sheets and soldered it to the internal side of the cover. At the same time it works as a guide to the magazine, since it would be hard to fit it into the slot.
The internal part I filled out with Aluminum Perforated Drywall Corner glueing it with epoxy glue.
Step 4: The Stock
Rifle’s stock was made of two parts of 2 mm sheets. No soldering. It was just riveted and it holds even today.
I used 4mm aluminium rivets.
I wanted to make a retractable adjustment, but I couldn’t do it, so it’s all stiff.
At least there’s no rocking and no scrunching.
I planned to put the battery in the mag’s cover, so I searched for the one that would be small enough to fit in there. I also moved the cables from the mag’s cover to rifle’s stock cover. I found a small Li-poly battery, but in the end I moved the battery to the stock. Here I used original Thompson cables going to motor.
However, it turned out that removing the battery out of the magazine’s cover is quite hard, so I placed it in the stock. It fits, it makes no trouble and it doesn’t stand out.
Step 5: The Barell
The external barrel is made of parts of copper pipes. Two layers are wound around with insulating tape to make them stiff enough and to fill out some existing gaps.
I used a hammer and a few pieces of wood to bend the external barrel’s shell. I didn’t care about perfectly even bends, since it was supposed to be spackled together with replica’s main part.
Step 6: Granate Launcher
Original M41 was equipped with integrated 30 mm grenade launcher in a stylish SPAS cover. Conversions though were equipped with a mockup that served to hide the battery and electric parts of the counter. I wanted my replica to have an operational grenade launcher. At first I planned to fit a tube for 40 mm gas grenade there; however, the case would be too big when compared to replica’s overall width.
I also had an idea to install a banger launcher inside. The construction of a slingshot with a guide rail seemed promising, but launching the banger posed a little problem. After each launch, there was just a short moment in time for taking a shot. As a result, my ‘grenades’ were exploding before even reaching the target.
Finally, I decided to stick to the original replica’s construction. I bought a cheap airsoft shotgun at local kermess, removed unnecessary accessories and shortened it as much as I could. It fit just right.
Then, I drew a template for the shotgun’s cover. I based it on some web images and on my cheap kermess SPAS. First cover that I made was plastic, but it didn’t work out - the surface wasn’t smooth enough.
So...
I cut a piece of alu sheet and used my template to drill out end holes 4mm. Then, I connected them through drilling and filing. The grinding sound that accompanied the whole process could be compared to scrubbing a blackboard with Styrofoam. My teeth hurt every time I think of it even today.
I also made holes for ejector port, loading port and the trigger. Extrusions on both sides I made using a hammer and a couple of wooden pieces.
A horizontal, long hole holds the guiding rail and the shotgun's pump. I also had to sand it all to remove any sharp metal scraps.
In order to combine the grenade launcher with the body, I cut a 30x4,5cm board out of 2mm alu sheet. Next, I screwed it with two screws into the place where normally Thompson had its frontal handle. Then I could finally place the launcher’s cover.
Last thing - blind stopper. I made it of wood and painted it black for elegance.
I had more trouble with the pump handle. I used an element of my cheap kermess shotgun. I had to widen it, hence wooden elements again.
Step 7: Magazines
There were only two types of magazines for Thompson - hi-cap 250 and 500 pellets. Obviously, a long magazine doesn’t fit this kind of gun. So, I bought two shorter ones. Metal body... Damn, it rattled as hell!
I had to do something about it.
Once I used to soundproof my bottles for pellets using a sponge, so I tried the same method here with the mags. I covered the internal side of the sheet with insulating tape and plastic elements with thin felt pieces. After that, my mags could hold about 50 pellets less.
Step 8: Speckling and Painting
Main parts were bent and connected. Now it was time for epoxy tuning.
I spackled element joints and upper bar with a slat in which I planned to cut the counter afterwards. I also speckled the blind stopper at the rifle’s stock. Then sanding and again speckling.
I used Professional Novol’s reinforced epoxy car putty. Its strongest side is that it dries fast, so I didn’t have to wait long with sanding.
Its weakest side, however, is that it stinks and stains. I really recommend wearing some gloves and a face mask while using it.
On the upper handle I glued a wooden 4 mm slat. Then I cut a small hole that was to serve as an aimer.
After spackling, grating and polishing, it was time for painting.
I used Fosco Spray paint. First, I put two layers of base, so that it covered aluminium well enough and then Forest Green and Black Matte colours.
I painted only aluminium parts and the paint still holds with some small exceptions resulting from an excessive use of the gun.
Step 9: The Counter
In the meantime, that is by night, I worked on my pellet counter. It was supposed to count down from 99 to 0. Well, it was quite a challenge, since I don't know much about electronics.
I wanted to use IR diode and a photodiode, as it fit my possibilities. The moment the pellet was between these two elements, the ray of light was supposed to be interrupted and the counter was to be given the right information.
It turned out that the counter based on a photodiode works great when it comes to detect a pencil, but a pellet - not so much.
Then I found a web page with a working pellet counter (programming is not my strongest skill either).
http://jenswilly.dk/tag/airsoftroundscounter/
This solved most of my problems. The program worked exactly as I wanted; I was able to understand it and even to modify it a bit. The program counts from 180 to 0, but the counter display shows only two last digits. For me it is better this way.
I switched photodiode to phototransistor and it started to work. Well, at least it detected a few series of pellets while shooting.
One year later I switched that phototransistor to type QRD1114 and it worked just as I wanted - it counted every single pellet shot and pellets shots in series.
My display consists of two 7-segment displays. That may not be the best solution, but it gives quite clear view and it’s user-friendly. I soldered both displays to a universal board together with two buttons. One button manually switches the counter off and the other one resets the system.
Inside magazine’s chamber I placed a microswitch that engages the counter whenever mag is put in, and switches it off whenever it’s removed. So, everytime you switch mags, you reset the counter.
I had to re-design the board in Eagle PCB program.
I moved several elements, so that the board was more narrow and I changed smd elements to through-hole elements.
I also added an ISP socket, in case I needed to make some changes in the code, and an off-switch to cut the power.
I printed the project, placed it on the PCB laminate and used a pin to make dots - later solder points.
After making all necessary dots, I connected them by drawing line paths with CD marker.
After prepatrations, I placed the board in a jar filled with a solution of ferric chloride. The ‘bath’ took about 30-40 minutes. I had to stir it several times in the meantime, so that the process underwent evenly.
Then, the board needed to be washed under running water. I painted it additionally with resin solution to protect it from corrosion.
At the end, I drilled some holes for electric parts with 1mm drill.
If that’s something new for you; check out some manual beforehand, e.g.
https://www.instructables.com/id/PCB-Creation-with...
https://www.instructables.com/id/Making-A-Customiz...
All this, so that I could fit all electric parts inside mag’s chamber (only there I found necessary space for it).
Attachments
Step 10: Fun's Over, Now Back to Work!
That’s how I build a replica of M41a replica.
The project took me about 7 months, including nights (leaving my wife alone in bed). Its cost closed in about 250$.
But... After several airsoft games it turned out that the ‘aiming rail’ is good enough only for shooting from the hip, and I’m way behind Vasquez’ level of badassness, so I had to add some genuine accessories. At the time I didn’t want to change the gun’s original look too much. That’s why I chose MRDS aimpoint.
To install it, I had to add RIS rail in the middle of the bar. I used the plastic one that was part of my cheap shotgun. The aimpoint itself was nice, small.. and faulty. It didn’t always work in the field. I couldn’t figure out if it was because of the wind or rain. I tested it in the forest during springtime. After that, I tested Flip Flop, but I don’t remember its producer.
In order to install it, I had to add two RIS rails - one in the back and one in the front. They were precise and durable. They also had wide regulation possibilities. I played with them during respawns.
I had used them for a couple of months until I lost the sight somewhere during one big game. It was the time when the gun had already become commonplace and I didn’t care anymore so much about sticking to the original look. I decided to install Eotech 551 clone. To be honest, it raised the aiming spot quite high, but such configuration made this gun more comfortable to use. It has worked flawlessly for two years now.
Once the external barrel slackenned off and I shot the phototransistor, that found itself in the shooting range. Since that accident, the counter display still works, but it doesn’t react to shots. After a few shots the grenade launcher’s pump handle cracked. The pin that was cropping out from the shotgun’s slide was too small and it tore its socket in the handle.
But... After three years my replica still works. I built it to endure rough conditions, and I have to admin that I really didn’t spare it. It survived heavy rains, snow, minus temperatures and heat. It survived close counter with mud and sand. I dropped it many times, bumped with it into trees and walls.
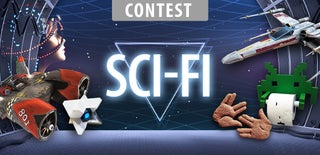
Runner Up in the
Sci-Fi Contest 2016
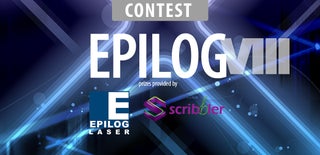
Participated in the
Epilog Contest 8