Introduction: Alien Chestburster That MOVES!
Alien (1979) - alien bursts out of Kane's chest - YouTube
Here is a video of my chestburster in action: Here
The iconic 1979 Sci-Fi Horror film Alien set a standard for films to come especially with the terrifying Chestburster scene. If you haven't yet seen this movie, it is a must have for true horror and sci-fi fans alike. WARNING: Not suitable for those with a queesy stomach for blood. See the link to the scene on YouTube,
My friends and I decided to go as the Aliens Crew this year and my buddy Rick needed a costume. Not only does Rick look like the evil android Ash, he loves Halloween as well. Look for his "Chronicles of Riddick" Lord Marshal costume on this site. Anyway I told him if we are doing the Chestburster, he needs to move and open and close his jaws. A static 3D print will not be good enough. We named him Chester!
FOUR complete builds later.. . I finally got something that worked. The Chestburster 1.0 tried a "spine of 1/4" rods that simply were far too stiff to bend with the fishing line I intended to use. See photo. Scrap that. Rev. 2.0 used a large door spring as a center spine and that was too loose and floppy. I then shifted over to a "Segmented Snake" design much like the 3D printed jointed snakes / dragons seen many places on the internet. This concept would prove to be a challenge as well to be able to get the control cords through the body, turn a 90 degree angle and down to a "marinette puppet" control cross and still be able to pull the body left and right and move the jaw. I
Chester 1.0 was too stiff and I never made skin for that one. 2.0 skin was too thick and really made the body far too stiff. Chestburster 3.0 skin was very much improved and then I broke the Jaw cord after it was 100% complete. I was ALMOST there... so being a perfectionist I had to make 4.0 which threaded the jaw cord through an improved pathway and... I doubled up on the 50 lb. fishing line! Ok so there's the background... lets get started.
Supplies
3D printers: A Resin printer to Print out the following Parts - Head, Ribs, Teeth, Body Pivot Yolk
A FDM Printer to print the base and Split open Flesh/ Ribs
PLA FIlament - 200 g - I used Elegoo brand.
Resin - Use Ultra tough "ABS like" resin - I used Anycubic brand
4 mm ABS model rod for the pivoting connectors inside the ribs
1" Webbing, 1" Elastic and Webbing clips - Your choice but I used scraps I had.
50 lb fishing line (braided not the mono filament type)
Acrylic Paints, Modpodge or Glossy paint clearcoat (Glossy for a wet look)
Super (CA) glue)
Black Lagoon Latex Mask Casting liquid
Plaster of paris for skin mold
1/2" Flexible electrical conduit for the fishing line raceway and for casting the skin.
Hot melt glue.
small 5mm diameter rare earth magnets for pushing / snapping the mouth open (repulsing in opposite poles direction)
JB Weld Epoxy Steel Putty - Mounting the head to the body adapter and molding arms.
1/8" brass tubing for arms (Arms are optional) the original chestbuster has underdeveloped arms but I took some liberties here!
Crew Patches from the Nostromo (Available by others on Etsy)
Crew Shirt on Amazon as shown in photo of supplies.
And,,, some STL files I made on Forger and Fusion 360 that you can get here...->>> Chester's STL Files.
Step 1: Print the 3D FDM & Resin Parts
FDM Print the Base File and the four Split open rib/Flesh files since these take hours to make and you can go on to something else! Print the Marinette "tee" for tie down points to control the strings.
Resin print with a TOUGH resin. Regular resin is too brittle and will crack under motion stresses!!!
Resin print the head and the lower jaw at 1500% up scale. For some reason the Forger Software doesn't like up in scale to the other parts I drew in Fusion 360. Be sure to use plenty of supports especially around the teeth on the upper head.
Print three of the Ribs for the Up and Down motion (Rib UD) and three for the Left and Right (Rib LR) motion. Print out the lower teeth.
Print the Body Yolk and two harness plugs.
If you want arms on him, then print out the biceps and forearms x2.
I sculpted his hands from epoxy putty after several attempts in resin kept breaking off his fingers.
Step 2: Mold the Skin
Making a latex skin covering is in three steps: Make the positive model, create a plaster negative mold of the model, and then cast a latex skin in the plaster mold to get the positive skin.
Make a box approximately 12" long by 10" wide for the plaster to be cast into. A larger box than what can wrap around the body is ok because extra skin can be used as torn skin on the base and pieces stuck onto the top of Chester. It only needs to be about 1/2 to 1Inch deep just enough so the plaster can completely cover the molded parts. Cut a strip of the electrical conduit in half lengthwise to resemble the side ribs of the Burster. GLiue these down into the box and spaced to align up to the sides of the ribs. See photos on how the skin wraps around the body and head of Chester. Give the mold more texture of veins and an organic look by and using holt melt glue. GLue up the seams so the box doesnt leak.
Use vaseline or spay cooking oil on the mold to help as a release agent rom which the plaster will not stick to and break apart, etc. when trying to remove it from the mold box.
Mix up some plaster of Paris and pour it into the box and then tap the underside and sides of the box to drive air bulbles to the top, and let it harden about 6 hours. Carefully pull the box apart to let the air harden from all sides of the plaster mold. Wait 24 hours before use.
Once the moldis thoroughlydry, coat the mold with vaseline or spray cooking oil to help release the latex. Next take a chip brush and paint a coating of latex all throughout the mold and into all the fine mold details. THINNER IS BETTER! As we will add successive layers upon dried layer versus one thick layer that will not dry internally due to a skin that readily forms. Make up at least 4 layers. Latex is thin but very stretchy and strong. Too thick and it will inhibit the movement of Chester!
Step 3: Rework the Head & Jaw
After Resin printing the head halves, use a dremel tool and grind out the center portion of its neck so that the jaw activation string can pass through the neck. Do this as smoothly as possible on the entire inside of the head.
Take a 14 AWG copper wire and bend it into a loop and flatten one end so that it lays flat on the roof of Chester's mouth. This will be a turning point for the thread. Solder the loop together so the thread doesn't catch on the end of the copper wire. Epoxy it to the roof of his mouth.
Glue the bottom and top halves together with CA glue. Take a fine cutting tip to your dremel and cut off the lower jaw as shown in the picture. Cut around the jaw and underneath the throat. You can always cut more off to get a better range of motion but go in small conservative passes as to not leave a huge gap in the neck. Cut a piece of 14 AWG copper wire to fit between the lower jaw hinge points and ca glue with some baking soda in each pocket to strengthen the connection. You should now have a lower jaw with a horizontal wire connecting the two TMJ joints together!
Glue a small rare earth magnet just behind the lower teeth. using epoxy putty, glue another magenet behind the upper front theeth. Be sure that the magets are like poles facing each other as they will work to push the jaw open after you relax the cord when you pull them together.
Cut a 1/2" strip of thin sheet metal approx 2.5 " long and bend one end into a tight loop the diameter of the 14 AWG copper wire you spanned across the lower jaw. Join this to the loose jaw and check that the jaw will swing easily over this sheet metal hinge. Fit this sheet metal into the lower throat section with epoxy glue and adjust by bending it to align the jaw TMJ joints up into the cut out area of the upper head. See Photos.
Dremel out the neck area to allow the neck adapter to slide in tightly to the head. Use epoxy putty to fasten the neck adapter into the head making sure you do not plug up the thread path. You may want to put a piece of thin 22 AWG wire as a threader lead to ensure this doesn't get blocked.
Step 4: Assemble the Body
Note the body is made up of three segments to allow motion left and right and three for up and down. Each segment has the word "top" embossed on them. Be sure all segments are in the proper alternating order and all are top is right side up to ensure the threadways align.
One at a time, inster a ABS 4 mm rod through the rib as linked through to the next rib in the series. Study the pictures closely and note the rib closest to the base must be a RibUD for connecting to the yolk part. Glue the rods ONLY at the point where they connect to the outside perimeter of the rib - the internal connection to the piece next in the series must not be glued to allow for the body to pivot.
The LAST rib going into the neck adapter is glued to the adapter via expoxy putty. Ensure you do not plug up the threadway by having a leader wire in place before you epoxy putty the rib to the neck adapter. It is a GREAT idea to run a leader through the center and down ALL ribs for ease in threading the jaw motion later.
You should now have the head, neck, and 6 ribbed body sections toether. Now use CA glue and fasten the yolk to the base being careful to align the holes for the three control threads to pass through... Left, right and the jaw.
Now comes a critical REVISION for BEST MOTION !!! As shown assembled in the photos the first rib from the base allows for Chester to hang DOWN. This creates TOO MUCH of an angle for the control cords to pull the weight of the head and rest of the body through the pathway so I had to anchor the first rib at the yolk horizontally and prevent it from pivoting down. This was discovered AFTER I attached the skin because CHester pivoted fine on the shop bench in a Vertical Nose up position, but when you turn him nose forward like to wear it, he hangs down too much and the cords couldn't lift him up. So, I then cut open his skin and fed a wire from ribs through the base and anchored them to the bottom of the base plate. FOR YOU, All you need to do is to glue the RIB to the ABS ROD to The YOLK so that it will NOT PIVOT DOWN! In fact it may be smart to place an epoxy putty block under this rib for even more support. See picture.
Step 5: Thead the Body
Now the body, head, and neck should be all fastened to the base.
Cut a piece of electrical plastic conduit as measured to reach from the center of your chest and down to you front pants pocket. You can always make this shorter if needed.
Epoxy glue ONE of the plugs into the conduit end. The other will be glued in after the threads are run into the conduit.
Epoxy this conduit to the base as seen if the photos. I added a sheet metal strap with some 5 mm screw inserts into the base for added strength.
Cut a length of thread approx. 10 ft long and double it up and tie a knot on each end. Tie one end to a small nut like a size 6-32 or a 3 mm nut as a stop for it to be glued to the first rib by his neck. Start at the top of Chester's neck and run a line through each of the Left (or Right side) holes and all the way down one side of his body and out from under the yolk. GLue the nut with CA glue and dab some baking soda around the nut to fill in the guide hole.
From there you may want to use a long wire to fish the line through the conduit and out the end. Tie a washer or similar item to the end so it doesn't back up into the conduit. Do the same for the opposite side.
Now tie then glue a small washer to the third 5ft long (doubled up thread) cord and glue one end to the floor of Chester's mouth. Secure with more baking soda. Then run it up to the copper loop and down through his neck, neck adapter and the center of the ribs using the pre installed leader line from the rib assembly process. Run the jaw line down through the yolk and out the base and into the center hole of the conduit plug.
Once all three lines are run out of the conduit, thread all three into the second plug and glue that plug into the end of the conduit being careful NOT to use too much glue and you end up gluing the thread to the plugh hole!!!
Now thread each line into the marinette puppet cross Tee and run it through the hole several times and secure with CA glue and baking soda to fill the hole and stop the cord from sawing on the endge of the hole. ONLY GLUE WHEN YOU HAVE TESTED THE IDEAL LENGTH FIRST (DESCRIBED BELOW). Do this for all three cords.
Step 6: TEST FOR GOOD MOTION!
Take a key moment and hold the base in a vertical (as in use) orientation with Chester facing straight out. You may need a helper to hold the base to do this. Now using the marinette cross pull on it in each direction to tension up each cord in sequence. You should see Chester pull to one side or the other or see his jaw move. There may be too much cord so you may need to trim it and reattach the cross until the cord is at an ideal length for where you will wear the base against your chest. If it moves hard, trouble shoot where it could be hanging up and resolve that problem before adding the skin.
Step 7: Add the Skin
Latex glues very well to anything especially when using CA glue. You may want to seek out a second set of hands before attempting this step.
FOR THE LOWER JAW - I used a latex glove cut up and glued in place to cover up the cut open area to allow for jaw movement. TRY NOT to get CA glue on the area that spans the gap that needs to remain flexible as the CA glue dies stiff and hard and this will greatly affect his jaw action. The same is true for paint and modpoge finishes. Less is more for flexibility.
Tie a string around chester's head and up to the ceiling or something that can hold him upright. This will greatly allow you the freedom to wrap his body with minimal issues. See picture.
DRY FIT the skin you cast earlier around the body and cut it down so that the circumference is a taut skin with about 1/2" overlap as centered on his underside centerline. You can cut for length later when the body is glued up to his neck.
Apply CA glue to all ribs around the circumference starting at wrapping the yolk and then upwards. A second set of hands can apply masking tape or just hold it in position until the glue sets (and it sets faston latex). Work your way up the body until you reach the neck.
Trim the skin around his neckline being careful to trim in small increments to get it a close fit to his head.
Step 8: Add Arms (Optional)
The movie version does not have arms perse but small chicken like wings (underdeveloped I guess). But I wanted my spin on it so I added these afterwards. Versions 1.0 through 3.0 were way to hard to get them to move well so I gave up on it (for now ?) hmm maybe later.. Ok so I fabbed up some arm parts and sculpted some claws using a brass rod as a center support. The claw fingers as resin prints kept cracking off so I used epoxy sculpting clay and that seems to hold up well. I drilled a small through hole at their shoulders and into the first rib (DRILL CAREFULLY as to not hit the cords!) and then I used a small nail as a pin and CA glued them into position. I then coated the arms with baking soda again for strength and then with a few coats of latext to blend them into the body skin. Zoom in on finsihed photo.
Step 9: Paint & Install Flesh Ripped Sections
Use an airbrush and carefully lay down very LIGHT coats of primer first and then finish color paints. Test a variety of blood red, browns, flesh, and bone colors on a test strip so you do not overpaint Chester. THIN coating as possible to keep him flexible. Then come back with a glossy final coat to make him look wet.
The chest fragments sould be printed and then heated with a heat gun and bent outward. Take scrap pieces of Chester's skin or cast new and glue them to these flesh supports. Paint as you see fit. The more fleshy flexible skin you have the better it will look. Disguise the base with similar paint schemes. Not in the phot the conduit looks like an aeorta in the chest peeking through so paint it as well! Glue them into their respective slots on the base.
You may also want to glue scrap pieces on chester's head for more realistic mess on hand!
Step 10: Bloody Shirt & Crew Shirt
The crew shirt was purchased from Amazon as described above and the mission patches from Etsy (by others). Like the Android Ash in Alien, I used an old long sleeve tshirt and bloddied it up and added some hot melt glue strands the I made by dripping hot melt glue into a bucket of cold water. I then spray painted them and glued them to the t-shirt.
Step 11: Harness & Final Thoughts
To make the harness, I used 1" webbing for the shoulder straps, 2" Webbing for the chest and Webbing clips. Tio ensure a snug fit around the chest and so it wouldn't slide around, I sewed some elastic along the chest strapping and I also glued some craft foam on the underside of the base. See the photos.
Four versions of this project taught me a lot and there is always something you would change if you were to do it again. This project taught me to really borrow shamelessly from other ideas that work and to not over engineer something when simpler can be better. I learned a lot about latext casting as well as getting a good paint scheme to work with all of the variety of parts involved. The most important thing though is to keep trying and learning from your mistakes because I firmly believe that creativity is a combination of ideas with experience and failures teach us more than our successes! I'll post pictures at the Children's Hospital Benefit Party Chester is going to attend so keep watching the post!
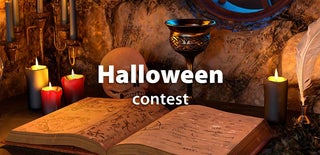
First Prize in the
Halloween Contest