Introduction: Aluminum and Wood "puzzle" Modular Shelf
Using a few simple tools you can make this unique modular puzzle shelf with supplies from any big box hardware store. While shelf is designed to hold A4 sized books, it's main purpose is to hold small daily use items and is not a heavy duty bookshelf. I've included some thoughts on how to make a heavy duty version at the end.
Materials needed:
- 10mm aluminium tube. I bought mine in 1m lengths, 19 tubes was enough to make the shelf pictured.
- 30mm x 30mm x 1200mm hard wood rods for the cubed nodes.
- 6 of 235mm x 95mm x 19mm DAR pine boards for the shelves.
Note the above wood sizes are based on shelf timber you get from big box hardware stores in Australia. Adjust the measurements for timber available in your area or cut to a size that matches measurements.
Tools needed:
- small saw
- hack saw
- sharp chisel*, 1" or similar will do.
- square
- 10mm drill bit and drill
- marking knife
- flat file
- hand or electric router
- metal ruler
- hand plane (optional)**
- mortice gauge (optional)
- printer for the template
Jigs needed:
- Saw box
Consumables needed:
- Sand paper
- Finishing oil, I used boiled linseed oil
- spray glue or a glue stick
* A note about chisel sharpening:
The chisels used for this project needs to be razor sharp. Don't expect to use the chisel you've been opening paint cans with (: Don't stress! You can restore and sharpen a chisel with sand paper and a flat surface. Watch this video on sharpening chisels. If you want to get serious about sharpening get a set of diamond lapping plates and watch this video on using diamond sharpening plates.
** About hand planes: To get quality results from a hand plane it needs to be razor sharp. Here is a good video on sharpening planes (sand paper can also be used if you don't have lapping plates).
Step 1: Watch the Build Video
Watch the build video to get an idea of what's involved. If you like my video please subscribe to my youtube channel, I've got lots more (:
Step 2: Make the Wood Cubes
The cubes used to join the aluminum tubes together are made from 30mm x 30mm wood rod. Make sure you use hard wood for these, softwood like pine is too soft and the aluminium will bruise it. If you watch the build video you can see I learned this the hard way (:
To make accurate wood cubes with a hand saw you need a saw box. Saw boxes can easily be make out of shop scraps or purchased from a hardware store. There is a good tutorial on making saw boxes here. Set up a saw stop on your saw box to exactly 30mm using a small clamp. Use a vernier caliper, or the rod itself, as the measuring guide for the stop block. Saw 18 30mm wood cubes. It's extremely difficult to make perfect wood cubes, so don't stress if they are a bit off, if they're close no one will notice (:
Step 3: Drill Holes in the Cubes
These holes need to be in the exact centre, 10mm deep. If you have a drill press and drill press vice then this should be easy. However, if like me you don't have a drill press, you'll need to make a simple jig.
Making the drill jig
To make a jig I used some scrap 30mm x 30mm pine rod, inserted the 10mm bit and measured how long the jig needed to be to make a 10mm hole in the cubes. Mark the centre of the jig by drawing cross diagonally from the corners. I marked the centre using a screw, then drilled a small pilot hole. When drilling the 10mm hole it's important to be exactly straight and centred, so make sure then drill is straight before drilling - get a second opinion if you need. When drilling start slow so the motor torque doesn't pull the drill off centre. This is difficult! Be prepared to make several attempts, it took me 5 tries to get it right :)
Once you have the jig, clamp it to the top of a cube using a vice as pictured, and make sure it's aligned flush with the jig. You can now drill centred holes, 10mm deep with out a drill press!
Drill holes on 5 sides of each of the 18 cubes.
Step 4: Cutting the Aluminum Tubes to Length
Using the saw box and hack saw cut the aluminium tube to the following lengths:
- 12 length of 33mm for the vertical post tubes
- 9 length of 27.5mm for the horizontal shelf supports tubes
- 12 length of 90mm for the long horizontal tubes
Aluminium is a very soft metal, a hacksaw will get though it quickly.
It's important for all the matching tubes to be exactly the same length. To achieve this, clamp down a piece of scrap wood to use as a stop block.
Use the flat file to smooth out the saw cuts so the tubes can be easily inserted into the holes.
Step 5: Assemble a Single Frame Module and Cut the Shelf Board to Length.
It should be possible to push the tubes in with hand pressure. This should result in a natural firm hold on the tubes. I felt this hold was good enough and it did not need glue, but make sure you firmly push the tubes in to ensure consistent frame dimensions.
Once you have a single module assembled, carefully measure the distance between the long axis edge of the corresponding horizontal shelf supports. This measurement needs to be accurate, I'd suggest measuring directly on the board it's self, not using a tape measure. Measure by placing the board on the shelf and marking the distance with a knife. Add 10mm to either sides of these marks, the shelf planks will be sawed to this length.
How to achieve accuracy with a handsaw
Using a 'knife wall' allows for accurate cuts with a hand saw, a tutorial can be found here. In short, a saw guide is created by scoring around the cut location and chiselling out a small grove along the line. If you make non square cuts on the woods waste side you can true it up with a hand-plane. If you don't have a hand plane, true it up with sand paper.
Step 6: Cut Dados in the Shelfs
If you have a mortice gauge, set the distance between the pins to 11mm* and the distance to the fence to 9.5mm, then carefully mark out the shelf board as pictured. If you don't have a mortice gauge use a knife and square, just make sure your accurate. Clamping the square down can help prevent movement when cutting. Now it's time to cut the dados.
* 11mm is enough give the aluminium bar a little room to move.
About chisel safety
You could shave with a sharp chisel, hence safety is important. In fact, shaving the back of your hand is a chisel sharpness test! My rule is to always keep your hands behind the blade, never in front.
Cutting the dados for the aluminium tube
If you're using a chisel to cut the dados set it about 3mm from the mark line at an angle, chiseling out a shallow groove along the length of the mark line. Remember to only use hand pressure or light taps with a mallet. Traversing the same line, lightly tap out a deeper groove by holding the chisel perpendicular to the wood. Along the same line, place the chisel 6mm from the mark line and make a deeper groove. Repeat these steps until you have a deep groove. When you get close to the other side, rotate the board and repeat the process.
Flatting the bottom of the tube
If you have a hand router flatten the bottom of the dado to a depth of 10mm. If you don't have a hand router, pare down the bottom of the dado with a chisel. Don't stress if it's not perfect to begin with, you can make small corrections by placing the tube in the dado and paring down the bumps after you cut the puzzle ends out in the next step.
Power tool alternatives
If you have a electric router or a table saw, these can be used to cut the dados.
Once your dados are cut on both ends of a shelf board, test fit them in the aluminium frame as some small adjustments in the frame might be needed. When you're happy with the fit, use the first shelf to mark out the dado placements on the other shelf boards and repeat the process.
Step 7: Cutting the Puzzle Ends on the Shelf Boards
To make cutting the puzzle ends of the board easy, I've created a 3D model in google sketch and a SVG 2D template. The sketchup, SVG and pdf files can be downloaded from github. If you're using 235mm boards you can simply print the pdf. If your using a different board width, you'll need to open the SVG file with inkscape, or similar, and scale it to size.
Notes on printing the PDF
When printing the pdf make sure the print scaling is set 100% and the paper size settings matches what you have in the printer. Double check the scale of the print with a ruler because it's easy for the printer's settings to be wrong.
Once you have the template printed, spray glue it to the end of the board. Make sure it's correctly lined up with the edge. Now carefully, with a knife and metal ruler, score a deep line around the template using multiple passes. Remove the template.
Chisel out a groove
On the waste side of the mark line, chisel out a small groove along the knife line. This groove will help guide the saw.
Saw out the shoulders and angled cuts at the board end
Mount the board in a vice, carefully saw out the shoulders and the angled cuts of the puzzle end. Take your time and always make sure the saw is on the waste side of the line. The cut can be tidied up with a chisel later if needed. You'll notice the centre piece of the puzzle is not accessible with a hand saw. You could use a coping saw or jig saw to cut this piece out, but I find a chisel is more accurate. Repeat the process of chiseling out a groove until you have a deep groove that's close to half way down. Then flip the board, cut a knife line between your saw cuts and make another deep groove. You will eventually meet in the middle and the scrap wood will break off. Clean up the cut with a chisel if needed.
Repeat the process on one end of each board. (If you plan to make this shelf larger then 2 modules long some boards will have to have the puzzle at both ends.
You will notice the same template can be used for both sides of the board as it flips around, allowing the boards to puzzle together in the middle.
Step 8: Finishing Up
Once you have all your boards cut and fitted. Sand them smooth and apply your choice of finishing oil, I used boiled linseed oil. When it's dry, assemble the shelf! I found no glue was needed in the cubes, friction was enough to hold the frame together.
You're done!
A short note on shelf strength
This shelf is designed to be a lightweight modular shelf. We use it to organise our everyday clutter, so it didn't need to be strong. If you wanted to make a heavy duty version of this shelf. Replace the aluminium tube with steel rods and add a support beam to the bottom of the boards. You might also need to use tensioned cross cables between the cubes to stop sideways racking.
Step 9: Conclusion
Thanks for reading this instructable! Making modular flat pack furniture yourself is heaps of fun and rewarding. If you like this instructable please follow me for future projects and checkout my other instructables. Also if you like my video please subscribe to my channel.
Thanks again!
Andrew
Me:
Instagram: @andrew_r_jones
Youtube: @andii1701
Twitter: @andii1701
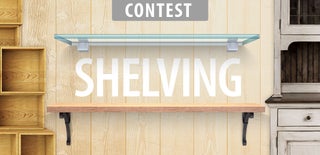
Participated in the
Shelving Contest 2016