Introduction: An Arabesque Cabinet
This project is not for the fainthearted. It took me all together over six months to finish, not continuously of course. Probably now, I could realize it in (much) less time, as the trial and error would not be necessary anymore.
In short, an Arabesque ( also called a Moucharabieh) is an Arab geometric pattern typically found in Morrocan / Arab Mosques and Palaces. The design is typically very complex, and takes quite some time to study and understand. The principles are as old as the 12th century.
My whole project could be subdivided in four major phases:
1. Designing the Arabesque - for which I used SketchUp;
2. Making the Arabesque - cutting the individual pieces on the bandsaw, and gluing them together one by one;
3. Designing the Display Cabinet - again with SketchUp;
4. Building the Display Cabinet.
Warning - this Instructable is not a step-by-step list of instructions. Each person should adapt them to his/her own environment and needs, and levels of woodworking competence. The Arabesque could also have been used for a whole different set of projects, such as e.g. the center piece of a coffee table.
Step 1: Get Your Inspiration
Before starting, I recommend that you do some background research and reading on Arabesques. The worst thing you could do is to plunge into your drawing software, and start fiddling around, or, worse, to run into your workshop and starting to cut off pieces in a desperate manner.
Best is to look at a number of examples. I got a lot of inspiration from a magnificent book on designing Arabesques by Jean-Marc Castera, obviously named "Arabesques - Decorative Art in Morocco". It is dated from 1999, but excellent stuff. Unfortunately, on Amazon, it is priced beyond reason, you may need to search further.
You can also search in Pinterest; or collect a few examples when browsing or travelling.I benefited a lot from understanding how Arabesques worked from going back to pencil, paper, ruler, and especially an eraser. It is time-consuming, but fun to try out, and it forces your brain to think geometrically.
Step 2: Design Your Arabesque
For this phase, you need to download a drawing software on your PC. There are certainly several drawing software packages that could do the job,including AutoDesk; I used SketchUp.
There are a few things that your software should be able to do:
- drawing in two dimensions for this first phase is enough. If you plan to use later the same software for designing the cabinet, you will need 3 dimensions;
- you only will need straight lines, which will go in five directions: 0, 22.5, 45, 67.5 and 90 degrees;
- you should be able to measure the distance between lines and between points quite precisely;
- the areas created by different lines have to be highlighted in different colours.
- the software should print the design at its real size, if needed segmented over different pages.
The principles for drawing the Arabesque include the following:
- First, determine the thickness of the wooden parts you will produce and use. This is the major determinant for how your Arabesque will look. I used for a 33 x 33 cm ( 12" x 12") Arabesque a 10 mm width ( 5/8").
- Next, look at the space between the parts that you would like to keep.
- In my type of Arabesque chosen, all the lines had an angle of 0, 22.5, 45. 67.5 and 90 degrees. To speed up the drawing process, I produced a 'stock' of spare straight lines at these angles on the side of my design, so I could pick them up as needed.
- Once I had the overall basic structure in place in my software, the next step was to painstakingly remove all the excessive lines - and there were quite a few. I wanted my wooden parts to be woven- one line digging under another one, and then at the next crossing jumping over the next one. Why make it simple?
- The next step was to colour-code all the different pieces. In all, I had about 16 different parts, so with 16 colours, it became easier to sort them out. Once you found the pattern, you can start to look for similar parts, usually displayed in a circle around the central ___ stars.
- Once your colour book is ready, copy an example of each part to the right of your design, sufficiently spaced out, and indicate the measurements for each part on your project. Be precise, correct measures will determine the overall success of your project.
- Now, print out your design in two copies in colour, and write the sequential number of each part on the printout to determine how many of these you need. Don't do this onscreen, it is too easy to miss out a part. Write down the total number of pieces you will need for each part on the printout.
- Glue the second printout on an assembly board, plywood or particle board will do. Size 50x50 cm ( 20"x20")
- Time for your calculator. Add 10% to the number of pieces, and multiply them by the length of the longest side of your trapezoid parts, to find out how much length of wooden bars you will need. Again, add a 10% to the overall length of wood required.
- That's it, ready to move to the workshop for the next phase! Finally!
Step 3: Cut and Paste the Arabesque
What you will need in this phase:
- A table saw to rip the wooden sticks
- A planer to thickness these wooden sticks
- A bandsaw
- Good woodworking glue, e.g. a Titebond III
- A lot of precision and patience
Now, you are ready to start with the real stuff. First question is, which stuff? You have to choose the wood you will be using. From the previous phase, you know what length of wood you will need ( in my case, it was about 6 linear meter ( 25 feet) of a 10x10 mm ( 3/8" x 3/8"). Don't skimp on the wood species - once you get to the end result, a proper type of wood will highlight your achievement to your eternal self-pride and vanity. I went for a tropical wood species, "cocobolo", but many other could work well: rosewood, palissander, ... Take something with lively and coloured wood grain, not something dull or plain like ash, oak, pear, boxwood; and also, better hardwood, not pine or beech. I spent about 80 $ on my piece of wood, it was money well spent.
Cut the block or the wood on the table saw into parts slightly thicker than your final dimensions of 10x10 mm, in my case I left it at 12 x 12 mm, about 40 cm long ( 15"). That gave me the opportunity to pass them safely through my planer to get to the final dimensions.
Tip: mark two adjacent sides of the sticks, e.g. with an "X" and an "O" respectively. Pass all your sticks first with the X to the bottom of the planer, then, with the same thickness, all of them again with the O side down. Reduce the thickness to the final width, and now run them through the planer again, but this time with the X and O sides on top. You end up with perfectly square sticks.
Before continuing, sand the pieces lightly, preferably with a 220 grain sanding paper. For the insides of the Arabesque, this is your last chance of getting there.
Over to the bandsaw. In order to get perfectly identical puzzle pieces ( believe me, that is quite handy later on), I recommend that you build a simple jig to have exactly the correct angles of 0,22.5,45, 67.5 and 90 degrees. See the model above.
Both the stop block and the Arabesque square are fixed to the respective guides with (spring) clamps. The stop block determines the length of the piece, so check after the first cut that it has the correct distance from the bandsaw blade. From there on, it is a piece of cake. If you need to saw a 67.5 angle, just turn around the piece on the 22.5 degrees guide. Add a few extra's, some will inevitably get lost! Cutting different angles on the same piece is also easily done, fix two stop blocks on two different angle guides.
Keep your different parts in separate containers, and label them as you go. You will end up with about 200 parts, you don't want to get them mixed up.
All right, now you have all the parts in the right dimensions and the right angles, time to get them together. Pick up the printed, full-scale printout from the design phase, and start in one corner with each of the parts. Just a dip of (quality) woodworking glue will do on the mating faces, the outside row you may add a drip of glue on the bottom side to keep the pieces in place on the board. Once two pieces are glued together, stick a small piece of masking tape on top of them to keep them in place... and wait until the glue has settled. When you start working out of a corner, in the beginning, there are only a few pieces you can stick together at a time, but as the work spreads out, you can speed up the process. You can also start to make up some sub-assemblies, but be careful not to make assembly errors.
It became a routine, gluing a few pieces in the morning, at noon and in the evening in between some other woodworking projects.
Despite the limited amount of glue, because of the lattice structure, the whole assembly becomes incredibly strong. Invevitably, some glue will spill over to the printed layout, which is not a problem, it helps to secure the workpiece in the mean time. Just be careful to remove any side spills of glue as you work along, later on it is quite hard to clean up the Arabesque.
After the last piece of glue has hardened, and the last piece is in place comes the magical moment. Carefully slide a wide chisel between the workpiece and the support board from different sides. The printed paper will normally split, and your workpiece will become free. All you need to do now is to sand the top and bottom side of the Arabesque, and you are ready to start thinking where you want to put it.
Step 4: Design the Cabinet
After the labor of love, back to the drawing board, for the display cabinet that would surround the Arabesque. I wanted to include lighting on the top, so that when the doors were closed, the Arabesque would be illuminated from behind, and glass shelves, so that the light would shine down to the bottom. The inspiration came from two sources: Chinese cabinets, which have often straight doors with a circle in the middle; and James Krenov's beautiful designs of long-legged cabinets.
I started with one version of the cabinet, cloned it, made some changes, and so on, until I had finally what I liked - i.e., seven versions later.
Back to the workshop!
Step 5: Build the Cabinet
I was constantly thinking of Cindy Laupert ('The First Cut is the Deepest') when putting my long-cherished Arabesque on the table saw and brutely cutting it in two halves, to be attached to the two cabinet doors.
After that, it was just a matter of traditional woodworking to build the whole structure. The electrical cables are hidden in dadoes running along the posts, so invisible from the outside.
The cabinet is wild cherry ('merisier' in French), finished with shellac and wax.
And Hercule Poirot would say "Et Voilà!" when he would spot the final result
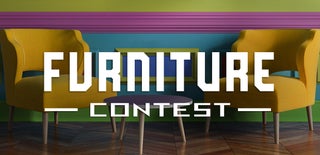
Participated in the
Furniture Contest 2018