Introduction: Architectural Cast Concrete: Wall Caps, Column Caps, and Fireplace Hearth and Mantel
As an architect I sometimes have a vision for a design element or finish that is difficult or expensive to acquire or build. For example, cast concrete products like countertops or furniture are beautiful and durable, but relatively expensive.
In 2011 I was starting my own architecture practice at a time when the economy was historically weak and, while I was not idle, I did have some extra time on my hands. The first project under my newly established firm, MS|Architecture, was a front-yard patio for outdoor living. This design challenge called for a bold statement - an elegant outdoor living space that could fit beautifully within a picturesque oak forest.
Working with the client's preference for a warm, tone-on-tone design theme, a beautiful and durable product was needed to function as column cap, wall cap, and fireplace hearth and mantel. While natural stone was considered, cast concrete quickly became the perfect solution due to its ability to take on virtually any form. Cast concrete also allowed for my vision of column caps that double as planters, with concealed LED lighting to boot. The budget wouldn't allow for this to be done by a concrete counter-top company, but I was determined! I decided to take on the project myself. The one obstacle was that I had absolutely no experience with cast concrete or form making, so I had a lot to learn!
I dove in and didn't look back. With 51 finished pieces and maybe 20 failed castings, it was a bigger project than I anticipated. I recommend a much smaller project for your first try at cast concrete. With that said, my experience was incredibly rewarding! Now I am excited to use instructables to share my experience and motivate others to create with concrete. Follow along with my instructable, study up on lots of other resources, and get started on your own project.
Please note that this instructable should not be your only reference - my intention here is to present tips and lessons learned from my experience, rather than a complete how-to guide. Refer to books and online resources like those I reference for steps not thoroughly covered here. As this is my very first instructable, please feel free to contact me with any questions or constructive feedback on how I can improve your learning experience or clarify anything that will help you be successful. Good luck!
Step 1: Research
Read, read, read! The first thing you need to do is learn all about cast concrete. Many of the books focus on countertops because that is a popular use for cast concrete.The same techniques used in making concrete countertops applied to my project. While all of the books and online tutorials are helpful, I do not believe they stress enough how finicky mixing concrete can be. If you can cook you should be able to mix concrete, but be careful because mistakes in mixing or pouring are expensive and time consuming as you often have to start the process over. For example, be careful about portions of ingredients, especially water. Too much or too little water can spell disaster!
Some books I studied and recommend:
- Concrete Countertops Made Simple, by Fu-Tung Cheng
- Concrete Countertops, by Fu-Tung Cheng
Concrete at Home, by Fu-Tung Cheng
Making Concrete Countertops, by Buddy Rhodes
Also, here are some online resources I found useful:
Step 2: Design
Concrete wall and column caps were an important part of this patio's design from the beginning, as shown in these SketchUp model images and CAD details. The rich, brick-red color was selected to play off the Spanish roof tiles. To maintain a clean, sharp look to the patio wall, I wanted to conceal all utilities - and there were many! The list included:
- low voltage wiring for the light fixtures (in plastic conduits)
- 110v wiring for plugs (in plastic conduits)
- Drip irrigation for the column cap planters
- Drain line from each column cap planter to drainage system below ground
All of systems listed below had to be run in concrete-and-rebar-filled masonry walls on concrete footings - not an easy task! Careful planning and installation were essential for each of these systems to function properly, especially because they are installed in rather permanent concrete masonry construction.
- Light fixture type and location
- Electrical sub panel, transformers and controllers
- Power outlets
- Fireplace gas and electric.
- Concealed and buried drainage system
- Water lines for hose bibs (run in ground-level planter beds)
Each project will have it's own set of design challenges. One of my many challenges was how to create a channel in the column caps for concealed LED rope lighting. I wanted to have tight tolerances for this feature to maintain a clean look. To get this right, I knew a mock-up would be a good idea. I knew detailed drawings would be critical, and they were. While drafting my details I began to research LED rope lights so I could select the right product for the job - a water-resistant type for outdoor use.
While discussing my project with an online LED sales representative at EnvironmentalLights.com, I learned that their LED rope lights can only be cut to length at certain locations along the rope, marked at 3" spacing. See my step on "Full-scale Mock-Ups" for more on why careful design and planning were so important.
Step 3: Build a Pour Table
A good, solid and flat table is important to have before starting on the concrete project itself. It will serve first as as a work bench and later as the pour table. I designed and built my table using TJI floor joists for the base, and plywood and 2x4 lumber for the table top. Design your table to have:
- Ergonomic height
- Lots of storage (I had dead space in the lower portion of the base, which I would correct if doing this project again)
- Flat and solid table surface that you can drive screws into if needed
- Easily adjustable for leveling. I used shims screwed in place under the bottom four corners of the base.
- Stability against racking (I gusseted both the lower and upper portions of the base using plywood to prevent racking)
Step 4: Full-scale Mock-Ups
Mock-ups can be a necessary and critical step in architectural detailing and finishing, especially for elements that are expensive and/or repeating in the design. This will allow you to validate most aspects of a design element allowing you to make the necessary revisions before committing to production. In this patio project I used two full-scale mock-ups, both turned out to be critically important design tools.
The LED rope lighting was a perfect example of why and how to mock-up critical design elements whenever possible. After purchasing and mocking up a section of the LED rope lighting, I adjusting my detailed drawings to accommodate the specified cut locations, spaced 3" apart. I then measured the outside length of the mocked-up rope-light section, including 90-degree elbows. I then designed my column cap concrete forms to accommodate this dimension critical dimension. Purchasing and mocking up these lights at the design stage allowed for a perfect fit with the final cast column caps! Note that the images above show final assembly because I could not find pictures of the initial mock-up.
Another successful full-scale mock-up was done for the cast concrete column caps. I used 2x lumber and plywood - both common building materials that are easy to work with. After placing my full-scale mock-up directly on a newly-completed masonry column I found that I didn't like some of the proportions. I easily modified the mock-up back in my shop, then placed the revised mock-up back on the column to see if I liked it. The revised version was perfect!
The mock-ups each only took a few hours to build, and it was one of the smartest things I did on this project.
If you have a digital 3D design file you might consider having a scale 3D model printed. Check online for pricing and availability in your area or find a web-based 3D printing company. You can have 3D prints made at any scale, but it is common practice to use a small scale for multiple, early design iterations, and a larger scale or full-scale at final mock-up for final confirmation of the design.
Step 5: Templates
Templates are well-covered in all of the books and online resources I used, so please refer to other resources for detailed instructions. That said, templating is a pretty simple process. I used 3"-4" luan strips glued together with hot glue. Be sure to mark the top and bottom of the template. Important: be sure to flip the template over when assembling your form - the bottom of the template faces up in the form. You should mark the template bottom to say "(Up in Form)" or something like that to remind you.
For my project I had two castings that required templates. By far the more complex template was for the fireplace hearth. The hearth wraps around the fireplace and against the wide central column. The front is a semi-circular curve that overhangs the heart's concrete masonry unit (CMU) structure. Once the stucco finish was completed I could get started.
To make my template I began by cutting 3" or 4" strips of luan to lengths roughly that of each finished segment. I started with the edges around the fireplace and along the column. To get the radius I traced the shape of the curve onto a larger section of luan that overhung the entire curve. I strengthened the template and stabilized its shape by gluing on an extra cross-bracing luan strip.
A second, more simple template was needed for a unique wall cap section that had to fit around a metal rail post, which was bolted to the top of the patio wall's CMU structure. This template was made on site just like the other one and then placed in one of my adjustable wall cap forms (remember to place template upside down!). The modified form was completed with the addition of a foam knock-out for the metal post. More on that next in Step 6: Forms.
Step 6: Forms
Another important task is building a good form for casting. Most of the form-making techniques, tools and materials I used were as taught or sold by Fu-Tung Cheng. There are other ways to make forms, but Cheng's instructions were based on common and easy to find products including white melamine and black 100% silicone caulking. The later is used to seal form corners, while also creating consistently radiused corner edges for the castings. Refer to Cheng or other resources for more on form-making basics. Be sure to make multiple forms for something like pavers so that extra concrete does not go to waste after casting your primary parts.
I had to make forms for 33 wall caps, 7 column caps (two separately cast parts for each), a hearth and mantle. I needed to make a lot of forms and cast a lot of pieces, 51 not including mistakes! Because of the scale and scope of my project, I needed to make as many forms as possible to be reusable.
The large number of similar wall caps needed, along with their simple shape, made that part a perfect candidate to be cast in reusable forms. Working with custom cabinet builder Randy Womack of Redding, California, a prototype re-usable form was built. Once we had a good prototype Randy then made nine more forms, which were simplified yet accurate copies of the prototype form. To be re-usable the forms had to be:
- Strong and stable in shape and dimension
- Adjustable in length (allowed for variable cap lengths and consistent grout line widths)
- Impermeable by moisture (after each use the casting surface had to remain smooth and consistent for subsequent pours)
- Customizable (allowing for placement of knock-outs for concealed lighting fixtures, etc.)
I learned early on that plywood, medium-density fiberboard (MDF) and other paper-board surfaces that I used initially absorbed water after the first casting. For subsequent pours I had to refinish the forms' surfaces with water-resistant finishes. I found a perfect product at the local big-box home store, a plastic wall panel that I cut to size and placed into the curved surface of the mold that forms the crowned wall cap's top surface. The original forms' paperboard surfaces were now covered by re-usable and replaceable plastic form inserts - a major improvement in the form's design. Another big improvement was to waterproof the sides of the forms. I used Formica laminate that was finished by a local countertop shop, Coastal Counter Tops in Morro Bay, Ca. I also used pipe wrap tape to line certain parts of the forms.
To create recesses for the concealed wall cap LED lighting, I attached a MDF bridge across the form and mounted a foam knock-out to the bridge.
The half-round hearth was another fun and challenging form to make. Due to the size and shape of the hearth, it needed to be cast in three separate pieces - a center and two side or end sections. To achieve a perfect match with fit and finish I for the three-part hearth, I created a single form for all three pieces and used two vertical plexiglass dividers to create three separate pieces in a single pour. The back edges of the form were created with melamine walls, but another product was needed for the curved front edge. The curved form product I used from Cheng Concrete Exchange is discontinued but has been replaced with these foam strips, which can also be curved.
To establish the curve I drew a full-size pattern using my CAD program and then printed and taped it down onto the melamine, being sure to properly locate the pattern with respect to the template. Next I placed finish nails along the curve every few inches and then installed the foam curve form against the finish nails that were then removed. With the hearth form finished I built a simple form for the mantle - a flat slab basically just like a concrete counter top.
The final type of form for my project was for the column caps, which are inverted, two-step pyramids featuring integrated planters and recessed LED rope lights. Each column cap was cast in two pieces in separate melamine box forms and foam knock-outs for the inner void.
With the forms ready the next step is to prepare rebar, metal lath or wire reinforcing used to prevent the finished concrete pieces from cracking.
Step 7: Metal Reinforcement
Concrete is strong in compression but weak in tension. To minimize cracking, structural reinforcement should be integrated into all cast concrete projects. There are various ways to provide reinforcement including plastic fibers or glass fibers, but I chose to use #3 (3/8") reinforcing steel, or "rebar" for short. My local concrete and masonry vendor, Air Vol Block, provided most of the rebar bends based on my reinforcement drawings and dimensions. I bent the rebar for the curved hearth myself because those shapes were more complex and there were only three pieces to do for that. To make my bends I use a rebar bender borrowed from a contractor. Along with rebar I also used wire "remesh" and expanded metal steel lath. Rebar wire tied everything together.
Step 8: Mixing Concrete
It is said that if you can bake a cake you can mix concrete - although I have never baked a cake and cannot verify this. Even if this is true, if something goes wrong with a concrete mix the outcome can be an expensive and messy disaster requiring you to start all over. The concrete colorants are expensive and the entire process takes a lot of time, so be careful with this step! Refer to the colorant manufacturer for the recommended mix, and be careful to use precisely the correct amount of water per the manufacturer.
Mixing concrete was one of my biggest issues for my project, as it was my first time. As I learned by doing, too little water makes concrete difficult to work with and can cause too many large air bubbles. Too much water can cause the concrete aggregate to separate and settle to the bottom of the mold, leaving a wet soup of fines and colorant floating at the top, ruining the pour altogether. This latter case occurred two or three times for me, causing many days of expensive delays while forms, rebar, concrete mix and colorant had to be prepared all over again. Refer to both the concrete mix and colorant manufacturers for correct amounts. The colorant might contain add-mixtures that require a amount of water different from what is called for on the sack of concrete mix.
Step 9: The Pour
After all of the hard work and preparation comes the easy part (aside from mixing) - pouring the concrete into the forms! This is a two-person job, at least, especially for a large project like mine where each pour required multiple batches of concrete mix. You only have about 20 minutes before the concrete sets up, and in that time all pieces need to be poured and vibrated.
Vibration is important to release air bubbles near or at the surface of the castings. These air bubbles will affect the appearance and strength of the castings, and you probably won't get them all out. However minimizing them will make for a better casting. The air bubbles can be vibrated out with a concrete vibrator or a vibrating table, the latter is usually only available to large cast concrete shops because they are expensive. I borrowed a concrete vibrator from a contractor, which would be my recommendation if your are doing a one-off project. Be sure to thank your contractor friend with lots of beer or something they will appreciate!
Also, be sure to read up on how to place steel reinforcement such as rebar without causing something called "ghosting." Ghosting will ruin a casting because you will actually be able to see a "shadow" of the reinforcing steel on the surface of the finished piece if the steel is not placed correctly. A common cause of ghosting is to plunge the rebar down into the concrete after it has been poured already. This pushes the aggregate down into the casting and allows fines and colorant, etc. to float back up to the top, thereby leaving a ghosted image (change of color) in the shape of the rebar visible on the surface. The ghosting actually is integral to the casting between the rebar and the surface, so it is not possible to remove with slurry or polishing, which takes place after our next step - curing.To avoid ghosting place the rebar into the pour after the form is partially filled with concrete, then complete the pour over the top of the placed rebar.
Rebar placement is important as to structural integrity of the casting, so be sure to study up on that as well. The key to remember is that the rebar's job is to be in tension, so it is typically placed in the lower third of the finished piece (usually upper third in mold). Be sure to have at least 1" of concrete around all sides of the rebar to prevent spalling which is caused by moisture rusting the rebar, which then expands as it rusts.
Step 10: Cure
The easiest step! Let the parts cure under a sheet of plastic for about a week, or per the instructions provided by the colorant and/or add-mixture manufacturer. The only difficult part is being patient and letting this process complete before demolding.
Step 11: Demolding
When demolding be careful not to damage the castings with tools because the concrete is not fully cured until 28 days. Prise open by levering against the form itself, not the casting. Remove foam knock-outs with similar care. If you have access to compressed air that can be very helpful to pop out knock-outs and form sides without hurting the concrete. Be sure to have enough help to assist with heavy pieces that need to be rolled over or moved. Again, remember the concrete is still relatively soft, so be sure to use foam blocks to rest the demolded castings on for the subsequent processes including slurrying and sealing. I have kept my re-usable molds and knock-outs in storage under the house in case I ever need to re-make a piece.
Step 12: Slurry, Polish and Seal
To finish the castings the first step is to apply a slurry coat to fill in surface pores caused by air bubbles that inevitably settle against the form walls. A slurry coat is a mixture of colorant and fine cement without aggregates. Apply slurry by hand over all exposed surfaces of the casting, being sure to completely fill all pores. I was going for a monochromatic finish so I used color-matched slurry, but you can get creative using a contrasting or complementary color for your slurry coat.
Polishing is the next step and, like the slurry, I paid a professional to complete this step. Polishing is a wet-grinding process that creates a lot of muddy run-off. Professional cast concrete shops are set up for that and I was fortunate to have a great concrete counter-top company just 10 miles down the road - Wells Concrete Works in Los Osos Ca.
Because of the monochromatic finish desired by the client, we only lightly ground each piece using fine diamond polishing pads, exposing only the finest sand aggregates located at the surface. It turns out that this finish is a little more difficult to accomplish compared to the typical heavy grinding that exposes heavier stone aggregates because you have to be careful not to take down too much of the surface. You can always take more material away but once you've gone too far the piece is ruined. I recommend letting the pieces cure longer than a week if you are going for a lightly ground surface so it is easier to control how much material is removed. Cheng Concrete Exchange sells all of the polishing tools you will need.
Sealing is also a messy process but I was able to do it because it does not require any real skill. However I did use Wells Concrete Work's facility to do the sealing. This process is best done in cool temperatures and in the shade because you do not want the sealer to dry before completing the process. Apply sealer per the manufacturer's instructions. Use exterior grade sealer if your castings are going to be exposed to outdoor elements.
Step 13: Column Cap / Planter Modification
After delivering the lower portions of the column caps to the site I found that the conduits did not align well with the holes I had cast in place to fit tightly around each conduit. Even though I provided the contractor with a template to make sure proper conduit alignment was maintained, it just was not possible to maintain such precise tolerances during construction. Additionally I was not happy with the planter's soil depth. so I decided to cut out the bottom of each lower column cap so that there was 2" of additional soil depth. This made it quite easy to install the column caps. To make sure the structural integrity of the column caps was not compromised, I used a 2" diamond hole-saw to make the corner cuts first, then completed the cuts with a diamond bladed circular saw.
Step 14: LED Lighting
Two types of concealed, indirect LED landscape lighting were integrated into the project, each on separate circuits. Placement and light fixture types were considered early in the project so that electrical circuits and conduit could be property installed in the masonry walls during construction.
For primary landscape lighting, recessed wall-cap lights were installed in the center wall cap (centered between columns), washing each wall section in warm light, casting shadows off texture of the Mission-style hand troweled stucco wall finish. The wall cap lights were placed in recesses I made using foam knock-outs during casting. These lights run on a programmable timer that was wall-mounted along with an electrical sub-panel and transformers, hidden, yet easily accessible behind the barbecue.
Secondary accent lighting was integrated into each column cap planter. Waterproof LED rope lights were used for this application. As mentioned previously, early on in my planning and design I found out that these rope lights can only be cut at specific locations every three inches or so apart, as marked by a cut line printed on the rope. With this in mind, and before completing my design of the column caps, I bought a complete section of the rope light, including the 90 degree corner connectors and electrical leads. Mocking up the rope light allowed me to precisely design and cast my column caps so that the rope lights fit exactly as designed.
All lights were tested before final installation of the column and wall caps because they are practically impossible to service. With a life expectancy of 50,000 hours, the lights should be fine with no maintenance expected for decades, if ever.
Step 15: Installation
With a total of 51 finished pieces needed to complete the project, it took months to cast and finish everything. As castings were finished they were brought on site and staged, waiting for the last piece to be delivered so they could finally be installed by professional mason Leon Smith of Stonesmith Masonry in Templeton, Ca. I highly recommend Leon for any masonry job you might have on the Central Coast.
The wall caps were produced so that the fifth and final piece in each wall section was made to fit precisely, even though there was some small variation in the overall wall lengths between the various columns. To achieve a precise 1/4" grout line between each wall cap, a paint stir stick was placed between each wall cap as they were staged in their final locations. With the first four wall caps staged in place, the fifth wall cap was made to fit precisely in the final spot on each wall section thanks to my adjustable-length wall cap molds, which were particularly useful to cast these last wall caps.
Because the column caps have four equal sides I was able to turn them in the best direction needed to reduce the visibility of imperfections. This process, called "facing," is also used when planting trees, and it is important to do during staging and before final, permanent installation.
Because the brick-red colorant for the mortar bed is expensive, the mason used less expensive uncolored mortar beds, then raked out the exposed mortar so that colored mortar could be filled in with a grout bag for the finish.
Step 16: Waterproofing
Finally, waterproofing of the cast concrete column cap planters was important to prevent spalling and efforescence. Out of an overabundance of caution I elected to use two methods for waterproofing. I first applied a heavy, cement and acrylic (I believe) mix that was painted on with a masonry brush. I cannot recall the exact product, but it was something I found at Home Depot. In addition, my Dad and I also fiber-glassed the interior surface of each planter.
Special care was taken to protect the finishes of the entire patio project for both of these messy waterproofing applications. Plastic sheeting covered basically everything except the areas being waterproofed. I suggest anyone interested in waterproofing look into the system that works best for your project, as there are many different products available. Be careful to select the right product because some are simply water repellent and might not be a good long-term solution.
Step 17: Conclusion
While in hind-sight I vastly underestimated how difficult, time-consuming and expensive this project would turn out to be, I have absolutely no regrets for taking this on, am very proud of how it turned out and would certainly do it all over again. It must be said that the clients are my parents, so they were perhaps more understanding and patient than others might have been. One of the highlights for me on this project was getting to work so closely with my Dad, who helped me with the electrical, waterproofing and fireplace gas plumbing and electronics. Our family, friends, and everyone who visits just love this warm, inviting patio for which the careful planning and execution are evident in every detail.
If you have questions or are interested in my design services please do not hesitate to contact me and visit my website where you can find out more about my work.
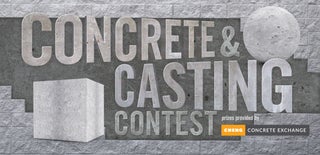
First Prize in the
Concrete and Casting Contest