Introduction: Articulated Sequential Interlocking Puzzle Snake
Just goes to show you that if you put enough of those $10 words together you can create a pretty impressive title.
It's a 3 dimensional bendy snake puzzle thing - made of wood!
I analyzed the various designs available on line. I was able to determine that there are several keys to successfully creating a great puzzle.
Each piece is cut at a 90 degree angle from the previous piece.
Each cut needs to be carefully made. A wire type saw blade that allows for sharper angles and better interlock of the pieces.
Sanding and finishing of the outer surface is easier if it is done before the pieces are cut apart.
There must be overlap between cuts or the pieces will not interlock.
The head piece must extend far enough back to allow the eye dowel to go through it.
No matter your skill set or budget, you should be able to build one of these fine animals and show them off to your friends and family.
I was inspired by the following Instructable:
https://www.instructables.com/id/Scroll-Saw-Puzzle-Cubes/
and the following websites:
http://poppyarts.com/woodpuzzlesbyclassmenagerie.aspx
http://chapmanpuzzles.com/
Step 1: Materials and Tools
Wood - A good piece of wood to start with is a 2 x 2 by 15 inch piece of pine. The size of this piece of wood makes it manageable and gives enough surface to make good cuts that will interlock properly.
Pine is easy to work with and sometimes you can get a piece with interesting grain that will really highlight your work.
Dowel - I had a piece of 1/8 inch dowel sitting around - I suppose a toothpick would work if you have one.
Saw - I have a Craftsman Scroll saw and I love it. I have several different types of blades, each with a special purpose. I use a skip tooth blade to make my long cuts on pieces that do not require great precision or where one side will be scrap so the width of the cut is not critical. I have a spiral blade that is basically a fine wire with a spiral wound cutting surface. This blade makes extremely fine cuts, as narrow as .035". It also allows for cuts in any direction, forward, backward or sideways and because it is so fine sharp corners are very easy. The perfect blade for cutting puzzle pieces. These blades came from Home Depot in packs of 18 or 36 for about $12. Smaller packs are available for less.
A little more about blades for scroll saws: I chose a reverse tooth blade for the puzzle piece cuts because I am cutting on a finished surface and the reverse tooth blade makes a much smoother cut on the bottom side. There is almost no need to sand or file the lower edges. The disadvantage is that the blade cuts only in one direction so when the piece is too long to completely rotate on the saw table, you have to remove it and approach from the other side. This problem goes away as the snake gets shorter. My opinion is that the smoother edge is well worth the extra work involved in making the second cut.
Coping saw - for those who have one and know how to use it, precision cuts are easily done with a coping saw. I have one, but chose the scroll saw for convenience and time.
Band Saw - I do not own one of these but clearly they are an ideal tool for this type of project. Especially if you are cutting thicker pieces of wood.
Sandpaper - I use a coarse grit (100) for the first pass. When I am satisfied with the surface I step up to a 150 grit and then finish with a 220 grit paper.
Drum sander - I purchased a 20 piece pack of drum sanding supplies at Harbor Freight for around $7.99. The largest drum in the pack is perfect for my project and saved me quite a bit of time smoothing the edges and rounding the corners.
Drill press - I have a small variable speed drill press from Harbor Freight. I use this to drill the eye hole with a 1/8" bit. I also use this to shape my wood with a drum sander.
Portable Drill - A hand held portable drill would work just fine for drilling the one hole that is required for this project. Use care to make sure the bit remains perpendicular to the work surface so the hole you drill goes straight through.
Finishing supplies - Bare wood is just fine for this project, but to give it a little flare adding a stain provides contrast between the cut parts of the pieces and the outer sides. The grain of the wood is also highlighted with the right stain. I have a can of Minwax One Step on the shelf that I used a few years ago to re-finish some window molding. One step means that I can save some time by staining and sealing with one product.
Latex or vinyl gloves - These are worn to protect the hands from the finish.
Paint brush, rags or paper towels - I use paper towels to apply the stain to my project. Sometimes a brush will leave stroke marks and you have to go over the surface with a rag or towel anyway.
Good wood glue for repairing any broken pieces.
Clamps to hold any pieces that had to be glued.
Safety equipment - Safety goggles, leather work gloves and a dust mask to protect you from the dust produce by sawing and sanding.
Pine is easy to work with and sometimes you can get a piece with interesting grain that will really highlight your work.
Dowel - I had a piece of 1/8 inch dowel sitting around - I suppose a toothpick would work if you have one.
Saw - I have a Craftsman Scroll saw and I love it. I have several different types of blades, each with a special purpose. I use a skip tooth blade to make my long cuts on pieces that do not require great precision or where one side will be scrap so the width of the cut is not critical. I have a spiral blade that is basically a fine wire with a spiral wound cutting surface. This blade makes extremely fine cuts, as narrow as .035". It also allows for cuts in any direction, forward, backward or sideways and because it is so fine sharp corners are very easy. The perfect blade for cutting puzzle pieces. These blades came from Home Depot in packs of 18 or 36 for about $12. Smaller packs are available for less.
A little more about blades for scroll saws: I chose a reverse tooth blade for the puzzle piece cuts because I am cutting on a finished surface and the reverse tooth blade makes a much smoother cut on the bottom side. There is almost no need to sand or file the lower edges. The disadvantage is that the blade cuts only in one direction so when the piece is too long to completely rotate on the saw table, you have to remove it and approach from the other side. This problem goes away as the snake gets shorter. My opinion is that the smoother edge is well worth the extra work involved in making the second cut.
Coping saw - for those who have one and know how to use it, precision cuts are easily done with a coping saw. I have one, but chose the scroll saw for convenience and time.
Band Saw - I do not own one of these but clearly they are an ideal tool for this type of project. Especially if you are cutting thicker pieces of wood.
Sandpaper - I use a coarse grit (100) for the first pass. When I am satisfied with the surface I step up to a 150 grit and then finish with a 220 grit paper.
Drum sander - I purchased a 20 piece pack of drum sanding supplies at Harbor Freight for around $7.99. The largest drum in the pack is perfect for my project and saved me quite a bit of time smoothing the edges and rounding the corners.
Drill press - I have a small variable speed drill press from Harbor Freight. I use this to drill the eye hole with a 1/8" bit. I also use this to shape my wood with a drum sander.
Portable Drill - A hand held portable drill would work just fine for drilling the one hole that is required for this project. Use care to make sure the bit remains perpendicular to the work surface so the hole you drill goes straight through.
Finishing supplies - Bare wood is just fine for this project, but to give it a little flare adding a stain provides contrast between the cut parts of the pieces and the outer sides. The grain of the wood is also highlighted with the right stain. I have a can of Minwax One Step on the shelf that I used a few years ago to re-finish some window molding. One step means that I can save some time by staining and sealing with one product.
Latex or vinyl gloves - These are worn to protect the hands from the finish.
Paint brush, rags or paper towels - I use paper towels to apply the stain to my project. Sometimes a brush will leave stroke marks and you have to go over the surface with a rag or towel anyway.
Good wood glue for repairing any broken pieces.
Clamps to hold any pieces that had to be glued.
Safety equipment - Safety goggles, leather work gloves and a dust mask to protect you from the dust produce by sawing and sanding.
Step 2: Design Pattern
Draw pattern onto wood.
The design of this puzzle allows for a great deal of flexibility.
Since my goal is to build this without spending a lot of money, I am using scrap wood, along with tools and supplies that I already have. You may or may not have everything that you need, regardless, purchasing the required items will still make this a very affordable project.
Using the drawing as a guide, with a pencil, draw a simple pattern on the top and side of your wood. Keep it simple. (A note on using a pencil - my 7th grade wood shop teacher told us not to use ink because it would soak into the wood. You could sand it off of the surface but if you put a finish on the wood, the ink or more accurately, the oil in the ink would seep to the surface and ruin your finished work. Probably reducing you final grade from a B to a C)
Take care to make the lines dark enough that you will be able to see them when you begin cutting.
Notice the recommended cuts use the edge of the wood whenever it is practical. This is to prevent long straight cuts that usually turn out a little wavy when done with hand tools.
The design of this puzzle allows for a great deal of flexibility.
Since my goal is to build this without spending a lot of money, I am using scrap wood, along with tools and supplies that I already have. You may or may not have everything that you need, regardless, purchasing the required items will still make this a very affordable project.
Using the drawing as a guide, with a pencil, draw a simple pattern on the top and side of your wood. Keep it simple. (A note on using a pencil - my 7th grade wood shop teacher told us not to use ink because it would soak into the wood. You could sand it off of the surface but if you put a finish on the wood, the ink or more accurately, the oil in the ink would seep to the surface and ruin your finished work. Probably reducing you final grade from a B to a C)
Take care to make the lines dark enough that you will be able to see them when you begin cutting.
Notice the recommended cuts use the edge of the wood whenever it is practical. This is to prevent long straight cuts that usually turn out a little wavy when done with hand tools.
Step 3: Drill Eye Hole for Locking Pin
Drill hole for eye – 1/8 inch diameter (or match the size of the dowel that you have on hand)
After you have drawn your pattern onto your wood. Locate the eye and drill a 1/8 inch diameter hole through the wood from side to side.
This hole will become more important as we get further along in the process.
The dowel that is inserted through this hole is used to keep the last puzzle piece from sliding out of place and since each piece holds other pieces in place, this is the pin that keeps the whole thing together.
After you have drawn your pattern onto your wood. Locate the eye and drill a 1/8 inch diameter hole through the wood from side to side.
This hole will become more important as we get further along in the process.
The dowel that is inserted through this hole is used to keep the last puzzle piece from sliding out of place and since each piece holds other pieces in place, this is the pin that keeps the whole thing together.
Step 4: Cut Off Top Scrap
Cut along pattern line to remove TOP
In choosing the order of the cuts for this project keep a couple things in mind.
When you cut a piece of wood on a scroll saw, it is easier to cut a pattern when the surface that is against the table is flat .
So if I cut the top off first, I will have one of the sides flat on the table which makes it easier to use the scroll saw material guide to hold the piece firmly on the table and makes it easier to trace the pencil line pattern on the wood with the blade.
The second cut I decided to make was down one side and then the other side. These cuts are made with the bottom of the piece flat on the table. The top surface is uneven because we have cut the top off, but having the bottom smooth still allows for easier cutting down the sides. Additionally, by cutting the sides now, you can match up any imperfections to retain symmetry in your design.
Last - turning the snake on the side, you can cut the bottom pattern.
There is a trick that you can use to make these odd shaped cuts easier: Keep the scrap pieces that you cut off and tape them back in place on your wood before you start cutting a different side. This will allow you to maintain a smooth surface against the saw table as you make your cut. If you use masking tape or clear packaging tape you will reap the added bonus of your wood sliding easier across the table surface. Be sure to remove the tape as soon as you finish the cut as the adhesive can sometimes make the wood difficult to sand or finish if left on too long.
In choosing the order of the cuts for this project keep a couple things in mind.
When you cut a piece of wood on a scroll saw, it is easier to cut a pattern when the surface that is against the table is flat .
So if I cut the top off first, I will have one of the sides flat on the table which makes it easier to use the scroll saw material guide to hold the piece firmly on the table and makes it easier to trace the pencil line pattern on the wood with the blade.
The second cut I decided to make was down one side and then the other side. These cuts are made with the bottom of the piece flat on the table. The top surface is uneven because we have cut the top off, but having the bottom smooth still allows for easier cutting down the sides. Additionally, by cutting the sides now, you can match up any imperfections to retain symmetry in your design.
Last - turning the snake on the side, you can cut the bottom pattern.
There is a trick that you can use to make these odd shaped cuts easier: Keep the scrap pieces that you cut off and tape them back in place on your wood before you start cutting a different side. This will allow you to maintain a smooth surface against the saw table as you make your cut. If you use masking tape or clear packaging tape you will reap the added bonus of your wood sliding easier across the table surface. Be sure to remove the tape as soon as you finish the cut as the adhesive can sometimes make the wood difficult to sand or finish if left on too long.
Step 5: Prepare to Cut Sides
Redraw pattern onto cut surface
When you cut off the top of the material, you also cut off the lines that you drew that showed you where to cut the sides.
You will need to re-draw these lines onto the top surface so that you can cut them off from the top of the work piece.
In the previous step I mentioned that you could tape the cut off scrap from the top, back in place. This is difficult to do if you have only cut small corners off as in the drawing in step 2. It is easier to just draw your design back onto the wood and proceed.
When you cut off the top of the material, you also cut off the lines that you drew that showed you where to cut the sides.
You will need to re-draw these lines onto the top surface so that you can cut them off from the top of the work piece.
In the previous step I mentioned that you could tape the cut off scrap from the top, back in place. This is difficult to do if you have only cut small corners off as in the drawing in step 2. It is easier to just draw your design back onto the wood and proceed.
Step 6: Cut Outline of Sides
Place flat (BOTTOM) side down and cut along the pattern line that you just drew, remove sides.
The snake that I have pictured doesn't match the pattern in step 2. Here I am cutting a snake with a wider head than body so I had to make a VERY long cut down the sides of the body. My cut ended up a little uneven and required some extra work to smooth it out later.
RECOMMENDATION: Keep with the simple pattern for your first puzzle. After you have completed a puzzle, then go a little fancier.
The snake that I have pictured doesn't match the pattern in step 2. Here I am cutting a snake with a wider head than body so I had to make a VERY long cut down the sides of the body. My cut ended up a little uneven and required some extra work to smooth it out later.
RECOMMENDATION: Keep with the simple pattern for your first puzzle. After you have completed a puzzle, then go a little fancier.
Step 7: Prepare to Cut Bottom Scrap
Now that you have cut off the Top and Sides, you will need to re-draw your pattern lines onto one side so that you can make you cuts to remove the bottom material.
Step 8: Cut Bottom Scrap
Cut along pattern line to remove BOTTOM
This can get to be a little tricky since you no longer have the supporting pieces on the sides to allow the piece to slide smoothly across the saw table.
This would be a good time to reattach a cutoff piece - especially for the tail section since that cut is longer.
This can get to be a little tricky since you no longer have the supporting pieces on the sides to allow the piece to slide smoothly across the saw table.
This would be a good time to reattach a cutoff piece - especially for the tail section since that cut is longer.
Step 9: Smooth the Surface
Sand sides to smooth surface.
Since we are making a sculpture of sorts, it is not vital to have the sides true and square. It is more important to remove any cut marks that remain from the sawing process and to create a general flow along the surface of the snake body.
I used a drum sander in my drill press to smooth the sides of my snake.
Allow the sanding surface to work the material, do not press into it as you will tend to make the surface uneven and clog the sander with wood dust making it ineffective.
It is better to make several gentle passes from one end to other barely removing any material with each pass.
I wear a pair of leather work gloves while doing this as it is very easy to accidentally touch the spinning drum as you work.
Since we are making a sculpture of sorts, it is not vital to have the sides true and square. It is more important to remove any cut marks that remain from the sawing process and to create a general flow along the surface of the snake body.
I used a drum sander in my drill press to smooth the sides of my snake.
Allow the sanding surface to work the material, do not press into it as you will tend to make the surface uneven and clog the sander with wood dust making it ineffective.
It is better to make several gentle passes from one end to other barely removing any material with each pass.
I wear a pair of leather work gloves while doing this as it is very easy to accidentally touch the spinning drum as you work.
Step 10: Round the Corners
Round corners but leave surfaces as flat as possible to make puzzle piece cutting easier.
Remember the flat surface on the saw table makes it easier to cut the odd shapes that we will be cutting in later steps. If you sand the body completely round it will make it difficult to cut the puzzle pieces later.
Remember the flat surface on the saw table makes it easier to cut the odd shapes that we will be cutting in later steps. If you sand the body completely round it will make it difficult to cut the puzzle pieces later.
Step 11: Apply Finish
Stain and finish entire piece.
Applying stain at this point has several benefits.
It is easier to apply the finish to the bigger piece than it is to apply to individual, small pieces.
The finish on the outer surface will provide an attractive contrast to the surfaces of the cut pieces and make the puzzle more interesting.
The disadvantage of staining it now is that the finish may get damaged in successive steps and will need to be touched up.
Applying the stain after the pieces are cut would allow you to create a contrast between the top cut pieces and the side cut pieces similar to the rattlesnake pictured here:
http://chapmanpuzzles.com/rs.htm
Applying stain at this point has several benefits.
It is easier to apply the finish to the bigger piece than it is to apply to individual, small pieces.
The finish on the outer surface will provide an attractive contrast to the surfaces of the cut pieces and make the puzzle more interesting.
The disadvantage of staining it now is that the finish may get damaged in successive steps and will need to be touched up.
Applying the stain after the pieces are cut would allow you to create a contrast between the top cut pieces and the side cut pieces similar to the rattlesnake pictured here:
http://chapmanpuzzles.com/rs.htm
Step 12: Terminology
I have created an image and identified some of the parts of a puzzle piece so that it is easier to explain the process.
Step 13: Prepare to Cut Puzzle Pieces
In Pencil, lightly draw puzzle piece cutout pattern down the length of the body.
Things to remember:
Each piece interlocks with the 2 pieces behind it. SO you have to have overlap.
Each interlocking tab needs to be wide enough that it will not slip out through the adjoining channel. Make sure each interlocking tab has a wide section (bulb), then a narrow section (connector), then another wide section (body).
Exaggerate the curves and angles because they will be diminished slightly as they are cut out.
Before you cut pieces out of your project piece - use another scrap to make some practice cuts. This will allow you to familiarize yourself with the requirements of your particular cutting tool and wood. It will also let you get your cutting skills tuned to the needs of cutting puzzle pieces out of wood blocks.
Things to remember:
Each piece interlocks with the 2 pieces behind it. SO you have to have overlap.
Each interlocking tab needs to be wide enough that it will not slip out through the adjoining channel. Make sure each interlocking tab has a wide section (bulb), then a narrow section (connector), then another wide section (body).
Exaggerate the curves and angles because they will be diminished slightly as they are cut out.
Before you cut pieces out of your project piece - use another scrap to make some practice cuts. This will allow you to familiarize yourself with the requirements of your particular cutting tool and wood. It will also let you get your cutting skills tuned to the needs of cutting puzzle pieces out of wood blocks.
Step 14: Make a Few Practice Cuts on Scrap Wood
It is a good idea to make a few practice cuts on similar sized scraps of wood so you can fine tune the speed of the cuts and the shapes you are cutting.
Step 15: Cut Puzzle Pattern Starting at the Head
This step is where we start separating the individual puzzle pieces.
Beginning at the head, from the top, we make a cut that has an hourglass shape.
This cut MUST extend past the eye holes and contain a bulb at the point farthest to the rear. The bulb keeps the nose piece from sliding out forward and it also keeps the 3rd piece from sliding out sideways. The eye dowel is then used to lock this piece in place so it doesn't slide out either up or down.
After the first cut, remove the cut piece and set it aside.
Rotate the work piece 90 degrees so it is on its side.
Make the second cut.
Remove this piece.
Rotate the work piece back onto its bottom and make the third cut.
When you are using a scroll saw take your time and let the blade do the cutting work. Move the material slowly into the blade so that you do not bend the blade as you cut. You could end up with cuts that aren't vertical and the pieces won't fit the way you want them to fit.
Beginning at the head, from the top, we make a cut that has an hourglass shape.
This cut MUST extend past the eye holes and contain a bulb at the point farthest to the rear. The bulb keeps the nose piece from sliding out forward and it also keeps the 3rd piece from sliding out sideways. The eye dowel is then used to lock this piece in place so it doesn't slide out either up or down.
After the first cut, remove the cut piece and set it aside.
Rotate the work piece 90 degrees so it is on its side.
Make the second cut.
Remove this piece.
Rotate the work piece back onto its bottom and make the third cut.
When you are using a scroll saw take your time and let the blade do the cutting work. Move the material slowly into the blade so that you do not bend the blade as you cut. You could end up with cuts that aren't vertical and the pieces won't fit the way you want them to fit.
Step 16: Whoops!
I squeezed a little to hard on this piece.
Not to worry, I have a bottle of Elmer's Carpenter's Wood Glue Max handy.
Not to worry, I have a bottle of Elmer's Carpenter's Wood Glue Max handy.
Step 17: Finish and Assemble
After all of your pieces are cut, carefully remove any wood splinters with a small file, emery board or piece of sandpaper. Try not to remove too much material as it will affect the way the pieces fit together and the appearance of the finished puzzle.
When you are happy with the edges, check to make sure there are no scratches in the finish and touch up where needed.
Assemble the snake from tail to head.
Interlock a piece, hold in place, then interlock the next piece.
After installing the last piece (Nose piece) carefully slide the dowel through eye holes. I had to open up the eye hole a little bit. Probably because of the stain. Anyway I went ahead and drilled it at 5/32 to give a little bit of room to insert it.
You can now cut the dowel to length and shape the ends.
Congratulations! You have completed your project.
When you are happy with the edges, check to make sure there are no scratches in the finish and touch up where needed.
Assemble the snake from tail to head.
Interlock a piece, hold in place, then interlock the next piece.
After installing the last piece (Nose piece) carefully slide the dowel through eye holes. I had to open up the eye hole a little bit. Probably because of the stain. Anyway I went ahead and drilled it at 5/32 to give a little bit of room to insert it.
You can now cut the dowel to length and shape the ends.
Congratulations! You have completed your project.
Step 18: Going Further
There are many variations to the basic puzzle.
Try making a snake that has a mouse inside of it.
Create another 3 dimensional animal.
Make a 2 tone creature.
Make a puzzle sculpture of your favorite pet.
Share your critters and take pictures of them.
Post those pictures of your creations for all to see.
Maybe I will try to make a sculpture puzzle of one of my dogs.
TWEEKS : There are a few things that you can do to change the outcome of your puzzle.
If you want it to be more flexible - use a wider cut between the pieces and/or make shorter body sections.
You can also sand or file some of the material between the pieces to make the gap wider.
To make it more rigid - make very fine cuts between pieces and/or cut body pieces longer.
Look for wood with high contrast in grain, this will make your puzzle much more interesting.
Try making a snake that has a mouse inside of it.
Create another 3 dimensional animal.
Make a 2 tone creature.
Make a puzzle sculpture of your favorite pet.
Share your critters and take pictures of them.
Post those pictures of your creations for all to see.
Maybe I will try to make a sculpture puzzle of one of my dogs.
TWEEKS : There are a few things that you can do to change the outcome of your puzzle.
If you want it to be more flexible - use a wider cut between the pieces and/or make shorter body sections.
You can also sand or file some of the material between the pieces to make the gap wider.
To make it more rigid - make very fine cuts between pieces and/or cut body pieces longer.
Look for wood with high contrast in grain, this will make your puzzle much more interesting.
Step 19: What to Do With a Laser Cutting Tool
Several years ago, before the economy went into it's downward spiral, I devised a business plan that was centered around a laser cutting tool. The plan included cutting custom model parts for hobbyists, creating custom scale model structures for a local architectural company - with laser engraved 'paintings' and light switches on the walls etc. I also was looking into creating precision wood projects such as the puzzle boxes that I have so painstakingly cut out by hand. My goal was to have enough different types of business to be able to eventually make a full time business out of it. So I decided that I would also custom cut fabrics for patterns, etch photographs into wood and essentially utilize every possible opportunity to make something with my laser cutter.
As the economy turned, I missed my opportunity. The machines were too expensive to risk starting such a venture and with the poor state of the economy, it would be very difficult to make it as a start-up.
Here is my opportunity to blow the dust off of the business plan, update the many modeling plans I already have and set about creating my new business venture. Doing something I love.
"Choose a job you love, and you will never have to work a day in your life."
— Confucius
Step 20: Other Things I've Made
Here are some videos of my puzzle boxes.
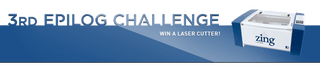
Participated in the
3rd Epilog Challenge