Introduction: Audioengine A2+ Speaker Volume Repositioner
I absolutely love everything from Audioengine. I have two sets of these speakers, their 512 portable Bluetooth speaker, two of their N22 amplifiers, a B2 wireless speaker, an S8 sub, and their D3 headphone DAC.
If you're in the market for new audio gear I highly recommend them.
So to start of with, along with many of you that find ourselves in a new telecommuting environment, I've been spending a lot of time recently upgrading my home office to make the transition as smooth as possible. In regards to music, I've moved one of my sets of A2+ (and its mated S8 sub) into the office since I spend so many hours a day listening to music while working. (Not having to wear headphones all day is sure a big plus.)
However, my one and only complaint with the A2+ speakers is that the volume knob (and On/Off switch) is on the back. And, yes, while that's not a huge issue. ("Geez dude, just get up and reach behind them!") It was enough to bug someone like me whose always trying to streamline and improve efficiency in virtually everything I possibly can. Plus I thought there would be a lot of people with the same complaint and would welcome a fix. And its a cool fix at that, I must say.
(Also, my Form 2 SLA printer from formlabs.com is literally 3 feet behind my chair in my little home office, so ignoring it is kinda hard. And I'm constantly looking for any excuse to keep it running just because its so much fun to work with.)
Supplies
1.) 1/4" Rod - Any material (though I recommend metal), solid round
- Rod must be exactly 0.250", even 0.252" or 0.248" will cause problems
- Qty 2, 0.575" long minimum for the small axles
Qty 1, 6.75" long minimum for the main axle
https://www.acehardware.com/departments/hardware/m...
2.) Super Glue
https://www.amazon.com/Gorilla-6770002-Micro-Preci...
3.) Hot Glue Gun and Glue Sticks
4.) Double Sticky Tape
https://www.amazon.com/dp/B00OXVG9FW/ref=twister_B...
5.) 2 Part Putty Epoxy
https://www.acehardware.com/departments/paint-and-...
6.) Tools for Cutting Metal - Dremel with Cutoff Wheels, Die Grinder, Lathe, Etc.
7.) Philips Screwdriver
8.) 3D SLA Printer (Set to 50 Micron)
https://formlabs.com/3d-printers/form-2/
9.) Petroleum based grease or other lubricant (optional)
Step 1: Design Choice #1 - Move to Stand? Nope!
I was going to simply open the back of the speaker (the left speaker houses the DAC, Amplifier, and all input and output connections) and reroute the volume knob's potentiometer to the front and integrate it into some angled stands I was 3D printing. The angled stands were a redesign I did based on the licensed accessory you can buy from Audioengine (link below and left image above is from their product page).
But the entire electronics assembly is fully potted and thus physically moving the knob was not possible! (Right image above.) This is proof of the high quality of Audioengine's design and build.
What to do now, though?
Hmmmmm. Gears? That might work! So design on location choice #2 began.
(Here's a link to the stands from Audioengine:)
Step 2: Design Choice #2 - Gear Train? Yep!
The image above shows the CAD model of the concept using a quantity 4, 1:1 gear train.
A gear train labeled 1:1 means:
No mechanical advantage (So, torque applied to gear #1 = Torque exerted (minus friction) at gear #4)
Same rotational magnitude (& velocity) (So, 20 degrees of rotation to gear #1 = 20 degrees of rotation to gear #4 (and at the same speed of rotation))
Basically, the knob, now on the front, will operate in the exact same way as the original!
Step 3: Gear Train Explanation
With four gears (or any even number), the rotational direction from the input to the output (new front position of the knob to the rear location of the potentiometer) is reversed, which is actually what we want.
If an odd number of gears were used, then the input to output direction would be the same, and would result in turning "UP" the volume on the front causing the actual volume to go "DOWN". See image above for explanation.
Another way to think of it is: When viewed from the front of the speaker a CW rotation of the repositioned knob will cause a CCW rotation to the potentiometer on the back. So that: Volume UP on the front = volume UP on the back.
Step 4: Location Reasoning
See image above for explanation as to why this location was chosen.
Step 5: 3D Printed Part #1 - "Front Pivot"
The foundation of the overall project is in the two corner braces that support the main axle. There are no features to attach anything to on the front upper left corner of the speaker (however, there is on the back) and I didn't want to drill holes into the speaker housing or do anything that would permanently scar the speaker.
This entire modification can be completely removed from the speaker returning the speaker to its original condition.
With both the front and back pivot parts, there are three large (around 1 square inch) faces that provide sufficient contact area to rigidly hold the axle in position. And the axle itself provides additional support to hold all the pieces together. Additionally, the corner brace design serves another purpose, which it to allow for a rather long receiving hole for the axle. This keeps the axle coaxial from front to back and ensures smooth movement when rotating the axle.
Attachment of the front pivot 3D printed part to the speaker is via a single piece of the gorilla double sided tape applied to the surface opposite the emblem. (If you don't recognize the emblem on the front, it's the Audioengine logo.)
NOTE: If you attempt to make this project, do NOT add additional pieces of the gorilla tape to the other two faces thinking it will be held better. Doing so will misalign the front axle hole from the rear hole. Those two surfaces should be in contact with the speaker surfaces with no glue or tape in between.
Step 6: 3D Printed Part #2 - "Rear Pivot"
This part transfers the rotational movement of the knob, now on the front, over to the original volume position though the quantity 4 gear train (explained earlier).
Opposed to how the front pivot part attaches (with a single piece of tape), this one is mounted using the upper right screw in the back panel. Simply remove the screw, place the 3D printed rear pivot part on the speaker's rear upper right corner, and reuse the same screw. (Do NOT over tighten.). The screw goes into the middle hole.
The other two holes adjacent to the screw-mounting hole are for the fixed small axles that will receive the middle two gears.
The raised boss around the three holes allows for the mounting screw to sit below and out of the way of the gears in the final assembly. The gusseting around this raised boss helps to keep this face rigid and perpendicular to the other two faces. (Earlier iterations of the design resulted in this face warped outward either from the printing process or the post cure. The gusseting fixed that problem.)
Attachments
Step 7: 3D Printed Part #3 - "Small Gear"
TIP: Mcmaster-Carr website (and catalogs if you are lucky enough to have one) are a treasure trove of information.
The gears in this project are based on this gear:
https://www.mcmaster.com/6832k59
In fact, the starting point for modeling on this project was to use their CAD files they provide for most parts. (See right image above.)
The center hole on this gear is a clearance fit for the 1/4" metal rod listed in the supplies.
Attachments
Step 8: 3D Printed Part #4 - "Knob Gear"
This gear is modified for a tight line to line fit (not a press fit and not a clearance fit).
The four small hole are "squeeze-out" holes for hot glue to flow through when attaching to the main axle.
Step 9: 3D Printed Part #5 - "Volume Gear"
This gear is intended to mate onto the splined shaft of the potentiometer. It is just barely a press fit.
Similar to the knob gear, there are "squeeze-out" holes for the hot glue when attaching. However since only the main hole ID is different between this and the knob gear, I added another hole to differentiate the two:
- 4 hole pattern gear goes to the main axle
- 5 hole pattern gear goes to the potentiometer
Step 10: Assembly Start - Full Parts List
All parts needed to start assembly are shown above:
- 6 3D printed parts (front and rear pivot, and all 4 gears)
- Main axle (.250" OD, 6.673" long)
- 2 short axles (.250", 0.548" long)
- Volume knob
NOTE:Axle lengths are exact dimensions per the CAD model. The large axle can be undersize by up to 1/8" and still function, while the short axles can be longer. Any extra length on the short axles will just protrude further from the back surface.
Step 11: Assembly Step #1 - Knob Install
This is probably the trickiest part of the entire project. The volume knob after removing from the rear panel of the speaker. (And it does come off by just pulling directly away, but it is very tight.)
The volume knob is made up of two parts:
- Outer metal shell
- Inner soft plastic sleeve with an ID smaller than the 1/4" rod we are inserting into it
I tried, even knowing it wouldn't work, to drill the sleeve to the larger ID, but it just grabbed and pulled completely away.
Problem: Now the ID of the metal shell of the knob is way too large for the 1/4" rod.
- Use a scrap piece of wood or other material and using a drill press (the hole needs to be very perpendicular), drill a 0.250" hole through it. (TIP: If using wood and the resulting hole is slightly too large, add some water to the hole and the wood will swell slightly to make a tighter grip on the metal rod.)
- Insert the main axle so the amount protruding is 0.535"
- I used the only washer/bushing I had with a 1/4" ID to trace a marking circle on the front surface to use for reference (in hindsight I should have used a forstner bit to make a counterbore on the topside)
- Use the metal 2 part putty epoxy and fill the knob about halfway full
- Insert knob into the axle until the knob is resting flush on the scrap material surface and centered visually to the circular mark
(The picture shown above on the right was the first attempt using hot glue. It later separated, under pretty low stress, so I chose to redo with the metal epoxy.)
Step 12: Assembly Step #2 - Gluing Small Axles
- Insert the short axles into the rear pivot part so the metal is flush to the backside.
- Use normal super glue (not the gel type) to squirt the glue into the three smaller holes surrounding the center holes. These smaller holes allow the super glue to wick fully down into the space.
- Clean up the excess glue
Step 13: Assembly Step #3 - Front Pivot Attach
As stated earlier, only apply the 2 sided tape to one surface. The surface is indicated in the image above.
When installing this part, ensure the two other surfaces (TOP and LEFT) are fully in contact and slide the part aft until the tape makes contact with the FRONT surface. Press firmly.
NOTE: This tape is not ridiculously strong like some other types. It can be easily separated if need be and doesn't leave any residue.
Step 14: Assembly Step #4 - Rear Pivot Attach
For the rear pivot, here are the steps:
- Remove the top right screw (First image above.)
- Position the rear pivot and reinstall the screw just until snug. Do NOT over tighten.
- Ensure its fully seated on all three sides
Step 15: Assembly Step #5 - Gears
The outer two gears (knob and volume gear) have added features to "capture" the middle two gears. So you have to install the small gears first.
Knob and volume gears are attached by hot glue:
- If not already done, insert the main axle with the epoxied knob from the front so the exposed end of the axle protrudes on the back (Sorry, I missed taking a picture of this step.).
- Fill the center hole of each gear almost full with hot glue
- Insert onto main axle and volume post while engaging the gear teeth
- Allow the excess hot glue to squeeze out the 4 and 5 hole patterns
- Allow the hot glue to fully cool and resolidify
- Use a razor blade to cut away the glue that squeezed out
Step 16: Final Test
In the short test video above, it starts in the OFF position, turns ON, goes to full volume, stop, then goes to lowest volume, and ends in the OFF position.
It's actually so smooth, I decided not to add any kind of lubricant or grease, as it would most likely just transfer to somewhere else and make a mess.
Was also tempted to paint at least the rear facing surfaces of the gears for better aesthetics, but decided against it as its not seen from the front.
IMPROVEMENTS:
If I were to make again these are what I would improve:
- Don't paint. I hate painting (and I mean HATE painting.) I've always had this saying. "I'd rather build an entire house than paint a single room in that house.". I tried artist brushing some surfaces and that turned out bad and I had to scrape off and refinish the surface. Then I decided to just add a layer of gloss poly and that turned out horrible, so had to remove all that. And finally got a somewhat decent coat of gloss black on the two large parts. Next time I would just leave grey or switch over to black resin in the printer.
- Do a better job of getting the knob attached to the axle. Its smooth and mostly unnoticeable (to other people) but its not perfectly centered and has a slight "wobble"
- Make the opening for the screw slightly bigger. After my horrible paint job, the walls were a bit narrower where the screw recesses and I had to grind down the head OD of the screw to fit right.
- Make the middle small gears a little bit thicker or place some Teflon washers between the gear and the rear pivot surface. Those middle gears have a bit too much play axially.
Step 17: In Use
I retract my earlier satirical statement ("Geez, dude just get up and reach behind them!").
This is a MAJOR improvement.
- Easily reached for simple adjustments (you know how some songs are louder than others, or when your favorite song comes on and you want to jam out!)
- Quickly turn them off when you get a phone call
- And just in simply turning them off. Before the modification, I would mostly leave them on but turn the music source off, which just wastes electricity.
Definitely one of the better DIY projects I've done in a while.
Hope you enjoy. Please let me know if I can be of any assistance for those that have these speakers and want to tackle making this improvement. I may also entertain selling kits (if that's allowed).
Thanks for taking the time to read through my Instructable.
(Still printing the other stand for the right speaker.)
Step 18: Update 4 May 2020
Was having some issues with my 3D printer. Back up and running now. Just wanted to update with a few images of the whole project now fully complete.
Also added here are stl files of the stands. The one with "LW" is a thinner walled version (LW=lightweight). The first one was fine but it was just way too bulky, so on the second one I thinned the walls just to save resin from the printer (it's expensive). If you FDM print these, I'd use the non-LW version.
For the feet on the stands, I created protrusions in the part that hold these little rubber bushings (last image above). I get them from Ace Hardware in their electrical section. Please message me if anyone needs to know the PN of those.
(The color on the stands is Meadow Green, a new color, from Rustoleum.)
Step 19: Update 21 May 2020
A kind reader pointed out my utter bone-headed move of somehow reversing the speakers. Seriously, I have no idea how I made that glaring mistake and didn't notice it whatsoever during this entire build.
Hopefully, it hasn't induced a case of audio dyslexia.
(Step 17 and 18 - in those images, the modified speaker should be on the left not the right.)
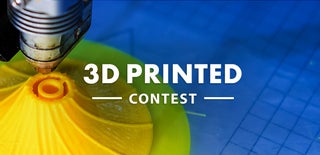
Participated in the
3D Printed Contest