Introduction: Aviator Inspired Desk
I graduated from Virginia Tech in 2009 with a Bachelor's in Aerospace Engineering. I love airplanes and stumbled across Restoration Hardware's Aviator collection. I bought a couple pieces on sale, including a desk chair. The matching Aviator desk is crazy expensive and also looked more Star Trek than Aviator. Not really my style. I decided to make my own to match the chair instead. This desk was partially inspired by the chair and partially inspired by another instructable: Birch And Aluminum Desk by zwild1
Step 1: The Base
I choose to make the base of the desk out of galvanized pipe to get more metal into the build. My desk is is 66" long by 34" wide, but you can choose to make yours any size you like. I also used 3/4" pipe, but you could use a smaller diameter. To build a base similar to mine, you'll need:
Materials
(1) 56" pipe
(6) 24" pipes
(4) 4" pipe nipples
(2) 2" pipe nipples
(6) tee fittings
(4) floor flanges
(4) end caps
If you decide to change up the length or width of your desk remember that your fittings on either side will add roughly 2-3 inches overall.
Assembly
Each leg is assembled as follows:
floor flange -> 24" pipe -> tee fitting -> 4" pipe nipple -> end cap
Each pair of legs is joined widthwise as follows:
leg -> 24" pipe -> tee fitting -> 2" pipe nipple -> leg
Finally, the two pairs of legs are joined lengthwise with the 56" pipe.
Step 2: Building the Top
For the top, I glued (3) 1x10s together. I ripped one of the 1x10s to 9" in width. I needed an overall width of 29" because I made a frame for the top which adds 5" overall. You can simplify your top by skipping the frame and just using your glued boards as the top.
The bottom frame is made by 1x4s, the top frame from 1x3s. This gives a nice lip to set your glued up boards into. You'll need:
(2) 66" 1x4s
(2) 34" 1x4s
(2) 66" 1x3s
(2) 34" 1x3s
(1) 61" 1x4
*NOTE: My cuts are mitered. If you choose to make straight cuts you will need to adjust your lengths.
I like to use the cutoffs from my mitered cuts to help clamp the corners together. Just put a *small* dab of glue on the cutoffs and glue them to the boards you wish to join. When dry, you can glue the corners together by leveraging your clamps on the cutoffs. When your joint is dry, you can knock the cutoffs off with a hammer. You can also use corner clamps. I used both methods.
After both frames were dry I glued them together.
Next I drilled two pocket holes on both ends of the 61" 1x4 and then attached that to the middle of the bottom (1x4s) frame for center support. If you don't have a pocket hole jig you can wing it or use brackets.
I also trimmed down four of the cutoffs into nice even triangles and glued them into the inside corners of the bottom frame. This gave me more room to position the floor flanges when attaching the base.
Step 3: Finishing the Surface
The first step in finishing the desktop was sanding it down smooth.
Next, I attached the base to the top by drilling screws through the wholes in the floor flanges into the top. You could remove the top for finishing but I decided to leave it on because the stain easily wipes off the galvanized floor flanges.
I always like to use wood conditioner before staining because it helps the stain penetrate more evenly. I chose to use Rustoleum Kona wood stain because this color is the closest match to my black-brown Ikea bookcases in my office.
After two coats of stain, I sealed the wood with two coats of polyurethane.
Step 4: Creating the Aluminum VT Logo
I used aluminum flashing to make the VT logo. First I downloaded the image from the internet. Next I used some basic image processing skills to create the outline. I selected the VT shape based on color, shrank the selection by a few pixels, and then deleted everything inside the selection. This leaves just the outline. I used MS Paint to print the actual size of the image over 12 pieces of paper.
Once I had my outline I taped all the pieces together and measured off the lengths of flashing I would need. To cut the flashing, I found it easiest to duct tape the flashing flat to a piece of cardboard and cut straight through the tape. Make sure you wear gloves. Aluminum flashing is sharp! I knew I should have, but didn't and I sliced my finger as a result.
Next I placed the template onto a piece of cardboard. I lined up each piece of flashing on top of the template and used a scrap piece of wood as a straight edge to make the cuts.
I glued the flashing pieces together using 3M's Super 77 spray adhesive. I cleaned them off using brake parts cleaner. It works great for cleaning the pipes as well.
Once glued together, I used a wire brush on my Dremel to create the swirls. Afterwards, I was told by a friend that if you start in the center and work outwards in a circle, overlapping each circle by half each time, you will end up with a 3D effect. I didn't know this at the time, so you may have better results if you go this route.
I also used the spray adhesive to stick the flashing to the desktop. It didn't work too well sticking to the poly. You may be better off trying a different adhesive. I was able to get it to stick long enough to place the lexan sheet on top.
Step 5: Angle Iron Border
The angle iron border with screws is meant to mimic the riveted look on my chair. You'll need:
(2) 66" pieces
(2) 34" pieces
*Again, my pieces are mitered so if you use straight cuts you will need to adjust your lengths accordingly.
I used a reciprocating saw with a metal cutting blade to cut the angle iron. Make sure you use a file to knock off the rough, jagged edges from the cuts.
I used #14 x 1.25" flat phillips head wood screws to screw the angle iron border onto the desktop. These screws were fairly pricey so I didn't use one in each hole, just every 5-6 or so.
Make sure to pre-drill the holes. Also, because the screw widens at the top, once you drill your pilot whole switch to a larger bit and drill into the lexan only in order to countersink your screw. This is very important because it also prevents the lexan from cracking due to the pressure of the larger screw head.
Step 6: Enjoy!
Enjoy your awesome new custom desk or table. The lexan makes it easy to clean up those coffee spills. If you don't have one of the newer laser mice that can operate on glass like surfaces you're going to need to dig up an old school mousepad :D
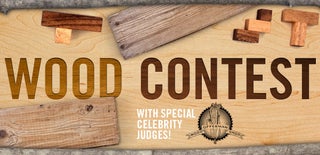
Participated in the
Wood Contest