Introduction: Backyard Railroad Tie Spiker
In my backyard, I'm building an F-Scale dual gauge railroad. This is when 1:20.3 G-Scale is treated like 3-foot narrow gauge, which implies that standard gauge is about 2.8" in width between the rails. For the entire circuit and including sidings and spur tracks, I need to make 165' of track. That's 495' of aluminum rail, 1,980 ties made from recycled pallets, and 11,880 spikes! I really don't want to hammer each spike into the ties and gauge the track as I go along on my hands and knees. My solution was therefore to build a machine that I could load the nails into at the correct spacing, and have them sunk into each tie with the pull of a lever. There are many gauges of railroads, both in prototype and in model, so my goal here is to show you the concepts I am attempting here so that you may try it for yourself and hopefully make it work even better.
Step 1: Machining the Parts
This hand-powered tool has been machined out of aluminum and stainless steel with a wood handle. In the photographs for this section, I've shown how I staged where to put the retractor spring bolts, as a lot of this tool was engineered as I made it. After the aluminum parts were finished, they were finished by "jitterbugging"; sanding with a handheld vibratory sander. This gives them a uniform appearance before being sent out for anodizing, which of course is optional. The main body is a composite of two blocks, one to mount the assembly to a vice, the second to serve as a place for the nails to sit in slots while the wooden tie is forced over them. The slider shafts and bearings for the main rotating shaft are all mounted to this block. The slider block which shuttles the tie over the nails has been bored out .001" above the diameter of the hard-anodized aluminum slider shafts. The stainless steel plates provide a spacing for the nails to protrude through the tie while still allowing for changes in angle as in the case for making banked curves. Between the tie-push and the main block is a small strip of sheet metal with slots in it for the nails to slide through. This is to keep the nails upright, parallel and properly spaced throughout the spiking cycle.
Step 2: Assembly
As this device was designed as I went along, it was assembled as I went along as well. If something didn't quite fit right, I would take it right back apart and put it back on the lathe or mill to shave off some material. Oilite bronze bushings were pressed in to form the bearings for the linkages. I found very quickly that it's best not to tighten everything until it all works in a smooth fluid motion. Tightening slowly while working the components ensures that they have found their natural home where they can slide freely.
Step 3: How It Works
These pictures were taken while I was test fitting it up, so the mounts for the nail slider are not shown. In principle, when the operator pulls down on the lever, the two linkages on the sides will pull the slider block into the tie, and force the tie over the nails. The machine works very well, but there are some bugs that should be looked at. Wood will split when a nail too large is driven through it. I elected to soak a few of these pre-cut ties in water for a few days before spiking, and it worked perfectly. In the future I might like to make a clamp that bites down on it to help keep it from splitting, but for now, it's a handy little machine that is reliable, easy to use, and will make handmade railroad track a very pleasant experience.
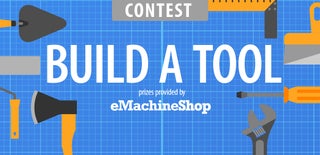
Participated in the
Build a Tool Contest 2017