Introduction: Bicycle Caliper Brake Power Modulator (Doubler)
This modification to a bicycle caliper brake doubles the force applied through the brake, while requiring twice as much cable to be pulled through by the brake lever. I designed this to improve the braking and safety on my road bike. Another option would have been to replace the whole caliper with a dual-pivot type, but I wanted to keep this Campagnolo brake with the rest of the groupset, and I also like customization and uniqueness in bicycles. This mod could also be useful if using a (long pull) V-brake lever with a caliper brake.
CAUTION: this modification may not be practical on cheap, thinly constructed, weak alloy caliper brakes because they may break under the extra force. Look for calipers that are thicker, or steel ones, that can handle the extra force.
Step 1: Make the Pulley Wheel
The pulley wheel is made from a jockey wheel, taken from an old 5-6 speed bicycle rear derailleur. The jockey wheel needs to be cut down to a circular shape and then have a track/groove cut into it. To do this, first make a mini lathe for the jockey wheel to spin on, using a drill and a 6mm bolt with the head cut off. The jockey wheel will need the bushing removed (put the dust caps back on after the bushing is removed), and is then sandwiched between 2 nuts on the cut-off bolt. The threadless end of the bolt is locked into the drill chuck. If using a hand drill, the drill should be sandwiched in a vice with thick cardboard or towel around it to protect the drill case from crushing - don't over tighten in the vice! This is to hold it steady while shaping the jockey wheel.
CAUTION: wear safety googles while spinning the drill, and keep it at a slower speed. It may kick the hacksaw, and it may spit out bits of plastic if done carelessly.
With the jockey wheel spinning on the drill, gently press a hack saw blade against the wheel to cut it into a disc 25mm/1" diameter. It helps to regularly clean off the plastic granules from the blade. Once you have made the disc, cut a groove into the middle with the hacksaw. Do this without spinning the drill at first, to mark the line of the groove. After it is marked, spin the drill and hold the hacksaw blade against it to create a straight even groove, and finish with the corner edge of a file to create a V that the brake cable can easily slip into (brake cable is 1.6mm diameter).
Once the wheel has been shaped, remove from the lathe and refit the bushing with a little grease, and fit the dust caps (these will sit loosely either side until it is bolted into place).
Step 2: Make the Anchor Bolt Which Clamps the Cable
The piece used to make the anchor bolt can be found on an old single-pivot brake caliper holding the barrel adjuster (the hollow bolt that can be screwed out to increase the brake cable tension).
This piece has an oval/egg shaped section behind the thread. This needs to filed down to a circular shape, without damaging the threads too much. Shape it until a 6mm washer can fit over it.
The arm will need a 2mm hole drilled into it which the brake cable will thread through. The cable can then be clamped into position with a nut and some suitable spacing washers. Use a centre punch to mark the hole position. TIP: a centre punch can be made by grinding a worn out hardened steel Philips-head bit to a point.
Step 3: Attach the Pulley to the Caliper Arm
The brake caliper consists of two arms. Before being modified, the brake caliper had an anchor bolt and nut clamping the cable on one arm, while on the other is a barrel adjuster which holds the end of the brake cable housing.
Remove the anchor bolt and nut from the caliper arm. Widen the hole where the bolt was removed, drilling it to 6mm.
CAUTION: make sure there is enough material after drilling to 6mm. There are jockey wheels (to make the pulley) that take a 5mm bolt which could easily be substituted and make the hole smaller if required.
Now fit a 6mm bolt through the hole and fit the pulley wheel onto it, securing with a nut (ideally a nylock nut). Test that the pulley spins freely.
Step 4: Attach the Anchor Bolt With the Barrel Adjuster
The anchor bolt attaches with the barrel adjuster. Remove the barrel adjuster, then thread it into the anchor bolt, and thread it back into the caliper arm. The thread on the barrel adjuster needs to be M6, to match the thread in the anchor bolt you made.
Step 5: Thread the Cable Around the Pulley and Clamp to the Anchor Bolt
The brake cable is not flexible enough to make the tight turn around the pulley arm without first being bent into that shape. Insert a new brake cable (the original cable will likely be too short) through the brake lever and brake cable housing to the caliper. Pull the cable with one hand while pulling the brake lever with the other hand; this is to ensure the cable is running smoothly and that it has been pulled through as much as possible. Now start making small bends in the cable, either by hand or with pliers, and begin working it into shape. Avoid bending the cable severely in one spot - be gentle and work in small increments to create a nice flowing bend to match the shape of the pulley.
NOTE: in order to get the cable bend in the right spot, clamp the brake pads against the rim using a pedal strap or cable tie. This allows the cable to be pulled through to the correct position. If you make the bend first, then bring the brake pads in to the rim, then you'll find that the bend will be in the wrong spot (i.e. not around the pulley).
With the cable bent around the pulley, insert the end of the cable through the anchor bolt. Use washers as required on the anchor bolt so that when the nut is fastened, the cable is pushed flat against these washers. While holding the caliper in, pull the cable through and tighten the nut lightly to clamp the cable. Test the brake lightly to see if the cable is tight enough, or too loose or too tight. If it needs adjustment, hold the caliper in again with one hand, then loosen the nut, reposition the cable and tighten it back up lightly with the other. Once the desired cable tension is achieved, then tighten the cable fully. If the cable is crushed repeatedly by fully tightening the nut against it, then it will eventually become brittle and start breaking strands of wire. That's why I suggest tightening lightly until it's where you want it.
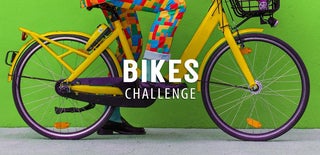
Participated in the
Bikes Challenge