Introduction: Bicycle Chariot: Santa Sleigh Edition
Hello World!
This project started as a favor to a mentor, but as fun projects do it became much more.
About this 'vehicle':
- This is a chariot. By this I mean that it is 3+ wheels and front drive.
- This is holiday themed.
- I butchered lots of french bikes to make this #sorrynotsorry.
- I have access to many resources that you may not. This is ok, I will go through how to make this with the bare minimum of tools/equipment.
- The design is not amazing, this is my first version of a chariot, my first time trying front drive. Feel free to critique me, I love to learn + fail better.
- There are reindeer puppets involved.
If making art bikes/freak bikes is of interest to you I assume/expect you have some knowledge of bicycles. This instructable will not address bicycle mechanic skills. With that said this bike is not meant to be used as a commuter, due to that reason I intentionally used old bikes + parts that are obsolete.
What is it good for? This chariot is good for sitting in and parade riding and as an example of a pedal powered puppet system...
SKILLS WE WILL USE:
- Welding (Flux core, MIG or TIG- whatever you're comfortable with/have worked with/ have access to...)
- Basic Metal Working knowledge (i.e. using an angle grinder + fixturing techniques + common sense)
- Basic Bicycle Mechanics (i.e. you know when to use grease vs lube, you have taken apart a bike or two before + put them back together successfully)
- IMAGINATION (if you are here I assume you make things + know how to use your brain)
Step 1: Be Safe + Assemble Tools + Parts
*this is me, not wearing a jacket, because I valued my personal comfort in the short term (i.e. it was hot.) Got horrible arc burn, wear a welding jacket!
If you know how to weld I assume you know how to weld safely.
TOOLS:
- Welding apparatus
- Angle grinder - with grinding disc, wire wheel, cut off wheel
- Measuring tape
- Sharpie!
Parts:
- 3-5 Steel bike frames (preferably similar in size)
- box tubing/round tubing- sturdy stock
- Bike components
- 3 wheels (one with coaster break, preferably smaller, 2 of same size)
- bottom bracket with pedals, cranks, etc.
- chains (2)
- derailleurs (2)
- free wheel hub + free wheel
- I used machine tubing + rod for my puppet system, you all have imaginations + access to different hardware, I trust your abilities.
*use common sense and be safe!* I have a pair of prescription safety glasses- best purchase of 2016 #3M for life!
Reference book that is awesome:
If you want to get into building freak bikes as a vocation this is the bible
Step 2: Mock Up Your Design
*These are all the bikes + parts put together (upside down) to get a general idea of the form + figure out how everything is going to be attached*
Two methods were used for this design process:
- Drawing
- Ramshacklery
Drawing - sketch out your ideas, starting from the original bike forms. Make them life sized- trace you bike's profile to get an idea of how it could look and where you bottom bracket will be.
Ramshacklery - mock up your design with bike parts. Pictured above. Remember it's smarter to cut things later than earlier.
During the mock up you may want to cut your bikes in pieces - feel free to do so-
Design realities to keep in mind:
- Your legs will be in multiple positions, think it through- maybe make a cardboard leg with articulated knee to test
- How do you plan to steer?
- What are the bicycles and tools you have on hand?
- Center of gravity. Where will the most weight on the bicycle be?
Be smart- use the parts of the bikes you have, be realistic about your skill set.
More weld + metal = better structural integrity
This bicycle is designed to support my weight not to go fast.
Step 3: Start Marking + Cutting + Paint Removal
Once you have a good configuration that generates confidence it's time to start marking and cutting.
Use your sharpie to mark where you want to cut. Remember it's easier to subtract material then to add material.
When joining tubing together you want to cut what I will refer to as fish mouths - also called mitering or coping.
Like the second picture above *insert drawing*, the easiest + fastest way to do that is with the 1/4" hard disc. The point of doing this is to get everything to fit together as nicely as possible for ease of welding + a stronger joint.
Remove paint + chrome before you weld. Use a sanding disc.
Notes about fork extensions:
- Tack each drop to a piece of scrap/old axel to keep them together/properly aligned before cutting
- Sleeve the tubing of the fork! Lots of stress will be on an extended fork and you want more support then butt welds.
Step 4: Dry Fit + Make Adjustments
Once you have your vehicle tacked together it's time to dry fit!
This step is important to determine details like chain line and steering. Plus it will help you make better decisions about what to reinforce + making better before laying your final beads.
After this fit up I determined that I needed to add more supports to the fork and a back rest plus give the chariot more structural integrity overall.
The last photo is the dry fit with some tacking and the fork fully welded together.
Step 5: Weld It All Together!
Once you are happy with the design + the fit up weld it all together.
You now have a front drive tricycle style art bike!
Above is a photo of me on the v1 assembled bike. There is no puppet system included, I made an initial attempt using the front wheel to drive the axel of the puppet system but it did not work out...
*Reasons for v1 puppet failure:
- the rod used for the axel was too malleable
- the rod did not have enough traction for the wheel
- the difference in circumference between the wheel and the rod meant that the rod would go waaaaay too fast
These were addressed and solved in v2 with chain drive!
Step 6: Let's Talk About This Puppet System
It took me about a week to make the actual art bike- it was assembled on site as part of a demo: making sparks.
The puppet system is the real gem that took months to make.
After the failure of the front wheel to get the axel moving I moved the system to the back of the trike.
It's made from 1/8" rod and mechanical tubing that fit around the rod, plus a hinge to tension the hub against the wheel.
In the above photo v2 you will notice:
- still a friction drive system
- the spring tensioner is welded to some plate, is welded to the bicycle frame
- now we're cooking with gas
- still too fast!
After some thought I decided to attach the drive system to a free wheel hub on the back of the bike so I could change the gear ratio if needed to slow down the system or speed it up. More options sometimes means more fun.
Step 7: Puppet System V3
Here's a back and side view of the puppet system.
This is the final version of the puppet system - dry fit then weld.
Attaching a separate axel to the bicycle was a good call. It made for a pretty good drive system.
Here's some video showing the Santa Sleigh in action with cardboard cut out reindeer attached to the rods.
The next step is painting!
Step 8: Paint + Reassemble
Painting Process:
- sand current paint job to rough it up
- wipe down with de-natured alcohol
- prime
- if you're doing lighter colors
- if you want to have stripes/ some 2 tone pattern. Tape off areas to maintain first layer of color.
- add color
There are instructables about this I'm sure you can find some if you have questions or want more details.
Once you've painted and paint is dry (~24hr assuming you're using spray paint) time to reassemble and show off your new ride!!
Be sure the properly grease those bearings, and for added flair add some cardboard reindeer !
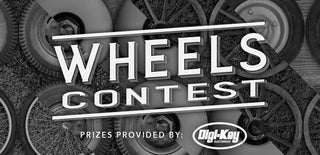
Runner Up in the
Wheels Contest 2017
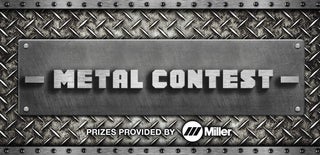
Participated in the
Metal Contest 2017