Introduction: Bicycle Frame Bag!
Do you hear that sound? Not the horns, engines, or back up alarm from dump trucks. And I'm certainly not talking about the hustle of city traffic or the non-stop talking in your office. I'm talking about the sound of your tires crunching over hardpacked gravel, the birds chirping, and that gentle sound of wind blowing in treetops. This is bikepacking. A simple concept of packing all your lightweight (or not) camping stuff on your bicycle and just getting away from it all. No designated route necessary, just a will to move your body and bicycle. Despite the dreamy sounds I described, it's okay if you're in a super urban environment like I am and have to suffer in group campgrounds.
But why? Because a generic frame bag does not maximize your storage space and custom frame bags can be pricey. Generic frame bags only get minimal options and custom frame bags keep adding prices for options you may want. This Instructable is all about how to build a frame bag fit for your bicycle and utilize the lost space in the main triangle.
I cannot urge you enough to please read through all the steps first and make mental or written notes. A fair amount of visualization is required to complete this.
Supplies
Hard stuff:
- sewing machine
- zipper foot (not required but certain very helpful)
- fabric pins or clips
- seam ripper
- tape measure
- marking device (colored pencil, chalk, pen...)
- scissors (or another cutting device)
- cardboard
- straight edge (not required)
Soft stuff:
- Velcro or another non-copyrighted hook and loop fastener
- nylon webbing if you decide to go the daisy chain route along the top tube
- fabrics (choose your own adventure here, I went with 1000d Cordura, I would also recommend ordering more than you need to experiment with what your sewing machine can handle)
- zippers (recommend longer than needed so you're not confined to exact dimensions)
- threads (nylon recommended)
I would recommend waterproof fabric with the explicit understanding that it's not really waterproof once you punch in thousands of tiny pin holes. You can waterproof the seams to get around this problem but then you still must consider the zipper. Are you using a waterproof zipper too? So many decisions here!
Determing how much fabric you'll need is something only you can determine with your bag dimensions.
Step 1: Template Your Frame.
Grab your cardboard and template your frame. Tape works well or you can have a helper hold it up. Use a marking device of some kind and trace the interior and cut along your lines. In theory, it should fit nicely inside the frame now. If not, use more cardboard and try again. This is a great starting point that we’re going to refine. I used cord wraps I had lying to hold it in place and evaluate my decision. You could use this to also measure how long your attachment straps will need to be for a later step, but I tend to just eyeball that one. Once you a refine the cardboard cutout, put your bike away or place it nearby to admire its beauty and keep you motivated.
Decision point: What features do you want? Perhaps a cut out along the top tube that you can slide your hand around to lift the bike up? A thin pocket on one side that is non waterproof but easily accessed? Do you want a daisy chain attachment point along the top of the bag where you can use hook and loop attachments, or would you prefer one long piece of sewn in hook and loop fastener? Are you going to carry a hydration bladder on your back or are you using water bottles? Do they mount on the underside of the downtube or are there only mounts on the top side of the downtube? This might be a necessary modification but a really easy one. Contemplate here as well if you really overstuff the bag, is there potential it may interfere with your front chainrings? If so, perhaps moving the bottom of the bag to just parallel or a little below the top ring isn’t a bad idea. I say parallel or below because it’s impossible to stuff the bottom 1/2” beyond capacity that it may hit the ring teeth.
Maybe take a few hours flipping through pictures on Google to figure these ideas out now and make notes right on your cardboard template. Don't worry about messing it up; it's cardboard. Costco/Sams Club/recycling centers has cardboard in bulk for free.
Step 2: Cut Out Your Fabric.
Decision point: Do you want your zipper to have a hood to help keep mud and grime out? If so, cut one side to the template with the 5/8" seam allowance all the way around. The side with the zipper will still maintain a 5/8" seam allowance but will stop at the zipper and we'll actually have two different parts to cut: below the zipper and above the zipper. For cutting out fabric below the zipper, lay your template on the fabric and make two marks on either side of your template zipper line. Remove the template and add 5/8" seam allowance above that and cut this out. Place your template back down and mark out the fabric for above the zipper giving a 5/8" seam allowance. Once you reach the zipper line, remove your template because it's free hand time. It may be worth pinning your fabric at the zipper line to remember where you'll freehand. Essentially, we're duplicating the angle of fabric above the zipper line because this will flipped over and match the template angle. Words are confusing, pictures help. I strongly recommend you use paper to play with and understand how this process works before you cut your material. For more information, look at step three pictures.
Lay our your material on a flat surface and place the template down. Either pin in place or freehand if you're feeling extra confident. I'm a horrible tailor so I must pin in place. Pin on the inside of the lines so when you cut, the fabric doesn't slide away from its duplicate. (This was a lesson learned in version 1.). Add a 5/8" seam allowance all the way around. (Note: don't forget to flip your template over if your material has a wrong side and a right side, otherwise you'll end up with two of the same side and waste material.)
Now that your main pieces are cut out, you can can start cutting top, bottom, front and back materiail to width Utilize scraps as much as possible! 2.5" finished width is the most common size I saw during my research but feel free to experiment. Regardless of how much you want your finished width to be, do NOT forget to add 5/8" seam allowance to both sides which will give us a full 3.75" wide piece for a finished width of 2.5".) Know how I know this? Lesson learned in version 1.
Even though hook and loop attachment is included in the picture, let's leave that for a later step.
Decision point: Are you a massive human and can easily handle 3" of fabric between your knees when you're pedaling? Go for it! Plan on packing nothing but a cup for river water and a tarp for cover? Psh, you won't even need this bag! What I'm saying here is customize this bag however you want. If you need to understand what all these dimensions look and feel like, get some more cardboard, dimension it to the template you have and add 2.5 all the way around. Tape it to your frame and go ride around the block. How'd that feel? Adjust as necessary.
Step 3: Zipper Sew In.
First, admire your bicycle and the pile of fabric in front of you.
After you're done admiring, you'll need to gather the zipper foot, and zipper side panel which should consist of a zipper, above the zipper piece, and below the zipper piece. Attach the zipper foot.
Start with the "below the zipper" material because it's easiest and makes the top substantially easier. Fold and press the 5/8" seam allowance over wrong sides together, pin the material and zipper together. The sewing will occur on the right side of the zipper and you should be looking at three layers of material: the zipper and the folded over seam allowance. Sew in the fabric along the zipper as shown in the pictures.
The top is a little more difficult to describe and if you need video lessons, query "lapped zipper" for more information. All we're doing is taking our 5/8" seam allowance, pressing it over like the bottom half but giving a little extra to create a hood. What makes this difficult is we're working with a template with only a little wiggle room. I'll try to describe it:
- Lay your other panel wrong side up.
- Lay your zipper panel with the "below the zipper" material and sewn in zipper on top of the other side panel. Line them up very nicely at the bottom and sides.
- Lay the "above the zipper" material right side up and align it to the non-zippered panel along the top.
- Fold the bottom of the "above the zipper" material under itself and align it to the top of the zipper, pin or clip in place. This should be the moment of realization of how much hood you have to cover the zipper. Unclip the top of the "above the zipper" material and sew the zipper onto this piece.
- Once you've sewn in the zipper to the top piece, you can flip it back over and you should be looking at a near finished product. If you need to align the other panel to the zippered panel side to determine your hood length again, now is the time.
- Sew the hood down, the same as you did the zipper. The zipper foot should pick up zipper height and you can continue sewing along.
If you're this far, you're doing great!
Step 4: Visual Zipper Tutorial.
This is an alternative view to the zipper sew in because it can be kind of confusing.
- In the first picture I'm using a scaled down view of the fabric agains the template.
- Lay the top of the fabric against the non-zippered panel and pin or clip in place.
- Fold under the bottom side of the "above the zipper" piece and align to the top of the zipper and clip or pin in place. Sew a line along this and you're almost done!
Note: this is also a nice technique to determine the size of the fabric to cut during step 1.
Step 5: Dividers.
Decision point: Are you electing to sew in dividers? Now is the time.
I am sewing them on this bag because I think they help keep the bag from being overstuffed, pulling at the edges, and potentially ballooning into your legs if you manage to pack the kitchen sink. Plus you can divide items in your bag.
Choose your length, I didn't measure but instead held up the hook and loop against the bag and guessed. Use your hem tape and sew the hook and loop attachment along the middle. I chose hem tape because it's easily flexible unlike my 1000d Cordura. (My hook and loop measurements vary here and yours will to depending on how much space you have to work with.) Once the hook and loop is sewn to the hem tape, measure where you want it on your side panels, pin and sew. The best way to get these dividers to the same location is to place the two main panels together, push pins through and make a mark on the inside of the fabric. You probably should measure it because you’ll need to duplicate the location on the opposing panel. It would be functional but not perfect if you just eyeball it. But some honesty here is okay: we’re not producing this to sell.
Step 6: Let's Pin and Sew.
Now it gets serious. In this step, we're going from "what have I started" to "look at what I've made!"
But first, hook and loop attachments need to be cut to length and adjusted for your style. I elected to cut longer strips around 6" long because it's easy to trim excess but hard to attach more. The part I struggled most with here was determining which way the hook and loop needed to face so when we turn the bag right side out, the hook and loop lines up correctly. For the top of my bag, I wanted a longer strip of hook and loop that is parallel to the top tube. This required a little creativity. I used scrap fabric cut into a rectangle and sewing the hook and loop to it. Then I pinned it in place on the bag and set the incomplete bag on my frame to determine how much I needed to adjust these parallel hook and loop pieces.
Take one of your big side panels and lay it right side up. It's easiest to start with the long top/bottom/front/back piece here so grab a long side and lay it good side down. (If you're lost here, both good sides - meaning what you want to face outwards - should be facing each other.) Use your template to determine where you want your hook and loop sewn in. (Note: if you forget to add it here like I did, use the seam ripper to cut our some thread, insert your hook and loop, and sew back over everything. If you maintain your seam allowance when sewing, nobody will be the wiser because it's all on the inside.) Sew down the sides using your 5/8" seam allowance. Note: Pin and sew to your corners 5/8" seam allowance exactly but do not sew all the way to the end; this will show up very well in your finished product.
From here, it's a repeat process for all the 3.75" wide strips we cut earlier. Remember, 2.5 is the finished width and we're using 5/8" seam allowances. Make sure the edges align to the main side panel including the corners.
Now grab the remaining opposing panel and repeat the pinning bit. Caution: unzip the zipper once you sew past it before you complete sewing up the panel! This will make your life way easier in the next step. If you manage to forget this, you should be able to still undo the zipper but it’s just more agony. (Lesson learned version 1.)
Step 7: Here It Comes!
Well, this is it. Reach your hand through the zipper and flip your entire bag right side out and manipulating the fabric in the corners. At this point you should have a completed frame bag that matches your bike frame dimensions exactly and the attachment points should be sewn in.
You've worked hard to get here, lace your new custom bag to your bicycle and go ride! Show it off to your friends and offer to teach them how to do this too!
Step 8: Final Thoughts.
- This custom bag is custom for a reason. Experiment with sizes, tapers, zippers, pockets, etc until you're sick of the project.
- If this is your one shot to get it right, maybe using some basting stitches is in your favor until you get it absolutely correct. But I recommend using really cheap scrap fabric and building a practice bag. It helps in the long run and I created a total of three bags. The first one for theory, the second for practice, and the third for a finished product.
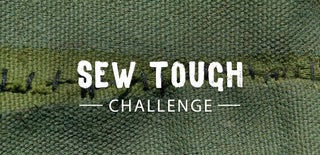
Grand Prize in the
Sew Tough Challenge