Introduction: Bicycle Safety Aid Prototype: 3D Dynamic Wheel Light
This is an ible on a prototype design for a safety aid for cyclists. This design is just a prototype so full details on materials and the full construction process is just a general idea. Particularly, the wheel light is aimed at cycling work commuters to be more visibly from the side, especially at intersections. The wheel light is designed to be controlled by an accelerometer which changes the brightness and colour of the bikes light depending on the bikes speed (not included in this design). The light is designed with a special 3D illumination space which makes the wheel largely visible and bright.
General Materials/Cutting list (for one wheel)
2 x Polyethylene/Polypropylene plastic shells: 22'' by 22''
1 x RGB LED strip 5m: (The design uses 3.5m)
12cm long thick plastic tube to be recessed:
Plastic pipe 40mm long (I used an old drainage pipe)
3 x 18650 Rechargeable Batteries.(Yet to make a protection charging and discharging assembly)
Soldering iron, solder and electrical tape
Hot glue gun
Duct tape/Gaffa tape
Pliers, Wire snippers, Stanley knife
Drill and 7mm or similar drill bit
Large compass cutter
Small compass cutter or chassis die tap
Step 1: Making the Light Dispersion Shells and Testing the Replacement Battery Pack
First of all, we made 2 plastic shells which slid through the spokes of the wheels and fit inside. Two plastic shells were cut using a compass cutter. I made the shells fit a 22 inch wheel, so they are 22" in diameter (basically to cover the spokes of the wheel). After this we cut a custom hole so that the shell can fit around the hub of the wheel and also a curved slit so that the shell can be easily threaded inside the spokes of the wheel.
After doing this we trialled a battery pack to replace the standard wall supply for the RGB LED 5m strip. We used three 18650 rechargeable batteries in series to provide 1.1Ah. So the wheel light can run for 2 hours before needing to be recharged. (Note that since this is a prototype we are yet to integrate a protection circuit for recharging and discharging of the 18650 batteries which is essential for safety)
Step 2: Making the Air-holes for the Shells
Here we made 6 air-hole pieces to connect the two shells and to help reduce wind effects on pushing the whell while riding. The pieces were recessed on a lathe so that the inner lip is 45mm to match the hole in the shell, whilst the material between each of these recesses is about 5mm more in diameter (This keeps the shells apart and act as wedges to hold the shells securely under the spokes of the wheel.
Step 3: Mocking Up the Arrangement of LED Strip Inside the Shells
I decided to investigate two arrangements of mounting the LED strip in my development, I mocked each arrangement up and also mocked up the air-holes and their positioning with the LED strip:
*The first arrangement uses 2.1m of strip
*The second arrangemt uses 3.5m of strip
I chose the second arrangement even though it uses more strip because it is the brightest and covers the most area in the light shells. Basically, the second arrangement is best suited to light sufficiently the 3D illumination space created by the plastic shells. It is also important to note that when the wheel is turning the lights should 'merge' and create a more bright effect.
I also decided the position in which the LED strip faces (the strip has a 180 degree view area). To light the wheel and disperse the light between the light shells meant that facing the strip inwards was best. However I did decide to face half of the strip to each side of the wheel. Whilst the remaining joing strip in between (arounfd the hub and air-holes) would make the shells light up more.
Step 4: Cutting the Air-holes
At first a compass cutter was used to cut the holes in the plastic shells for the plastic air-hole parts to fit. After the compass cutter gave a rough finish we switched to cutting the holes using a die cutter (45mm). After drilling a pilot hole for the cutter, punching each of the holes and trimming the flash I did the same on the second plastic shell.
Step 5: Connecting the Plastic Air-hole Parts
Using the soldering iron to melt one plastic shell to the plastic air-hole parts we bonded them together. It was a lengthy process and slightly dangerous. Also the strength of the bond was only just viable for the prototype. Next time we might melt both sides of the parts together or use glue.
Note: We drilled some holes in this plastic sheet for fastening cable ties to connect the slit.
Step 6: Marking Out the Strip, Making the Hub Cover, Etc
Basically we prepared for the final assembly in this step:
1) Marked out the arrangement path of the LED strip.
2) Battery pack and LED controller position
3) Made a plastic ring out of drainage pipe (45mm, the same size as the plastic shell centre hole). We slit the ring to fit it around the hub and duct taped the ring at the slit in place so it wouldn't contract whilst gluing. I then fired up the glue gun and glued down the plastic shell to the hub cover- this kept it in place strongly.
Note: the plastic hub cover is here so that the LED strip isn't wrapped directly around the hub itself and therefore the device can be easily removed in the future.
4) Cable tied the slit so it stays closed and even
Step 7: Gluing Down the LED Strip
After gluing down the LED strip to the chosen arrangement for a few turns I noticed that I had glued down the wrong connector for the controller. After ripping it up again and using the hot glue gun again I was back in business, gluing down the strip strongly against the shell. When gluing the strip with the LED's touching the side of the shell, I tried to glue only to the side of the strip or between each LED. However the glue ended up flowing onto the LED's and obscuring them slightly. When I tested the wheel light I noticed no significant difference especially as the wheel was moving and both sides of the light ended up shining equally. I also hot glued the controller down, trying to allow easy access to the power cable and LED cable yet still allowing space for the second shell to squeeze inside the spokes. I then cut the strip on the cut lines exactly at the hub.
Step 8: Soldering the Temporary Battery Pack and Connecting It to the LED Strip
I will soon replace this battery pack with a protected pack in due time which is able to be recharged. After covering the contacts with gaffa tape and then prepared to connect the battery pack wires with the power socket (came with LED strip). After stripping the wire ends, soldering the leads together and protecting the bare connections with electrical tape followed by gaffa tape the pack was done. Well not really, because when we plugged it in the light didnt work. After testing the lights with the wall adapter power source and using a multimeter to test the polarity of the this socket, we realised we had wired the battery pack to the socket the wrong way. So we unsoldered and Hey Presto! the battery pack works!
I choose to place the battery pack opposite to the LED controller to try balance out the weights on the wheel and also because of the wire length (I also put these components close to the hub therefore). Even though I glued the controller down I trusted that th jamming action of the plastic shells would keep the battery pack in place.
Step 9: Finishing Off
The only thing left to do was to fit the other plastic shell in between the spokes and connected to the whole assembly (This plastic shell is bare whereas the other shell holds all the battery pack, controller, LED strip and air-hole parts). It was challenging to fit the other shell in between the spokes because of all the other components in the way. Basically I pushed and pulled one side of the ring into the spokes and turned the shell 360 degrees so that the whole shell was inside the wheel. I then he holes in this shell with the air-hole parts of the other shell. Even though the second shell didnt fit perfectly it worked pretty well and kept everything together.
And its done!
Overall, the wheel light turned out excellently as a design prototype. The combination of the LED strip with the 3D illumination design of the plastic shells made the light very bright from many angles, perfect for side visibility at intersections. This with the dynamic nature of the light controlled by the bike's speed make the light not only bright but eye-catching and warning. An effective design for a cycling work commuter's safety on urban roads.
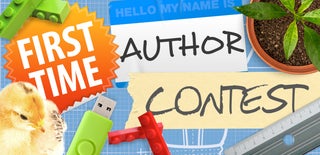
Participated in the
First Time Author Contest