Introduction: Bike Powered Phone Charger
This is a Bike Powered phone charger that is cheap, 3D printable, easy to make and install, and the phone charger is universal. It is a useful thing to have if you ride your bike a lot and need to charge you phone.
The charger was designed and built by five teens at Vector Space in Lynchburg, Virginia.
Supplies
- Generic Generator, $12.97
- LM2596 voltage regulator, $6.99
- 2 USB ports, $2.22
- 4 diodes, $0.56
- 4700UF Capacitor, $1.95
- 100 ft of Red Primary waire 22 GA 22 GA, $7.76
- M3 screw x 30mm socket head,(hardware store) $0.49
- 3D Printer Filament PLA (65g total for box, handlebar clamp, and phone holder), $1.30
- Rubber Bands
- Velcro
Total: $30
Step 1: 3D Printing
Phone Holder
I, sir James, through many trials and tribulations, designed a phone holder that will mount on most bike handlebars. It’s made in two parts. The first is the handlebar mount, and the second is the phone mount.
Handlebar Mount
The handlebar mount is attached to the handlebars and held on by a screw. You can use an insert nut on one side of the mount, and drive a screw from the other side. I designed the mount to use an M3x20mm screw. See the video in the assembly step.
Another key component of the handlebar mount is the size of the large hole. Our design has a 27mm hole, which gives it just enough space to be securely clamped to our handlebars. If your handlebars are a different size, you can access and modify our TinkerCAD design here.
The phone is held by two rubber bands that goes through the holes of the phone rest to keep the phone in place. You connect the phone rest to the handlebar mount by super gluing them together. This is a universal phone holder that means it works for all phones.
Electronics Enclosure
We also used TinkerCAD to design our electronics enclosure. You can access the design and modify it here.
The purpose of the box is to protect the circuit. The box is designed this way so it can be tied to the bike and to let the USB cords pass in and out. Our only consideration with material choice was whether it would be waterproof. We found that all of the major plastics meet this requirement, so we decided to use PLA because of its low cost and ease of printing. The electronics enclosure takes 41 grams to print, which costs approximately 82 cents.
We printed everything on a Lulzbot TAZ 6 using PLA at 0.25mm layer height and 20% infill. No supports necessary.
Step 2: Electronics
AC to DC Conversion
The generators produce AC voltage, which needs to be converted to DC in order to charge a phone. We used a full bridged rectifier to convert the power then a voltage regulator to bring it down to 5v so it wont fry the battery of your mobile device. We also put a 4700uF capacitor on it to make it charge more smoothly then it goes out to the output USB. We used 22 gauge copper wire to connect everything.
A full bridge rectifier is made from four diodes placed in a specific configuration. You can find details of how to build one here, keep in mind, you don’t need a breadboard, you can solder the diodes directly to one another. See how we did it in the picture show
the pin outs you wont to use are the farthest left and right pins to solder to the wires if the USB ports are stacked then you wont to use the ones in front if you are using the one closest to the pins
Voltage Regulation
In order to convert from voltages above 5 volts to exactly 5 volts, we used a LM2596 voltage regulator. The output voltage of this regulator can be adjusted by turning the small screw on the blue box. In order to set this screw properly, we connected a digital power supply to the input pins at 9 volts and we measured the output voltage with a multimeter. While doing this, turn the screw and watch the output voltage until you get as close as you can to 5 volts. If you go over five volts, your phone will be fried so it is important to get it as close as you can to 5 volts. Use a small flat head screwdriver to turn the screw. Next, you want to solder the red wire to the hole labeled in+ and the black wire labeled in-, then you want to do the same thing to the other side
Step 3: Assembly
The phone holder and handlebar mount are connected to each other using super glue. Insert a rubber band through each of the two holes in the phone holder.
Place the electronics into the box, plug the USB cables into the USB ports, then hot glue the electronics in place. Make sure to get the input and output correct with the labels on the box.
The generator we used came with a clamp piece to attach it to the bike. It was fairly simple there were two bolts for the clamp that goes on the bike. We attached it to the seat stay. Make sure it is under the wire for the shifter so it wont interfere with it. It is easiest to put the generator on the attachment piece before you put it on the bike.
Step 4: Installation
Electronics Enclosure
The box is attached with Velcro so you can put it where you want on the downtube. Put the Velcro strap in the tab slits and then make sure it is nice and tight on to the place you put it on.
Generator
To install the generator you have to screw the generator to the end of the bracket first then screw the bracket on to the seat stay of the rear end of the bike and screw the bracket to the generator. When you do this you need to make sure that the end part is pushing hard enough, but not too hard or that will effect the tire pressure. Before you start riding your bike you will need to make sure that the screws are on tight enough so the generator won't fall off. You will also need to keep the center axis of the generator pointing toward the center of the wheel.Then you will need to attach the wires to the bike generator and then attach the other end of the wires to the USB port at the end of box that says "Input". Then you put your own USB cable into the "Output" hole on the other side of the box and plug your own charger into your phone.
Phone Holder
Clip the handlebar mount on to your handlebars and secure it using an M3 screw. Then use the rubber bands to hold the 4 corners of your phone. It's sturdier than it looks!
Step 5: Appendix A: Research
By:Ellie Weeks
To give your phone a full charge, the battery needs 5 volts. So you only need to go about as fast as 4 mph. If you go slower, you will get no charge, if you go faster, the voltage regulator will maintain 5 volts.
Experimental Setup
Bike Speed versus Voltage
- We tested two different generators (Sanyo and unbranded)
- We used a power drill to spin the generator
- we used a tachometer to measure generator RPM
- In order to convert from generator RPM to bike velocity, we assumed a bike with 24 inch wheels
This is how we came to this conclusion from our experiment. If you are using a 12$ Sanyo generator. 1150 generator rpm = 73.3 bike tire rpm. 75 inch tire circumference x 73.3 = 5500 in/min= 5.2 mph. It is at this speed that the generator will start producing 5 volts. We know this based on the following data collected during our experiment.
- 950 rpm produces 3.5 volts
- 1150 rpm makes 4.24 volts
- 1900 rpm makes 6.7 volts
If you are going to use a 9$ generator which is smaller you will only need to go 3.2 mph to get 5 volts and to actually put a charge into your phone and going 5 mph will give you a little more than 6 volts.
1500 generator rpm = 47 bike tire rpm. 47 rpm x 72 (bike circumference)=3384 in/min= 3.2 mph
- 1300 rpm gives 3 volts
- 1500 rpm gives 5 volts
- 1700 rpm gives 7 volts
Charging Rate
We set up an experiment to measure how much electrical current is delivered to the phone when charging. Our results showed that the Sanyo generator produced 0.9 Amps and the unbranded generator produced 1.0 Amps.
We can use these numbers to calculate approximately how long it would take to charge a typical cell phone. Since many cell phones have a battery capacity of 3 Amp-hours, it would take the unbranded generator about 3 hours to charge from 0 to 100%.
Because of the lower price, lower bike speed required for charging, and because of the better charging rate, I would recommend the generic generator over the Sanyo generator.
Step 6: Appendix B: About the Project
This bike powered phone charger was invented by 5 teens (Ellie, Ian, Adam, Isaac, and James) from Lynchburg, Virginia at Vector Space, the local makerspace. The project was sponsored by the Nuts and Bolts Foundation.
We built this charger in five days for about 5 hours each day. On the first day we just did some 3D modeling and figuring out where the phone was going to be placed.
On day 2 we did some soldering and editing our 3D models and making them better, we did some math calculations as to how fast you need to go and wiring for converting A.C. (alternating currant) to D.C.(direct current).
On day 3 we did some 3D printing and editing and some of the first boxes didn't fit the dimensions then we fixed them and put our electric wiring and calculated how long you would need to bike to to go from 0% to 100%.
On day 4 we were making everything ready for use so we could have our first prototype, perfecting the dimensions,testing and documenting.
On day 5 adding finishing touches and documenting.
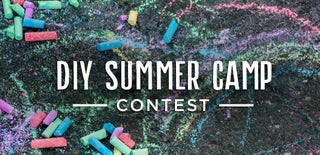
Participated in the
DIY Summer Camp Contest