Introduction: Blank Flight Shield
One tradition in a club that I am part of is for every group to paint flight shields every semester as a team bonding experience. Well after who knows how long we we ran out of blank flight shields, so for anyone who wants all of the info on how to do this here it is.
Although this Instructable is for wooden flight shields the techniques can be used for any simple 2D image you wish to cutout (letters, numbers, fraternity / sorority greek signes, ext.)
By the way,
"I made it at TechShop"
www.techshop.ws
Although this Instructable is for wooden flight shields the techniques can be used for any simple 2D image you wish to cutout (letters, numbers, fraternity / sorority greek signes, ext.)
By the way,
"I made it at TechShop"
www.techshop.ws
Step 1: CAD
Using CorelDRAW the original JPEG image needs to be converted into a vector file. Corel has a very useful
tool to do just that… Bitmap trace. Depending on the type of image and what you
want cutout you will need to play around to get the bitmap to convert into a
useful vector. After the bitmap has been
converted, delete everything except the lines you want to cut. Lastly save those lines as a dxf, or dwg.
Attachments
Step 2: CAM
Now that we have something to cutout, we need to convert it into GCode for the ShopBot to read.
Although I used Vetric’s Aspire, Vcarve Pro works equally as well.
1. Set material properties. I used 3/8 sanded (sanded has a much nicer finish than regular sheeting) plywood 4’x8’ sheets for my flight shields.
2. Import your vector file (dxf / dwg).
3. If you are making more than one, use the nest feature to have Aspire (or Vcarve) automatically fit as many objects as it can on the one sheet of wood. Note: I used a 3/16 end mill with .3” between objects and a 2” boarder.
4. Select all of your vectors you wish to cut and click on create profile tool path. Set the depth slightly thicker than your material (in case your Z depth on the machine is slightly off), for 3/8 plywood I used .4”. Select your cutter type, speeds & feeds. A great tool to do this is GWizard, no fancy math, no guess work, just plug in all of your numbers, and it pops out an accurate speed and feed. For my 3/8 2 flute HSS end mill, 18000 rpm, 150 ipm. Next add tabs, I personally like the 3D tabs, and used 3 per flight shield at .375 wide and .3 thick. Note: Put the tabs somewhere on a flat section or outside curve so you can easily sand it (inside corners suck to sand).
5. Lastly save your tool path to a USB drive as a .sbp (ShopBot Gcode).
1. Set material properties. I used 3/8 sanded (sanded has a much nicer finish than regular sheeting) plywood 4’x8’ sheets for my flight shields.
2. Import your vector file (dxf / dwg).
3. If you are making more than one, use the nest feature to have Aspire (or Vcarve) automatically fit as many objects as it can on the one sheet of wood. Note: I used a 3/16 end mill with .3” between objects and a 2” boarder.
4. Select all of your vectors you wish to cut and click on create profile tool path. Set the depth slightly thicker than your material (in case your Z depth on the machine is slightly off), for 3/8 plywood I used .4”. Select your cutter type, speeds & feeds. A great tool to do this is GWizard, no fancy math, no guess work, just plug in all of your numbers, and it pops out an accurate speed and feed. For my 3/8 2 flute HSS end mill, 18000 rpm, 150 ipm. Next add tabs, I personally like the 3D tabs, and used 3 per flight shield at .375 wide and .3 thick. Note: Put the tabs somewhere on a flat section or outside curve so you can easily sand it (inside corners suck to sand).
5. Lastly save your tool path to a USB drive as a .sbp (ShopBot Gcode).
Attachments
Step 3: Cut
1. Secure a sacrificial board to table. I like plastic nails,
but if you don’t have a nail gun, brass screws also work (brass so that if your
end mill hits it bad things won’t happen).
2. Secure your piece to the table, nice side down (the upwards cutting end mill tares up the side facing up). Once again using brass screws or plastic nails. One tip don’t just put screws at the corners of your work piece. If you are using a thin wood (like 3/8) the end mill will pull the wood up and off of the table. Instead use Aspire to find gaps / free space throughout your work that you can locate your screws at. Using those X & Y locations move the ShopBot to each coordinate and mark those locations. Then drill & screw at your marked locations. For my 4’x’8 board it took about 9 screws to fully secure the work piece. (X",Y")(54,21)(41, 34)(71.5,15)(25, 11)(73, 33)(7, 40) (91, 40)(90, 6)(7, 4)
3. Set home, for X&Y, I used the machine home. For Z, chuck up your end mill in the spindle and use ShopBot’s Z setting feature.
4. Subtract 1” from the Z axis, and do an “air pass” to double check everything. 5. Add 1” to the Z axis, and press go.
2. Secure your piece to the table, nice side down (the upwards cutting end mill tares up the side facing up). Once again using brass screws or plastic nails. One tip don’t just put screws at the corners of your work piece. If you are using a thin wood (like 3/8) the end mill will pull the wood up and off of the table. Instead use Aspire to find gaps / free space throughout your work that you can locate your screws at. Using those X & Y locations move the ShopBot to each coordinate and mark those locations. Then drill & screw at your marked locations. For my 4’x’8 board it took about 9 screws to fully secure the work piece. (X",Y")(54,21)(41, 34)(71.5,15)(25, 11)(73, 33)(7, 40) (91, 40)(90, 6)(7, 4)
3. Set home, for X&Y, I used the machine home. For Z, chuck up your end mill in the spindle and use ShopBot’s Z setting feature.
4. Subtract 1” from the Z axis, and do an “air pass” to double check everything. 5. Add 1” to the Z axis, and press go.
Attachments
Step 4: Finish
1. Using a deadblow hammer and a chisel, cutoff all of the tabs on your objects. Don’t just rip
them from the base wood, you may find that the base wood rips off portions of
your object.
2. Sand, sand, sand, sand your tabs off, sand your edges, Just sand everything smooth until your are happy.
3. Clean up. Seriously, spend 10 – 20 minutes and get everything vacuumed up. Don’t just leave everything better than you found it. But leave the tools how you would like them to be when you use them next.
2. Sand, sand, sand, sand your tabs off, sand your edges, Just sand everything smooth until your are happy.
3. Clean up. Seriously, spend 10 – 20 minutes and get everything vacuumed up. Don’t just leave everything better than you found it. But leave the tools how you would like them to be when you use them next.
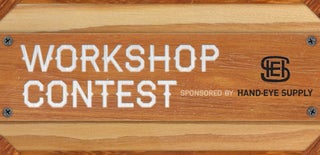
Participated in the
Workshop Contest