Introduction: Custom Boat Refrigerator and Chart Table Cabinet
First of all, this is my first instructable after many years of joyful and inspiring reading.
Our 28' sailing boat needed a fridge. When we bought the boat, the only place to store cold food was under a folding chart table, in a peltier cooled portable cooler (the type you bring for camping). This was strapped under the chart table, was not good looking, impractical and used quite a lot of juice.
The only viable alternatives were side opened fridges that aren't nearly as nice to look at and leak more heat through the doors. It also proved difficult to find one that suited and utilized the space available.
So last year it was time to replace this with a fridge that fits in the boat.
Parts needed:
- Teak plywood sheet 9mm thick for walls (USD 52 for 122*61 cm), 15mm thick for top table (USD 65 for 122*61 cm)
- Teak stick for flush 45 degree corners (USD 32 for 1m 30*30mm)
- Insulation plates (I used 50mm thick plastic covered polystyrene plates, USD 130 from Isotherm)
- Fridge complessor (USD 445 for an Isotherm 80)
Total USD 724
Step 1: Making Use of the Space
This is the space we had on offer. It is the only place the chart table and fridge could go. Everything onboard a small vessel needs to serve at least two purposes. The space is between the galley and the aft bunk, and there needs to be a small passage between the ladder up to the cockpit and the fridge for the person sleeping in that bunk. As you can see, there are not many square corners to use here.
The idea was to fit the aft wall of the fridge nicely toward the outer hull, with two 45 degree turns to make the passage, and fit the forward end just under an existing hand rail.
Step 2: Cut the Plates
This is what took most of the time. It is very cumbersome to use proper tools onboard a small sailing boat, so each plate had to be cut several times to fit where it should be. Once I was happy with the plate parts I had made, I glued them together.
I wanted the joints to be flush on the outside and not too clumpy on the inside (as that would create hot spots in the fridge). So the teak rods were planed to allow 1/2" landing of both plates and to be flush and rounded on the inside.
This took a lot of careful and creative clamping and gluing to achieve.
Step 3: Fit the Insulation and Finish
After the gluing came another trip on board to verify that it still fit the place.
Then came the insulation. These are plates of styrofoam with a plastic coating on both sides. I tried not to leave air pockets in the joints. After I was happy, I applied some sealing mastic and fitted the compressor.
After that came final sanding and several layers of varnish
The interior volume is about 50 liters.
The family was very pleased with the new cooler, as am I. I hope you enjoyed reading about it as well.
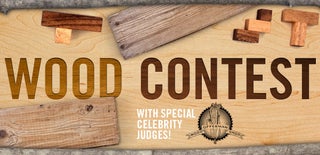
Participated in the
Wood Contest
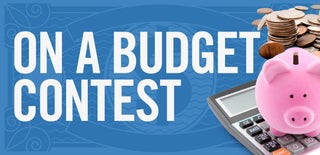
Participated in the
On a Budget Contest