Introduction: Reclaimed Bowling Lane Table
I recently moved into my first house and was in need of a dining room table. I saw a picture of a table that used an old section of bowling lane for its top and decided that I'd like to build something similar for myself. With about 30 hours of work over a few months I was able to turn a tattered piece of wood into a beautiful, sturdy table that should never need replacement.
To find the lane section I did a Craigslist search for bowling lanes and happened to find a guy about 50 miles away from me that was selling lane sections that he procured during a demolition job he was hired for. I paid about $300 for an 8 foot section with the arrow inlays. The section was about 2.5" thick and weighed about 250 pounds.
I've included a .dxf file of the wooden leg parts in this Instructable so that anyone can build one if they'd like.
To find the lane section I did a Craigslist search for bowling lanes and happened to find a guy about 50 miles away from me that was selling lane sections that he procured during a demolition job he was hired for. I paid about $300 for an 8 foot section with the arrow inlays. The section was about 2.5" thick and weighed about 250 pounds.
I've included a .dxf file of the wooden leg parts in this Instructable so that anyone can build one if they'd like.
Attachments
Step 1: Preparing the Lane
The first step in the process was to add support to the lane section to keep it from sagging. When the lanes are installed in the bowling alley they are built in place. The builders lay down long strips of maple and side nail them to the adjacent maple pieces. No glue is used in the entire process which means that once the lane is taken up from the floor it doesn't behave like a single slab of wood. All of the maple pieces are still tied together via the nails, but there is a certain amount of flex that the lane has. If not supported properly the lane will sag quite dramatically in the middle due to its weight. To add support to the lane I chose to inlay aluminum bars width-wise across the bottom of the table.
Using a hand router and a piece of metal to serve as a guide I routed out three pockets across the width of the table. I made the pockets 3/4" wide to accommodate the 5/8" aluminum square stock and made sure to make them a little deeper than necessary because I needed to sand the bottom down and didn't want the belt of the sander to touch the metal pieces.
With the pockets routed, I set out drilling out the aluminum bar stock. I spaced the holes so that each was on center with piece of maple. The goal was to tie all of the pieces of maple together using the bar so that the table won't sag in the future. When this was done I ran screws through each hole and into the bottom of the table.
This resulted in a sturdy top that shouldn't sag.
Using a hand router and a piece of metal to serve as a guide I routed out three pockets across the width of the table. I made the pockets 3/4" wide to accommodate the 5/8" aluminum square stock and made sure to make them a little deeper than necessary because I needed to sand the bottom down and didn't want the belt of the sander to touch the metal pieces.
With the pockets routed, I set out drilling out the aluminum bar stock. I spaced the holes so that each was on center with piece of maple. The goal was to tie all of the pieces of maple together using the bar so that the table won't sag in the future. When this was done I ran screws through each hole and into the bottom of the table.
This resulted in a sturdy top that shouldn't sag.
Step 2: Sanding and Finishing the Lane
When I picked up the lane section from the seller it was in pretty good shape, however the top was dirty and covered in decades of bowling alley oil, dirt, etc... I really wanted to sand a layer of the top to help clean it and to sand a layer off the bottom to create a nice flat surface to mount legs to. I struggled with the trying to decide the best way to sand the lane down and finally came across a local wood working shop that had a wide enough Timesaver belt sander. I brought the lane in on my day off and paid $60 to have them sand about 1/8" off of the top and bottom surfaces. Because the aluminum inlays on the bottom side were recessed we were able to totally flatten that side out. If I hadn't recessed them the shop said that they wouldn't have been able to sand that side. I felt that this was a great deal because not only did the sanding come out perfect, but it saved me countless hours trying to recreate that process at home. I still had a little bit of hand sanding to do on the edges, but that was relatively easy compared to the top and bottom. I worked up to a 220 grit sandpaper and called it good.
The lane was then ready for a few coats of polyurethane to seal it up. I used an oil-based polyurethane with a satin finish made by Minwax for the finish because I wanted to keep the natural color of the wood. I applied first to the bottom and sided of the lane, then flipped it and did the top half. I applied about 6 coats in all, sanding with 220 grit sandpaper between each coat. The finish went on beautifully and I was really happy with the results.
The lane was then ready for a few coats of polyurethane to seal it up. I used an oil-based polyurethane with a satin finish made by Minwax for the finish because I wanted to keep the natural color of the wood. I applied first to the bottom and sided of the lane, then flipped it and did the top half. I applied about 6 coats in all, sanding with 220 grit sandpaper between each coat. The finish went on beautifully and I was really happy with the results.
Step 3: Making the Legs
Because I don't really have a wood shop at home, I decided to have the legs CNC routed from 18mm thick Baltic Birch plywood. This way all I had to do was glue the various sections together to make thicker sections, sand and apply a finish, not to mention there are some neat tricks you can do with this type of manufacturing process such as using slots as passages for bolts, creating pockets to keep weight down and the overall accuracy makes it possible to things that would be more difficult using traditional woodworking methods.
I designed the legs using Solidworks and sent the files to a local CNC routing shop called RoboCut CNC. A few days later I had the parts in hand and was ready to start gluing them together. I was amazed at how well the Baltic Birch cut. There wasn't any chipout on the edges and everything fit together perfectly.
To glue the parts together I spread Titebond II wood glue faces to be glued and pressed them together using about 8 C-clamps per part. Because alignment was critical I included holes and pockets in all of the sections to accept 2 dowel pins. The dowels serve to align the sections together. This is important for looks but also because I had several through holes that would need to accept hardware and if those were misaligned the hardware wouldn't fit correctly and this could create an unsightly gap between the hardware and the wood. The gluing went well, but there are some things I'd do differently next time. When pressure from the clamps is applied some excess glue will squish out at the edges. My instinct was to wipe the glue off with a wet paper towel. Although this cleaned the bulk of the glue off, it also pressed a thin layer of glue into the pores on the edge of the wood. This created an ugly yellow glue smear that needed a lot of sanding time to remove. Next time I would just let the glue be until it was dry and then remove it with a sharp chisel. This would have saved me lots of sanding time. Oh well.
With the legs glued together it was time to apply a finish to them. By this time it is really cold where I live, so applying finish in my unheated garage wasn't an option. Because of this I needed to do the work in my basement which meant that odor from the finish was a major concern. To cut down on the amount of VOCs in the air I opted for a water based polyurethane finish made by Minwax. The odor was almost non existent and I was happy with the results.
I designed the legs using Solidworks and sent the files to a local CNC routing shop called RoboCut CNC. A few days later I had the parts in hand and was ready to start gluing them together. I was amazed at how well the Baltic Birch cut. There wasn't any chipout on the edges and everything fit together perfectly.
To glue the parts together I spread Titebond II wood glue faces to be glued and pressed them together using about 8 C-clamps per part. Because alignment was critical I included holes and pockets in all of the sections to accept 2 dowel pins. The dowels serve to align the sections together. This is important for looks but also because I had several through holes that would need to accept hardware and if those were misaligned the hardware wouldn't fit correctly and this could create an unsightly gap between the hardware and the wood. The gluing went well, but there are some things I'd do differently next time. When pressure from the clamps is applied some excess glue will squish out at the edges. My instinct was to wipe the glue off with a wet paper towel. Although this cleaned the bulk of the glue off, it also pressed a thin layer of glue into the pores on the edge of the wood. This created an ugly yellow glue smear that needed a lot of sanding time to remove. Next time I would just let the glue be until it was dry and then remove it with a sharp chisel. This would have saved me lots of sanding time. Oh well.
With the legs glued together it was time to apply a finish to them. By this time it is really cold where I live, so applying finish in my unheated garage wasn't an option. Because of this I needed to do the work in my basement which meant that odor from the finish was a major concern. To cut down on the amount of VOCs in the air I opted for a water based polyurethane finish made by Minwax. The odor was almost non existent and I was happy with the results.
Step 4: Machining the Hardware
The table legs are built in several sections which are then bolted together to form 'trestle style' legs. To attach the sections together I used cross dowels that I custom machined. They are made from 1.25" diameter aluminum round stock and there are 20 of them in total. These were a simple part that involved facing each piece to the right length (about 4.4"), putting a small chamfer on the edges using a file, and slightly turning down the diameter to fit in the hole properly then drilling a tapping a 3/8-16 hole through the middle.
I had designed the holes in the wooden pieces to be slightly oversized by about 0.005", however I learned that the tolerance on the aluminum stock was slightly larger than expected so the aluminum stock would not fit in the holes as is. The benefit of this ended up being that I could get the fit of the hardware just right and also that turning down the diameter left a nicer finish on the part.
Also, because of the gluing step for the wood there was a little bit of glue residue left on the inside of the holes that the cross dowels needed to slide into. I hadn't counted on that and needed to get the glue out of there. To do this I turned a tool on the lathe that was simply a long round piece of aluminum that had a diameter just slightly less than the diameter of the hole in the wood. I centered this in the hole and with a few blows of the hammer the tool was forced through the holed and sheared off any glue that was in there. The cross dowels where then machined slightly smaller in diameter than the tool and when slipped into place everything fit perfectly.
I had designed the holes in the wooden pieces to be slightly oversized by about 0.005", however I learned that the tolerance on the aluminum stock was slightly larger than expected so the aluminum stock would not fit in the holes as is. The benefit of this ended up being that I could get the fit of the hardware just right and also that turning down the diameter left a nicer finish on the part.
Also, because of the gluing step for the wood there was a little bit of glue residue left on the inside of the holes that the cross dowels needed to slide into. I hadn't counted on that and needed to get the glue out of there. To do this I turned a tool on the lathe that was simply a long round piece of aluminum that had a diameter just slightly less than the diameter of the hole in the wood. I centered this in the hole and with a few blows of the hammer the tool was forced through the holed and sheared off any glue that was in there. The cross dowels where then machined slightly smaller in diameter than the tool and when slipped into place everything fit perfectly.
Step 5: Assembly
This was the fun and easy part. Using the cross dowels and 3/8-16 x 5" bolts (available at Home Depot) and some washers I attached each section together until the table legs were standing. I also added some felt pads to the bottom of the table. It was pretty easy to do this by first assembly the legs and leg cross bars, then adding the two long spanner pieces last. I had the table top resting on sawhorses that were slightly taller than the leg assembly. I slid the sawhorses to the extreme ends of the table top and was able to just slide the leg assembly underneath, then removed the sawhorses one by one and now the top was resting on the legs. Using some long screws I was able to attach the top to the legs in a semi permanent way so that everything will break down easily for moving someday.
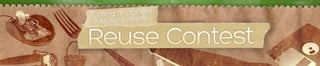
Grand Prize in the
Reuse Contest
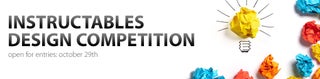
Participated in the
Instructables Design Competition