Introduction: Brass Pen
I've wanted to make my own everyday-use pen for a while now, and finally decided to do it when I came upon a stash of brass rods in the shop.
The ink cartridges I'm using were cannibalized from my favorite pens, Uni-ball's 0.38mm Signo pens. I adore these, so I opted to build the pen around these cartridges instead of using a more standard sizing.
Materials
- 3/8" brass rod (two 3.5" long pieces)
- pen cartridge of your choice
Tools
- Lathe
- Knurling tool (optional)
- Drill bits, 5/16" taps and dies
- Calipers
- Hacksaw (optional)
Step 1: Reverse-Designing a Pen
If you're making a pen to fit a standard cartridge, the barrel and taper dimensions are available on the internet.
Since I was designing mine around a specific cartridge, I took measurements on the workbench instead. (And ended up making a test pen)
The biggest limitation in my design was the length of my drill bits. I chose to make a two-part pen that screwed together, with the mating line hidden right behind a knurled grip. Knurls in this pen serve several functions: grip surface, aesthetics, and hiding any differences in diameter between my front and back halves.
But 99% aesthetics. I love knurls.
Step 2: Shaping the Front Half
After selecting a comfortable-sized brass rod and cutting it to rough front and back halves, I stuck the front half in the lathe and faced it flat. I then set a taper angle (originally a 20 degree taper but I later decided 10 degrees looked nicer.)
After making the rough passes, I rotated the turning tool nearly parallel to the part to make a finish pass. Then I made knurls!
Step 3: Drilling Out the Barrel
Once the outside is complete, turn the part around to drill through the back.
I first started with a 1/4" drill bit to accept the tap, then used successively smaller bits to fit the contours of the ink cartridge. I allowed roughly 200-micron clearance, which worked fine. Your mileage may vary depending on the metal you use.
After tapping the threads on the lathe, I removed the part and hacksawed off the section of brass that was clamped in the jaws.
Step 4: Machining the Back Half
The procedure for the back half starts off the same way; then I turned down a smaller cylinder and cut threads with a die. You definitely want to form the threads before drilling holes, otherwise you will be either working with fragile threads or run the risk of squashing/bending your part!
There ended up being a 0.07" difference in diameter between my part, but the raised contours of the grip ensure that only I would notice.
Step 5: Finished!
Everything should screw together nicely, and can be easily disassembled when you need to refill!
I ended up needing a longer back-piece than I had originally anticipated, so part of my clamping-scrap ended up in the final pen. I hid the toolmarks with more knurls and some artistic tapers.
I really like the weight of this pen, as well as the shininess and the knurls. It is comfortable to hold and use for extended periods of time, and has already served as a conversation starter.
After two weeks of near continuous use and indiscriminately dropping it in every bag and pocket, I definitely want to make a cap for this soon.
I hope this has provided you with ideas for your own projects.
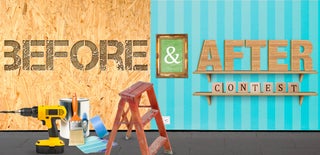
Participated in the
Before and After Contest

Participated in the
Metal Contest