Introduction: Bubble Breezer Deadpool
In this instructable I am going to show you how to modify a BUB-L Breezer toy to look like Deadpool. Admittedly this is a pretty stupid idea, but it made me laugh, I decided to share it. Maybe others have the same immature humour to appreciate this.
As you can see here, the original toy has pretty bad ratings and when I got mine more often than not it wouldn't work. So I decided to improve it to get it to work more consistently. If yours is better from the start you can of course skip these steps.
Step 1: Things You Need
- BUB-L Breezer (e.g.here)
- Bubble solution (or glycerole, distilled water and soap)
- Modelling clay (I used some left over QuikSteel I had, which is a bit of an overkill in terms of stability and cost, but otherwise it is perfect for the application. You won't need any glue to hold the head in place, it sets really quickly and is very easy to sand. Since I ran out of QuikSteel I also used some Milliput)
- Paint (red, black, white and skin tone), I also used a red wash; paint brushes
- Filler primer spray paint or sandable primer (e.g. this one)
- Sanding paper
- Utility knife
- 3D printer (you won't need one if your BUB-L Breezer is working fine and you are able to build the head by hand)
- Soldering iron (you don't have to solder anything, but the quality off the wires is very bad and they might tear off, so it is better to replace them)
Optional (to improve the mechanism)
Step 2: Changing the Head
The most important part to make the figure look like Deadpool is to change the head.
I used this model from Thingiverse by nika9282 and simply cut the body off. I printed mine in three different sizes, to see which one I liked best. The file I uploaded is the size I used, but you can of course scale it differently. In my opinion the original head look a bit small, but feel free to use which ever size you want. The model has a slightly low polygon count, but I figured since I would have to sand it anyway it wouldn't matter. You can of course use a 3D program to smooth it before printing, e.g. Meshmixer.
Pulling the original head off turned out to be more difficult than I imagined. So I simply cut it off.
I used QuikSteel to add the head to the body. Cover the hole from behind with some tape, and add a layer of QuikSteel. Then press the head into it and smooth the transitions. Once it was set I used some Milliput for further improvements. As you can see in the pictures I also modeled the gloves. Make sure that you are still able to open the figure.
Attachments
Step 3: Modeling the Skin Cancer
Before Deadpool became a test subject in the U.S./Canadian superhuman enhancement project, he was terminally ill with cancer. Due to this his skin is permanently damaged. If you are further interested in his back story, please check out this link.
In the comics there are many different images of how the cancer supposedly looks like. So you can get creative, for inspiration simply google "Deadpool skin cancer".
I suggest removing all the mechanics and electronics before painting. I actually got rid the sound module, because I found it really annoying and filled the small holes in the front.
I covered his butt in a thin layer of modeling clay and used a nail to remove the clay from some of the parts. After the clay had hardened I primed the whole body with two rather thick layers of grey filler primer, sanded it and covered it in two thin layers of red primer. Then I used some masking tape and spray painted the skin.
Step 4: Painting
Deadpool's suit was designed by his friend Weasel, a weapons designer and arms dealer who designed most of Deadpool's equipment. It has a large a number of pockets that contain multiple types of weapons. It also has two holsters on his back to house his katanas.
As you can see in the pictures, I decided to go with a minimal amount of details. You can of course add as many elements to the suit as you like.
For the skin cancer I used a red wash and a bit of black, as you can see in the second picture. Don't forget to paint the arm.
If your BUB-L Breezer is working well, all you need to do is reassemble it and you are done. Sadly mine wasn't and reading the amazon.com comments I certainly wasn't alone.
Step 5: Improvement - Reducing the Noise
There are three things I decided to improve:
- The mechanism was way too loud
- The airflow seemed to be too weak
- The arm didn't move consistently
I decided to start by reducing the noise. When I opened the gear box, I was quite surprised. There was silicone grease everywhere. Actually, blobs of it. All the noise came from the first two gears. So I decided to replace the first one (sadly I didn't have a replacement for the second one). It reduced the noise quite a lot. As you can see in the second picture I also added some padding, but it didn't change much. The mechanism is still quite loud; I am probably going to try to replace the second gear as well. If you find it somewhere help would be appreciated.
Removing some of the silicone grease helped with the strength of the mechanism, since it reduced the resistance it had to deal with.
Step 6: Improvement - Air Flow
In order to improve the air flow I decided to design an adapter. Once it is printed simply press it on.
I've uploaded it under the following link. Simply change the parts to fit your printers tolerances.
I used an Ultimaker 2+ extended with a 0.4 mm nozzle and a 0.1 mm layer height.
If you are interested in 3D design I highly suggest getting Fusion 360, there is an option for hobbyist to get it for free and I am really impressed how good it is. If you are new to 3D design check out the 3D printing class.
Attachments
Step 7: Improvement - Arm Movement
Improving the arm mechanism turned out to be more difficult than I expected. As you can see in the first picture, the parts I printed in PLA kept on breaking. I than decided to use Carbonfil filament. I was quite impressed how light and strong it is. Sadly it turned out to be even more brittle than PLA. Since I was having trouble printing with Nylon I chose to go with PETG e.g. form FormFutura. Which finally worked really well.
As you can see in the pictures I remade most of the mechanism in Fusion 360. The turner disc on the bottom was slightly bent and therefore the whole original mechanism was wobbly. The further you move the pin to the inside or outside of the disc the further down or up the arm moves. It also decreases or increases the speed of the arm movement.
You can download and play with it here:
http://a360.co/2oqHXHC
An even easier and better way to correct the arm movement is to change the angle between the two pins on the slider. Before deciding to optimize the mechanism I tried to slightly twist the bubble stick and ended up breaking it. I had to fix it with some modeling clay, I hope you can learn from my mistake and simply edit the slider:
http://a360.co/2nOOcnB
When you reassemble the mechanism don't forget to add some silicone grease.
As you can see in the pictures I left the third piece of the mechanism as it was, because it's been working fine.
Step 8: Improvement - Arm Movement Part 2
To reduce the friction, I decided to add a ball bearing. Before the mechanism wasn't always strong enough to lift the arm fast enough and more than half of the time the bubbles would fly against the barrel and burst immediately.
As you can see in the first picture, I designed a part called "AlignmentDisc.stl" in order to make gluing the gear holder in place easier.
Here you can find the arm connector and edit it, should it be necessary:
http://a360.co/2nxEmUt
Simply place the gear over it and screw it in place (with two 2.2x2.9 mm screws). Turn the whole thing on and stop when the arm has reached the position shown in the third picture. Then slide everything in place.
Congratulations you are done!
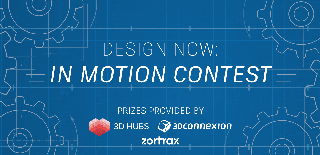
Runner Up in the
Design Now: In Motion Contest
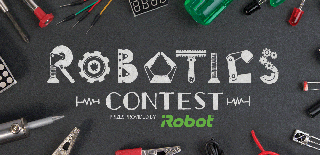
Participated in the
Robotics Contest 2017