Introduction: Build Extendable LED Lights to Make a Great Storage System
If you have a hobby, you have stuff, probably a lot of stuff. We are all trying to come up with that perfect system for storing and organizing our stuff. For me, it's electronics components like LEDs, wires, sensors, motors . . . . .
I found something that works well for my stuff in my space, it's from IKEA and they call it Trofast. It's in the kids toy storage section. It consists of a wooden frame with slots to slide in plastic bins/tubs of various sizes. The frame and bins are modular so you can mix and match to get to a solution that works for you and your stuff.
I often work on my little projects at night and my room lighting is not the best. Most of my bins are black and some are deep, it can be hard to find what you are looking for even if you remember which bin it's in. We need some LEDs! Because this stack of bins is 5 high it would be great if the lights would extend out so they could illuminate farther down to the lower tubs. What we need is a little LED IKEA hack.
Here is a link to the Trofast at Ikea
There are several models of Trofast, this hack will work with most of them but NOT the ones listed as "wall storage". I have some of those on my table and they don't have the wide board at the top of the units that we need for mounting the brackets. You would have to hack the hack to make it work.
I have used this everyday for around 6 months, I can honestly say it may be the most useful thing I have ever built.
Step 1: What You Will Need
We will assume we are adding our LEDs to a Trofast (article number: 990.063.81).
Materials
(4) 1 X 17cm 12V LED strips like these (ebay link)
12 volt 2 amp power supply (the connector does not matter we just need + and - wires) ebay link
4ft of 1/2 x 3/4 inch angle aluminum (4 one foot sections) Lowes link
(8) 1/4 x 3inch carriage bolts
(8) 1/4 inch nylon lock nuts
12ft of single pair wire (4 sections of various lengths)
On/off switch like these (ebay link)
Epoxy
Paint
Electrical tape and/or heat shrink tube
Optional: small block of wood for the switch, a few inches of tubing for wire management
TOOLS
Measuring tape
Drill + 1/4 and 1/8 inch drill bits
Hack saw
File
Hot glue gun
Optional: a vice is helpful
A few words on the LEDs. There are a lot of LED options that will work. Make sure your power supply can easily drive whichever ones you decide to use. They all don't draw the same number of amps. Find the number of amps each LED strip draws and multiply it by the number of LED strips you plan on using then add a little extra and that is how many amps your 12V power supply needs to be able to handle. Heat could also be a problem. I was planning to use the aluminum brackets as heat sinks. It turns out that it wasn't needed. The LEDs I used were meant for cars so even though they were listed as 12V, cars usually run between 13V - 14V. Since I only use 12V they are not pushed hard and barely get warm. Make sure yours don't to hot with your power supply The seller claims they are also waterproof for what it's worth.
Step 2: Cut the Brackets
Let's make 4 lights. The width of each section is very slightly over 12 inches. I cut each brackets 12 inches long
- Use your tape measure and hack saw to measure and cut (4) 12 inch lengths of aluminum angle
- The cuts may be a little rough and the corners sharp - use your file to slightly round the corners and smooth out the cuts of each piece.
- Each bracket is going to have 3 holes, 2 for the bolts and 1 for the wires. The brackets are not symmetrical. One side is 1/2 inch wide the other is 3/4 inch side. We will be mounting the LED on the 3/4 inch side and bolting the bracket to the Torfast on the 1/2 inch side. It would be a good idea to take one of your pieces over and hold it up against the cabinet to get a good idea of which way it will go.
- Measure 1 inch in from each end and draw a vertical line on the 1/2 inch side
- to find the middle of that line, measure 1/4 inch up from the line you just drew and draw a horizontal line through it. Do the same at the other end. These mark where our bolt holes will go.
- The wire hole is going to be in between the two bolt holes close to the right bolt hole.
- Measure in 1 3/4 inches from the right side and draw your vertical line
- Measure up that line 1/4 inches from the edge and draw a horizontal line. This is where the hole for the wires goes.
- Before you drill your holes check your bracket against the cabinet again. The bracket fits under the "lip" of the top shelf. The 1/2 inch side where you marked your hole locations should be flat against the cabinet with the 3/4 inch side pointing away from the cabinet towards you. The LED will go on the underside of the 3/4 inch section so it shines down.
Step 3: Drill the Holes
All of the brackets will be the same so we will get one right then use it to make the others.
We are using 1/4 inch x 3 inch carriage bolts so we will need a 1/4 inch drill bit to make the bolt holes (the outside 2 holes)
To help drill in the right spot use a center punch to start the hole
After you drill your holes drop your bolts in and make sure the heads properly seat flush against the aluminum
Now drill the wire hole, it will be smaller than the bolt holes, for my LED wires a 1/8 drill bit worked fine
If the holes are rough, especially your wire hole, use a file to smooth them out
Take your prototype bracket to your shelves and do a dry fit.
- Position the bracket under the top shelf lip
- mark where the holes need to be drilled into the wood using your bracket
- Drill your holes (do this on the most inconspicuous shelf in case something goes wrong). You want your bolt holes a little bit bigger than the 1/4 inch holes you drilled into your bracket. Don't make the holes too big, we will be adjusting them later
If all went according to plan you now have a successful prototype, use it to make your other 3 brackets
Step 4: Attach and Paint
Use your brackets to make the rest of the holes in the other shelves.
Important: keep track of which brackets go with which shelves. There are slight differences that can bind the sliding action if they aren't matched up properly. Numbered them to keep track
Attaching the bolts to the brackets:
We are using carriage bolts because they are only threaded on the end, they will slide smoothly through the holes. If you use regular bolts your life would be much simpler, you could secure the bolt to the bracket using a regular nut, then you could use a 2nd nut at the end to keep the bolt from pulling out of the shelf. Of course the bolts wouldn't slide as smoothly and you would digging into the wood with the threads each time you pulled it out and pushed it in. - Your call (maybe some kind of plastic grommet?)
For the carriage bolt solution:
- Mix up some 2 part epoxy that is good for bonding metal to metal. I used JB Weld but had to go back and fix several bolts then I used Bob Smith Epoxy which seemed to work better. Its a good idea to rough up the aluminum with sandpaper around the bolt holes first to help the epoxy adhere. I missed that one, you can do better.
- Make sure the bolt heads sit flat against the bracket which will make them hang down perpendicular to the bracket
- Apply epoxy to both the bracket and the bottom of of the bolt head
- After the initial epoxy set up I added a little more to the back of the bracket holes for good measure - not too much or the bracket won't sit flush with the shelf
- Give the epoxy plenty of time to dry
Paint
The silver brackets look good in their own right. In fact you may prefer the contrasting look for your shelves and leave them au naturel. If you want to have the lights completely blend in with the black Trofast units. Use matte black paint. It's a good idea to prime them first but I must admit I didn't. You will need several coats of paint.
Random tip: I have these aluminum stakes, they are dirt cheap, easily bent but pretty strong. They are intended for use in the garden holding down tomato cages and the like but I use them for a million other things in my projects like hanging my brackets so I can paint them
I didn't want the smooth part of the carriage bolt to get painted for 2 reasons. I thought it looked better unpainted and paint would get chipped off with use. You can paint the backs of the brackets before you attached the bolts (as I did) or just tape off the bolts before painting. If they do get painted you can fix it with a little paint thinner.
These LEDs had a black aluminum housing but the double sided tape used to mount them is white and really noticeable even from the side. I taped off the LED and spray painted the sides but a black Sharpie helped finish the job
Mount the lights on the bracket
As mentioned before these lights didn't even get warm when driven by my power supply so using the double stick tape that came on the lights worked fine. If yours did get hot you could remove the LED housing and attached the strips directly to the aluminum with thermal glue.
Center the light - in this case if I measured in 2 1/2 inches in on one side, it would leave 2 1/2 inches on the other side so the LED was centered
Before you peel off the paper and stick it down make sure the wire is on the side where the wire hole is drilled
Feed the wire through the hole
Step 5: Power and a Switch
For power I used a decent 12V 2A wall wart power supply from an obsolete battery charger for this project.
Clip off the connector to give you access to the red (+) and black (-) wires
You can use wire nuts to connect everything together
A quick test found each LED draws just under .4 amps at 12V. I plugged in all 4 lights and let them run for a while and nothing got too warm.
Now we need a switch. I went with this simple 12V toggle switch with a little LED that is lit when the switch is on. It's actually quite useful to have that LED when you are looking for the switch at night to turn it off.
Check out the goofy image of how to hook up simple rocker switch, power supply and the 4 LEDs
At this point, it's a good idea to temporarily connect everything together including your switch to make sure it all works together. Once we feel good about that we can start mounting everything more permanently
You could connect the wires and hot glue a switch to the back of the shelves and be done. Just for fun, I made a block to hold the switch and help hide the wires. I made the switch mount with a scrap of 2x2 wood (which is actually more like 1.5 x 1.5).
- Cut the wood to your desired height, I used 2 inches
- Find the center by drawing diagonal lines from corner to corner, where the intersect is the center
- Do the same thing on the bottom of the block
- Drill a hole through the center of your piece large enough to hold your switch
- when you buy a switch the info usually tells you what size hole or shaft you need to mount the switch
- this switch needs a 20mm hole which is 25/32"
- I used a 3/4 paddle or spade bit in my cordless drill
- you need to lock your piece of wood in a vice for this - DON'T try to hold the drill in one hand and the wood in the other - bad idea
- go half way in from the top then turn the piece over and finish the hole from the other side, it doesn't matter if they don't meet up perfectly
- decide which end looks best, that is your top, figure out which side looks best, that is your front
- We will cut a small notch (about 1/4 inch x 1/4 inch) out of the bottom-back piece of the wood for the wires to go in and out of the mount
- Sand where needed
- Paint your masterpiece
- You can use spade terminal connectors to make the wire connections to the switch. Soldering would be a good choice if you don't use connectors. Feed the wires in through the notch and up and out the top, connect them to your switch.
- Mount your switch into your homemade housing, it may be snug enough that you don't need any glue, if not, use your glue of choice
Step 6: Mount Up
The last steps are to get the brackets sliding in and out as you like and cleaning up the wiring.
After epoxing the bolts to the brackets, the bolts and the holes in your shelves may not line up and slide perfectly, that's OK, we are going to fix that. DON'T force the bolts to slide in the holes. You have each bracket numbered right? That will give us a good start.
As usual, start with your least visible shelf and gently start to slide your bracket/bolts into the holes. Be Careful, it's very easy to break the bond between bolt head and bracket when doing this (the epoxy is plenty strong for everyday use after the bolts/holes are fitted properly). If you do happen to break the bolt away from the bracket, all is not lost, it's just back to the epoxy.
When you feel the fit getting a little tight pull out the bracket, take your drill and ream out the hole(s) a little - repeat It took me about 3 times per bracket to get it it so the lights would slide smoothly but not too loose.
You can dictate how far your lights slide out by adjusting the nut on the end. I used 3 inch carriage bolts but you could go longer or shorter.
When finished use a black Sharpie to color any exposed rough edges of the hole
Wire management
It's easier to connect everything on one end (the switch or the lights) then mount the wires as you work your way back to the other end. I started at the switch. Keeping the wires out of the way makes sure they don't get tangled with whatever you are storing in your bins
How much wire you need depends on where you mount your switch and how you route the wires in the back. Start long and cut off what you don't need.
It's a good idea to solder your connections and cover them with heat shrink tube
You will want to drill a small hole in the back of each self for the wires
You can use whatever wire you want, I used wires I liberated from some old bulk ethernet cable, one of the nice things about this wire, other than it was free, is that it is stiff and will hold it's position especially in conjunction with a little hot glue
Cut little pieces of plastic tubing and hot glued it to the top underside of the shelf. It allowed the wire move while working on it and you need some flexibility for your brackets to slide in and out. Straws would probably work just as well
Hot glue the wires running across the back of the selves on their way to the switch to keep them out of sight.
Step 7: Bask in the Glow of Your Stuff
Flip the switch, extend your LEDs and see all the way to the bottom of you lowest tub. Your stuff will have a much harder time hiding from you now. When the LEDs are off and pushed back, no one notices the brackets, they blend right in. Turn on the lights and your people are impressed, 100% of them want to slide the brackets in and out.
I hope you found this useful, if you did, please consider voting for this project, I have entered it in the "Lamps and Lighting Contest". There is a Vote button in the top right corner of the page.
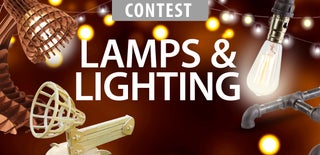
Participated in the
Lamps and Lighting Contest 2016