Introduction: DIY 3D-Printed Soldering Fume Extractor
If you are an electronics hobbyist, soldering is essential in almost all of your project, but the smoke/fumes from burnt solder and flux isn’t something you want to breathe. It smells bad and can be very dangerous to your health but you can reduce the hazards by employing a fume extractor. Even if you only solder things once in a while, it's a good idea to have a solder fume extractor to suck in those toxic fumes.
If you want to buy a good fume extractor from the market, you have to pay more than $70. So I have made my own by using a 120mm PC cooling fan and 3D printed enclosure.
Credit:
I found online an amazing 3D printed model that I tweaked and customized in Autodesk Fusion360 according to my needs (source: "Minimalist 3D Printed Fume Extractor" by rdmmkr used under CC BY-NC-SA 4.0 / Modifications: size, 120mm fan, speed control ).
I have used a 120 x 25 mm fan whereas the original design is suitable for an 80 x 38 mm fan.
My Book : DIY Off-Grid Solar Power for Everyone
You can order my Book on Off-Grid Solar Power from Amazon
Support me On Patreon:
If you enjoy my work here on Instructables, consider joining my Patreon, it will be a great help for me to make more interesting projects in the future.
Patreon Link: https://www.patreon.com/opengreenenergy
Supplies
Components Used:
1. 12V Fan ( Amazon )
2. Speed Controller ( Amazon / Aliexpress )
3. DC Jack ( Amazon / Aliexpress )
4. Rocker Switch 15 x 10 mm ( Amazon / Aliexpress )
5. 5mm LED ( Amazon / Aliexpress )
6. Resistor - 580Ohm ( Amazon / Aliexpress )
7. 22 AWG Wires ( Amazon / Aliexpress )
8. Heatshrink Tube ( Amazon / Aliexpress )
9. Threaded Heat Insert ( Amazon / Aliexpress)
10. Activated Carbon Filter ( Amazon / Aliexpress )
11. Double-sided Tape ( Amazon / Aliexpress )
12. M3 x 12 Screws ( Amazon / Aliexpress )
13. M5 x 8 Screws ( Amazon / Aliexpress )
14. Rubber Feets ( Amazon / Aliexpress )
Tools Used:
1. Soldering Iron ( Amazon / Aliexpress )
2. 3D Printer ( Amazon / Aliexpress )
3. Wire Cutter ( Amazon / Aliexpress )
4. Wire Stripper ( Amazon / Aliexpress )
5. Hot Air Blower ( Amazon / Aliexpress )
Step 1: How It Works ?
The main component of this fume extractor is based on a 120 x 120 x 25 mm cooling fan. The fan sucks in the fumes from the soldering area and passes them through a layer of the activated carbon filter and cleans the odors from the air, effectively absorbs toxic gases, and provides a safe working condition.
The above image from the DIYODE article is really a nice pictorial representation of the working of the fume extractor. Thank You DIYODE for designing this picture.
Schematic Diagram:
The fan is power by a 12V DC adapter. The input power is fed into the circuit through a DC jack.
The speed controller is used to regulate the fan speed.
The 5mm LED with a current limiting resistor ( 580 Ohm ) is used to indicate the power status.
The rocker switch is connected between the DC jack and speed controller to isolate the power from the entire circuit.
Step 2: Prepare Fan Wire
I have used an Arctic F12 casing fan for this project. The fan comes with 3 wires with a connector. The wires are designated as GND, 12V, and Signal. For this project, we need only the two power wires i.e 12V and GND.
Cut the connector by using a nipper then discard the signal wire.
Strip out the insulation from the wires for connecting them to the speed controller.
Step 3: Prepare the LED
Here I have used a 5mm Red LED to indicate the availability of power. The forward voltage of a red LED is typically 1.5V to 2V, but we have to run it from 12V. This can be done by using a current limiting series resistor. The value of the resistor can be easily calculated by using this online calculator.
Trim the legs of the LED by using a nipper, the longer leg represents the positive terminal.
Solder one leg of the resistor to the positive terminal of the LED.
Solder a piece of red wire to the other leg of the resistor and black wire to the negative terminal of the LED.
Insulate the soldering joint by using the heat-shrink tube.
Step 4: Prepare the DC Jack
The DC jack is used to feed the power from the 12V adapter. Here I have used a 5.5 x 2.1 mm DC jack.
First, apply a small amount of soldering flux on the two terminals.
Solder a piece of red wire to the positive terminal ( Short leg ) and black wire to the negative terminal.
Insulate the soldering joint by using heat-shrink tubing.
Step 5: Prepare the Speed Controller
First I have tried to mount the speed controller directly onto the lid. But, unfortunately, it was not accommodated in that space. So I have removed the potentiometer from the PCB.
Desolder the potentiometer by using a desoldering pump then remove it from the PCB.
Then connect the potentiometer to the PCB through 5 wires. Insulate the soldering joints by using the heat-shrink tube.
Step 6: Enclosure Design
I have designed the enclosure in Autodesk Fusion 360. The dimensions of all the components are measured by a vernier caliper then the same were considered during the design.
The enclosure has 5 parts:
1. Body
2. Body
3. Cartridge
4. Lid
5. Fan Grill
Download the STL files from Thingiverse
Step 7: 3D Printed Enclosure
I have used my Creality CR-10 Mini 3D printer and 1.75 mm Blue and Yellow PLA filaments to print the parts. The main reason for selecting these colors is just to match my Hakko soldering station. It took me about 10 hours to print the main body and around 4 hours to print the other parts.
My settings are:
Print Speed: 60 mm/s
Layer height: 0.2mm ( 0.3 also works well)
Fill Density: 20%
Extruder Temperature: 210 deg C
Bed Temp: 55 deg C
Step 8: Prepare the Bodies
Before assembling the main body, smooth all the rough edges with sandpaper.
Place the M3 threaded insert as shown in the above picture and apply heat by using your soldering iron tip.
Step 9: Install the DC Jack
Insert the DC jack into the holes provided at the right side of the body. Then tighten the nut.
Apply a small amount of hot glue to secure it.
Step 10: Install the Fan
Insert the fan to one half of the enclosure, then attach the other side, parts should fit snugly together. Ensure that the fan is oriented correctly to suck in air from the front and push the air out the back.
After snapping together the two sides of the enclosure, pull the wires to the front as shown in the above picture.
Step 11: Prepare the Filter Cartridge
The fan used in the fume extractor will suck in toxic fumes from the soldering iron, but the exhaust will be trapped inside the room which is again harmful to health. This problem can be avoided by running the fumes through a carbon filter to neutralize them.
First I have measured the 3D printed cartridge size, then cut the carbon filter by using scissors or a box cutter. Here will use 2 pieces to improve filtration.
Finally, add the carbon filters to the cartridge one on each side, and snap it together.
Step 12: Install the Fan Grill
Attach the fan grill to the back, my fan came with a grill and (4) M5*10mm pc case mount screws so I reused them.
If you don't have the fasteners you can use super glue for a permanent joint.
Step 13: Wiring and Final Assembling
Install the speed controller, led, and switch into their respective slots in the lid. Then solder all the connections as shown in the circuit schematic.
Don't forget to use heat-shrink tubing around exposed wires and connections to insulate and protect the wires.
Connect the positive wire from the rocker switch to the DC IN + terminal on the speed controller, and the negative wire from the DC jack to the DC IN - terminal. Then connect the positive and negative wires from the fan to the MOTOR OUT + and - terminals.
Finally, add some hot glue to the switch, LED, and speed controller to hold it in place and install the lid with the two M3 screws.
Step 14: Final Testing
Now the Fume Extractor is ready for final testing. Insert the 12V DC adapter into the DC jack on the right side, then switch on the rocker switch. You will notice the LED will be turned ON, then set the fan speed to maximum by turning the potentiometer.
Place your soldering iron tip with small flux on its tip, you will notice the fumes are sucked into the fume extractor. I have placed the extractor about 10-15cm away from the soldering iron and found it works great.
The downside in this fan ( 74 CFM / 126 m³/h @ 1,350 RPM. ) has a lower CFM, meaning you'll need to keep it closer to what you're soldering. If you want to increase this distance, you may use a fan with High airflow (CFM).
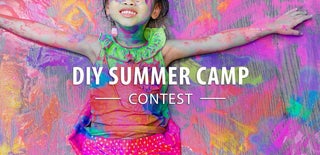
Participated in the
DIY Summer Camp Contest