Introduction: Build Your Own Eco-Quad Copter From Reused and Recycled Materials
Being on a high school student's budget is not the best place to begin. The more I looked into the possibilities, the more discouraged I became, because the typical materials and components used in a quad copter are either out of my price range, or prone to destruction after just a couple of rough landings. I soon realized that I was really going to have to think outside the box to come up with an affordable design concept that could get off the ground, without breaking the bank, or my hopes and dreams for flying.
As I began designing this, my first quad copter, I had certain goals that I wanted to achieve. First my multi-rotor must be watertight, since I want to fly it over water, as well as land. Therefore, I needed to consider the materials for the fuselage, as well as those that would connect the body parts together. Obviously, my quad copter must also be buoyant, so again material composition, as well as the weight of each part, needed to be considered. Finally, I wanted to be able to fly the quad copter at night and have it be discoverable, if it were lost in a wooded area with dense foliage, so my lighting choices were also important.
After spending some long nights in front of a computer screen, as well as many days experimenting, designing and assembling, I present the AZ-Eco Quad...
.
Step 1: Potential Recycled Materials
Step 2: Materials I Used
2-b. Many components make up the electrical system of the quad copter. The space that these components require must be considered when choosing the containers that will house everything.
2-c. I have always enjoyed Arizona Ice Tea™, so early on I decided that the durable structure of the 42 oz containers would make substantial fuselage arms for the quad copter. When I came up with this layout idea, I started looking for a sturdy, square-type container that would provide a dry environment for the main electrical components.
2-d. It took some time and experimentation to find a plastic container that would house the power distribution board, control board, battery and wiring. I discovered that this Planter’s™ 40 oz container had enough room for the components and would fit well in my design with the 4- 42 oz Arizona Ice Tea™ bottles.
2-e. Since many plastic containers that could be used for a project like this one have adhesive labels, you will have to plan on spending time removing the stubborn ones. Some typical household products that can help in this process include soaking in vinegar, mayonnaise, or even hot soapy water. These require a little more time and effort, while products like Goo Gone ™ work quickly, with less work. No matter which method you choose, be sure to remove all of the residue from the surfaces, so that later on, the process of painting your containers is more effective.
2-f. It is very important to have a variety of adhesives and fasteners on hand to assemble the components required to complete this project. Adhesive products such as contact cement, epoxy, duct tape, Shoe Goo ™ and JB Weld ™ may be needed to connect plastic, metal and wood surfaces. Other useful items might include: Velcro, zip ties, thin wire, string, rubber bands, and various sizes of screws, nuts and washers. Cannibalizing of broken or discarded small appliances can be a great source for all kinds of useful fasteners.
2-g. Different types of plastic items may also be useful. For example, worn out pens and markers can be emptied, taken apart and used as spacers, or tubing for wires and screws. I am cutting up an old plastic food storage container as the base and cover plates for the power distribution board. PVC pipe connectors left over from home plumbing projects will be used for part of the arm and motor platform assembly.
2-h. An important tool used to build this quad copter is a soldering iron. Electrical solder is needed for tinning and splicing wires. Bullet connectors and other devices must be properly soldered together so that electricity flows through the system effectively. During the assembly process, it is also helpful to have a heat gun to reduce the shrink wrap around connectors and bundles of wires to keep them insulated against electrical shorting and protected where rubbing, or vibration might occur. Note: Shrink wrap must be placed over the wires and connectors before doing a soldering job. Then you slide the shrink wrap up and over the parts to be protected, and it is ready to heat and shrink.
2-i. The power distribution board (on the left) and the control board (in the center) will both be housed in the capsule container. The wires (on the right) will connect the control board to other components.
2-j. A foam cold drink holder, like this one, can provide a safe environment for some of the sensitive, electronic equipment that will be used. I plan to cut one up to create a protective housing for the control board.
2-k. Because the inside base of my capsule container is not flat, I will need to use two layers of foam, glued together with contact cement, to create a raised, level and cushioned perimeter for the power distribution board.
2-l. In a quad copter like this one, four ESCs (electronic speed controllers) are required for flight. They will be housed in each of the four fuselage arms, close to the capsule body and within short reach of the control board.
2-m. A wire cutter/stripper is needed to cut and strip the 12 and 14 gauge wire used for the electrical system. It also helps to have a multi-meter to test electrical continuity to be sure that soldered wires, connectors and circuits are constructed correctly.
2-n. When choosing a battery, it is important to consider the load and flight time requirements of the quad copter. For this specific project, I decided to use an 11.1 Volt LiPo battery.
2-o. Each of the four brushless motors and their components will be mounted at the end of an arm on the quad copter. 1) Male and female bullet connectors, 2) Motor, 3) Propeller mounting parts, 4) Prop Savers, 5) Prop saver connectors, 6) Motor mounts with screws
2-p. Because spinning propellers are potentially dangerous, attaching them to the motors is one of the last things you will do during the assembly process. Two of the propellers will rotate in a clockwise direction and two will spin counterclockwise. It is also a good idea to use propellers of two different colors, so that the operator can easily distinguish between the front and rear of the quad copter during flight.
Step 3: Quad Copter Capsule
3-a. Let’s get started with the capsule. After removing all of the labels, make a template to show where your screw and wire entry holes will be located on the capsule container and arms. I created a template and marked the hole locations on the 4 sides of my capsule container.
Since drilling can crack this type of plastic, I used a heated screw (held by adjustable, locking pliers) to melt and push through the plastic to make these holes. Not only does the plastic stay intact, but the melted plastic actually forms into a ring and helps to reinforce the holes. (See picture in step 4-a.) Note: This type of activity should definitely be done with the help of an adult, who knows what he/she is doing. An adjustable, high heat soldering iron, or wood burning tool with multiple tip attachments can also be used to complete this type of task.
3-b. The ESC wires will run through this hole. The melted plastic reinforces and creates a smooth pathway.
3-c. This is one of two screw holes for the bridge parts that will support the battery holder across the inside of the capsule near the top.
3-d. Four screw holes, like this one, are required on each of the four sides of the capsule to allow the connection of the fuselage arms. During the final assembly process, secure fuselage arm attachments will be made with waterproof glue, lightweight plastic wall anchors and screws.
3-e. (1) Assembly inside the capsule container will start at the bottom. Since the base is raised in my container, I glued these two foam circles together with contact cement to form an even, stable platform for the control board housing. If you are using this type of container for your capsule, be sure to cut the bottom foam circle slightly bigger than the top one, like a beehive, so that it will take the shape of the bottom of the container.
3-e. (2, 4). The power distribution board assembly will sit on top of the foam circle base. Using an old plastic food storage container, I cut top and bottom plates, slightly smaller than the capsule container, for this purpose. (The type of plastic that I used allowed slight bending, so that I could fit the plates through the top of the capsule container.) The bottom plate has 5 circular plastic pieces that serve as spacers that I glued with Shoe Goo™. (I cut mine from old plastic knitting needles with a Dremel ™ tool.) The bottom plate is attached to the upper foam circle with Shoe Goo ™ applied with a worn out craft brush. The middle spacer/post has a screw hole through it and allows the large center hole of the power distribution board to be placed over it securely, and then the top plate, with a screw hole in the middle, covers the board.
3-e. (5, 6) The control board housing will be put into the capsule container next. I cut a foam cold drink holder to create this environment. The foam container has been cut to a height of 2 ¼ inches, with rectangular openings (about 2 ½ inches by ¾ inch) cut into each side for air flow and wires to pass through. The 2 inch (5 cm) control board sits snugly into the foam base of the container. The holder is covered at the top with a round, clear plastic circle cut from a spinach container and attached to the foam base with 4-#6 x ¾ inch nylon screws with nuts. The bottom of the foam housing sits firmly in a 3 ¼ inch diameter plastic peanut butter jar lid, into which a screw hole has been cut that allows a screw to go through this section, connecting it to the top plate and the center post of the power distribution board section.
3-e. (7, 8, 9)You need to create a stable, dry environment for the battery in your capsule container. In my quad copter, the battery and its holder is located at the top, just below the container lid.
3-f. I cut the holder from a piece of Luan plywood into a 5 ½ inch (4 cm) by 2 inch (5 cm) rectangle, with the corners cut on a diagonal to fit the wall contours of the capsule container. I drilled out some of the wood with a ¼ inch drill bit to lighten the weight of the board and to allow air flow. I then cut slits into the sides of the board to allow Velcro straps to pass through so that the battery will be held securely in place during flight.
3-g. Finally, you will want to have air flow in your capsule container, because the electrical components can get pretty hot. I cut holes for two air vents in the cap of the capsule container, and glued watertight seals for attaching old vitamin caps that snap open and closed.
Step 4: Quad Copter Fuselage Arms
4-b. The cutout in the base of the tea bottle (one of the four arms of the quad copter) is where the ESC wiring will be run from the capsule container.
4-c. Because of the heat generated by the electrical components, I wanted to create a venting system, but one that would be waterproof. As you can see in the corresponding pictures, I cut off the ends of toothpaste tubes that snap open and closed. Then I cut the appropriate sized holes into the middle of each fuselage arm, about 2 inches (5cm) away from where the arms and capsule containers will be attached. I created an adhesive water seal, using Shoe Goo™.
4-d. Now you will need some kind of support in each arm for the ESCs. I layered two pieces of foam inside each of my tea bottles, as seen in the corresponding pictures. The ESCs will be positioned on top of the foam, with adhesive Velcro for support and shock absorption.
4-e. You will use wall anchors, screws and Shoe Goo™ to insure a watertight connection between the fuselage arms and the capsule container. In this step, I inserted the 4 plastic wall anchors in the screw holes already cut into the base of the of the tea bottles (in step 4-a), and again… held them in place with Shoe Goo™. (The screws will be used in the arm to capsule assembly later.)
Step 5: Motor Platform Design
5-a. To make the motor platforms, you will need to choose a base and materials to fill in as layers, to create a firm support for the motors.
5-b. I decided to start with identical, metal pickle jar lids that have diameters of 2 ¾ inches (7 cm) and circular pieces of Luan plywood. After creating a pattern for the circular plywood pieces that would fit securely into the pickle jar lid, I used a Dremel™ tool with a barrel sander attachment to sand and shape all of the larger wooden areas.
5-c. When the wooden cutout had a rough outline, I took a smaller Dremel™ routing attachment and removed the wood in the tighter areas of the pattern and cut out the almond-shaped piece for the motor platform, as well.
5-d. Two slits are cut into PVC slip/slip connector to match the curve of the pickle jar lid, using a small Dremel™ rotary saw blade. Three 1/8 inch holes are drilled into the base of the connector between the two slits. Then two #6 by 3/8 inch screws are screwed into the outer two holes. The hole in the middle allows the epoxy to flow over the connector wall and into the pipe, during motor platform assembly.
5-e. This is the basic layout of the motor platform. The wooden pieces will be placed inside of the pickle jar lid first. Then the PVC slip/slip connector will be positioned so that the screws line up with the two outer curves in the wood, with the almond-shaped piece being placed between the inside edge of the connector and the lid edge.
5-f. These pictures show the basic positioning of the wooden pattern against the PVC slip/slip connector, as well as the way the almond-shaped piece fits inside of the connector, in order for you to understand how these components will be placed inside this section of the motor platform.
Step 6: Motor Platform Assembly
6-a. To assemble the four motor platforms for the quad copter, you must first organize all of the necessary materials. I chose the following materials: four patterned pieces of 3-ply plywood, 4 almond-shaped pieces of 3-ply plywood, epoxy for plastics (5 minute epoxy works the best, in my experience), 4 pickle jar lids with diameters of 2 ¾ inches (7 cm), 4- ¾ inch (2 cm) slip/slip PVC connectors (with slits cut and screws attached), 4- ¾ inch (2 cm) 90° street spigot/slip elbow connectors, 8 circular fiberglass cloth pieces (cut slightly larger than the inside circumference of the pickle jar lids), 4 circular fiberglass mat pieces (cut to the same size as the 4 fiberglass mat pieces), popsicle sticks, newspaper, small throw-away paint brushes, and rubber gloves.
**Note: There are other types of materials that could be substituted for the ones I have mentioned. The ultimate goal is to build motor platforms that are solid and keep the motors stable and free of vibration during flight.
These are the steps I took to complete the motor platforms, using the materials listed above:
6-b. After collecting all of the materials, thoroughly mix the two parts of epoxy with a popsicle stick at the bottom of one of the pickle jar lids, and spread it evenly.
6-c. Then place a fiberglass cloth circle over the top of the epoxy and push it down gently with a popsicle stick, in order for the cloth to adhere to the metal base.
6-d. Use a brush to carefully tuck the cloth under the lip of the lid and distribute the epoxy evenly.
6-e. Once the fiberglass cloth is in place, carefully slide the wooden pattern and the almond-shaped piece into the lid to form the next layer. The wooden almond-shaped piece will be secured between the inside of the slip/slip PVC connector (to be placed in the next step), and the edge of the pickle jar lid. Mix and apply more epoxy on top of the wood and spread it evenly.
6-f. Now take one of the PVC slip/slip connectors and place the slits over the lid, so that the half of the connector with the two screws is sitting inside the lid. You may have to move or shift the PVC slip/slip connector around a little bit in order for the almond-shaped piece to fit inside the pipe. (You are checking for proper positioning in this step.)
6-g. Next mix and brush a layer of epoxy between the slits in the connector to create a strong connection between it and the base. While doing this, be sure that you are spreading the epoxy generously into the hole in the middle of the slip/slip PVC connector, to further ensure a sturdy connection for the base.
6-h.Then place one of the fiberglass mat circles as the next layer. Mix and apply more epoxy over the top of the circle and brush it down until all the loose fiberglass strands are glued down to the base and adhere to the pipe. Push the epoxy in and around the two screws.
6-i . After applying the epoxy, place the second fiberglass cloth circle on top of the fiberglass mat and press it down with a brush to make sure that the fiberglass mat fibers are trapped.
6-j. To finish off the motor platform, mix and apply one last layer of epoxy to seal it off and ensure that all of the layers are secure. Repeat these steps three more times to complete all of the motor platforms needed for this quad copter.
6-k. After completing all of the motor platforms, you will need to attach each of the PVC slip/slip connectors to a 90° street spigot/slip elbow connector so that the motor platforms can be attached to the arms of the quad copter.
6-l. This elbow connector fits snuggly into the opening of the 40 oz Arizona Ice Tea™ container. Use 2- #6 by ½ inch stainless steel screws to connect each elbow connector to either side of the tea bottle. Select a drill bit that is slightly smaller than the #6 screw for drilling the holes, so that the screws will grip tightly into the bottle. I also blunted the end of each screw ahead of time with a Dremel™ tool, so that wires would not be cut.
Step 7: Soldering and Wiring
7-a. Soldering is an important step in assembling the electrical components. This picture shows the soldering jobs that are necessary:
1) Connections for the battery
2) ESC wiring to the battery and motors
3) 12 gauge accessory wiring
4) Motor wire connections
5) 14 gauge accessory wiring
7-b. Soldering is a skill that requires some background knowledge and practice. Here are some tips that will help someone who is unfamiliar with this activity:
7-c. The underside of a 12 inch by 12 inch (or larger) ceramic tile is a perfect surface on which to do soldering jobs, because it is fire-proof and impervious to the melting solder. Lay out the materials you need for the job on the tile ahead of time, because soldering involves some quick moving steps.
7-d. Keep the soldering tip clean at all times using a very wet sponge or cotton cloth saturated with water. I also use a copper wire scourer to help keep the soldering tip clean, while it is hot.
7-e. Be sure to melt a tiny amount of solder on your tip immediately before undertaking your next soldering task. This will allow the solder to melt more quickly and freely as you begin the task.
7-f. When working with wire, remember to always tin the tips of the wires before attempting to solder into electrical connectors. This is done by heating the copper wire with the soldering iron. After heating the wire up, continue to hold the iron to the wire and melt the electrical soldering wire until all of the small gaps in the copper wire are filled, to ensure a solid electrical connection.
7-g. While soldering the bullet connectors, it is helpful to bring the tip in contact with the barrel to preheat it. By following this suggestion, you will reduce the chances of making a poor, or “cold solder connection”. Once you have preheated the connector, quickly move the tip through the tiny hole in the side of the barrel, while at the same time, insert the solder downward through the rim and against the iron's hot tip. Keep the iron in continuous contact until the solder begins to melt. Once melting occurs, fill the barrel close to the top of the rim. Immediately push the electrical wire (that has been previously tinned) into the molten pool of solder, while simultaneously removing the iron from contact. With the iron removed, the liquid solder will harden instantly. Doing this step rapidly will ensure that the solder will not spill out onto the external sides of the connector. Repeat these steps for the wiring of all your male and female bullet connectors.
**Note: For tips on how to tin, solder, and remove solder, there are many sites on the Internet and videos on YouTube that demonstrate these tasks.
Directions for Soldering Jobs
1) Connections for the battery:
Although my battery came with a pair of Dean’s connectors pre-soldered at the manufacturer, that might not be the case in all situations. So… the following steps I took may not directly apply to your component specifications. Having said that, here’s what I did with the electrical path from my battery to my power distribution board: To the bare end of the Dean’s connected wires (supplied by the manufacturer), I soldered an insulated pair of bullet connectors, male to the black wire and female to the red. To further strengthen that connecting point, I added a ¾ inch piece of black shrink-wrap.I decided to do this step, because I was not sure I’d be able to detach the supplied Dean’s connector (for reuse) without damaging the plastic casing. This decision required that I make a length of wire-pairs soldered at one end with mated insulated bullet connectors and then soldered directly to my power control board at the other. For all of the above, I used 12 gauge wire that I had previously measured, cut, stripped and tinned.
**Note: Shrink-wrapping options include using a heat gun on a low setting, cigarette lighter, butane torch, or hair dryer with a very high heat setting. Heat the material carefully until it shrinks tight around the connectors and wires to be protected.
2) ESC wiring to the battery and motor wires:
On the battery side of an ESC, solder a male bullet connector to the red wire and a female bullet connector to the black wire. Repeat this step for each ESC. On the motor side of my ESCs (not pictured), there are three blue wires which lead out to the propeller motors. To these I spliced and soldered three separate lengths of 14 gauge wire which were needed to reach through the fuselage arms to the point where they would connect to the motors. I used one red, one black and one yellow wire to complete this process. At the ends (motor side) of each of these spliced wires I soldered female bullet connectors. I then insulated all exposed wires and connections with shrink-wrap.
3) and 5) 12 and 14 gauge accessory wiring for added components to the distribution board:
You may want to add other components to your power distribution board, if you have extra connection circle pairs left on your board after soldering your ESC wires. One advantageous component to add is a low voltage alarm that emits a loud audible sound just before the battery is exhausted, giving the operator time to land the quad copter. You could also include lighting, camera power and servo lines to perform tasks such as camera movement and parachute deployment, which I hope to add to my quad in the near future.
4) Motor wire connections:
On the three wires attached to my motors (red, black and yellow), I soldered male bullet connectors to match up with the females coming from the corresponding ESC wires. Each were shrink-wrapped accordingly. Repeat this process for each of the other motors.
7-h. Next work on wiring that will be soldered to the power distribution board which will later get connected to the ESCs and other accessories. I organized the wires into red and black pairs. I stripped off about 3/16 of an inch of insulation off the ends of each wire. I tinned all of the wire ends. I then decided which color of wire would be attached to the inner and outer circuits of the board. Based on my research, I chose to solder the red wires to the inner circle and the black wires to the outer circle. I positioned my wire pairs so they can be soldered to the small contact points of the board so that they lead out conveniently to the fuselage arms. It is important to remember that none of the solder should cross over from the inner circle to the outer circle, and vice-versa.
Step 8: Fuselage Arm and Motor Assembly
8-a. Begin the arm/motor assembly with the completed motor platforms.
8-b. After drawing a line through the middle of the pickle jar lid and marking two motor mounting hole locations, (on the underside of the motor platform), drill the holes completely through the motor platforms. (Size and placement of the holes will be determined by the specs of your motors.)
8-c. Attach the motor mounts to the base of the motors with the small screws that come with them, using Allen wrenches.
8-d. To check proper fit and placement, set the motor units on the platforms. Use two screws and nylon lock nuts to attach each motor assembly. Then remove the motor units, and plan to reattach once the fuselage arms are painted.
8-e. The wiring that transfers electricity from the ESCs to the motor wires are connected with male and female bullet connectors that have been soldered to the ends of the wires. It is a good idea to check your wiring layout, before painting.
8-f. After painting the fuselage arms and attaching the motor platforms, you are ready to put in the ESC wiring. Make a snake of some kind to assist the careful pulling of this wire bundle through each arm into the PVC slip/spigot and PVC slip/slip connectors. Once the ESC wires are through the PVC connectors, connect the color-coded ESC and motor wires with the male and female bullet connectors.
8-g. Once the wiring of an arm is completed, use Velcro to attach the ESC to the foam that was placed in the quad copter arm previously.
8-h. Finally, reattach the motors to the motor platforms with the screws. **Note: So that the motor wires at the point below the propellers do not get hit and cut, strap elastic bands around the wires and attach the bands to the motor mount screws. This will keep them out of harm’s way during flight.
Step 9: Landing Gear
9-a. You will need to design landing gear for your quad copter. First I removed labels from these 16 oz Arizona Ice Tea™ containers. Then I created a template for a cutout that would allow for the attachment of the legs to the fuselage arms. Next I cut off the caps and placed the template over the tops of the bottles to mark my cutout locations. Using a Dremel™ tool, I made the necessary cuts.
9-b. This is one type of landing gear that could be used. These are more stable for landing, but affected more by windy conditions during flight.
9-c. Landing gear made from these broken spray nozzles are a bit less supportive during a landing, but also less affected by adverse wind conditions. After much testing and tweaking, I decided that this was the best lading gear overall.
Step 10: Painting
10-a. Decide what type of paint you will use to add the finishing touches to your quad copter. Being a part-time Arizona resident, I decided to use red, blue, yellow (AZ flag colors) and silver spray paint. I started with silver paint to spray the fuselage arms, because they needed to be painted earlier in the process for wiring purposes. Before spray painting the arms of the quad copter, I taped a piece of paper that had been cut to mask the base of the bottle, because I didn’t want to spray any paint on the foam located just inside the bottle, or clog up the plastic wall anchors that are attached to the bottom.
10-b. The silver color will reflect heat and keep the inside of the quad copter cooler during flying time.
10-c. The capsule container must also be masked on the top for entry of light. (Some control boards require light to work properly. I also plan to use LED lights that I want to see clearly from the top of the capsule.) I also masked the sides where the fuselage arms will be attached.
10-d. In contrast to the silver fuselage arms, I masked around the outer edge of the capsule container bottom to spray paint it red, which I predicted would make the capsule easier to see during flight.
10-e. I also decided to paint my clear propellers red, so that they will be more visible, while flying. I carefully wet-sanded each thin coating of spray paint, to create a smooth, thin uniform surface that would not add weight or create additional vibration, which can adversely affect flight of the quad.
10-f. For even better visibility of the quad’s underside, skins can be patterned and cut from brightly colored materials, that can be interchangeable. I used fluorescent orange tape to attach to the undersides of the 4 motor platforms and landing gear legs.
10-g. These pictures show the final painted look of one of the fuselage arms attached to the motor platform.
10-h. The final painting step was to spray paint the landing gear. Since I have two sets of landing gear, I chose to paint them differently.
Step 11: Final Quad Copter Assembly
11-b. Space in the capsule container while making these connections with a screwdriver might be a little tight, but with some patience, you can complete the job. As you proceed, it might be a helpful to ask for some assistance.
11-c. As you continue to follow the steps of attachment for each arm, the space inside the capsule container will get even tighter, so you may have to use a smaller sized screwdriver.
11-d. While attaching the arms to the capsule, it is helpful to make a string of rubber bands to wrap around the wires, so that they can be pinned against the sides of the quad copter to keep them out of the way. The other side of the rubber band strings are attached to the motor platforms.
11-e. Fuselage arms are attached and ready for the landing gear.
11-f. My first set of landing gear is attached by pushing the cutouts of the smaller painted tea bottles, into the grooves of the fuselage arms. The cutouts allow them to “clip” over the screws that are located there. Zip ties and Shoe Goo™ can be used to make a more permanent connection. For my second set of landing gear, I used foam tape for compression into the ridges of the tea bottle. Zip ties will hold them tightly to the fuselage arms. They have been painted yellow and blue, and detailed with decals cut from free bumper stickers.
11-g. After attaching the landing gear, it is time to assemble the components of the capsule container. I had previously used Shoe Goo™ to attach the foam circles to the base.
11-h. Next I glued the lower plate of the power distribution board to the foam. Then I set the board over the middle spacer and distribute its wires toward the fuselage arms for the ESC connections. The battery wires should be placed in a way to reach and connect to the battery. I placed the top plate over the board, and then the peanut butter jar lid (base for control board housing) over it. I used a screw to attach all of these parts together, through the preset holes.
11-i. Then it was time for me to set the protective, foam control board housing into the peanut butter jar lid, as seen in the corresponding picture.
Next with my KK control board positioned snuggly into the base of the foam enclosure, I connected each of the four ESC ‘data-lines’ onto the labeled pins as required for proper operation. In my experience building this quad copter, this aspect of my project really seemed like it might require a ’rocket scientist’, but somehow everything has come together!
**Note: It is not likely that you will use the control board that I ended up purchasing (KK Multicopter Controller by Rolf R. Bakke, 2010 - Version 5.5 - www.kkmulticopter.com). Although this board was extremely powerful a couple of years back and is still a functional component today, there are now quite a few newer options available. Thanks to the great support at the above website, I am learning a lot of technical information related to ESCs, RC transmitters and receivers and of course… control boards.
11-j. Battery placement is next. In my quad copter it is attached to the Luan plywood base with Velcro and placed securely underneath the cap of the capsule container.
11-k. You will need to purchase a remote control transmitter with a compatible receiver. I chose a Fly Sky Model FS-TH9X because it was a great price, and it is a virtual clone to the Turnigy version that is so popular with people I know who fly quads. Make sure to install the appropriate reciever for the RC transmitter of your choice. I installed mine below the capsule lid so that the antenna could be positioned through one of the vent holes. This provides a strong signal connection to my transmitter.
11-l. LED lights were selected to be installed into this quad copter, because they are lightweight, bright and operate independent of the LiPo battery. This unit was attached under the capsule lid with some Velcro. These lights, when turned on before flight, will continue to strobe for many hours when the quad copter is being flown at night, or if it lands or crashes out of the operator’s view.
11-m. In addition, I used Velcro to attach a lightweight tap light to the underside of the capsule container to assist in night flying. A lightweight “keychain’ video camera is attached to the underside in the same way.
11-n. The corresponding picture shows the completely assembled AZ-Eco Quad. With independent lighting and landing gear, my quad copter weighs just over 4 pounds.
Step 12: Conclusion
As you can see, I am better at building quads, than flying them!
While making our family’s annual summer trip from the east coast to Arizona, I was frantically typing the information and directions for this Instructable contest. Please excuse any “bumps in the road”… it was a long trip.
Well, I made the deadline… creating a quad copter that floats, is watertight, and can be flown at night or in a forested area, without being easily lost! With the quantity and availability of reused and recycled materials, the possibilities for designing and creating new drones is limitless. Every time you are ready to throw something into the trash or recycling can, look at the shape, check out the weight, and let your imagination take flight!
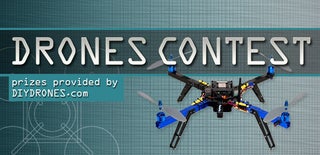
First Prize in the
Drones Contest
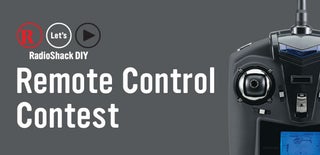
Participated in the
Remote Control Contest
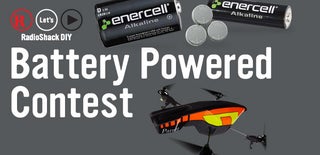
Participated in the
Battery Powered Contest