Introduction: Build Your Own Motorcycle Hard Bags
I wanted a set of hard bags, but I couldn't find any that were perfect. And I'm kind of .... thrifty. So I decided to make my own fiberglass hard bags.
Step 1: Materials. I Used Cardboard As a Template, a Bit of Plywood, Balsa, Fiberglass Resin & Cloth, Sandpaper, Auto Body Filler, Paint, and Some Hardware.
Step 2: Make a Template
I knew the basic shape that I wanted the outline of my saddlebags to be, so I first cut it from cardboard, then transferred the shape to a piece of plywood. This image shows it attached to the siderail of my bike, so I could see how much clearance I had between the bag and the exhaust. Cardboard will let you play with the size and shape easily.
Step 3: The Lid
You'll need to get into your saddlebag, so part of the template has to be cut to start forming the lid. This is the plywood, after transferring the shape from my cardboard template. You'll need 4 of these pieces to make 2 bags.
Step 4: Width
At this point, you'll need to decide how wide you want your bags to be, and you'll have to cut some ribs. I used plywood, because I had a spare piece around, but any small dimension stock would do. This is also a good time to make some copies of that side we had a template of - you'll need four in all. I wanted my bags to be wide enough to hold a gallon paint can or milk carton, so I went a little wider than most of the bags I've seen for sale commercially.
Step 5: Start Forming the Framework.
With some ribs cut, and a couple of side templates made from thin plywood, you can glue the ribs between your side pieces. I used toolboxes just to hold everything in place while the glue dried. The newspaper is there to keep any glue drops that run from sticking my project to the shop floor. You only need to do a couple of ribs along the bottom at this point - you're just trying to connect the two sides.
Step 6: Add More Ribs
Give your bag more structure by gluing in more ribs. You'll also need to think about the shape of the opening of your saddlebag when the lid is raised. To help keep rain out, I planned to build a little raised lip around my opening under the lid. The square section of ribs glued in at the top are the beginning framework of that.
Step 7: Now Start Adding Your Skin.
This is where things start to get exciting, as your bags begin to look like saddlebags. I glued individual pieces of balsa to the frame and ribs. I used balsa to keep it as light as possible, while providing some structure for my fiberglass to stick to. (Can you tell that I had observed a friend applying fiberglass to a cedar strip canoe he was building?) These pictures also show that I added some ribs to my lid template pieces, and used small blocks to give the tops of my lid a rounded curve. Balsa bends easily, so you can use it to give your bags compound curves. I used plywood for the bottom of the bag, as that can just be flat and I wanted it to be strong.
Step 8: Compound Curves
I wanted the outside of my bags to have a more rounded shape, so I used the balsa to give them a compound curve. The side of the bag lying on the floor will be the flat side that attaches to the bike. This is probably a good time to remind you that if you do a compound curve on the outside instead of slab sides, you need to make a right and a left bag, not two identical rights or two identical lefts. Slab-sided bags can be identical, but curved-sided bags need to be mirror images.
Step 9: Start Fiberglassing.
Here I have the two lids in my workshop. I cut a single piece of fiberglass cloth big enough to do each lid, then applied a layer of resin according to the product instructions. I left a bit of extra material which I later cut off.
Step 10: Keep Fiberglassing
You'll need to cut some interesting shapes from your fiberglass cloth. I tried to cut pieces as large as I could, for strength, with little tabs and such for overlaps. You'll also need to figure out ways to stand your project up to apply the resin without accidentally gluing it to your shop floor or your support. You want 2-3 layers of cloth. Try to get them as smooth as possible - that will save you some time sanding later on.
Step 11: Don't Forget the Lids
Don't forget to fiberglass your two lid pieces. Here I have everything glassed and the lids are just sitting on top of the cases. Be careful to keep your pieces separated as you work - you don't want to accidentally glass your lid to the bottom and have them stuck together.
Step 12: Hardware
A note about hardware. I got these hinges & latches from a marine supply site on the web. They're stainless steel, to stay shiny after years of use. Also, the latches can be locked. I bought one of those trailer hitch pin locks to be able to lock up my stuff.
Step 13: A Lip.
To help keep rain out, I added a raised lip to the edge of my case opening. You'll want to fiberglass the insides of your cases and lids, too. Well, it probably isn't totally necessary, but I did mine that way to make them as strong and weatherproof as possible.
Step 14: Smoothing
To prep for painting, I used auto body putty to smooth things out. Apply a layer as thin as you can, sand smooth, repeat.
Step 15: Brackets
To attach the bags to the bike, I needed to make brackets. I used angle iron from the hardware store. I welded pieces together to get the dimension I needed, but you could probably bolt pieces together as well. The piece of cedar here is just to ensure I would have space between my exhaust and the bottom of the bag. Exhaust pipe = hot.
Step 16: Keep Sanding & Smoothing
You didn't think you were done sanding & smoothing, did you? Seriously, keep sanding. Let the body filler dry, then sand some more. Go to the spot putty when you're down to the tiny flaws.
Step 17: Prime
When you think you're done sanding, it's time to prime. I used a rattle-can of auto primer. Notice that I have predrilled the holes for my hardware before painting.
Step 18: You Didn't Think You Were Done Sanding, Did You?
Primer will reveal flaws. Time to use the spot putty and smooth those over.
Step 19: Now for Some Color.
I went with flat black, followed by gloss clearcoat. All from rattlecans, as this was a relatively small project.
Step 20: And You're Done.
Here are the finished bags attached to the bike. I've just got the brackets bolted though my side rails. There are just two bolts that go through the side of each bag, so I can remove them pretty quickly if I need to. I can carry 4 gallons of paint on my widebody motorcycle!
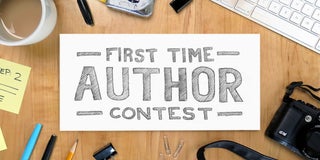
Participated in the
First Time Author Contest