Introduction: Build a Printmaking Press!
Have you ever wanted to get a press for making block prints, searched online, saw the multi thousand dollar price tag and dejectedly said: "dang nevermind"? This is exactly what went through my mind as I looked for presses online. I make a decent amount of prints, enough that I realized I was spending so many hours pressing our prints by hand, and because I'm pretty busy these days, I'd like to recover as much of that time as possible. So I took matters into my own hands and put that [almost] engineering degree to use building the machine I need to take this to the next level.
If you aren't familiar, in relief printmaking, you place paper over a block which has been carved like a stamp and then rolled with ink. By either pressing on the paper with an object like a spoon or baren, the design is stamped onto the paper. A press allows me to roll the paper and block under high pressure, essentially doing this job for me more consistently and much quicker, as well as using less forearm effort.
This press is sturdy enough for linocuts, but since I do not do etchings and other kinds of printmaking, I'm not sure how it would do with jobs requiring higher pressure. For this reason, I hesitate to call it an etching press. Nonetheless, it does what I need easily and up to standards so I'm very happy with how it came out.
Even if you don't plan to build a press, maybe there's a neat trick or two you can take from this to implement on your next project!
So let's go build this thing!
Step 1: Design Considerations
To start, I went online to look for inspiration for this project. Initially I purchased a set of plans from https://buildapress.com/ which had many helpful ideas. You would certainly benefit to get those plans if you are thinking about building a press. Ultimately though, I ended up doing a different design I created after looking at the showcase of presses that people had built on that same website. This new design uses lightweight parts that are easier to manufacture by hand, and makes several replacements in design and materials in places where I do not need as much strength for my applications. Specifically, this design is based off images of a press model by David Cambridge: https://buildapress.com/images/show/David%20Cambridge/David%20Cambridge-2016-bench.html
Step 2: Functionality
Here's a quick and dirty primer on how the press works:
- A sandwich is formed between the upper and lower roller, consisting of the paper, the ink, the linoleum printing plate, and the bed (see image)
- Turning the handle drives the bottom roller, advancing the bed forward
- If the top roller is low enough down, the sandwich will be under pressure as it passes through the rollers
- This pressure is what forces the ink to adhere to the paper, making your print
Step 3: Assemble Drawings
I modeled all parts for this design in Solidworks, which is a kind of CAD or Computer Aided Design software used often by engineers. I decided to make the press bed 19" wide and 4 feet long to handle even fairly large prints. This software allows me to create 3d models of each part needed, assemble them into a final "assembly", and then create a packet of engineering drawings. Each drawing shows the part from several views, and all the useful dimensions labeled
These drawings will be key to let me machine all the parts I need, so it's worth spending a lot of time making sure they are well made and accurate.
Step 4: Materials
This press is mainly built of aluminum and steel, held together with hex bolts and nuts. I avoided glue as to make it possible to disassemble, flatpack, and transport because I move around a lot. In total, everything I needed (including a lot of new tools I had to buy) cost a bit over $600. That sounds like a lot (and it is) but it is significantly less than the prebuilt presses I found online ($1700 to $4000). Obviously there is also the cost of my time to consider, but I was on vacation anyways and decided to spend much of it doing this. The goal is that this machine will pay for itself as I'm able to work faster and produce higher volumes.
You can buy all these metal parts at Metals Depot online or Coremark Metals online. Both will let you specify to cut the parts to the length you need (which is totally worth the time and labor saved) and they deliver in about one week turnaround. This was my first time using them but I highly recommend both honestly. I also bought a piece or two from ebay, which sometimes has a decent supply of metal in different shapes and sizes
For structural parts, I mainly used 1/4" thick aluminum bars and angle, and also steel angle. I also used several 3/8" diameter and 1/2" diameter steel rods
The top blocks require some 1"x1" steel and the hub piece requires a small square of aluminum 1" thick too
You'll also need two key parts common to almost all press designs out there: flange bearings and take up bearings
The rollers use some 1" diameter steel rods, some large aluminum tube (3" and 5" diameter for lower and upper roller respectively) as well as more 1/4" thick aluminum plate to cut out some donuts
In the mix is some assorted hardware (3/8"-16 hex screws and nuts, 1/2"-13 nuts and washers, a 10-24 set screw and 3/32" hex wrench for it, some bearings and shaftcollars) which I just got at Home Depot / Lowes / your local hardware store
I added some 3d printed parts to the mix, though arguably they could be considered optional as you will see later. These I printed using my Ender 3 printer (Worth the $200, would recommend as a first foray into 3d printing if you're interested!)
Step 5: Tools
Originally I did not have many tools for metal, since I've never built anything involving so much metal before. Still, I had an assortment of wood tools, many of which turn out to still be applicable to metals. To accomplish the operations I needed, I invested in a few key things:
- Hacksaw + replacement blades
- Various taps and a tap wrench (used for cutting threads inside a hole)
- Various dies and a die wrench (used for cutting threads on the outside of a rod)
- Cutting fluid / lube
Most of the time I try to get away with cheap alternatives especially if I know I'll only use it once. But I suggest you spend a little more to get decent quality taps and dies that aren't the $10 set from harbor freight. Cutting threads SUCKS if you have poor quality, dull, tools. It's amazing how good it feels to use a decent sharp tap or die. Just. Do. It. And save yourself hours of frustration!
By the way, using a tap and die was totally new to me, but it turns out to be a very handy skill- if you're interested to learn how to do it, many instructables such as this one have already done a good job explaining: All About Tapping for Screws and Bolts : 7 Steps (with Pictures) - Instructables
If you don't already have one, a small vice like this one (YOST VISES LV-4 Home Vise 4-1/2" (1 Pack)) is absolutely essential here. Actually, it will be very helpful for working on many many kinds of projects far beyond just metals so it will likely be the most versatile and useful tool used today
Step 6: PART I: Handle
The handle which turns the bottom roller consists of four rods connected to the hub piece
The hub piece connects to the shaft of the bottom roller using a "key" which is just a small piece of metal stuck in a slot that allows the hub to turn the shaft. A set screw keeps the key in place, making sure the handle does not fall off
The handles are deliberately very long to increase the torque and mechanical advantage of the user. All this means is, I can turn the handle from the very end using even very low force, and the press will apply significant pressure to the print. I added 3d printed balls to end of the rods to improve the aesthetic and mask off the raw edges of the rod. That part is totally optional.
Step 7: Hub
The hub is basically just an octagon of metal with several important holes. Namely, there is:
- Four holes that go partway into the sides to accept the handle rods. They are tapped to have threads inside the holes
- One through hole in the center face to accept the 1" diameter shaft of the lower roller. There is a rectangular cut out as well to accept the key- this was made just by filing away material until the key fits in place
- One through hole in the top that comes out into the slot for the key. It is tapped to have a set screw sit inside, which can be tightened down onto the key to keep it in place
The octagon shape can just be made by cutting the corners off a square with a hacksaw, and filing down until smooth
Step 8: Handles
The handles are reasonably simple things, just four 18" lengths of 1/2" steel rod with threads cut partway down one end of the rod. Cutting threads requires a die like the one in the picture above. When die cutting threads, clamp the rod into the vice, tightening it AS MUCH as POSSIBLE! Literally pull with all the force you have to tighten it enough that it wont rotate when you cut the threads
To cut threads, the die is turned around the rod, turning one rotation, then turning it backward a bit to crack off all the cut metal. This is continued downward until there's enough threads on the rod. These rods will screw into the hub piece
Step 9: Handle Caps
To cover the raw ends of the rods, I 3d printed some handles. The shape is just a sphere with a hole partway down one end
This filament I used changes color as you move down the spool, so you get this fun gradient effect!
The caps can be glued onto the non threaded end of the rod using some 5-minute epoxy
Step 10: Assembly
The whole handle comes together just by screwing the handles into the hub piece and it's good to go!
Step 11: PART II: Take Up Mechanism
The press needs to have a way to lift the upper roller up and down to adjust for different thicknesses and pressures required going between the rollers. To do this, a piece called a take up bearing is used. This bearing has a hole in the middle for the axle of the roller, but also channels along the side and a special slot in the top
The take up bearing can move up and down along the direction of the channels when a screw is locked into into the top part of the bearing with a shaft collar. The shaft collar is a ring shaped piece tightens onto the screw and prevents it from coming out of the bearing
By turning the screw (which lives inside a threaded piece), the screw moves up and down very gradually, allowing for fine adjustments
Step 12: Sidebars and Guiderails
The sidebars are just two pieces of angle steel. These serve crucial structural purpose holding the whole thing together while also holding the guide rail pieces. The sidebars are made just by drilling several holes into the pieces, being sure to remember the symmetry of the piece (there is a left and right "handed" piece!)
The guide rails are cut from 1/2x1/2 extruded aluminum square. The only other preparation for these is to drill two holes and tap them for the 10-24 screws which will come from the sides and screw into the guide rails, attaching them to the sidebars
Step 13: Top Bar
This piece of 1x1 aluminum square is key to the whole operation. Two holes are drilled partway down on the small faces, which will then be tapped to accept 3/8-16 hex bolts.
Then, one larger hole is drilled in one of the larger faces. This hole needs to get tapped for the large seven inch long 5/8-11 hex head screw
It's a simple piece, but takes a bit of time since you're carving out a fair bit of material, so patience is key
Step 14: Knobs
To make it easy to turn the hex head screws without a wrench, I 3d printed nice big knobs with a hexagon shaped indentation in the bottom. This makes it very easy to just epoxy the knobs onto the screws like I did earlier with the other handles
These handles unfortunately are not that strong because they're still just semi-hollow lightweight plastic, so if the screw ever gets really tight, I occasionally hear a tiny cracking sound, which is never a good thing. Having these parts made out of solid plastic would likely help a decent bit
Regardless of knob material, if the screw is really tight, there is a problem in the mechanism that needs to be addressed first, like something binding up due to awkward angles, since the handle should not take considerable effort from the human to twist in the first place
Step 15: Assembly
First, the guide rails are attached to the side pieces
Then, the top piece is attached using two bolts
The take up bearing can be slid into the assembly between the guide rails
The screw comes in from the top until it enters the hole in the top of the take up bearing
A shaft collar should be placed in this slot so that the screw then enters the shaft collar
Once it's in, the shaft collar is tightened onto the screw using a hex wrench
That's it! Test for operation by twisting the screw. As you turn it counterclockwise, the take up bearing moves down, and as you turn it counterclockwise, the take up bearing moves up. If it is very tight to turn, try loosening some parts, and also check that the guide rails are really tightly screwed onto the side pieces (such that they are not squeezing/binding the bearing)
Step 16: PART III: Structural Components
I chose to have this design use pieces that don't require major cutting or shaping of curves, because doing that by hand ISN'T FUN! AT ALL! When you have just a hacksaw, the less cutting the better I say.
Hence the structure is mainly just flat bars and angle aluminum that I can order online cut to the right lengths. Then, I *mostly* just have to drill the holes (which is still a big job, but largely reduced the brunt work)
Step 17: Top and Bottom Horizontals
The top horizontal pieces are just aluminum flatbar with several holes drilled
Two slots needs to be made- these slots allow support axles to move up and down the slot and be adjustable. The way to make slots by hand is just:
- Drill two holes
- Cut out the material between the holes by opening up your hacksaw (use a mini hacksaw) and threading the blade through the top hole, then close it back up. The hacksaw is now literally stuck inside the hole, which is actually just what you want! You can then cut out the piece, and unlatch, remove the hacksaw
- File the slot edges with files until adequately shaped
The top horizontals also need one small cut to remove material to make room for the axle of the bottom roller. This is unfortunate but I couldn't think of a design fix in time so this is what I went with. (At least i'm honest about it!) Thankfully it doesn't have to be a very neat cut since nobody will see it
The bottom horizontals truly are just angle aluminum with holes in them. That's it
Step 18: Structural Shafts
There are four 3/8" shafts (two at the top, two at the bottom) which connect the two halves of the machine. They will connect to the halves using nuts, therefore they need to be threaded partway down each end
Once they have been cut to a good length, a die is used to cut threads on each end, around an inch down. Enough that the nuts and thickness of the sides material will fit, plus a little excess for good measure
Step 19: Support Shafts
There are two support shafts in the design, which have two bearings on each of them. They fit into the slots we worked on earlier. The idea is that they will support the bed as it passes through the rollers hence the name support shafts
They are mostly the same as the structural shafts (rods cut to size and threaded down both ends) but with the addition of the bearings. The bearings I bought turned out to be incredibly tight on the shaft. Enough so that I could not possibly get them on with my hand alone
The fix is simple: bang them on using a pvc pipe!
You can't hammer down the bearing with a mallet alone because as you hit some point on the bearing, the point on the bearing 180 degrees around is not getting pushed down. As a result of the downward force from hitting down on one end, that other edge actually gets pushed up, leading to the bearing just getting tightened onto the rod crooked. It will never go down smoothly.
Instead, you need to hit the bearing with equal force all around the face. The best way to do this is to find a pipe that fits around the rod, but also still sits on the face of the bearing. Then, I just hammer down on the end of the pipe, which applies just the well distributed force I need to slowly push it down, a few millimeters at a time
When I'm satisfied with the positioning (it's not that important) I can move on
Step 20: Bottom Crossbars
This piece is unnecessary unless you are in my specific situation. Let me explain myself. I knew that this press was going to go on a table that was just barely not wide enough for the full footprint of the machine. I could not just rest the machine on the bottom horizontal angle aluminum because they would be falling off the table. For this reason, I introduced the bottom crossbars, two steel flatbars that provide a surface upon which to support the machine.
By putting rubber feet on the crossbars, the machine can be supported with the angle aluminum resting on top, overhanging the table. This is best seen in the second image above
The crossbars are simple to make anyways, just two holes drilled and that's all
Step 21: In Memoriam: the Vertical Supports
Originally, there was supposed to be four small sections of aluminum bar going vertically on each corner, providing relief to the top horizontals, which overhang quite a long distance without any support. I thought there would be a significant moment, which means a tendency for the aluminum bar to rotate
However, two things happened that caused me to eliminate these pieces:
- I realized the metal is plenty strong enough to support the forces involved
- I ran out of time lol
So it really was a happy finding that once all the nuts are tightened well, there is no need for these pieces
Step 22: Assembly
This pic is from a test fitting I did of all the pieces. It's extremely satisfying to see it take shape
Thankfully, it mostly went together well! Metal is unforgiving, if the hole is off, you can't just squeeze and bend the parts to make it fit, you have to drill another hole or file/reshape the parts. And thankfully that was not necessary
Step 23: PART IV: Rollers
The rollers are a key part of the design, and also something which caused me considerable unhappiness- you will see where this pain originated shortly
The rollers are built up from an axle in the middle of a section of tube. To connect the two, a donut shaped piece is inserted on both ends so everything can turn concentrically
Step 24: Shafts
The shafts are straightforward– the top shaft is a plain 1" shaft cut to length, and the bottom is keyed 1" shaft cut to length
As a reminder, the keyway is needed so that the handle hub can connect to the bottom shaft and turn it using a small piece called a key which, naturally, fits into the keyway
Step 25: Donut Caps
At this point in the process, I was running out of the time. I had to move back to school and leave the shop in literally a few days, and things were looking bleak. As soon as I started cutting out these donut caps from a small plate of aluminum, I realized how awful it is to cut weird shapes out of aluminum by hand. Each circle took almost an hour each. This is exactly why I made the design use mostly commonly available shapes with minimal custom contours
Many of you will say: go buy a DISC of aluminum! To which I say, yes, I would have, but at this point in the timeline I could not find a way to procure them in 1-2 days
So I cut out the donut caps (at least for the smaller bottom roller) and filed them down so they'd fit internally on the section of aluminum tube. One helpful method I found was the following:
- Place the donut on top of one end of the tube, trying to have their centers aligned onto the same axis
- In some parts you will see a tiny gap between the donut and inner diameter of the tube (meaning the radius of the donut there is small enough to fit inside the tube). In some parts the donut will overhang the tube (meaning the radius of the donut there is too large)
- Mark the sections of the donut that are too large with marker
- Return to the vise and file down the marked sections
- Repeat this process in a loop until the donut just perfectly slides down into the tube
Step 26: Joining
Originally, I wanted to try joining the roller parts using these aluminum brazing rods I found, which can apparently form a very decent joint even without welding (which there was no way I was going to do)
I gave it a shot, but failed miserably. With the blowtorch, I could not get the aluminum parts up to the required 700 degrees Fahrenheit; I got close to 300 and it immediately dropped down when I removed the torch (I used a laser thermometer gun to check often). Thus any joint I got was due to melting the rods themselves which creates a very poor joint. What's more, the alloy kept beading up and not adhering at all.
What I'll say is this: The fault was probably completely mine and not that of the rods. I have seen plenty of people do this correctly, but:
- My parts were enormous, thick heat sinks
- I likely did not clean the parts well
- My torch was pretty underpowered
I think it would be best to have someone with experience do this job for you
But with this being literally the last day to work on this, since I would leave the shop the next day, I needed a solution and QUICK. I turned to gluing the parts together with JB Weld, a type of glue for metal. This worked very well and set to a strong bond overnight. I would definitely suggest this method and skip the brazing rods altogether. Easier and also less dangerous
Step 27: Troubles!
So I have a confession to make. I didn't have enough time to cut the donuts for the upper roller......
But determined to make this work, my frantic last minute solution was to 3d print the donuts, which you see above in these seven spoked wheel looking parts. In a moment of pure luck, they fit perfectly inside the tube and perfectly on the shaft
Actually, they worked surprisingly well. The only issue is that they are definitely NOT durable to very high pressures. It turns out they do not break under the pressure I need for my linocut prints, but when I push the pressure further than that, I hear little cracking sounds when something goes through the rollers. The wheels themselves stay intact but I suspect tiny fractures are forming inside the wheels. For the future, i will look into having these parts made of either solid plastic or going back and finishing those metal donuts that didn't get finished. The 3d printed solution is only temporary.
Step 28: PART 4.5: Extraneous Bits
The only last couple of things needed are many hex screws, nuts, some washers, rubber feet, and a little brass key
Oh and obviously the table for the press. This is just a piece of melamine that has been cut to 19" across by 4 feet on a table saw. This cut is kind of dangerous if done improperly, so make sure you do this with all the support you need, push sticks, standing in a safe place out of the way of kickback. Consider where the cut piece or outfeed will go. Will it have reliable support to rest on? Melamine is REALLY HEAVY and the last thing you want is for it to fall when a blade is spinning. This cut might be better achieved using a circular saw
If you ever feel uncomfortable going into a cut, your gut is probably telling you something. Pause, rethink it, and consider alternative ways to do the job.
Step 29: PART V: Assembly
The way the press was designed, almost all parts can be carried in a disassembled state and packed long and flat like IKEA boxes- nice!! So the pieces can be transported to a suitable location, and then:
It's finally time to assemble this thing! Find a nice big table and grab an adjustable wrench along with your ratchet
Step 30: Base Structure
The bottom of the machine is built up from the crossbars and bottom horizontals. Then, one merchanism assembly and top horizontal can be added, along with the several rods that fit into these parts. One flange bearing can also be added now.
The rollers can also be added now. This was probably the most frustrating step of the process, because the fit between the axles and the bearing was extremely tight. Be patient and if you have the ability to, filing down the edges of the axle can help it enter the bearing holes more easily
Then, the other mechanism assembly and top horizontal can be added along with the other flange bearing, going around, making sure all the rods and axles are going into the holes they're supposed to
First, check that nothing is terribly crooked, and when you feel confident that you dont need to make any adjustments, go ahead and tighten all the nuts well so nothing moves around
Step 31: Table and Handle
The table just slides onto the support bearings and between the rollers of course. Now is a good time to adjust the support rods so the table doesn't flop around so much
The handle is deliberately built to be removable by just loosening or tightening the set screw which presses down on the brass key. I'm in a small space, and I would easily bump into the enormous handle, so this is a helpful feature. Just keep track of the hex wrench and key piece
Step 32: Tuning
The press will not make perfect prints the first time around. Though I still need considerable practice to better understand this machine, a few things are really key upon first trials:
- Pressure
- Pressure Too Low: If the roller is too high up, it will not engage with the plate and push down, leading to not enough ink transfer
- Pressure Too High: If the roller is too low, it will take a lot of force to turn the handle, and the roller will squeeze too hard on the plate, forcing the paper into the small crevices. In turn, you lose the fine details and the lines become uneven. This is easy to see in the comparison images above
- Pressure Sweet Spot: There is a sweet spot where you have just enough pressure, and when you do, the result is really very satisfying (Medium Pressure in the images demonstrates this sweet spot)
- Axle angle
- Crooked: If the axle is not parallel to the melamine bed, then one end of the shaft is higher than the other. This means your press will come out pressed too hard on one end, and not enough on the other. Spend some time correcting this so the axle is not visibly crooked
Step 33: Completion!
That's how I built my own press, saving hundreds of dollars (but spending dozens of my own hours) in the process! I'm excited to see what this bad boy can do, and I may even post tutorials on how to use it in the future. With practice, I will be able to roll out prints with speed unimaginable to me before
In one timed test, I was able to hand print a plate in about ~ 1-2 minutes, while it took 12 seconds to do with the press (including aligning and placing the paper down), meaning the press is potentially able to increase my speed six or more fold!
What's more, in the comparison images in the last step, I tend to like the medium-pressure press output better than the hand printed. When I press by hand, the tool in my hand sometimes falls into the valleys of the block, picking up chatter marks / noise and stray ink that I don't want, also thickening lines slightly. Because the press roller by its design only pushes straight down and to a limited extension, it's able to avoid these effects due to the hand printing.
One might say they prefer the hand printed version. Another might say they prefer the press version. Ultimately, that's completely subjective and up to you to decide! But I'm very happy with how this project turned out, and can't wait to continue to put this tool to use
If you stayed along this far, thanks so much for reading!
-Javier
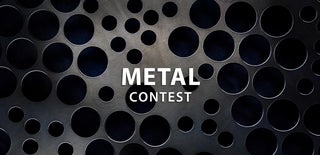
Second Prize in the
Metal Contest