Introduction: Build Your Own Professional Forestry-Trailer!
In this Instructable I will show you how to build your own professional Forestry-Trailer with a lot of technical highlights!
For example:
- an overrunning brake
- movable boogie axle
- flexible loading platform
You can build it for your own, personal woodwork, but its also strong enough for a commercial use. It has a load capacity from about 6tons, and the logs can be up to 5 meters. I tried build this vehicle as professional as possible, but with keeping an eye on the total costs. Thats why I spend a lot of time with searching for cheap components e.g. at junkyards, farmhouses etc.
In this instructable, I don't want to enjoin every measure or every material you have to use, because this really depends on the resources that are available on your personal storage, steel trader or junkyard. I will give you a rough guide how to begin such a great project, and give you some ideas how the biggest problems during the manufacturing can be solved.
At first I will give you a short overview of the tools and machines I used:
Very Important to have:
- Welding Equipment: I used a MIG-welder with a power from about 200A
- Angle Grinder: for cutting and grinding, its good to have a small, and a big one
Machines you don't need that often (steps can also be done by someone else, friend/metalworker/whatever):
- Drilling Press
- Turning Lathe
- Bending Machine
So you can see, if you own a small welding machine and an angle grinder you already comply with the basic requirements!
But you also need other components that you better not build on your own:
- a crane or excavator: this can be a small crane that is mounted on tractors or trucks, it should have a load capacity from about 300-600kg with a minimum range of 3,5m
- two axles from agricultural trailers
- an overrun breaking unit (hopefully its mounted on one of the trailers where the axle is from)
- hydraulic cylinder for moving the boogie-axle
- 4 rigid flange bearings for mounting the boogie-axle
- other things like hydraulic components, a long bowden-cable for the brakes, 4 tires
You can see that the complexity of this project really depends on you and the recources you have. You can build a more easy trailer, without brakes and without a moveable axle, or you can choose this highly sophisticated version!
So lets get started with the things you need, two trailer axles and the breaking unit: Just butcher two old agricultural trailers and in the best case you have two axles with tires and a braking unit.
After that we can start building the main frame.
What you need:
1 long square pipe, I found a 5,1m long 180x180x5mm Pipe at the junkyard
6 square pipes, 160x90x5mm
6 pipes 70x5mm, 200mm long cut with an angle of 30°
12 pieces of flat steel, 30x5 with a length of 160mm
2 U-profiles, 160x65x6mm
At first you cut the big pipe 600mm from the ent with an angle of 10°. Now you turn around the short part and weld it onto the pipe again to get the hitch into the right distance from the ground. After that you can weld the other square pipes on both sides of the frame. I started with the first on 250mm from the back end (without the angle), the other ones 2270mm and 3120mm from the end. After this is done you can mount the 6 round pipes on the ends of the square pipes by supporting it with the flat steel.
The two U-profiles are welded to the end of the frame, they are for mounting some lights or the license plate.
The next step ist the axle carrier:
What you need:
2 angle profiles, 200x200x19mm with a length of 600mm
4 flat steels, 40x10x600mm
2 square pipes, 180x100x7mm
2 pipes, 70x5mm 200mm long, cut with an angle of 30°
4 triangles of metal plate for the reinforcement (e.g. 150x150x15mm)
2 flat steels, 120x320x15mm
2 flat steels, 120x160x15mm (these four components carry the flange bearings, so you should drill the holes before welding it to the frame)
The two angle profiles are the sled that can slide on the frame to change the position of the axle. This function is used to reduce the turning radius or adjust the supporting load. After you drilled fife 14,5mm holes into each of the four flat steels (40x10) you weld them onto the l-profiles with an angle of 45°. Make sure that the holes fit correctly before welding it to the L-profiles. After that you can mount the two square pipes at the L-profiles. These square pipes carry the mounting for the stanchions, so you have to make an 70mm cutout. The cutout can be made by drilling a circle of many small holes, the edge doesn't have to be very precise!
After drilling the holes for the flange bearings, you can weld the two longer flat steels at the end of each square pipe. The shorter flat steels should have a distance of 350mm to the outer ones.
The four triangles can be used to reinforce the hole construction.
Now we can start building the boogie-axles!
What you need:
2 square pipes, 90x90x733, with a length of 900mm
2 axles 50x350mm
the two trailer axles
You have to cut a hole in the middle of each of the two square pipes. The position of the bar, relative to the axle depends on the measurements of the tires you are using. The distance between the tire and the bearings should be as short as possible, to reduce the torque that is exposed on the bearings. You should also give the trailer the same track width as the tractor to reduce the roll resistance on forest soil.
After that you have to put the trailer axles and the bars on an plane surface to adjust it precisely parallel. After you have welded the axles to the end of the bars, you can cut out the middle part of the trailer axles.
The stanchions
8 pipes 60x4mm, 2m long
8 pipes 70x5mm, 50mm long, cut with an angle of 30° (take the parts you cut away from the pipes before)
The stanchions are made of a 60x4mm Pipe. I don't have a bending machine, so i had to give these pipes away for bending it. I choosed a parallel offset of 500mm to get an outer width of 1800mm. The bending radius depends on the material you are using, a bigger radius is stronger! After bending the pipes, adjust the length so that all pipes have the same measures. After that you can put the stanchions into their bracket at the frame an weld the pieces of pipe at them. Now they will always return into their "home" position after turning it!
You can weld an angle profile on the frame between the stanchion brackets, the sharp edge will help to keep the logs in position.
Now you can construct a mounting for the hydraulic cylinder to move the axle. I chose a cylinder with a diameter of 50mm and a stroke of 400mm. The mounting depend on the cylinder you are using, in most cases you can just weld a rod onto the frame.
You will also need a headboard to keep the logs from damaging your crane. The shape of this headboard really depends on the crane you are using, make sure that the boom can't touch the headboard. In case of an emergency brake, It must be strong enough to keep the logs in position!
The crane
You need a very strong mounting for the crane! The design of this mounting depends on the shape of the crane or excavator you are using. Its good to have a tractor with a front loader, a forklift or something like that to mount the crane.
Most commonly those cranes are driven by the tractor hydraulics, so you will just need two hydraulic hoses in the correct length and two couplers.
The hitch
The hitch with the overrun braking unit must be mounted at the angled front of the frame. You can either weld it directly on the frame, or you can make it adjustable by using two plates with holes, to adjust the position of the hitch.
Assembling
Now you can assemble all the parts you made, make sure that you give it a nice color! Don't forget to mount some back lights and blinkers!
Now I'm at the end of my little instructable, I hope the pictures will answer the rest of you questions. If not: don't hesitate to contact me!
Have fun with your own DIY Forest Trailer !!!
For example:
- an overrunning brake
- movable boogie axle
- flexible loading platform
You can build it for your own, personal woodwork, but its also strong enough for a commercial use. It has a load capacity from about 6tons, and the logs can be up to 5 meters. I tried build this vehicle as professional as possible, but with keeping an eye on the total costs. Thats why I spend a lot of time with searching for cheap components e.g. at junkyards, farmhouses etc.
In this instructable, I don't want to enjoin every measure or every material you have to use, because this really depends on the resources that are available on your personal storage, steel trader or junkyard. I will give you a rough guide how to begin such a great project, and give you some ideas how the biggest problems during the manufacturing can be solved.
At first I will give you a short overview of the tools and machines I used:
Very Important to have:
- Welding Equipment: I used a MIG-welder with a power from about 200A
- Angle Grinder: for cutting and grinding, its good to have a small, and a big one
Machines you don't need that often (steps can also be done by someone else, friend/metalworker/whatever):
- Drilling Press
- Turning Lathe
- Bending Machine
So you can see, if you own a small welding machine and an angle grinder you already comply with the basic requirements!
But you also need other components that you better not build on your own:
- a crane or excavator: this can be a small crane that is mounted on tractors or trucks, it should have a load capacity from about 300-600kg with a minimum range of 3,5m
- two axles from agricultural trailers
- an overrun breaking unit (hopefully its mounted on one of the trailers where the axle is from)
- hydraulic cylinder for moving the boogie-axle
- 4 rigid flange bearings for mounting the boogie-axle
- other things like hydraulic components, a long bowden-cable for the brakes, 4 tires
You can see that the complexity of this project really depends on you and the recources you have. You can build a more easy trailer, without brakes and without a moveable axle, or you can choose this highly sophisticated version!
So lets get started with the things you need, two trailer axles and the breaking unit: Just butcher two old agricultural trailers and in the best case you have two axles with tires and a braking unit.
After that we can start building the main frame.
What you need:
1 long square pipe, I found a 5,1m long 180x180x5mm Pipe at the junkyard
6 square pipes, 160x90x5mm
6 pipes 70x5mm, 200mm long cut with an angle of 30°
12 pieces of flat steel, 30x5 with a length of 160mm
2 U-profiles, 160x65x6mm
At first you cut the big pipe 600mm from the ent with an angle of 10°. Now you turn around the short part and weld it onto the pipe again to get the hitch into the right distance from the ground. After that you can weld the other square pipes on both sides of the frame. I started with the first on 250mm from the back end (without the angle), the other ones 2270mm and 3120mm from the end. After this is done you can mount the 6 round pipes on the ends of the square pipes by supporting it with the flat steel.
The two U-profiles are welded to the end of the frame, they are for mounting some lights or the license plate.
The next step ist the axle carrier:
What you need:
2 angle profiles, 200x200x19mm with a length of 600mm
4 flat steels, 40x10x600mm
2 square pipes, 180x100x7mm
2 pipes, 70x5mm 200mm long, cut with an angle of 30°
4 triangles of metal plate for the reinforcement (e.g. 150x150x15mm)
2 flat steels, 120x320x15mm
2 flat steels, 120x160x15mm (these four components carry the flange bearings, so you should drill the holes before welding it to the frame)
The two angle profiles are the sled that can slide on the frame to change the position of the axle. This function is used to reduce the turning radius or adjust the supporting load. After you drilled fife 14,5mm holes into each of the four flat steels (40x10) you weld them onto the l-profiles with an angle of 45°. Make sure that the holes fit correctly before welding it to the L-profiles. After that you can mount the two square pipes at the L-profiles. These square pipes carry the mounting for the stanchions, so you have to make an 70mm cutout. The cutout can be made by drilling a circle of many small holes, the edge doesn't have to be very precise!
After drilling the holes for the flange bearings, you can weld the two longer flat steels at the end of each square pipe. The shorter flat steels should have a distance of 350mm to the outer ones.
The four triangles can be used to reinforce the hole construction.
Now we can start building the boogie-axles!
What you need:
2 square pipes, 90x90x733, with a length of 900mm
2 axles 50x350mm
the two trailer axles
You have to cut a hole in the middle of each of the two square pipes. The position of the bar, relative to the axle depends on the measurements of the tires you are using. The distance between the tire and the bearings should be as short as possible, to reduce the torque that is exposed on the bearings. You should also give the trailer the same track width as the tractor to reduce the roll resistance on forest soil.
After that you have to put the trailer axles and the bars on an plane surface to adjust it precisely parallel. After you have welded the axles to the end of the bars, you can cut out the middle part of the trailer axles.
The stanchions
8 pipes 60x4mm, 2m long
8 pipes 70x5mm, 50mm long, cut with an angle of 30° (take the parts you cut away from the pipes before)
The stanchions are made of a 60x4mm Pipe. I don't have a bending machine, so i had to give these pipes away for bending it. I choosed a parallel offset of 500mm to get an outer width of 1800mm. The bending radius depends on the material you are using, a bigger radius is stronger! After bending the pipes, adjust the length so that all pipes have the same measures. After that you can put the stanchions into their bracket at the frame an weld the pieces of pipe at them. Now they will always return into their "home" position after turning it!
You can weld an angle profile on the frame between the stanchion brackets, the sharp edge will help to keep the logs in position.
Now you can construct a mounting for the hydraulic cylinder to move the axle. I chose a cylinder with a diameter of 50mm and a stroke of 400mm. The mounting depend on the cylinder you are using, in most cases you can just weld a rod onto the frame.
You will also need a headboard to keep the logs from damaging your crane. The shape of this headboard really depends on the crane you are using, make sure that the boom can't touch the headboard. In case of an emergency brake, It must be strong enough to keep the logs in position!
The crane
You need a very strong mounting for the crane! The design of this mounting depends on the shape of the crane or excavator you are using. Its good to have a tractor with a front loader, a forklift or something like that to mount the crane.
Most commonly those cranes are driven by the tractor hydraulics, so you will just need two hydraulic hoses in the correct length and two couplers.
The hitch
The hitch with the overrun braking unit must be mounted at the angled front of the frame. You can either weld it directly on the frame, or you can make it adjustable by using two plates with holes, to adjust the position of the hitch.
Assembling
Now you can assemble all the parts you made, make sure that you give it a nice color! Don't forget to mount some back lights and blinkers!
Now I'm at the end of my little instructable, I hope the pictures will answer the rest of you questions. If not: don't hesitate to contact me!
Have fun with your own DIY Forest Trailer !!!
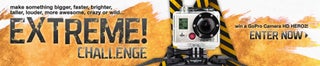
Finalist in the
EXTREME! Challenge
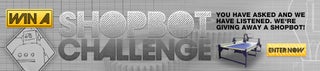
Participated in the
ShopBot Challenge