Introduction: Building XR-35 Toy Truck (3D Printed)
The XR-35 Fuel Rig is the first of the fully 3D printable toy series called the Drone Age from Blokko.
Set in a world ravaged by a total ecological meltdown in the late 22nd century, the XR-35 is the first of the machines that would dig deeper into the earth's core, soar high to the lower atmosphere where agriculture is still possible, and take to the stars in search of a new habitable planet. This, is the start of the Drone Age.
That's the backstory. Oh wait, should it be called a backstory if the story takes place in the future? How about we call it the prologue.
Alright in this instructable, I'll go over how the truck is printed and assembled in a comprehensive manner.
Who is this for
Anyone with a 3D printer / access to a 3D printer.
Materials
- 1 x XR-35 files (here)
- 5 x Rubberbands
- Printing Material - PLA/ABS for rigid parts and Flex for tyres.
I always recommend using PLA for printing, as it is a biodegradable material (arguably), and much more easier to print compared to ABS. Please always buy your material from a reputed source (Verbatim is a great company, though expensive, remember the old floppys ?) to make sure that it is free of contaminants.
Note
I am the designer of this toy and a co-founder at Blokko. I wanted to share this tutorial here for two reasons. First, I had a great time building this, the kids love it and I love to show that 3D printing is not just about cups and plates. Second, here I can show all the little nuances involved in the building process. I grew up building trucks, jeeps and whatnot from cardboard boxes and natural latex (it was the 80s and we had a rubber plantation).
Step 1: Calibrating, Printing and Cleanup
The toy was designed to be printed without supports and to fit together right off the print bed. The current 3D printing process though, still requires a bit of human touch to get right. But you know that already.
Assuming a fair familiarity with the process, we are going to calibrate the filament settings so that all the parts in this set can fit together as intended. Why? Not all filaments are made the same, and their diameters could vary greatly between manufacturers and even between colors. So to get prints that fit well with each other consistently, we have to calibrate the filaments to a single standard unit.
Calibration (figure 1)
Print the file calibration_puck in the folder "Calibration" with a 15% infill and without supports/rafts. The idea is to get the two parts of the puck to fit together with a fit described in engineering terms as between "tight" and "sliding" and they should be able to fit together from either ends. This step requires you to meddle with a couple of slicer settings (flow rate / filament diameter). Once you print the first puck, try to fit it together and look for the following results
- The parts fit tightly together from both sides : The flow rate is at a good value and the bed height is at optimum. Good job!
- The parts fit tightly together from one side, not the other : Means you have a good filament diameter/flow rate setting, but your bed is too close to the hotend making the first few layers to squish together too much. Adjust the bed height down or add a z-offset in your slicer.
- The parts fit rather loosely : Increase the flow rate setting by 3% and print the puck again.
- The parts don't fit together at all : Decrease the flow rate setting by 3% and print the puck again.
- The print comes off the bed before completion : The bed is too far away from the hotend. If you find that the bed height is not the issue here, it might have to do with the filament or the bed surface. Kapton tape + heated bed is a great solution for PLA. Reprap forums are a great resource for general printing issues.
This is a step that has to be repeated for every new filament. The silver lining is that you can save a separate profile in the slicer for each filament and use the profile when reusing an already calibrated filament. To do this, once you have a good flow rate value, increase the filament diameter setting in the slicer the same percentage as the reduction in flow rate (and vice versa), and save the filament profile. One thing to take note of - when slicing with a calibrated profile, make sure that you reset your flow rate to the nominal (1.0/100%).
Printing & Cleanup (figure 2)
So you have calibrated the filament. Congrats, you have completed the hardest step in this entire tutorial. Onwards to printing.
Slicing at a 0.2mm layer thickness with an average 45mm/sec print speed gives a good balance of speed and quality. A 15% infill is more than enough in most cases, depending on whether your printer is good at bridging gaps. That number can be increased if you get holes on the top printing surfaces.
Once the prints are done, its time to check the parts for sharp edges and smooth them out. There will most certainly be some for the surface that was touching the bed. Now, you can clean this up using a penknife/file/sandpaper - also known as the hard way - or use a kitchen gas lighter to just heat the edge up for 1-2 seconds and then just put your thumb over the surface lightly. This might take a few tries to get right but this is the fastest and the cleanest way to do it. One small issue with this technique is that it might darken the area depending on the flame. Be careful here not to heat the part for too long or you might burn your finger.
Step 2: Chassis Build
Now that the the parts are rolling in, its time to make the chassis (sorry about the bad pun).
Assemble the parts as shown in the pictures.
- Start by inserting the axles into the axle-box. You might have to tilt the axle from side to side to do this.
- Secure them with the axle-pins. Make sure that the axle can move in the box fairly freely, or you might have to take it apart and clean up the touching surfaces a little. Note : It doesn't necessarily have to be super smooth.
- Rubberband time! Tie the rubberbands any way you like around the axles (or you can use the hooks as in the images). The tighter the bands, the stiffer the suspension.
- Add the wheels and lock them in with the wheelnut. To lock the wheelnut, just turn it about 30 degrees counter-clockwise (it will click in).
There you have it! A great looking chassis with a working suspension.
Step 3: Cockpit & Boot
This a a fun step! Choose any of the boots from the 3 designs (Sleek, Bobber or Fuel). These were designed with printing time in mind with Sleek <2hrs, Bobber <5hrs and the full Fuel Boot taking a whopping 9 hours to print. The images features Bobber (red) and Sleek (blue). I personally love the Fuel boot as it makes the truck look substantial.
Again, follow the images.
- Put the cockpit top and bottom parts together with the frame_pins.
- Join the cockpit and the boot as shown, and push in the clickpin from below. This here, is what we call a pump-action joint.
The Pump-Action Joint
This is a joint that we developed specially for 3D printing. It is strong and opens up a world of possibilities for modular design. It gets its name from the fact that you have to pump it to open the joint. To open the one shown above, hold the boot and pump the cockpit towards and then away from the clickpin, essentially loosening it. Pull the clickpin out and its open!
Step 4: Let's Roll Out!
The last step is to put the two assembled pieces together.
If you look at the images, I have added an additional step to add a retaining rubberband to the clickpin for the chassis. This is an optional step, but a personal favorite of mine.
And Voila !
There you have it! A toy truck dripping with awesomeness that you made! Now roll out!
Personal Note
This is my first instructable, I had a lot of fun writing this and I hope you guys and gals enjoyed it too. If you would like to say hi or hit me with images, you can find me on twitter @pradlal
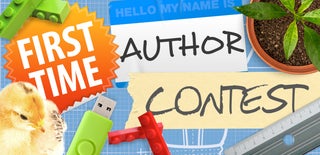
Participated in the
First Time Author Contest