Introduction: Building a 3D Printer Enclosure
Hello, this is a companion instrucatble to a video I posted about building an enclosure for my Ender 3 3d printer. The video talks mostly about the design choices and overall aspects of the enclosure but doesn’t really go into detail about how the whole thing is put together.
That’s what this is for. In this instructable I am going to go through the parts and pieces you would need if you want to build one yourself. However, this is going to be a bit of a ‘here’s how i did it’ NOT ‘here’s how you should do it.’ This works for me in my situation, it may not work well for you. So fell free to take any ideas from this to implement.
Supplies
The parts list for this project is a bit flexible. But I used the following parts. All of the parts I used I either got at the hardware store or 3d printed. I also used only tools that I knew I had or could get access too, which is part of the reason for the parts list.
Materials
- (3) 2”x2” 8’ furring strips - more on why these in the video
- (14) 3D printed corner brackets
- 1 box (1lb) of #6 3/4” drywall or wood screws
- (1) 2’x4’ 1/2” sheet of MDF
- (2) 2’x4’ 1/16” sheets of hardboard or mdf - more on this too
Tools
- Drill, with drill bits and screw driver bit to match your screws
- Handsaw and a joiner box (the joiner box is optional it just makes it easier)
- Table saw (also optional if your hardware store has a panel saw, or will cut panels for you, mine won’t)
- 3D printer - ngl this one seems obvious
- Measuring tape or ruler (I like this one from IKEA as it has both inches and mm) (editing note: it looks like they are discontinuing the worlds best tape measure for some stupid reason so this looks like the worse replacement.)
Step 1: Cut Everything
This is the most annoying step as it just takes a lot of time. You need to be fairly accurate and make the cuts straight, (the Joiner box helps a lot here if you are using a hand saw to cut the furring strips).
I have the dimensions and quantities listed bellow but note that this is for my printer in my location. You may need to make changes to get to work for you.
A bit more about my application seems like it would be useful. I have my printer in a closet in my office. I have 2 Ikea LACK tables that used to hold all of my printer/electronics stuff. I am replacing one of those tables with this enclosure. That means that my overall foot print is going to match the size if the LACK table so 550mmx550mm. The base frame will fit around that, and I want the height of my enclosure (excluding the top and bottom) to be 24”, if you are afraid of mixed measurements look away now, but being and engineer in the US I’m fairly used to it. This is a bit tall for just the printer but I have the KevinAKASam Belted Z-mod installed. This height won’t fit the standard filament roller mount so you may want to make sure you have a filament mounting location ready.
Here are the cut lists.
MDF
Cut the one sheet into (2) 21 5/8”x21 5/8” [550mmx550mm] these will be the top and bottom
The bottom is optional but I want to be able to move the printer in the enclosure so I added a bottom.
Masonite or Hardboard
For the sides I am using Masonite, at the store this was labeled as hardboard. You could use Plexi or acrylic for the sides so its clear, which I plan to do at some point but acrylic is expensive so I’ve just been keeping an eye out on second hand markets for it. Masonite is a cheap stand in for now.
I cut the (2) sheets I had into (4) side panels that are 24”x22” [610mmx560mm]. I cut the forth one just because.
Furring strips
These are the most annoying, if you want some thoughts on why I used furring strips instead of something like a printed member or aluminum extrusion, check out the video I have linked.
- (4) 533mm, 21" (Verticals)
- (4) 550mm, 21 5/8" (Horizontals on the sides)
- (3) 475mm, 18 5/8" (Horizontals around the middle)
Step 2: Print Everything
For this project I only printed 14 of these corner brackets that I designed. The overall print time is about 90 minutes each with my print settings.
I would suggest printing these out of PETG if you plan to print ABS or other high temp materials. I didn’t have any on hand so I printed mine from PLA+ and they seem to be doing alright but I expect I will replace them. I printed these face down. You can do several at once but I used sequential printing to reduce the risk of failure.
Also, print any hinges that you want. I haven’t put doors on mine yet because I am still trying to figure out what I want.
Step 3: Assemble the Side Frames
I designed this to be assembled into the side frames, then the side frames are joined together. and then the top, bottom, and sides are installed.
To assemble a side frame, connect 2 of the 21” and 21 5/8” pieces as show. Be sure to place the 21” piece inside the other. This will make a stronger joint as the force can move down the vertical piece in the final assembly. The other way will have all the force being supported by the printed bracket.
Use a corner bracket in each corner with 2 screws in each side.
Do this for the other side frame too.
Note, I did use a pilot hole for the first few but found it was not needed so stopped doing it.
Step 4: Connect the Side Frames
To join the side frames together. I use the remaining furring strip pieces and the remaining corner brackets to join them at the corners. Again see the image.
For the front I placed the corner brackets on the back side of the strip to give more clearance.
Also, I only use 3 here not four to keep the bottom front clear, this wont cause any issues once the bottom is attached.
Step 5: Attach the Panels
To attach the top and bottom I marked out where I wanted the screws to be, then pre-drilled clearance holes, three on each side and used a larger drill bit to increase the size of the top of the hole so the screw will sit flush with the MDF. The same can be done if you have a counter-sinking bit.
A huge note here, MDF likes to blow out on the back side when drilling. I placed the pieces on two cut offs of the furring strips and drilled into those cutoffs to keep the back of the MDF in good shape.
I did the same for the side panels, pre-drilling the Masonite is optional but it gives a cleaner look.
To attach the panels just place them on and put the screws in. with the panels added the frame should be fairly ridged.
Step 6: Install the Printer
With the assembly done I put the enclosure in place and put the printer inside. I added a few upgrades to my printer to make it fit better, including the front skirts, an under mount front electronics enclosure, and on the back, an under-mount PSU mod. These reduce the overall footprint of the printer and make it fit better.
I also drilled a small hole on the top of the enclosure and put my filament roller up there.
Now plug it all back in and give it a test.
Step 7: Conclusion
I’m pretty happy with how this turned out. I do have a few upgrades planed for it to really work as well as I want. I’ve listed them below.
- Doors
- Lights
- Air filter
- Rpi Camera mount
I plan to keep working on this enclosure and will post updates on Instagram and YouTube. So go check out those platforms as well.
If you would like to support me you can do so here
Thanks for stopping by!
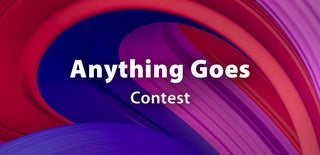
Participated in the
Anything Goes Contest