Introduction: Building a 40 Ton Hydraulic Press Brake Machine
There is no way around it. If you're looking to make clean bends in steel plate, you're going to need a good press brake.
There are a lot of press brake varieties out there. Depending on features, these machines can get pricey (upwards of tens of thousands!). If you're in the market for one, but don't want to shell out the bucks for it, why not make it yourself!? Sounds intimidating right? Where should you start? How big of a press brake do you really need?
To help answer those questions and more, here are the steps I took to build my own hydraulic press brake.
Step 1: Understanding Press Brake Basics
Before you begin, it's good to have a basic understanding of how these machines operate.
What does a Press Brake do? It allows you to make bends in sheet metal and in thicker steel plate.
There is nothing overly scientific about how a press brake works. Attached is a sketch showing the main components along with some details below:
- Main frame - the core of your machine. In essence, this is nothing more than a rectangle made from some beefy materials. Due to the size of mine, I added some legs and wheels. If yours is small enough, you can leave it as a table top version.
- Lower bending die - also referred to as the "v die." The work piece will get pressed into the "v die" to create a bend
- Upper bending die - also referred to as the bending blade. The bending blade will press down across the top of the work piece and force the material into the "v die."
- Bending blade assembly (as I call it) - this is simply the assembly that holds your upper bending die. It needs to be pretty beefy to resist deformation when making a bend
- Hydraulic jacks - the muscle behind your machine. These generate the force required to make the bends. I have two jacks on my machine but based on your required machine capacity, you might only need one.
- Return springs - these springs will pull the bending blade assembly back upwards after a bend is completed. The springs need to have enough force to lift the weight of your bending blade assembly.
Keep in mind, there are other versions out there that operate differently. This particular style was best suited to my needs.
Step 2: Where Should You Start?
First, ask yourself this: What is the maximum thickness and width of steel you envision yourself needing to bend?
The answer to that question will help drive the rest of your build.
For me, I needed to bend 3/16 inch thick steel in a 4 foot wide section. This resulted in a pretty large machine.
No matter how large or small of a machine you need, you can apply these same process steps to build your own press brake.
Step 3: Determining How Much Force Your Press Brake Needs
Attached is a press brake capacity chart for plain steel. If you'll be working with other materials like stainless or aluminum, you can easily find charts for those online. The left hand side of the chart has options for steel thickness. The top of the chart has options for "v die opening" size (refer to the illustration shown on the chart for a better understanding). The middle of the chart shows force in tons per linear foot.
How do you use this chart? Lets say for example that the max thickness and width you anticipate needing to bend is 10 gauge steel that is 2 feet wide. Take a look at the left hand side of the chart and find '10 gauge.' Now take a look at the top of the chart and select a 'v die opening' size (a typical v die size for 10 gauge steel is 1.25 inches). Now look at the center portion of the chart and see where those two selections intersect. The chart shows that 7.3 tons per linear foot is required to make this bend. Since you need to bend a 2 foot width, you will need 14.6 tons of force.
How big of a press brake do you need? In this example, you would need a 2 foot wide press brake capable of generating at least 14.6 tons of pressure. With this information, you can now start designing your own machine.
Step 4: Designing Your Press Brake
This is the most important part of the entire process - plan the work, and work the plan.
First, consider what tools and equipment you have available to help you with this build. I have a wide variety of fabrication machinery in my personal shop. Don't worry, you don't need this level of machinery to build your own press brake. However, the equipment you have at your disposal may impact your design. For example, I have a milling machine that I used to mill my upper bending dies. If you don't have one, you can make a bending die out of angle iron and flat bar or even buy a commercially available bending die and adapt it to your design.
Attached are some sketches showing my press brake design. Autocad and Fusion 360 are great options for CAD modeling. If you're more comfortable with hand sketches, those work just fine as well. The important part is to ensure you consider and plan all details big and small.
A few notable features of my design:
- 40 ton and 63 inch capacity - this was driven by my need to bend 4 feet of 3/16 inch thick steel
- Adjustable hydraulic jack locations - jacks slide side-to-side for optimal positioning dependent on work piece thickness and width - if your press is 2 feet wide or less and you're using a single jack, this adjust-ability isn't necessary
- Spring compensated and adjustable gauge rods on both sides allow for consistent and accurate repeat bends. The compression springs prevent damage to the gauge system in the event that the stop point is accidentally exceeded - you can also use two rulers mounted on either side of the machine as an alternative
- Bending blade, main bending bar, and bottom die assemblies built from cold rolled 1018 for a typically higher material hardness than the work piece - I've seen several folks build their presses with plain carbon steel dies with no issues
- Adjustable width bottom die assembly using two 1.5 inch diameter cold rolled solid round rods - using two round rods is a good way to have an adjustable width bottom die
- Bending blade will be cut into fingers to allow for box and pan bending operations - a nice feature to have but not necessary for everyone
- Hydraulic jacks plumbed together for simultaneous operation but can also be operated individually for level adjustment - this is a must when using two jacks on your machine
- Adaptable, adjustable, modular, and easily repairable design utilizing minimal welding of components onto the main frame - facilitates easier modifications and repairs going forward
What size of materials do you need to use? Without getting too deep into engineering calculations, you can simply look up similar size machines online and see what materials other folks used to make theirs. General rule of thumb: if you think it might bend, throw more steel at it!
Step 5: Procuring Your Materials
With your design set, it's a good idea to generate a full list of all materials you'll need. The more detail the better - even breaking it down into the specific material types and lengths that you'll need to cut out. You can then procure all of your materials and parts at one time - I like to have all parts on hand before I start a build.
Here are the materials and parts I used for my machine:
- 4 x 6 x 1/4 inch rectangular tube - for the main frame
- 2 x 3 x 3/16 inch rectangular tube - for trusses and bracing
- 5 inch x 6.7lb/ft c-channel - for the upper horizontal beam of the main frame and the lower bending die
- 3 x 3 x 1/8 inch square tube - for lower bracing
- 2 x 2 x 1/8 inch square tube - for lower bracing
- 2 x 6 x 3/16 rectangular tube - for the base of the machine
- 4 x 1/2 inch flat bar - for the main frame
- 5 x 1/2 inch flat bar - for the bending blade assembly
- 4 x 3/4 inch cold drawn 1018 flat bar - for the upper bending die
- 1.5 inch cold rolled 1018 solid round rod - for the lower bending die
- Various parts cut from 1/8 inch and 1/4 inch steel plate
- Various lengths of 1/2 inch threaded rod and bolts + nuts
- 186 pound capacity extension springs
- 20 ton air over hydraulic jacks - I chose air over hydraulic jacks for the convenience of operation. These are hydraulic jacks that function on air pressure as opposed to pumping a handle.
- 4 inch steel casters
Step 6: Cutting Parts for the Main Frame
This is the classic measure twice cut once stage.
Using your detailed design and parts list, work your way through all the parts necessary for the main frame. At this stage, I suggest cutting out parts for the main frame only. All other parts can be cut out later just in case you encounter issues with the main frame that drive changes to the overall design.
In the photos shown here, I'm cutting out the required lengths of rectangular tube and c-channel using my abrasive chop saw. I also started welding together some of the sub-assemblies for the main frame.
Step 7: Assembling the Main Frame - Establish a Work Surface
After cutting out all parts for your main frame, you'll want to ensure you have a flat and level surface available for assembly. If you have a welding fixture table, even better. I used a sheet of 1/4 inch steel plate with some rectangular tubes and shims to create a level surface.
Step 8: Assembling the Main Frame - Start With a Datum
Once you've established your work surface, the best place to start is the area of the main frame where your lower bending die will sit. Once this part is square and true, you can use it as a datum to build the rest of your frame.
Some tips for this stage:
- Take your time and ensure your parts are positioned properly and securely fastened before you weld
- Be conscious of where you place your welds to avoid the need for grinding or cutting later down the line
- Watch for material deformation due to heat from welding - symmetrically applied welds will help to keep things straight
- No need for full welds at this stage. Just tack things together but ensure the tacks are substantial enough to keep your parts stable.
My welding machine:
- I'm using a 210 amp welder with 75/25 Argon/CO2 shielding gas and .035 solid MIG wire for all welds
Step 9: Assembling the Main Frame - Adding Bracing and Trusses
Once the core of your frame is securely tacked together, you can begin adding the bracing and trusses. If you're making a smaller capacity press, this level of bracing and truss work might not be necessary.
Once all of your braces and trusses are tacked in place and you've confirmed that everything is true and square, you can begin fully welding your seems. Keep in mind, symmetrically placed and evenly spaced welds will help to minimize heat distortion.
Step 10: Assembling the Main Frame - Final Welding
At this stage, your partially welded frame should be rigid enough to pick up off the work surface so you can fully weld all remaining seems. Due to the size of my machine, a forklift was a must. Smaller presses can easily be handled by an engine hoist or even by hand for tabletop versions.
Continue to use symmetrical and evenly spaced welds to reduce heat distortion.
Step 11: Inspecting the Completed Frame
Now that your main frame is complete, take some time to measure and check it against your original design. You'll want to ensure that the frame is straight and square throughout. If any adjustment or modifications are needed, now is the time to make them.
Step 12: Fabricating the Remaining Parts
You can now set your main frame aside and concentrate on the remaining parts and pieces.
I used 1/4 inch thick plate for most of my parts but your material will vary dependent on the capacity of your press.
My CNC plasma cutter allowed me to efficiently incorporate unique shapes and features. However, fabricating parts that serve the exact same function is easy to do with standard fabrication tools (chop saws / drill presses / grinders), you'll just have to account for this during the design phase as previously mentioned.
Here is a breakdown of the various parts for my machine:
- Vertical guides for the bending blade assembly - qty 2 of these keep the bending blade vertical and stable while it is forced down by the hydraulic jacks. I designed mine to clamp around the main frame.
- Spring supports - qty 4 upper and 4 lower supports help secure the extension springs to the main frame and to the bending blade assembly
- Load spreader plates - qty 4 of these cut from 1/2 inch thick material help to distribute the load at the top and bottom of my hydraulic jacks.
- Jack retaining plates - qty 4 of these interlock around the top pad of my hydraulic jacks. These plates, along with some additional hardware, help to "hang" my jacks from the top I-beam on the main frame. My jacks can slide side-to-side for optimal positioning dependent on work piece thickness and width.
Step 13: Fabricating the Lower Die
I built my dies out of cold rolled 1018 which has a slightly higher material hardness than plain steel. However, I've seen several folks build their own dies using plain steel with no issues.
My lower die is made out of 5 inch c-channel and 1.5 inch diameter solid round rod. The rods sit inside the c-channel and shims are used to adjust the distance between the rods. Other common options are to make a bottom die out of angle iron, machine one out of solid stock, or buy a commercially available die and adapt it to your machine.
Step 14: Fabricating the Bending Blade Assembly
This is the component that holds my upper die. I built this assembly out of .75 x 4 inch cold rolled flat bar and .5 x 5 inch hot rolled flat bar. Evenly spaced 1/2 inch bolts tie all three pieces together. Holes were drilled using my milling machine. This bending blade assembly alone weighs approximately 300 pounds
I designed this assembly for easy and efficient installation and removal of the bending blade dies. I simply loosen the bolts with an electric wrench and the bending blade sections will drop out
Step 15: Machining the Bending Blade
My upper die (aka bending blade) is made out of .75 inch thick by 4 inch wide flat bar. I used my milling machine to create the angle on the blade. You could also make your blade out of angle iron if you don't have access to a mill. A third option is to buy a commercially available die and adapt your machine to accept it.
How I determined my blade angle: See the attached cross sectional sketch. Based on geometry, the minimum achievable blade angle is 47.26 degrees at which point the work piece would start to clash with the bending blade assembly. Thus, I set my mill to machine a 24 degree angle on both sides of the blade.
I will subsequently cut the blade into smaller "fingers" which will allow me to perform box and pan bending operations.
Step 16: Inspecting All Components Prior to Final Assembly
I now have a main frame, all loose parts, and both lower and upper die assemblies fully complete. Prior to assembling everything together, it is prudent to do a quick inspection of all components to ensure everything is sufficiently welded and built per your design specifications.
Step 17: Final Assembly
The best part of any build - final assembly.
Some tips for this stage:
- Safety precautions, especially if you're building a machine as large as mine, are critical. These are heavy components that can cause serious injury
- Think through each stage of assembly and ensure you are progressing in a safe manner
- Use wooden blocks or other means of support to keep gravity on your side
My assembly process:
- bottom die - this simply lays over the frame
- bending blade vertical guides - these clamp around the frame (one on each side of the machine)
- bending blade assembly - this is suspended using four extension springs. I used wooden blocks to help support the assembly before getting the springs attached
- hydraulic jacks and spreader plates - these jacks hang from the upper I-beam. They also have lower mounting plates that slide on the bending blade assembly for side-to-side adjustment
- bending blade (AKA upper dies) - these simply slide up into a retaining slot and are cinched in place by tightening the bolts along the bending blade assembly
Step 18: Adding a Gauge System
Commercially available press brakes typically have a couple key features:
- You can set the machine to stop at a specific bend angle or fixed angle dies are used to generate repeatable specific bends
- The bending blade will remain level as it lowers during a bend - this is usually accomplished through electronic feedback control systems that monitor levelness of the blade or through the use of a torsion tube that mechanically keeps the blade level
My particular machine has neither of those features. Instead, I incorporated the following:
- In order to generate consistent repeat bends, I designed a spring compensated gauge rod system. This is a mechanical system that allows me to set a stop point for the blade assembly. Compression springs prevent damage in case the stop point is accidentally exceeded. See attached photos for more information. The adjustable nut on the lowest portion of the threaded rod serves as my stop point.
- I use a bubble level mounted on the bending blade to monitor levelness. It is also quite easy to check the levelness of the blade against the bottom die with your eyes only.
Check out the video above to see the gauge system in action!
Step 19: The Completed Machine
Here are a few photos of the completed machine. I have plans to add a material support bar for the front and an adjustable back gauge on the rear but that will have to wait until later.
Check out the next step for pics and videos of the machine operating
Step 20: Test Bends
Control wise, I have both hydraulic jacks plumbed together with identical couplers and hose lengths. There is a single 1/4 turn valve located upstream of the factory triggers for both jacks.
I can operate the machine in two ways:
- Lock the factory air supply triggers open and use the 1/4 turn valve to operate both jacks simultaneously
- Open the 1/4 turn valve and operate both jacks individually using their factory air supply triggers
Check out the video above to see the machine in action!
Step 21: Summary
I spent approximately 2 weeks designing and 1.5 weeks physically building my press brake. Total cost was around $1,000 for all of the materials and parts (purchasing a commercially available machine of the same capacity would cost me upwards of $10,000!). Total machine weight is around 1200 pounds.
Thanks for checking out my build and I hope this provided useful information for your own press brake project!
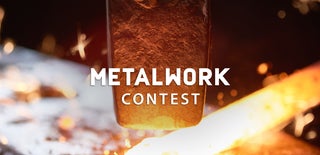
First Prize in the
Metalworking Contest