Introduction: Building a Solar System for Pumping, Agricultural Irrigation and Stock Watering, 27 Steps
Solar pump systems can be constructed at any scale from a backyard pond to broad acre irrigation. This Instructable demonstrates how to construct a multipurpose solar pump system that enables water transfer to storage from a creek, irrigation of 5Ha from a creek or the dam and providing drinking water to stock from the dam, bore or creek.
This Instructable is designed to allow you to scale up or down as required. It is detailed and comprehensive- the go to resource for EVERYTHING you need to know to design, build, commission, operate and maintain your own Solar Pumping System- from 1kW to hundreds of kilowatts in scale.
As such its is very large and long Instructable as it covers a significant, expensive and complicated project in detail. It includes everything you need to understand solar energy, pumping systems and irrigation. Using this you will be able to design and build (or manage) the construction of your own large scale solar irrigation system. You may simply want to refer to sections, so I have included a table of contents as the first step to help you navigate the material.
The system I demonstrate utilizes a lot of used and recycled items in order to keep the costs down to less than half the price that all new construction would cost (ie AUD$30,000 DIY V's AUD$70,000). Which is terrific value for a 10kW solar system. The pump has a maximum head of 100m and maximum flow of 9m3/hr.
Solar pumping has significant benefits over the diesel pumping we used to do:
1) The energy is free; We would never have considered pumping from the creek to storage in a dam before due to the cost of diesel. Now we can capture water during high creek flow periods and store it for dry spells, improving our resilience to drought. Much like storing fodder.
2) Operation and maintenance is simple; Pretty much set and forget, the system turns on when there is enough sunlight and switches off when it is too dark. We no longer need to worry about topping up diesel, changing engine oil, fuel filters, oil filters, etc.
3) It is clean and silent; No more complaints from neighbors about the droning diesel pump, wildlife is not disturbed and there is no risk of diesel or oil spills in the creek.
4) It is lightweight; the submersible electric pump weighs under 30kg and replaces an equivalent diesel pump weighing over 100kg.
5) It is flexible; We can move the submersible pump between 3 water sources, the creek , the dam and the bore (or well as it is called in the USA). While the diesel pump could work on the dam and the creek, there was no way it could pump out of the bore
This Instructable will take you through the whole process from site selection and concept design to commissioning and operating a solar pump system. You should be able to build your own system of any size by copying the methods of this Instructable.
I would like to pay special thanks and acknowledgement to the National Landcare Program: Agriculture Smart Farms Grants – an Australian Government initiative, their support made it possible to create this Instructable for you, the Australian Farmer.
They have also made possible a field day for you to come and inspect my system in person, see Step 28.
This Instructable has been written for Australian conditions, using Australian Dollar costs in 2020 and System Internationale (SI) units. If using it in any other part of the world you will need to adjust for your location, unit system and currency.
Supplies
Given that your system will be different to mine, I will just briefly cover the major components here. This Instructable will cover each of these parts in much more detail.
Solar Panels- New or used, power output must be at least equal to the pump demand, ideally 4x greater than what the pump needs.
Solar panel mounting- Typically a groundmount or a structure such as a shed to mount the panels on. Standard panels are typically 1.6m2 in area so every 10 panels will require 16m2. You will need footings for this structure, typically screw piers or concrete
Solar inverter/controller- Choose between DC and AC operation, there are suppliers of both types of equipment
Grid integration- You may want to have backup power supplied from the electricity grid, in which case you will need cabling and maybe a transformer
Batteries- If you want to be able to run at night or on significantly overcast days you will need batteries (I chose to operate without batteries)
Pump- needs to be suitable for operation with your chosen inverter/controller
Control equipment- You will need pressure switches, flow switches, pressure tanks and valves to control your system
Fencing- If you run livestock you will need to keep them away from the solar array and equipment as they will just love to scratch their itches on this gear.
Cabling- Electrical cables need to be installed to connect the solar panels to the controller/inverter and then to the pump
Piping- Pipes have to be installed to transport the water from where your pump is to where you need the water
Multimeter (clamp meter)- This is perhaps the one must have tool for this job with the ability to measure both AC and DC voltage and current
NOTE:All systems must be built and operated in a way that complies with all applicable state and Commonwealth laws and regulations, including WHS laws and any of those relating to the construction and maintenance of solar powered systems and/or the conduct and maintenance of electrical work.
Step 1: Contents of This Instructable
This is a long Instructable and you may want to refer to just parts of it, so this step gives you the contents for quick reference:
Step 2- Why Go Solar
Step 3- Drought, Fires and Flood
Step 4- Choosing Solar, V's Diesel, V's Grid Electricity
Step 5- Batteries or Not and Hybrid
Step 6- Irrigator Selection and Sizing
Step 7- Storage Options
Step 8- Site Survey
Step 9- Existing Infrastructure and Integration
Step 10- Different Pump Types Explained
Step 11- Sizing the Pump
Step 12- Solar Array Sizing and Location
Step 13- Solar Array Technicalities and How to Choose Panels
Step 14- Designing Strings of Panels
Step 15- Roof Mount or Ground Mount
Step 16- Ground Mount Foundations and Weed Management
Step 17- Ground Mount Frames and Assembly
Step 18- A Short Note on Fencing
Step 19- Installing Solar Rails and Panels
Step 20- Wiring the System
Step 21- Control System and Valving
Step 22- Testing and Commissioning
Step 23- Pontoons, Jetties and Flying Foxes- Getting Your Pump in the Water
Step 24- Risks: Fire, Flood, Lightning and What Can go Wrong
Step 25- System Operation and Maintenance
Step 26- Costs and Benefits
Step 27- Environmental Benefits
Step 28- Field Day Invite
Step 2: Why Go Solar?
Like many farmers the idea of solar pumping interested me, the idea of not having to pay for the diesel or electricity to move water is very attractive. But when I started to look into solar it seemed to come with a big upfront cost for the solar panels. Given I was irrigating for typically around 500 hours per year at a cost of around $1000 for fuel and maintenance spending $70,000 on a solar system seemed uneconomic
Time has had a big impact on the cost though. While panels have not come down in price per panel, they have got much more powerful- Now in 2020 you can buy a 330W panel for the same as a 185W panel cost back in 2010, so in reality the cost ($/Watt) is approaching half the cost of a decade ago. This is likely to continue as new technologies emerge to make solar panels cheaper.
Another big change is that solar panels are now readily available second hand, people are upgrading old systems and fully replacing them with new. Often these panels are only 5-10 years old and usually come with guarantees of 20-25 years. They can often be bought for $30-$50 per panel or less, especially when you buy a lot at once.
So I was able to build my system for around half what I originally anticipated by using used panels and parts for the mounting. Still, around $30,000 to save $1,000 per year does not seem a great investment at a mere 3.3% return on investment. The big benefit came with the realization that the more I use my solar pump the better the payback.
I have a 25ML dam that was nearly emptied by the drought from 2017-2020. It has a small catchment area of about 8Ha in a region with average 1200mm/year rainfall, the dam does have a spring which opens during wet periods. Given the limited runoff and evaporation losses it is difficult to fill this dam from empty in an average year- the dam normally only fills during flood events and holds capacity during average years.
I now use the solar pump to lift water from the creek while it is flowing and put it into the dam, we are located about 2.5km upstream of where the water becomes tidal and brackish. Typically we have summer dominant rainfall and a need for irrigation during dry winter and spring periods- given average conditions I can use solar for about 2600hrs per year, so up to 2100 hours lifting water to storage and 500 hours irrigation. This is almost enough to fill the dam using water that would otherwise be wasted. 2600hrs of operation using diesel pumping would cost about $7,500 so if I use the solar pump all the time it has a return on investment of 27%!
It is unlikely that I'll ever need to pump like this, as the dam will fill from catchment only eventually, but this allows me to keep the dam topped up during normal seasons and be better prepared at the onset of droughts- like having a full shed of hay all the time. Also there are often short, sharp storms during dry spells- given dry ground there may be little runoff into the dam, I can now take advantage of these events when the creek flows and pump water into storage when most needed.
So this system is helping my farm to adapt to increasing climate variability. Here on the North Coast of NSW we are to expect shorter, higher intensity rainfall events with longer dry periods in between. Having reliable access to water for stock and irrigation is essential for a sustainable farming operation.
The dam I have was built in the 1970's and it is low down on the property near the creek- about 4m above creek level. If I were to be building a dam for this system I would construct it as a Turkey Nest at the highest point on the property- that way I would be pumping water to the dam using solar, but then gravity feeding to irrigation. This enables irrigation at any time - day or night regardless of whether it is cloudy or clear.
If you are like me and have existing infrastructure such as dams, underground irrigation mains and stock watering points, you will need to think about how to integrate the solar pump with this. Every farm is different and this will be for you to figure out. I'll give my example of how I integrated the solar system and hopefully you will get some ideas of how to do it on your farm.
Solar pumping has other benefits as well. The noise from diesel pumping is often an irritant to neighbours, solar pumps are near silent and definitely unnoticeable from more than a few meters away. The only noise being a slight hum at the inverter/controller and noise of water passing through valves and the irrigator. So going solar has improved our social license to operate. Wildlife also benefits, especially bats that use echo location- noisy diesel engines operating at night can affect them along large lengths of waterway.
CO2 emissions are reduced- every litre of diesel burned produces 2.6kg of CO2. 2600 hours of operation would produce 6.8 Tonnes of CO2 emissions, this is roughly equal to the annual emissions from 2 cars.
With diesel we had to refuel every 2 days and change oil every 100 hours of operation, aside from the time and inconvenience there were occasionally spills. By going solar we eliminated all risk of fuel/oil spills into the waterway.
Also to get the heavy diesel pump to the creek we used an access track that had been cut into the side many years ago to enable a tractor mounted PTO pump to be operated at the creek. This was eroding badly and we were losing farmland in every flood. The solar pump is so light and easy to handle we can just lower it into the creek from a flying fox and have been able to stabilise and re-vegetate this old erosion.
In summary going solar delivers a lot of benefits- the most significant of which is giving you additional security against drought. There are very few risks with it provided you design and build it right. Design and construction is the biggest risk for you right now and I would like to think this Instructable provides all the guidance you need to remove that risk and helps you build a robust and economic solar pumping system.
Step 3: Drought, Fires and Flood
Farming is a challenging business, it is rare that we have a Goldilocks moment when everything is just right and you as the farmer can sit back and just enjoy life. We must always think and plan ahead for the next season and the one after, whether it is getting animals to spec for market, ensuring there is pasture for them to graze, getting fodder preserved or planning a crop. All of this depends on what the weather is doing now and will do in the future. The first thing I do every day is look at the weather forecast for today and the rest of the week, my plans change as the weather changes.
The weather works in cycles- we all know the seasons and what to generally expect. But overlaid on the seasons are longer and shorter natural cycles. For Australia we have the El Nino, La Nina and Indian Ocean Dipole (IOD)- these last for several seasons and influence wetter or drier periods depending on their phase. We also have The Southern Annular Mode (SAM) which acts quickly over a couple of weeks and last year a rare one; Sudden Stratospheric Warming. Some are reasonably predictable such as the Australasian Monsoon and others are very random such as East Coast Lows. I can strongly recommend DPI's climate dogs for more on this topic.
https://www.dpi.nsw.gov.au/climate-and-emergencies...
These cycles seem to be changing, they seem to be getting stronger and more frequent. We have just endured the worst drought since records began, and only in 2013 we had "yet another " 1 in 50 year flood. Regularly temperature records have been broken. All of this is making it harder to farm, so during this most recent drought I decided to prepare for the next one by building this solar pumping system. The big benefit would be to secure water supplies for the farm, by pumping water from the creek to the dam when there is water available and saving it for the dry times ahead, it is just like making hay or silage and putting it away for the winter.
The NSW government has an excellent report outlining what we can expect from our climate in the years ahead:
https://climatechange.environment.nsw.gov.au/Clima...
These are the projections as of now, 2020. They will probably change as time goes on and my apologies if the link stops working at some time as I suspect the host site may change too. So I'll provide a short summary or the forecast changes for the North Coast of NSW- these influenced my decision to build this pump system:
Rainfall: Currently significant variability between seasons with summer dominant. Winter rainfall is expected to DECREASE. Autumn and Spring rainfall is expected to INCREASE.
Temperature: Maximum and minimum temperature expected to increase by 0.4-2.4C with an increase in the number of hot days (above 35C) and decrease in cold nights (below 2C).
Fire weather: Severe and average fire danger weather is expected to Increase.
Considering these future changes there is some good- increased autumn rains gives me a better chance to get my winter pastures sown, increased spring rains will ease the transition from winter pasture (C3 grasses) to summer active tropical grasses (C4 grasses). But the downside is that less winter rain occurs at what is a traditionally dry period for us, so less rain then will increase the need for irrigation to keep the winter pastures growing. Harvesting water from active flows during spring-autumn for use in winter makes even greater sense.
Increased temperatures (along with increased autumn rain) keep the C4 grasses more active into autumn. This will likely delay the oversowing date of winter pastures into C4 pasture, it will also affect the number of frost days and when they occur. This can be a benefit in prolonging the C4 growing period. But this comes at the cost of increased evaporation of water from storages as well as drying out of soils. Again having more water stored to compensate for these losses makes good sense.
Increased fire weather is a problem, we live in a fire prone area, dry winters will see a lot more dry grasses and risk of pasture loss (and perhaps asset losses) to wildfires. Having a good water supply is some benefit as irrigated land is unlikely to be affected and there is some small extra security for asset protection.
Step 4: Choosing Solar V's Diesel V's Grid Electricity
Grid supplied electricity is much cheaper than diesel for pumping. We currently pay AUD$0.30 per kWh for grid electricity so a 2.2kW electric pump costs $0.66 per hour to run and has very little maintenance. An equivalent diesel pump is 3.5kW (larger due to less motor efficiency than electric) and uses about 1L of diesel per hour. Diesel is currently much cheaper than during the last several years at $1.30/L but has averaged $1.50/L for the last 5 years. The diesel pump requires a lot of maintenance- oil changes and oil filters, fuel and air filters, valve gap adjustment, ring replacements, etc so it works out to $2.67 per hour of use. But the pump itself only costs $3,100 to buy.
The problem with grid supplied electricity is having it where you need it. In my case there is an authority pole placed within 10m of the hole that I pump out of in the creek. Absolutely ideal for providing grid electricity. I inquired as to installing a new transformer and was told "at least $40,000 to put it up and then you have to have meters and switchboard". So my quick conclusion was that if power is not available already on site then new connections are just too expensive.
I could trench power in from my existing transformer- 700m away. This is more affordable at around $20,000, but again is a large amount of capital to allocate just to get power where you need it, the electric pump itself would then cost about $2,700 on top and then there would a a few thousand for switchboards, piping, etc. Say $26,000 for a fully installed system.
So I had another look at solar and decided I could fully install a system for between $25,000 and $30,000, if I was careful to use as much second hand gear and my own labour as far as possible. The PDF document attached to this step shows the comparison between the three options. (This is a simple version- a more detailed cost/benefit analysis is at Step 26)
I have assumed a life of 20 years for each system and I have not escalated prices through the period so that I have a simple comparison of each option. For 400 hours of irrigation only all systems are similar. Diesel looks to be the cheapest by about $6,000, but on the risk side I doubt a small diesel pump will last 20 years. I would probably need to spend another $3100 replacing it after 10 years. The diesel pump is also labour intensive requiring refueling and maintenance and the noise annoys the neighbors. Given these factors I would reject it for irrigation and consider the other two options.
The grid electric pump is only slightly more expensive than the solar pump but has the advantage of being available pretty much any time day or night and all up the system is very simple. So if I were irrigating only then I would probably chose the grid electric version.
Now consider the idea of lifting water to storage- I have assumed 1500 hours as a standalone (This could also be 1500 hours of irrigation in your situation). In this solar is a straight out winner being 2.5x less expensive than diesel and 1.5x less expensive than grid electricity.
Go further with combined irrigation and water capture and the figures are even more convincing, solar is 3.5x cheaper than diesel and 1.7x cheaper than grid electric.
The choice for solar became clear when I figured that the system is to do everything- it is to irrigate, lift water to the dam and give me a backup for providing stock watering. This decision is completely scalable whether you are after 2kw, 20kw or 200kW of pumping capacity, the simple principle is that the greater the operating hours, the more economic solar becomes. Scaling of cost estimates is covered in detail at step 27 Costs and Benefits.
Attachments
Step 5: Batteries or Not and Hybrid
Recently in Australia at least there has been a shift towards the installation of batteries with grid connected solar systems in houses. The economics stack up in many cases, especially when security from grid failure is necessary. Having battery backed solar is like an automatic backup generator in these cases.
For irrigation the case is somewhat more marginal. The key benefit is being able to irrigate at night. Usually winds drop off at night and evaporation losses are less so irrigating over night is better than during the day. The cost however is hard to justify.
In my case the pump is 2.2kW, let us say we want 10 hours of overnight irrigation, this would require 22kWh of battery capacity. With modern Lithium Ion batteries the capacity of the battery needs to be just slightly above the demand- so for 22kWh of demand about 25kWh of capacity would be necessary. Batteries of this capacity would currently cost between AUD$30,000-$40,000 which includes allowance for a charge controller inverter.
Using conventional lead acid batteries there is a limit on the depth of discharge. What this means is that if more than 20% of the batteries capacity is regularly used then the battery life is significantly reduced. So the installed capacity for lead acid would need to be 22x5= 110kWh. These would cost around $25,000-$35,000 including allowance for a charge controller inverter. Batteries have a limited life of charge cycles- 10 to 20 years of use is about all that can be expected from any of them.
In either case it is safe to assume that adding batteries doubles the solar system cost from around $30,000 to $60,000. This makes installing a grid connected pump much more sensible- It can pump day or night and does not have batteries that will need to be replaced.
Whilst I support reuse of many materials, reusing old batteries in an irrigation system is high risk. Old batteries are often removed from places such as data centres and emergency backups and can be purchased for near scrap prices- but they are near end of life and will not have many cycles left in them. Good perhaps for emergency backup to a farm house, but for a pump running every night they are unlikely to last long. You never know though, you may get lucky and find some very cheap but very good used batteries.
In my system I elected to go without batteries, the loss of ability to irrigate at night is offset by the cost savings for pumping through the day only. It also limits the amount of water I can transfer to storage- but this is not a huge issue as I have sized the system to deliver enough water during daylight hours.
Finally, there is one more system to consider- a grid/solar hybrid. If you are fortunate enough to have a nearby grid connection then you could consider hybridising the system with solar. This would require a setup much like a house with a grid connect inverter. Whilst you are pumping in the day the system runs on solar and at night on grid. If you are not pumping during the day or have surplus power you may be able to sell this back to the supplier to offset the cost of your nighttime usage.
Step 6: Irrigator Selection and Sizing
In New South Wales legislation is in place requiring agricultural irrigators to have both a licence to irrigate and a water allocation. The rules vary a little across catchments and water sources are also defined as surface or subsurface. Other states and territories have their own regulations, so ensure that you have applied for or hold the appropriate licences and permits before commencing agricultural irrigation.
The NSW legislation allows use of surface water for stock watering and domestic applications (eg water troughs, vegetable patch, lawn, home, etc) without any special permit. Bores require a permit to construct, having your bore approved for domestic and stock watering is relatively simple. It is somewhat more onerous to have it permitted for irrigation.
Sizing your solar system starts by choosing your irrigator- the pump must be capable of driving this at a minimum. For me I had an existing Trailco T50 Traveling (self propelled) irrigator with impact sprinkle and it is not economic for me to replace this unit.
http://www.trailco.com.au/Brochures/t50Brochure.pd...
With this unit I can irrigate up to 5Ha of pasture, but more reliably 3Ha. This is small scale for farming irrigators, but everything in this Instructable is scalable to whatever size you need.
I get from it a wetted width of about 35m delivering 25mm in a pass, taking about 14 hours to travel 100m- or about .025Ha/hr of irrigation. I have used it's bigger brother the T100 but it is only marginally better coverage, with the downside that it is considerably more heavy.
There are a huge range of irrigators to choose from. In this step I'll help you choose the type that is right for you. You need to start with how much area you want to irrigate per day and with how much water, this gives you the basic machine sizing. The nest step is choosing the type- this is discussed later in this step.
Sizing the Irrigator:
The area to be irrigated has the biggest impact on your system sizing. Using my example of 3Ha (30,000m2) to be irrigated, I want 25mm equivalent precipitation. Ideally I would like that over the entire pasture in one pass (eg overnight) but this would require 30,000m2 x .025m precipitation = 750m3 of water in 10 hours, each 1m3 of water =1000L so that is 750,000L in 10 hours or 75,000L/hr requiring around 20-30kW of pumping power. This figure is entirely reasonable and normal for larger farms, but is way too much for me as the system cost is outside my budget.
When I chose the little T50 many years ago I based it on covering about 1Ha per week, the maximum performance it is rated to is 1.54L/s (1.54 x 3600 seconds per hour = 5544 L/hr or 5.5m3/hr) with a wetted width of 40m delivering 30.2mm of precipitation when traveling at 7m/hr. I could speed this up a little and get just 25mm precipitation, but for design it is better to be conservative. The power required for this system is in the order of 2.3kW (I'll cover power calculation a little later) and this is much more within my budget.
I also know from experience that the application is not uniform across the 40m width due to wind and the way the jets work, so I allow about 35m effective width as I overlap each run to make up for poorly wetted edges. The unit also does not maintain constant speed- it is fast when it starts but as it drags more hose it slows down, so 7m/hr is just an average.
A typical clear winter day I get enough sun from 8am-4pm to operate a solar system, so 8 hours of run means the irrigator will cover 56m of length (about half a run) per day. 56m x 35m width= 1960m2 irrigated. To irrigate 1Ha will take 10,000/1960= 5.1 days. This is a comfortable margin as I know we get only about 80% clear days through winter, ie 7days per week x 0.8 = 5.6 clear days on average per week, you can get this information from websites such as below:
https://weatherspark.com/y/144604/Average-Weather-...
So I know that the T50 meets my needs for the amount of land I want to irrigate in the timeframe. The driver for 1 week per Ha is that in a dry winter I can return to the beginning after 3 weeks and do another cycle, that gives me adequate irrigation to keep rye or oats growing well. In a wetter winter I can stretch that to 5 weeks per irrigation cycle and cover 5Ha.
Data from this step that will be used in subsequent steps is that my irrigator flow rate is 1.54L/s, 5.5m3/hr
Selecting the Type of Irrigator:
Firstly consider the size of the jet or droplet from the irrigator. Many years ago "Big Gun" impact self propelled (traveling) irrigators were standard- they are big versions of my T50 with large diameter nozzles often around 25mm. These result in large jets of water traveling fast which means the drops hit the ground hard. There are two things that happen when droplets hit the ground, impact and shear. The impact is the vertical force and it tends to compact the soil surface, shear is the force across the surface and causes crusting. Both of these add to run off and longer term soil structural damage. The bigger the droplet and the faster the jet, the bigger these forces.
It is important with these irrigators to run the jets at the recommended pressure, if the pressure drops too low then the jet is not broken up (feathered) properly and exceptionally large drops hit the ground, think of it like washing your driveway with a hose with big droplets washing away muck compared with putting a sprinkler on your lawn and the fine spray that soaks in nicely.
These big gun units have the advantage of being able to cover very large areas and are very flexible to field shape as you shift them and align them to suit the field.
Over the last several years there has been a move away from large droplet sizes and high jet velocities. One approach is to use low pressure sprinklers such as Wobblers- they operate at about half the pressure of impact sprinklers (Typically 1-2 Bar). They can be adapted onto some irrigators (notably boom, pivot and line). I have not seen Wobblers used to replace the impact jet in "Big Gun" irrigators- the Wobbler just does not give the same diameter of coverage.
Low pressure irrigation delivers the same volume of water to the field, but at lower pressure. This saves energy as the power required by a pump is proportional to the pressure multiplied by the water flowrate, halving the pressure with the same flowrate halves the amount of power needed. This is of benefit regardless of the energy source you choose to use.
Rigid line irrigators are still in extensive use and Flexible Line irrigators have gained significant penetration in smaller farms due to their low cost and ease of use- typically these use a poly pipe with a pod at regular intervals holding a sprinkler head. They are shifted by quad bike or tractor. Sizing these units is based on the flow required for each sprinkler head- ie the more and bigger the sprinkler heads, the greater the flow required. You can choose high or low pressure sprinkler heads for these, the only downside of the low pressure units is they have a smaller diameter, but you can consider a longer line to give you the same area per day covered. The limit will be the weight you can shift and your willingness for frequency of shifts.
Drip or micro irrigation has become popular and has been adapted to centre pivot units as well as boom travelers, it has virtually no losses to wind drift and the very small droplet sizes means no soil damage, as such it is very efficient at delivering irrigation water. It also has the benefit of operating at low pressure but the downside of needing good filtration to prevent blockages.
There is one other type of irrigator that is worthy of consideration- they are the low pressure travelers. Typically they operate at around 1.5 bar. Unlike standard travelers that have a central impact sprinkler for the bulk of the wetting and a spinning arm for propulsion, these machines rely on the spinning arm only for both wetting and propulsion. As such the arm is very large- typically 7m or more in diameter.
The low pressure irrigators have the further benefit that they can be easily operated from a water supply fed by gravity. This is a better option than using batteries to provide night irrigation, simply use solar power during the day to pump water to a turkey nest dam elevated on a hillside or large header tank on ground at least 15m higher than where you plan to irrigate. Then use gravity to feed water back down to the irrigator. If I did not have an existing dam and had to build one, this is the approach I would have used.
If I did not have the Trailco T50 and I was buying a new irrigator I would very seriously consider a low pressure unit- such as a flexible line with Wobblers or a low pressure traveler, these nearly halve the energy requirements and cost of the system.
Step 7: Storage Options
I can highly recommend having the ability to store water. Running out of water on a farm is a disaster, it is far more expensive than feed to transport and a tonne of water does not go as far as a tonne of feed. So in principle the more water you can store the better. There are however some rules about this. Here in New South Wales we have a regulation about Maximum Harvestable Rights:
https://www.waternsw.com.au/customer-service/water...
In summary, landowners in the central and eastern divisions of the state can harvest 10% of the average runoff and 100% in the western division. The impact of this is it limits the total dam capacity that you can build on your farm, the limit is based on the land area of your farm and the annual average rainfall. As this varies so much by region you are best to use the calculator at the link above. As an indicator in the North coast region it works out at 5.2ML per 40 Hectares of land.
The ideal location for a dam is one that has some natural catchment but is also elevated above where you are planning to irrigate. If you are using gravity to feed your irrigator then every 1m in height difference is 10kPa. So if you wanted 200kPa then the dam would need to be at least 20m in elevation higher than where you are irrigating.
You need to take note of the height of your dam above the creek or the river as well as the length of pipe necessary to connect the two, the pump will need to be sized to lift the water this height as well as overcome friction in the pipe. This will be covered in detail in subsequent steps.
The soil in which you build your dam is important, sandy soils and red free draining soils do not hold water and your dam will always leak. Clays are the best soil in which to build a dam- the clay expands in contact with water and seals all the micropores. Dam construction is a subject all of it's own, but put simply a hole is dug into the clay- pushing topsoil to the downhill side to form the wall. When the clay is reached it is spread up over the wall of the topsoil and so seals it.
A Tank is another option, but these are much more expensive per unit of water stored. The volume required for most irrigation will mean it is nearly impractical to store more than a few days irrigation water- 400,000L (0.4ML) is pretty much the largest rural tanks. Bigger is available in the Industrial tanks range but the cost is very significant. In general if you are using a header tank like this then you are probably using most of the capacity in each run, at most perhaps having 2 or 3 times the capacity you need per night so that if you have cloudy days your irrigation can proceed uninterrupted.
The ideal location for your tank is the same as for the dam- elevated above the irrigation area.
In my case I have an existing dam built about 50 years ago, it is built down low on the property, almost on level with the irrigated area and within 100m to the creek. It was put here for a few reasons; further up the hill is red soils and they will not hold water, secondly it is in an area that has a lot of ground water coming to the surface- a spring which made it boggy land to work in wet seasons and finally as the best catchment point on a relatively flat farm.
You may well be in the same position as me with existing infrastructure to work with. As I can't use gravity to irrigate from the dam, I designed the solar pump so that it can be shifted from the creek and put in the dam when required. So when there is adequate flow in the creek to support irrigation or filling of the dam I can operate out of the creek and as winter progresses and flows reduce I can take the pump from the creek and place it in the dam to continue irrigating. This is a very cost effective solution with one pump doing both duties.
Step 8: Site Survey
In this step you will work out where to install pipes, the total length of pipe runs and the vertical height that you need to lift the water. An excellent tool to easily calculate horizontal distances on farms in NSW is Six Maps:
This has an easy to use tool to measure both distance and area. Many state governments have a similar tool available. The aerial photography in this step is taken from Six Maps to show the location of my survey and the longest pipe run.
In the absence of such a tool you can use a measuring wheel and walk the distances with it or a GPS (including apps for your smart phone).
I started at the lowest water surface and called this the "Datum" and assigned it a level of 0 (Zero) mm. Using a laser level I measured the height of the bank at the creek, the height of the field to be irrigated and the height of the dam bank. You can see from the survey that I have vertical lifts of 3600mm out of the creek to the field level and 5070mm to get over the dam bank (Technically I only need to lift to the dam surface level as energy is recovered dropping from the dam bank to the surface- but given this is only a meter or two it is insignificant and better to be conservative). I am very fortunate that the lift heights are very small as it makes measurement simple. In lifts that involve many hundreds of meters horizontal and tens of meters vertically you need to break it up into a series of stages equal to the height of your survey staff. This takes quite a bit of time.
You can use a dumpy or automatic level for this too. If the height difference is very significant you may be able to use an altimeter app on your smart phone, but I am reluctant to trust the accuracy of these. For very large projects you may need to engage a surveyor.
Having your lift height defined you move on to working out your longest (worst case) pipe run. This is the pipe run that will use the most energy to pump water through. If you are using an existing system, it may not be your longest length but a shorter run with a small diameter pipe (we'll cover pipe friction losses soon).
I got my horizontal length of 400m direct from Six Maps. It works for me as my ground is very flat. If you are on steep hills you will need to use a measuring wheel or similar as the photographic projection is not accurate.
Data from this step that will be used in following step is my vertical lift is 5.07M and longest pipe run is 400m.
Step 9: Existing Infrastructure and Integration
Most farms will have some water infrastructure in place. The photo in this section shows a rough layout of the 2km plus of buried water mains on my farm (the thin lines). There is an existing electric pump on the dam- marked with a circle, this pump is controlled by pressure switch and has pressure tanks.
The blue marking is the new solar array location and the white line is the new 2"poly pipe to allow the new pump to work from the creek, dam and bore. The bore is located about 8m north of the foot of the dam bank.
The system I have is like a giant figure 8, it ensures that at any irrigation hydrant water is delievered from two directions. This reduces the flow velocity and frictional losses. A ring main in 2" pipe is close to having a single main of about 3"diameter.
At the far ends of the system in some of the stock watering connections there is older pipe rated to 600kPa, but most of the system is more modern 800kPa rating.
This imposes the first restraint, that if I require more than 600kPa for irrigation with the new pump then I'll have to separate the irrigation system from the stock watering system. To achieve this I have installed valves which separate the circuits that the old electric and new solar pump can operate. So when the solar pump is irrigating, the old mains electric pump can do stock watering duty.
As I want to use the solar pump for stock watering at times I can open the valves to reconnect the system and just limit the pressure of the solar pump, using a pressure switch to cut it out below 600kPa to protect the pipes but at a slightly higher pressure than the mains electric pump. The solar pump will then do stock watering through the day and the mains electric through the night. They'll automatically hand over of a morning and evening.
Finally as I want to pump from the creek to the dam, I need to be able to do this without affecting the rest of the system. The biggest issue is that while pressure for this will be around that of stock watering, if I do not have an auto closing valve that shuts off the delivery to the dam when the solar pump stops of an evening, then the electric pump running on pressure switch will cut in and just recirculate water to the dam.
The easiest solution is to again separate the systems with valves- to enable the solar pump circuit direct access to the dam and the mains electric pump to do stock watering duty.
So with carefully placed valves and simple pressure switches the two pumps can be integrated into the one system. Every farm system will be different- depending on needs, geography, scale, etc. You can operate multiple pumps in one system. But to do this you need to think about the pressure and flow of each pump. In general you can use two pumps putting water into the same system at different locations simultaneously, provided that their capabilities are vaguely similar. In this situation they increase the total flow. If the pumps are in series (one after the other) they increase the pressure. But be very careful with this as the water leaving the first pump may over pressurise the second pump.
Step 10: Different Pump Types Explained
There are a huge range of different types of pumps available, entire books cover what is possible in pump design. I'll keep this simple and cover just the common types of pumps used in Agricultural Irrigation.
Pumps fall into two broad categories: Positive Displacement and Rotodynamic.
The difference is quite simple, Positive displacement move a fixed amount of water per shaft rotation, they have enormous pressure capacity- so much that stopping the flow may blow the pump apart immediately. In the simplest form they are a piston pump, just like the pistons in a diesel or petrol engine, but instead of compressing air/fuel they are pushing water.
Rotodynamic have internal clearances and the amount of water moved per revolution depends on the pressure.
Rotodynamic pumps
Rotodynamic have at least one rotor (and often many), the amount of water moved varies with the pressure in the system at a given shaft speed. They are on the whole more forgiving than positive displacement machines, a very brief stopping of flow will generally not hurt them (though is not good practice). I like to think of them as a sling- water comes in the centre of the throwing arm (vane) and as the vane rotates it "throws" it away from the centre.
The most common rotodynamic pumps are single and multistage. A single stage pump is simply one rotor- generally the larger the diameter and wider the vane the more pumping is done at a set shaft speed. Multistage pumps add additional rotors after they first, each stage increases the pressure, but not the flow. Changing shaft speed also changes the pump output- increasing flow with higher speed.
The characteristic of rotodynamic pumps is that as flow increases the pressure decreases.
You will come across submersible (e.g bore or well pumps) and regular pumps that sit on dry land. The main difference here is shape with submersible being long and narrow to fit in a bore while regular pumps tend to be more squat. The key technical difference though comes from the submersible pump having a flooded suction ie it is under water and the other sits usually above the water on a bank. You need to be careful with regular pumps as to the bank height- there are significant limits on how high a pump can lift water (suction lift), it is always less than 10m and usually closer to 5 or 6m. If you need to lift water further than this then you need to consider a submersible pump or how to get your pump closer to the water surface.
Pumps on the bank also need to be primed before use- that is they cannot suck air, so you need to fill the line with water before starting up (a foot valve at the end of the suction line is essential- often with a strainer to stop dirt and debris getting in). Submersible pumps are already under water and need no priming.
Positive Displacement Pumps
There are as many positive displacement pumps as there are rotodynamic: Piston, diaphragm, lobe, flexible vane, gear and progressive cavity to name just a few. While piston pumps were common in agriculture many, many years ago, progressive cavity now virtually monopolise the market for agricultural positive displacement pumps. Many positive displacement pumps are self priming as they have the capability to "suck air", but note that suction head limits apply equally to these, keep your suction lifts short.
Positive displacement pumps have a very "flat"pump curve characteristic, that is their pressure remains fairly constant (drops much less than rotodynamic) while flow varies.
The way a progressive cavity pump works is that a rotor, usually a long stainless steel screw that looks like a round steel bar with a very slow twist in it is fitted into a rubber or polymer sleeve. As the rotor turns it pushes pockets of water between it and the sleeve. (Archimedes screw is an ancient example)
I always recommend use of these pumps with a pressure relief valve set at or just below the maximum allowable pressure. This way if something blocks the outlet flow there is a mechanical release of excessive pressure. Electrical pressure switches can be used, but in my opinion are not always fast enough or reliable enough, for example ants may block the switch or it could corrode over time and lack of use. As such electrical pump protection controls are always a secondary option for me with positive displacement pumps.
Step 11: Sizing the Pump
At least an approximate (or concept) size of the pump needs to be established prior to deciding on the solar array size. It is usually not possible to choose exactly the pump needed from this step as different manufacturers make a vast array of pumps, all with differing characteristics- Pressure, Flow and Efficiency.This step gives you enough information to start discussions with pump suppliers.
This step establishes the system demand or "Duty Case". You may find you have several duty cases, if so pump selection becomes more challenging as each individual pump has a limited range of pressure and flow it can operate in. Operating outside this range is likely to damage the pump through instabilities such as cavitation, etc. That is the formation of air pockets in the pump impeller.
My data is used in this example, however everything in this Instructable is scalable to whatever system size you want to construct. If after reading this you are uncomfortable with the mathematics required then contact your local agricultural irrigation retailer. It would be very unusual for them to be unable to do this work for you. You do however lose a bit of autonomy as you don't get to see and manipulate all the variables. For instance you may elect to change a pipe size and route to lower pipe friction using knowledge of your land that your retailer does not have.
The data we fed in here from the earlier steps- Flow rate 1.54L/s (5.5m3/hr), Maximum vertical lift height 5.07m, lift to irrigated pasture height is 3.6m and maximum pipe length 400m.
There is a pressure loss in the pipeline due to the friction of moving water through the pipe, this is the same situation regardless of buried poly pipe or movable aluminium irrigation pipe. The friction loss is proportional to the velocity (basically speed) of the water through the pipe. While you can have any flow velocity you want, once it gets over about 1.5 meters per second (m/s) the friction losses increase very quickly.
The calculation for establishing a minimum pipe diameter is as follows:
5.5m3/hr / 3600 seconds in the hour = 0.00153m3/sec
cross sectional area of the pipe in (m) = Flow rate per second ( m3/s) / Flow Velocity (m/s)
Area = 0.00153/1.5 = 0.00102 m2
Converting area of a circle to a diameter
Pipe diameter (m) = 2 x square root ( Area/ 3.1416) = 0.036m or 36mm
This is great as I already have 2" Rural Class B buried in the ground, this has a 50.8mm internal diameter using the above this means I have a velocity in pipe of 0.78 m/s. This is nice and low and will insure minimal losses in the supply pipework.
Next you need to work out the friction losses in your pipeline. There are all sorts of different pipes you can use depending on your system eg polyetheylene, cement, aluminium, steel just to name a few. You need to have a pipe friction table for the type of pipe you want to use. An excellent source is the "Pipe Friction Handbook" from the Pump Industry Australia:
https://pumps.org.au/product/pipe-friction-handboo...
A copy of the relevant page from this reference is attached to this step.
The pipe manufacturers also provide this data and there are many free sites on the internet, just search for "Pipe Friction" of your chosen pipe.
From the Pipe Friction Handbook (see attached page) read across at 1.6L/s flow rate to the 63mm OD pipe (52mm ID- while this is not identical to my pipe it is very close, my book is a little old being a 1993 version and pipe sizes have changed a little) I have a friction head loss of 1.35m/100m of pipe. As I have 400m of pipe my total friction head loss is 4 x 1.35= 5.4m. This is great, it is a very small loss and it means I have the capacity to move quite a bit more water through these pipes (with a higher frictional loss) if I ever want to in future.
I have ignored fittings and valves as there are so few in my system, but if you have a lot of fittings and valves then you need to calculate friction for those as well, there is some information in the Pipe Friction Handbook and manufacturers also have data. Generally though, if there are only a few the friction losses through fittings are very small.
5.4m is the pipe friction loss from the creek to the furthest irrigation hydrant. I then use 60m of 1.5" layflat hose to get to the centre of the paddock and 60m of 1"rubber hose to get to the irrigator. These all have friction losses and they need to be calculated.
So that you can calculate the flow friction loss in the layflat hose, more information is required. This is available from manufacturers or sites such as the below:
https://www.nationalpump.com.au/calculators/pressu...
The chart at the bottom of National Pump and Energy web page is for layflat hoses. I have copied this chart into the PDF of this step so you can see how it is used. Flow rate is 5.5m3/hr which is 5.5/60= .09m3 / minute. Start on the bottom left hand side of the chart with the flow rate- say 0.1m3/min. Go straight up until you hit the length of hose, 60m is just a bit further out then 50 so just estimate when it is not exact. Then go to the right until you hit your hose size, mine is the last at 1.5", now drop back down to the bottom and read off the pressure loss: In this example it is 9m.
Finally I need the pressure loss in the 1"rubber hose that follows the irrigator, from the Trailco brochure it is 227kPa. To convert this to m divide by 9.81 so rubber hose pressure loss is 23m.
If this is not available from your suppler you can use the National Pump table at the top of the page- though it is a very coarse table and difficult to find values between what is put in the table. Another website you can use is the below:
https://www.engineeringtoolbox.com/water-pressure-...
The only downside is that all the values are in imperial units and you will have to convert from metric to imperial and back- don't be too concerned. You can just put into your search engine "convert kPa to PSI" and you will straight away get a calculator.
The final pressure drop we need to know is at the irrigator jet. Each sprinkler manufacturer states required pressure. Again from the Trailco T50 Brochure I need 345kPa sprinkler pressure which is 35m of head.
Adding them all up:
Lift from creek to irrigated pasture 3.6m + Friction loss in 2"pipe 5.4m + Friction loss in Layflat hose 9m + friction loss in 1"rubber hose 23m + pressure required at sprinkler head 35m = 76m Total Head or 746kPa (multiply by 9.81).
This now gives us our first duty point for pump selection 76m head at 1.54L/s (5.5m3/hr) flowrate.
We can estimate the pump power at this point in kilowatts = (water density kg/m3 x head m x flowrate l/s) / (102041 x efficiency %)
Water density varies slightly with temperature and altitude, but for most agricultural applications it is fine to assume 1000kg/m3. We do not know pump efficiency yet, but for an estimate 50% is a reasonable ballpark figure to use, it is to be expressed as a decimal ie 30% = 0.3, 50% = 0.5, etc
Power = (1000 x 76 x 1.54)/ (102041 x 0.5) = 2.3kW
This is around what I had expected and know is in my budget range. You need to check at this point that the pipe and hoses you are using is suitable for the pressure rating. Old poly pipe was usually rated to 600kPa, more modern Rural Class B is rated to 800kPa for buried services (the allowable pressure drops with temperature above 20C). For higher temperatures or pressures metric pipe with thicker wall thicknesses is required.
All pumps have a limited range that they can operate in- If the pressure exceeds their maximum rating they cannot push the water out and it will heat up inside the pump, boil and cause all kinds of problems such as broken seals or damaged impellers. Operating at too low a pressure can result in things like cavitation or thrust in the shaft that lifts the impellers. Put simply, always operate within the range allowable by the pump manufacturer.
So in choosing a second duty point, great care has to be taken. As an example we'll look at pumping from the creek to the dam. We know the lift is 5.07m and the distance is 100m of 2" Rural class B pipe. We know we are looking for a pump capable of around 76m head so in theory lot's of pipe friction is OK. If we say 10L/s , then looking at the pipe friction handbook page again to see the flow velocity is 4.71m/s and pipe friction is 40.13m. Total friction in this case is 5.07+40.13= 45.2m at 10L/s (36m3/hr) flowrate, which is Duty Point 2.
Attached to this step is a pump curve for a Grundfoss SP7-17 multistage submersible pump. This pump was selected by the supplier based on my 2 duty points. The question was asked "which of the 2 duty points is most important", the answer is irrigating. The pump curve shows that a 7.4m3/hour (2.1L/s) flow rate can be achieved with a 70m head- this allows me to increase my sprinkler head size a bit if I want to in future. It is always good to have some spare capacity. Using similar lines to look at Duty case 1- if we go horizontal from 5.5m3/hr until we hit a point halfway between the 70 and 80m pressure curves then drop horizontally we see that the pump power required is 2.2kW, this is very close to the 2.3kW we calculated earlier, the difference is because the selected pump is slightly more efficient than the 50% we assumed.
The pump efficiency is obtained by following the shorter curve from the base of the pressure curve- our vertical line intersects this at about 50%. This tells us that the pump and motor combination is 50% efficient ie 50% of the electrical energy input is converted to hydraulic power. This seems low, but is very much standard for pumps. The important characteristic to look at is where the efficiency curve levels off (goes horizontal). That is peak efficiency for that type of pump you always want to be close to that and not down low on the efficiency curve.
Looking at our second duty point, already there is a problem. The maximum flowrate that this pump can achieve is 9m3/hr (2.5L/s) and that is at a head of 50m. This pump can not possibly achieve the desired flow of 36m3/hr so in order to use it the second duty point must change to 2.5L/s at 50m, this requires 2.75kW of pumping power- you can see the 50m efficiency curve has dropped off maximum efficiency and is down around 45% for this duty.
In this example the duty points for design 1.54L/s and 10L/s are very far apart, no single pump can achieve this kind of variance. If I really wanted the second duty point then I would have to purchase a second pump that was a better match for it.
This result supports low pressure irrigation- generally pumps with high pressure capacity have low flows and those with low pressure have high flows, for the same pump power. By using the pump power calculation earlier in this step you can see how with the same efficiency power is a product of Pressure x Flow. As stated before I would personally prefer a low pressure irrigator, but had decided at the outset of this process to retain my existing unit. If I had chosen a low pressure irrigator and pump, then I would be closer to achieving duty point 2, though unlikely 10L/s but perhaps around 5L/s as the second duty point may have been feasible.
One activity that has been omitted here is calculating Net Positive Suction Head (NPSH). As I am using a submersible pump there is no need to consider it as the pump is always flooded- that is below the surface of the water. But if you choose a pump that is installed above the water level, care needs to be taken not to have it too high or too far away from the water body. The maximum theoretical suction head of water at 20C is 10m. This has to allow for vertical lift and friction in the pipe and pump. In reality pumps really can only lift around half that- so keep your suction head down to around 5m or as advised by your pump supplier. If you are marginal and it needs to be calculated, be aware as it is a complex calculation requiring the vapour pressure of the water and temperature range you'll be operating at. See the link below for more information:
https://www.engineeringtoolbox.com/npsh-net-positi...
Or if you really want to study pumps and pump systems consider getting a copy of the Australian Pump Technical Handbook:
https://pumps.org.au/product/australian-pump-techn...
Having your duty points is a good step at which to contact pump suppliers and ask for quotes. Pump suppliers just need to know from you the duty point/s, water condition- that is anything that is different from standard such as pH, particles, contaminates, etc, lift height (for non submersible pumps) and operating hours (ie how many hours per year you need to operate). This is your pump specification.
There is a huge amount of information on the internet, too much really, to make pump selection easy. Your pump supplier will know what models are actually available and supported in Australia and generally suitable for your application.
As with all things I have found you get what you pay for. With pumps this is especially so. There are a lot of cheap pumps available now, but I have heard a lot of horror stories about them. They may be fine for duties that don't require a lot of operating hours or temporary installations, but I cannot recommend them for longevity, reliability or arduous duty. I believe the reason for this is that there are a lot of ways a less than reputable manufacturer can save money when building a pump- compromise materials, low tolerance machining, poor quality control and limited testing are just a few.
There really are only a couple of major suppliers of solar pumping equipment in Australia, they are international and have strong reputations, long warranties and good support. If you want to have a robust system with longevity then I suggest you source your equipment from these well regarded businesses, it will cost somewhat more than a "internet bargain" but it will be worth it in the long run.
Attachments
Step 12: Solar Array Sizing and Location
Knowing your pump power requirement enables sizing of the solar array. From the last step my power requirements are 2.2kW for Irrigation and 2.75kW for transfer of water from the creek to the dam.
Solar power is limited by the amount of sunlight falling on the panel and efficiency of the panel in converting the light to electricity. Firstly if we take weather out and assume every day is clear and sunny then the amount of sunlight is very predictable. The website below is excellent for seeing how much sun falls at any location on the planet:
https://www.pveducation.org/pvcdrom/properties-of-...
Solar energy by latitude and season (and tracking):
Available solar energy varies by season- longer days and more intense sun in summer compared to winter. This section looks at how the available energy varies by season.
In the first chart at the link above you simply enter your latitude (if you don't know it just put the name of your nearest town and the term "latitude" in your search engine and you will get the answer). For Australia we are always a negative "-" latitude being in the southern hemisphere. Then choose the day number, so day 1= January 1 and day 365= December 31st.
My site is at Latitude -31.4, so looking at day 180 in the middle of winter we get sunrise at 7am and sunset at 5pm and peak solar irradiance at midday of about 0.9kW/m2. So if we had an area of 100m2 we would get 100 x 0.9 = 90kW falling on that area at Midday, assuming solar panel efficiency of 15% 90 x 0.15 = 13.5kW is what these solar panels could generate at midday.
This first chart is based on the array facing directly towards the sun ie the panels are tracking the sun through the day. We'll consider this first and then do the more complex calculation from it for fixed panels further down in this step.
It is worth looking at the early morning and afternoon as well. Only 0.2kW falls on the array at 7:30am and 4:30pm, this would give only 100 m2 x 0.2 kw/m2 x 0.15 conversion efficiency = 3kW of electrical power. I have picked 0.2kw/m2 as this is a useful minimum, you can harvest the sunlight earlier and later than this but the amount of area needed increases dramatically, and for the extra 1 hour per day it is really not worth it.
So if your system needs at least 3kW to operate it will only work between 7:30am and 4:30pm (9 hours) on a clear mid winter day with tracking.
(Note that as I have used 100m2 as the base area you can scale this result provided panel efficiency remains at 15% eg if you have 200m2 of panels then multiply by 2: 2x13.5 =27kW peak and 2x3kw= 6kw early and late in the day.)
You can also use this chart to size your solar system- for instance if you want 8 hours runtime at full power mid winter then solar insolation is at 0.3kW/m2 between 8 am and about 4 pm. So assume you need 3kw of power and panel efficiency is 15%, then an area (m2) = 3 / (0.3 x 0.15) = 66.7m2 is needed (about 42 panels).
For comparison it is worth looking at mid summer, day 365, the sun rises about 5am and sets around 7pm. Ignore daylight saving, it just shifts this to 6am and 8pm- the day length is the same. 0.2kw is achieved around 6am and 6pm so again if our system requires 4kw then it will run for 12 hours between these times on a clear day, with panels tracking the sun. (It is somewhat shorter without tracking)
The peak solar insolation has increased a bit to about 1.05kw/m2 at midday meaning the 100m2 system will give us 100 x 1.05 x .15= 16kW at midday.
We can now see that for my location at -32 degrees (32 degrees south of the equator) the useful solar day length varied from 9 hours in winter to 12 hours in summer and that the summer peak intensity is about 18% stronger than winter.
Next we'll look at the effect of solar array tilt.
Solar energy by array tilt angle:
To get the maximum power from the sun the solar panels should always face directly at the sun. This is entirely possible by using devices called solar trackers. They are a frame that the panels fit on and have actuators that move the panels through the day to face the sun. This is a great idea but it has two problems, firstly the system is expensive requiring electronic control and moving parts, secondly it requires a lot of maintenance as things get damaged or fail and the trackers stall in one position. It is entirely possible that a new system will be developed that overcomes these issues, but until then I suggest use trackers only if you have to. It is much cheaper and less maintenance to just use more solar panels to compensate.
So consider you are going to build a fixed array, what angle should you build it at? As the sun passes through the day it's altitude is changing and so is the angle a direct line from it makes. The answer depends on where you are located, The maximum average power is generated by your system when installed at an angle equaling your latitude so in Cairns you would build it at 17 degrees to horizontal and in Hobart 42 degrees.
Use the link above and consider the second chart. This gives you the maximum power (incident) which is what you would get with a tracking system, it also gives you the minimum which is what you would see if your panels were laid flat on the ground. You can vary the angle from 0 to 80 degrees.
The summer peak stays very much the same through all the flatter angles but starts to drop from peak possible at a tilt angle of approx half latitude. The winter peak can only be achieved with an angle of about latitude + 10 degrees. That is for my site if I wanted peak power in summer then I would orient my panels at around 15 degrees, but the compromise is less winter production.
Conversely, if I wanted to generate the maximum winter power I would increase my tilt to about 41 degrees, but this would reduce my summer power production.
You can set whatever tilt angle you desire, whether like me you want balanced energy production throughout the year or a peak in power production in summer or winter depending on how you tilt your panels.
There is another angle you can change and that is orientation which is discussed next.
Solar energy by array orientation:
As the sun travels through it's path every day it rises (roughly) in the east and sets in the west. In summer it rises south of east and sets south of west. In winter it rises north of east and sets north of west. It is only at the spring and autumn equinox that the sun rises due east and sets due west.
While exactly where it rises and sets changes a little every day, at midday it is always true north (solar north) in the southern hemisphere, again using standard time, not daylight saving time. On a clear day the amount of sunlight is exactly the same before noon as it is after. A system that faces solar north will give equal power output morning and afternoon.
You may want to bias your system to morning or afternoon production, if so then shift the system to face west of north for afternoon/evening production or east of north for higher morning and lower evening production. The main reason I can think of you wanting to consider this is overshadowing- if you have tall objects like trees to the east or west of your array site they will block sunlight whenever the sun is low in the sky in that direction, so you may choose to shift your array orientation away from the obstacles to compensate. Overshadowing is discussed further below.
In most cases though your array will face solar north. Please note this is not the same as magnetic north. Magnetic north is always changing a bit, it wriggles around over time as the Earth's magnetic field changes and the field is a bit different all over the Earth. So to find the offset from north for your location just enter into a search engine your nearest town and the term "magnetic declination". For my location it is +12 degrees (East). To give an example of how it changes at an equivalent latitude of -31 degrees on the west coast of Australia magnetic declination is currently -1 degree (west). So a compass has a difference of 13 degrees to north from the east to west coast of Australia!
The positive (east) and negative (west) is a convention that if magnetic north is east of true north then the amount of the difference is positive and if it is west of true north the amount is referred to as negative.
So to survey solar north at my location I must align 12 degrees west from the compass bearing of North, at the sample location in Western Australia I would need to align to 1 degree east of magnetic north.
How to do this in practice- firstly I just use a compass and a helper. I sit the compass on a flat surface and adjust to have a line of sight across the dial to 12 degrees west of north. I have a helper drive in a steel post in my line of sight, then a second one further away, a string line between these will align pretty close to true north. There are special compasses for this but I just use a regular compass and can get it accurate to about 0.5 degrees.
A second method is to put in as tall a post as you can, as straight as you can. Then wait until midday (standard time), drive in a second post at then end of the shadow, the line between the two posts faces true north. This method is more accurate if you do it mid winter around the 22nd June as the shadow is longer.
There are also customized instruments for doing this, but unless you need to establish true north all the time, they are not worth the money.
Calculating Solar output from a fixed array
The first chart in the link above is the solar insolation that falls onto a surface directly facing the sun (ie panels on trackers). As it is much easier and more reliable to build a fixed array, the amount of solar insolation that falls on it will be reduced somewhat.
This is especially the case with a solar north facing array during summer when the sun rises south of east and sets south of west. At these tiems the sun is actually behind the panels. Then when the sun is facing the panels it is shining across them rather than directly on them- think of the sun as merely providing a "glancing blow" to the panels at these times.
The page below provides a calculator for determining the actual insolation a panel at any tilt angle and azimuth (orientation) angle receives at any time of the year:
https://www.pveducation.org/pvcdrom/properties-of-...
S incident is the sun shining on the module but S module, the sunlight perpendicular to the module is all that it receives and can utilise to make electricity.
Going through an example:
Let us say that we need 0.25kw/m2 for the system to run, we'll look at mid summer and mid winter and see what times the system will start and stop.
Putting in the year 2020, month 12 and day 23- this is mid summer. Entering latitude and longitude, for me Longitude 152.9, latitude -31.4, Module azimuth 0 (facing solar north) and tilt angle 32 degrees.
Entering time values to seek 0.25kW/m2 I find that it occurs at UTC 21:15 which is local time 7:15am (Just use a UTC time to local time converter such as http://www.timebie.com/timezone/universalnsw.php it is simply Coordinated Universal Time and is a way to express time internationally, this time ignores daylight saving where it applies and is just the time at Greenwich in the UK)
At the other end of a day 0.25kW/m2 occurs at 4:20pm (6:20AM UTC time) so 9 hours operation
In mid winter, June 23, 0.25kW/m2 is achieved at 8:00am (UTC 22:00) and 3:40pm (UTC 5:40) so 7 hours 40 minutes of operation
The average solar hours in a year for these fixed panels, ignoring clouds is (9 + 7.67) / 2 x 365 days per year = 3042 hours
If we were using trackers, then according to the direct insolation chart (first link in this step) we would achieve 0.25kW/m2 at these times:
Mid Summer- 5:45am and 6:25pm, 12 hours and 40 minutes of operation
Mid Winter- 7:45am and 4:25pm, 8 hours and 40 minutes of operation
With trackers the available hours per year are 3894 hours or 28% more- mostly in summer (3 hours and 40 minutes more in summer and 1 hour in winter) in this example system. Note that the benefit of trackers increases with latitude so they are more benefit in say Melbourne than Darwin.
The problem with fixed panels is they are actually shading themselves at the start and end of a summer day and then the sun is at a very acute angle to them so it is quite some time after dawn and before dusk that production of panels drops too low for use.
During winter the sun rises to the north of east and sets to the north of west, the day length is shorter, but the angles at which sunlight strikes the panels are much more preferable.
Overshadowing
Solar panels do not work well when there are shadows on them, it does not matter if it is shadow on one panel only. When the panels are connected into a string (they are all connected one to the other), if one panel is in shade it affects the output of the whole string. Without getting too complicated with why this happens (it is a function of the semiconductor that makes the panel) just imagine each panel as a valve, when the sun hits the panel the valve opens and flow can occur. So if one panel is in shade then flow is fully or partly blocked through the entire string of panels.
The simplest approach is to avoid overshadowing through most of the day. If this can't be done you can install "optimisers" on each panel, they compensate for overshadowing by ensuring each panel can contribute its maximum power. These do increase the system cost.
One of the benefits of having a farm is having lots of space, so usually it is not hard to find a location where overshadowing is avoided for most of the day. Early morning and late evening are exceptions- shadows from trees, sheds and even fences can stretch out a long way with the sun low in the sky. But as we have seen above- it is very unlikely your array will be big enough to make use of dawn and dusk light.
The only way to overcome unwanted overshadowing is to either move the array further away from the obstacle or raise it up higher off the ground. Given dawn and dusk shadows are hard to avoid, just find a site with balance that ensures your array is in full sun throughout the useful daylight period and allow the shadows to fall upon it at each end of the day.
In my case I have trees about 50m tall 150m away to the east of the array. These cast shadow on one end of the array until about 8am in the middle of winter but are not a problem in summer. I have a farm fence about 35m west of the array, and then nothing but a mountain the sun sets behind about 8km away. I also have a fence around the array to protect it from my itchy cows. To prevent overshadowing from the fences, I have lifted the array 1.2m off the ground.
Another reason for this lift is that I have summer active grasses, they easily grow to 1m high and more. These can cast shadow on the array. Even though it is just a series of thin stalk shadows, it has a big impact. So every now and then when the area around the array is not being grazed I need to run the slasher around it and cut the grass down. In this case the higher the array above the ground the better.
The best measure of overshadowing on your farm is photographs. Take a photo of your chosen site at different times of the day around mid to late June and the same site again around mid to late December. You can keep an eye on it through out the 6 months if necessary. This process is slow, but likely you already know where the shadows fall at different times of the day and different days of the year.
If you don't have the time for this you can calculate shadows- see an architect or draftsperson to help you with a shadow diagram generated by a computer or for a simple obstacle that you know the height of look up a table of the azimuth and altitude angles of the sun at different times/dates and then use trigonometry to calculate the length of the shadow.
Clouds
All of the factors above we can control when we choose our solar array location and design our array. Unfortunately we can't control the weather. Clouds cast a shadow over the array, the thicker the cloud, the less light makes it through onto the array.
You can get some idea of how many clear days a year you get from the website we looked at earlier in this Instructable:
https://weatherspark.com/y/144604/Average-Weather-...
For my location on average I have 63% clear days in summer and 83% clear in winter, great for winter/spring irrigation and the longer summer days make up for their being less clear days for water transfer of peak flows to storage.
The impact on the fixed system above with 3042 hours available is to reduce this as there are 73% average clear days only so actual available hours are 3042 x 0.73 = 2221 hours per year.
Looking at some other locations:
-Cairns 19% clear in summer, 64% clear in winter. This is a much more difficult location for solar- being further north their is more sunlight, but there a lot less clear days, focus of systems in this area would be to work during the cooler months so you would probably orient them to make the most of winter sun and just not use them in summer.
-Perth 86% clear summer, 69% clear in autumn. Ideal for winter/spring irrigation and great for anything in summer.
- Hobart 62% clear in summer, 47% clear in winter. Another awkward but not impossible location, The array may simply need more panels to give the desired output, this will be covered a little further on.
I have attached a part of a solar module specification sheet to this step, all photovoltaic panels have the same type of response to different light levels. It shows the output amperage in response to partial irradiance. The panel output power is proportional to amps, the greater the amperage, the greater the power. You can see that the maximum is a bit over 5 amps at 1000 (1kW/m2) irradiance, we know this is typical of midday on a summers day, this drops to 1A at 200 (0.2kw/m2) as we know from above this is about an hour after dawn and before dusk. So the output power of the panel changes by 5x from dawn/dusk to midday.
You can consider cloudiness to have an effect during the day on reducing solar output similar to conditions in the morning. The effect of cloud is proportionate. For example thin cloud or light mist may just reduce irradiance by 50%, but thick cloud may reduce it by 80% or even more. If you want to assess this on your site you can buy an irradiance meter- they cost from AUD$200 to about $2000. But my rough guide is as follows, using "normal irradiance" to be the clear sky irradiance that could be expected for that time and day :
- Thin, high cloud, light mist: about half normal irradiance (hard/impossible to look at the sun through the cloud)
- Moderate cloud/ fog : about one third normal irradiance (can just look at the sun through the cloud)
- Thick cloud: less than one quarter normal irradiance (can't see the sun through the cloud- maybe around the edges if they are isolated patches)
For example if normal irradiance would be say 0.4kW/m2 at 8am and there is thin cloud/mist then actual irradiance would be around 0.2kW/m2, if it persists to midday when irradiance would be 0.9kW/m2, then the actual irradiance would only be around 0.45kW/m2.
So depending on the cloud type you have, you can add more panels into the array to compensate. I've found this really only be economically effective for moderate cloud, but in theory should be effective for any diminished irradiance level. So from the amperage/irradiance chart we see that output at 0.5kw/m2 is half the maximum it means we need 2x the number of panels to give the same power output as a clear day.
One last comment on clouds is that patchy but thick clouds can be a problem. The system will switch on and off with the passing of the clouds. So if you are running an irrigator it will start and stop according to cloud or clear. If this is a serious problem in your situation then consider installing a large pressure tank or batteries or grid hybrid. I just grin and bear it with a small pressure tank to take the hammering effect out. This is another effect and I'll cover it more later- every time the system starts and stops there is a hydraulic impact through the system called water hammer. So in all solar pumping systems it is good to have a pressure tank that can absorb these shocks.
My Site Selection
I wanted a site for the array close to where the pump would be located in the creek, bore or dam.The array can be further away but then electrical cable is needed to connect it to your pump- electric cable has losses (like friction in a pipe) called voltage loss. So as cables get longer they must get bigger in cross sectional area and so more expensive.
I also wanted a site that did not get in the way of other farm management such as moving animals, planting and maintaining pastures. Ideally a site that did not take away any productive land.
Obviously I wanted a north facing site with no or minimal overshadowing, occurring only early or late in the day.
I found that part of my dam bank was oriented to solar north and had a slope about 30 degrees. The first photo in this step shows the section of dam bank I chose, with a very pretty young lady who volunteered to provide a sense of scale.
Whilst the dam bank curves slowly this 24m long section was relatively straight. and about 5m on the diagonal from the top to the bottom of the bank. So total site area 24x5= 120m2
The next photo shows how I set up temporary profiles. They are the timber frames aligned to solar north and pitched at 32 degrees. I made sure we had a truly rectangular site by measuring the diagonals and squaring up. The string lines show where I planned to put my footings.
Sizing
The above provides all the background you need to know to size your array. I'll go through the example of sizing mine so you can copy the process. If this is all too much maths for you, then you can ask a reputable solar pump supplier or system designer to do it for you. They have their own computer models that make this very easy.
I need 2.75kW maximum in summer and 2.2kw maximum in winter. There are other system losses that need to be allowed for such as voltage drop in cables and losses in the inverter. At this stage apply 10% as an estimate and refine the calculation later once these losses can be better defined. So the design power becomes 2.75x1.1= 3kw summer and 2.2x1.1= 2.4kWwinter.
I also know that I need as long a day of irrigation in winter as possible, back in irrigator selection I decided that 8hrs per day in mid winter was the basic goal.
Given I have tree overshadowing until 8am mid winter, that is a good time to start. From the arbitrary orientation calculator (second weblink in this step) in mid winter at 8am (22:00 UTC) irradiance at my site is 0.2412kw/m2.
8 hours later at 4:00pm (06:00UTC) the irradiance is only 0.1651kw/m2.
Trying for the 8 hour irrigator run mid winter:
Solar Power (kw)= array area (m2) x solar irradiance at the time (kw/m2) x panel efficiency
2.4kw = array area x 0.1651 x 0.15
Array Area (m2) = 2.4/ (0.1651x0.15) = 97m2. This is possible, with panel area approximately 1.5m2/panel (Note that while the total panel area is 1.6m2, in framed panels the frame takes about 0.1m2 so the solar module area is 1.5m2) this would require 97 / 1.5 = 65 panels (65 x 1.6 = 104m2 total array area). This is a bit larger than I''d like, but close to what I can afford. So we'll shorten the day up a little and see if we can get a more affordable result.
Trying 8am to 3:45pm, just 15 minutes shorter. The insolation at 3:45 is 0.2256kW/m2, quite significant how much difference 15 minutes can make at the ends of the day.
Array area (m2) = 2.4 / (0.2256 x 0.15) = 70.9m2 or 47 panels. This is achievable, by taking 15 minutes off the operation, the number of panels required reduces by a quarter (along with the cost for the panels).
Solar panels are always rated at 1kw/m2, so to convert the area of panels to power rating is simply Area x efficiency x 1kw/m2 = 70.9 x 0.15= 10.6kW. So an array of 10.6 kW will achieve the 7 hours 45 minutes of irrigation in mid winter. Knowing the duty point at 1.54L/s this is 42,996L / day irrigated out.
Given this sets the array size, working backwards we can establish how many hours of water transfer can be achieved in mid summer:
2.75kw (transfer power) = 70.9m2 array area x solar irradiance x 0.15
Solar Irradiance= 2.75 / (70.9 x 0.15) = 0.26kw/m2. Referring back to the arbitrary orientation calculator at the second weblink we can see that 0.26kw/m2 occur at 7:15am (21:15 UTC) and 4:20pm (06:20UTC) giving us just over 9 hours of water transfer. Based on the pump chart in sizing the pump we get 9m3/hr x 9 hours = 81m3 or 81,000 L transferred to storage per day.
You can build your system with more or less panels, but my recommendation is to use at least 2x the total power of the pump, for example in my system 2x2.4 = 4.8 or say 5kw. If you go any less than this the number of operating hours per day will be very limited. Take in mind the effect of cloudiness at your location- the more cloudy your area is, the more panels you will require.
The last 2 attachments to this step show calculations of the pump performance provided by Grundfos, the pump supplier for my system. They model a 5kw and 10kw array. The 10kw array provides almost maximum production throughout the entire day while the 5kw system has "shoulders" of lower production during the morning and afternoon.
For my system I went with 10kW, It gives me the flowrate I need for the longest reasonable time. It is just below the 10.6kw calculated as required, but is close enough- there is a technical limit of string voltage that restricts my system and we cover that in step 14 Designing Strings of Panels. Generally the system will operate with light levels at the module of 0.25kW/m2 so it is a reasonably long day and fairly robust in response to cloudiness.
Finally using the panel efficiency gives us an overall array area, but at some point you need to convert that back to number of panels. A note of caution here, solar panels consist of individual cells, most commonly in Australia we see 60 cell panels they are usually about 1640x990mm (1.62m2 total area, about 1.5m2 of module) each. But there are also 72 cell panels, these are bigger 1981x990mm (1.96m2) and are usually used in commercial systems. There are also a lot of strange sizes related to special duty panels (camping) and older panels before they more or less standardised. I used 60 cell panels as they were readily available. A quick way to convert your array area to number of panels is as follows 70.9m2 array area/ 1.5 = 47.2 60 cell panels- now part panels don't exist so that means 48 x 60 cell panels.
You can also get panel power 10600w / 48= 220w per panel. These don't exist, the nearest size is 250W so The 70.9m2 array would be 48x 250w panels = 12,000W. The 250w panels are more efficient than our assumed 15%, so in reality we would go for 10,500W being 42 panels at 250W. Module area = 42 x 1.5 = 63m2 and total array area = 42 x 1.6 = 67.2m2.
Step 13: Solar Array Technicalities and How to Choose Panels
The last step covered the basic sizing and siting of your solar array. This step covers some of the detail necessary - the finer points if you are doing your own system. A system provider will take all this into account when designing your system if you contract one.
The specification sheet and panel label explained:
The attachment above is from BP Solar, they stopped making panels back in 2011 so this data is quite old, but it will serve to demonstrate what to look for on panels. These are a monocrystalline panel- meaning that each cell is grown from a single crystal. The alternative is polycrystalline (also called multicrystalline - it is the same) - each cell is made of many crystals. Mono are more expensive to make but are more efficient than poly.
Looking first at the table in the specification sheet, working from the top down.
- STC this is standard test conditions of 1kw/m2 and 25C panel temperature
- NOCT this is nominal operation cell temperature being 0.8kw/m2 irriadiance and 20C air temperature- it is a more realistic indication of panel perfromance that STC.
These both define how the values in the table are developed, STC is an ideal situation and allows comparison between panels NOCT is somewhat more like real life conditions in the field.
- Pmax, this is the maximum power the panel can generate
- Vmpp, The voltage at the maximum power point output by the panel
- Impp, The current at the maximum power point
The maximum power point is the point where V and I are such that they generate the most power. Power = Voltage V x Current I. Looking at the Irradiance curve you can see that at each irradiance the current is pretty well constant until 35 volts where it starts to drop off. For this panel the Maximum Power Point (MPP) is at 35.4 volts and 4.94A for 1kw/m2 irradiance (35.4x4.94=174.9W which is the panels rating).
- Isc Short circuit current
- Voc Open circuit Voltage
Short circuit current is the amount of current that flows when a panel is short circuited- that is it's positive and negative cables joined together, this is the maximum possible current the panel can produce. Open circuit voltage is the voltage that is measured from the panel under no load, that is take a multimeter and with the panel facing the sun measure the voltage from positive to negative. Typically this is the maximum voltage the panel can produce.
It is useful to have a "clamp meter"or "Tong tester" as they are sometimes known. I have attached a picture of my clamp meter- it measures current and voltage in both AC and DC - but only one at a time. The tongs go around or "hang off" a single cable (note do not attach to multiple cables as it will not work) to measure current using induction, this is not perfectly accurate but good enough for us. The probes are used to measure voltage between two points. Another useful function is continuity- you can check that there is a low resistance path between two points ie they are continuously joined.
If you are concerned your panels are not working properly you can test the Voc and Isc against what is on their label- make sure the panel is facing away from the sun or covered with something like a blanket when connecting or disconnecting the panel positive "+" and "-" leads in short circuit otherwise they will arc (throw a spark) between the plugs. The values you see should be something like what is on the specification sheet or printed label on the panel- you should do this test at midday on a fine and clear day with the panel oriented as close as perpendicular to the sun and compare results with STC or NOCT values.
- Tolerance
- Nominal Voltage
These are not very important to you, tolerance is simply how the above values can expect to vary as each panel is slightly different. Nominal voltage is just the typical indicative voltage the panels will operate at under normal load. The voltage output drops as load is applied.
- Efficiency reduction at <200w/m2
- Reverse current limit
Neither of these are very important to you, firstly panel efficiency generally reduces below 200w/m2 (or even a bit higher) but you are unlikely to be operating at that level. Reverse current is of technical interest only rather than practical interest- a solar panel can reverse itself, to stop this happening a diode is used. This is like a one way valve in water, stopping back flow. Sometimes the diode fails causing problems.
- Temperature coefficients of Isc, Voc and Pmax.
Solar panels are temperature sensitive devices, they prefer cold clear days, as the panel heats up the output drops. Typically current is temperature stable with very little change, but voltage and thus power both decline. Note that this is the surface temperature of the panel, not the air temperature. For these panels Power output changes by 0.5% per degree Celcius.
On a 38C day I have measured panel temperature at 50C (and it is possible for panel temperatures to reach around 70C) so the power output compared to STC is: (Actual surface temp 50C - STC Temperature 25C)*0.5% = 25 x 0.5% = 12.5% less. So reduction in power is power at STC 175W x 0.125 = 21.9W Actual reduced power = 175 - 21.9 = 153.1W
As mentioned in the previous step it is advisable to oversize your array. During operation the panel temperature is always significantly more than the air temperature. The worst of this effect is fortunately from mid morning to mid afternoon, as irradiance drops the surface temperature drops and gets closer to air temperature. Obviously though on very hot days the air temperature may not drop much until evening so if your system is sized marginally, it's performance will suffer in the afternoon of hot days.
The temperature effect is so important that many manufacturers provide a graph of panel voltage change with temperature- you can see from the attached example it is quite dramatic.
- NOCT
This is not always given. This manufacturer was thorough in this case and provided it, this gives the temperature value that was used for the NOCT testing.
- Maximum series fuse rating
This is the manufacturers recommendation for the maximum fuse size that should be used with the panel. All systems should have a fuse, this is covered in step 20, wiring the system.
- Application class
This is divided into three: A- for buildings, B- for energy suppliers, C- low voltage. You will mostly find class A panels available second hand.
- Maximum system voltage
This is the maximum voltage recommended in a string, that is when you connect a line of panels together the maximum voltage should not exceed the stated amount. There are 2 values as one is International Electrotechnical Commission and the other the United States Electrical Code. In Australia we use the IEC values.
Note that when you join panels together the voltage is additive, while current stays the same. So to determine maximum string length use Voc, for this example panel 1000/Voc = maximum number of panels allowed by IEC = 1000 / 43.6 = 22.9. In this case I would be cautious and round down to 22 panels. You may get away with 23 given that we have used the STC Voc rather than NOCT value, but I really recommend err on the side of caution.
- Mechanical Characteristics
These will vary a bit for all panels and is not worth looking at closely, dimensions and weight are of value- note that these are an old panel and are a bit smaller than the current standard of 1640x990mm and as such are a bit lighter than standard, typically panels now weigh around 20kg each. They are also a thick frame being 50mm, panels now tend to be 35-40mm thick. More recently impact testing has been added to panel mechanical data covering wind load and snow loads.
- Warranty
This is important, firstly there is a defects guarantee but secondly there is a performance guarantee, these usually stretch out to 25 Years. Look closely at it, there is about a 7.5% decline in output power with every 12.5 years of age. In my experience this occurs regardless of whether the panel is installed and working or stored in a box- an old panel is an old panel regardless and it's performance will be less than new. One that has been in storage will likely degrade less than one in service but it still degrades. Thermal cycling and moisture (humidity) seem to be the main culprits that cause panel degredation.
So what is the effect of this in reality? You are buying panels with a label (in this example) of 175W, we know from the specification sheet that under real conditions (NOCT) this drops to 126W, but after 12.5 years this is 7.5% lower again 7.5% of 126= 9.5W so the real module output of a 12.5 year old panel = 126-9.5 = 116.5W.
As the panel ages this continues, at 25 years it is around 100W under NOCT conditions.
As you will want you system to work well for 20 to 30 years it is yet another reason to ensure your array is significantly larger than the minimum ie at least 2x the calculated total power requirement and ideally more.
In some minor applications on my farm I have panels made in the 1970's that I have picked up for free, so they are now 40-50 years old. They still work but their output is less than the original spec. Some have failed- corrosion of the solder joints being the issue with these. All of them had some type of damage when I got them and they slowly get worse with time. I use them for jobs like fence energisers, battery charging at my cattle yards, powering small pumps, etc.
Back in the 1990's I met a retired professor from the University of NSW. He was a pioneer in the world of Photovoltaics and made by hand some of the first Australian cells and panels iin his lab. He was still using some of his prototype panels to power his remote bush hut. They were a simple affair with the silicon wafers mounted on window glass and sealed from moisture with contact- a self adhesive plastic film for covering books. Every few years he'd just replace the contact.
In conclusion panels will mostly outlive their "linear power warranty" and give many more years of service. The longer service life you want, the more you should oversize your array. However who knows what is 20 or 30 years down the road, doubtless by then you'll probably be able to get replacement panels with twice the power for half the cost. Perhaps a new energy source will replace photovoltaics and all you do is decommission your panels and plug whatever it is in. Best advice I can give is decide on what design life you want, what makes economic sense to you and then review your options in the future once the system has completed its "design" life.
- Drawing
Sometimes as per in this example the drawing will show you where the panel can be mounted to rails in order to maintain it's pressure rating. If this is not provided never have more than one quarter of the panel cantilevered (unsupported overhang) past your rails. So for a 1640 long panel, the maximum overhang top and bottom when installed in "portrait" orientation is 1640 / 4 = 410mm.
I have attached a photo of the data from one of my panels, this is representative of what you will find on all panels. It does not have all the technical information, but covers the most important. It is worthwhile when you get your panels to get a technical data sheet with them, I have found that manufacturers sometimes take theses spec sheets off their website when they stop making that model. They are very useful to refer back to in the future.
Choosing New Panels
The market is swamped with manufacturers and brands of panel. It can be very confusing as each touts theirs as "the best". I do not believe there is a "best", simply some panels are a bit better than others. So what to look for?
Tier 1 is a term very widely used. It has nothing to do with the quality of the panel but the financial stability of the manufacturer. It tells you something about the likelihood of the manufacturer being around in 25 years to honor their warranty. Keep in mind that since the closure of BP Solar there are no panels manufactured in Australia- they are all imported. So your warranty claim will most likely be through your retailer or distributor. This is the important issue to look into.
For instance a retailer may be directly importing container loads of solar panels from a "tier 1" manufacturer overseas. If these panels fail in the future and the retailer is no longer around then your only recourse is direct to the overseas manufacturer- a near impossible task.
The key is to look for a strong Australian presence- does the manufacturer have representation here? Many of the big names do and will back their warranties regardless of what happens to the retailer. If the manufacturer does not have a presence here then do they have a reputable distributor that is contracted to represent them? If so then the distributor may have an obligation to support your warranty. Simply ask your retailer- "Who will honor the panel warranties if you are not around".
From the first part of this step you know what to technically look for. But you will find all sorts of little differences between panels as manufacturers seek to find an edge. These are mostly of secondary interest compared with the NOCT performance.
Many people like the "bigger is better" and go for the highest wattage available, currently in 2020 this is something like 360W in standard 1640x990mm size but is easily around 500W and more in bigger dimensional sizes. Wattage is really cell efficiency- as we saw in the last step we get up to 1kw/m2 of light energy, for panels of the same area for one to be 360W and another 250W the difference is that the first is Panel power kw / (module area m2 x irradiation kw)= 0.36kw / (1.5m2 x 1kW/m2) x 100 = 25% versus 0.25 / (1.5 x 1) = 16.6% efficient.
Panel efficiency has been improving since photovoltaics were invented and is likely to keep improving for many years yet.
The highest wattage available is of use when your space is limited, for instance a small suburban roof and you want the maximum power possible, or your mounting system is expensive. Space is usually not a constraint on farms, where there is a huge amount of space for solar, but minimising the mounting cost may be worth while.
The best way to look at this is not maximum panel power (unless you are space constrained or have mounting issues) but cost/watt of power. Generally the higher the efficiency the panel, the more modern it is and the more expensive to make. Currently a 300W panel costs around $300 to buy so as of 2020 the ratio is about $1/W. This ratio will change but regardless of when you are doing your system- compare prices offered to you as $/W. A 360W panel now will actually have a higher $/W price of around $1.30-$1.50/W due to it being a new design.
In summary if you are buying new panels:
- Choose a reputable supplier with local representation or agency/distributor to ensure warranty security
- Compare panels on technical specifications, especially NOCT, and not additional features, unless those features are of significant value to you
- Don't worry about the most powerful panel unless you are space constrained, compare suppliers on $/W
Renewable Energy Credits (REC's)
All new panels purchased and installed by an accredited installer, either grid connected or not are eligible for REC's in Australia (while the scheme lasts, currently phases out in 2030). The amount of REC's issued diminishes a little each year. As of 2020 it is about 15 credits per kw for my location (the number issued vary by postcode- based on how much generation is expected at the location), and the current price per certificate is $37.50 so $562.5/kw or $0.56/W. This is under the small system <100kw or STC rules. If your system will be bigger than 100kW it is treated as commercial and the LGC rules apply.
Note that REC prices change as they are traded in a market, there have been periods where they have fluctuated significantly.
There are many rules around claiming REC's and before you assume you can claim them check your eligibility- some of the important factors are that your supplier and installer must be registered. See the website below:
http://www.cleanenergyregulator.gov.au/RET/About-t...
And the REC registry itself:
https://www.rec-registry.gov.au/rec-registry/app/h...
Choosing Used Panels
Used panels are an excellent option for agricultural systems. I have been able to buy reasonably modern panels (225-270W) for AUD$0.10 to $0.20 / W and have seen them sometimes available for less than $0.10/W. Often they are available in bulk, especially when systems have been replaced on factories. There are many valid reasons that used panels become available, some common ones are:
- Tenants, particularly commercial, leave their premises and their lease states they have to make good so must remove their solar panels.
- For many people, and especially small businesses that use a lot of electricity during the day, it is economic to upgrade and so change out an entire system.
- Often during upgrade the old system must be removed as it is not economic to upgrade it to new standards, or it compromises the efficiency of the new system.
- Buildings being demolished.
You cannot claim REC's on used panels, but used panels are already very cheap.
From this step you know that the panel power output drops a little each year, on average by 0.6 to 0.8%, so you want relatively new panels if you can get them. If you can't then make sure you apply the reduction eg for 185W 15 year old panels say they have declined by 0.7x15 = 10.5% so they really only are 166W. If they were $40 per panel at 185W that would be $0.21/W but in reality they are $40/166= $0.24/W.
Inspect the panels and look for damage, typical things to look for are:
- Delamination- often a discolouration where water has seeped in along an edge.
- Cracks- usually the back panel only, the front is hardened glass and will shatter.
- Corrosion- look closely at the solder on the face of the silicon, it should be smooth and shiny, if it is rough or shows green/black discoloration then it is oxidising.
- Frame damage- The aluminium frame should be in good order
- Scratches- even though the front glass is hardened it can still be scratched, make sure it is clean and smooth
The panels may still work well with some or all of the above damage, but it does affect the price as the panel will likely have a shorter life.
It is worth using your multimeter (clamp meter) to check that Voc and Isc are as per the label. This is challenging when buying panels as you can't easily get them at the right angle and can't always test them on a clear day at midday. It is also time consuming. So you are better to test just a few of what you are thinking of buying and make allowances for cloud and time of day. It is easier to do if you can test the panels before they are dismounted from their frame as they will all have the same orientation and you can just cover them one at a time with a blanket to do the short circuit current test.
I have attached a table of test results taken from one of the arrays that I built. Unfortunately the day was not ideal, but the results can be useful. Having a look at them I have 3 types of used panel in my array:
- 12x 270W Powerwave
- 3x 250W Trina
- 6x 225W Solon
The test was conducted at 3pm on 2nd April so irradiation would have been about 0.87kW/m2. There was patchy cloud that interrupted the tests, but clear between.
The Powerwave and Trina panels are reasonably new being in the order of 3-5 years old but I know the Solons are quite a bit older probably around 10 years old. All panels were made with a tolerance of 3%. Looking at the data, each panel performed close to it's group:
- Powerwave Voc -11.52 to -13.8% less than rated Voc and Isc 1.41 to 9.11% above rated Isc
- Trina Voc -15.11 to 15.16% less than rated Voc and Isc -0.57 below to 3.98% above rated Isc
- Solon Voc -13.02 to -13.64 less than rated Voc and Isc 14.12 to 16.13% above rated Isc
It is reasonable that Voc was lower than normal across the board, the spec data is at 1kW/m2 and the test was at about 0.87kW/m2 incident irradiance, and then the array is at a fixed tilt resulting in a further reduction.
The Powerwave panels had the biggest variation in Isc with 3 panels in particular lifting the upper limit and a wider variation in Voc. In comparison to the Trina panels that are similar age I'd say that the Powerwave have poorer quality, if the 4 worst Powerwave panels are omitted then the range drops to Isc 1.41 to 6.29% above rated Isc- similar to the Trina.
It may also be that there is just a bigger sample of Powerwave and if there were the same number of Trina then perhaps they would show the same variance.
What I have seen consistently as panels age is that Isc increases, this suggests a gradual breakdown of internal resistance. I have not been able to find out why. So when you are assessing panels try to find those with Isc as close to specification as possible as this seems to be a good indicator of panel age.
You will have noticed that I have used different makes and power ratings of panels in my array. Solar installers avoid this as it causes some problems, but they are solvable. The reason I did this was because when building my array I could not get enough of the same type of panel to achieve the 10.5kW output that I wanted.
The next step 14 Designing Strings of Panels covers the practicalities of how to match different panels together into strings.
A Note on Joining the Panel Cables
The last 3 photos on this step show the male and female plugs that are on each panel, one is positive, the other negative. To join just push the male into the female, some force is required and they are home when the little lugs on the side click into place. These hold it together and ensure the rubber seals make the joint waterproof.
Taking them apart can be challenging for the uninitiated. The solution is to get a solar panel plug wrench (or spanner as it is also called). The last photo shows one of these. You slide the prongs over the pins to push them down, you can then pull the plugs apart- it takes a bit of force. The round end is for doing up the nut on the end of the plug to ensure it is water tight.
If joining panels that come with different plugs you should cut the old plugs off and crimp the same plug set on at the joint- male one side and female the other.
Attachments
Step 14: Designing Strings of Panels
Solar panels are connected in series to make a "string". That is the positive of one panel is plugged into the negative of the next and so on until they are all linked like beads in a string. In the last step we looked at the maximum string length based on keeping the string voltage below 1000V. This is the upper limit, the supplier of your pump may specify a maximum input voltage less than this. For instance my pump has the maximum input voltage of 800V- this limit stopped me achieving the 10.5kw that I wanted as the string voltage rose above 800V.
If you can't get enough panels in one string to reach the total power you are after, you must have multiple strings to create your array.
There is no limit on the number of strings that you can have. The only rule is that within an array each string must be identical in voltage and current.
In some systems several array's can be used. However these require special controls to regulate- usually an inverter with at least 2 MPPT (Maximum Power Point Tracking) inputs. The rules for each string in each array are the same, regardless.
It is even possible to put arrays at different orientations to increase the length of the day that power can be provided eg one array facing north and a second facing west.
My system is an excellent example for designing a basic string and an array, Each string has 3 different types of panels: Different wattage, Voltage, current and power. This step will show you how to combine them together.
See the attached schematic showing the layout of my 42 panels into 2 strings of 21.
The rules for array design is that the panel voltage is additive and current is limited by the panel with the lowest current capacity. This is the same as overshadowing- one panel can reduce the current through the whole array. For adding strings together into an array the array voltage = the voltage in each string but the array current = string current x the number of strings in the array.
Each string should have the same voltage.
Calculating maximum string voltage = 12 x Powerwave Voc + 3 x Trina Voc + 6 x Solon Voc = 12 x 38.7 + 3 x 38 + 6 x 36.52 = 797.52V , this is below the 800V maximum voltage limit of the pump supplier so OK.
Calculating String Vmpp = 12 x Powerwave Vmpp + 3 x Trina Vmpp + 6 x Solon Vmpp = 12 x 31.7 + 3 x 30.3 + 6 x 29.4 = 647.7V and is also the Array voltage.
The String Impp = Impp of the Solon as that panel has the lowest current capacity = 7.65A
There are 2 strings in the array so Array Impp = 2x String Current = 2x 7.65 = 15.3A
The String Power = String Vmpp x String Impp= 647.7x7.65. = 4955W
There are 2 strings in the array so Array Power = 2 x String Power = 2 x 4955W = 9910W or 9.9kW
OR Array Power = Array Vmpp x Array Impp = 647.7 x 15.3 = 9.9kW
Either method of arriving at Array Power is OK.
For interest I can calculate the average string efficiency: Module area = 21 panels x 1.5m2 = 31.5m2, at 1kw/m2 (STC) Irradiance Efficiency = Power output / ( module area x Irradiance ) = 4.955 / (31.5 x 1) = 15.7%
Simillary average cell output at 1kw/m2 irradiance = 4955 / 21 panels per string = 236W. This demonstartes how much the 225W Solon panels drag the whole system power output down. It does give me good scope to upgrade in future by replacing them with 250W or ideally 270W panels.
This is a much simpler process when all panels are the same! In that case the panel power can just be multiplied by the number of panels eg if I had 18 x 270W panels the power would be 4860W.
There is no theoretical limit to the number of strings in an array, If I had another 21 panels I could make a 15kW array. But take note of how the array current increases, with 3 strings the array current would be 3 x 7.65= 23A. Check with your pump supplier if there are any maximum current issues.
Also note the fuse requirements, the spec sheet for the Powerwave recommends a 15A fuse. As my 2 combined strings are above 15A I have put the fuse in the string before combining ie I have 2 fuses (string fuses) instead of 1 array fuse. In solar work fuses are much better than circuit breakers as they are faster acting and give much better protection to everything in the circuit.
It does not matter what panels you make use of. Just copy this method to calculate the voltage, current and power. You cannot just add up the rated (nominal power) of each panel when they are different.
The best tip for putting strings together using different panels is try to find panels with very similar Impp. This will require the same number of cells- that is you can't easily mix 60 cell panels with 72 cell panels, etc. Some manufacturers have higher Vmpp and lower Impp even in the same panel size to others. So look at the spec sheets of what you are going to buy and get them as closely matched as possible.
Step 15: Roof Mounting or Ground Mounting
Solar panels are mounted on rails using clamps. There are an enormous number of different rail and clamp systems available (with virtually no interchangeability between systems).
Before you chose a rail system though you need to decide on ground mount or roof mount. If you have a structure near your solar pumping site then this may be perfect for mounting panels on. In which case you would use a roof mount system.
I will not cover tracking systems- while they increase the systems output (mainly in summer) the additional cost and complexity is currently generally not worth the return- it is cheaper to add more panels or extra arrays with a different orientation.
Roof Mount
Roof mount rails are a lot smaller in size, and a lot cheaper to buy, than groundmount, this is because they are lighter and need to be supported at regular intervals on the roof- often 900-1200mm between rail supports. Each rail system has instructions available on how to install depending on the region of Australia you are in (cyclonic regions have more supports than elsewhere).
If your existing roof does not have the right pitch, you can install a tilt frame to fit rails to. These are adjustable and enable you to set the panels at pretty much any angle you desire. They are available commercially or you could make them yourself.
One thing to check is that your roof can take all the additional weight of panels, rails and frames, this may be in the order of 24kg/ panel or 240kg/10 panels. If in doubt consult a structural engineer. If using tilt frames the panels may also act as a "sail" and create uplift that could tear the roof off, again, if in doubt seek the advice of a structural engineer.
Roof mount has many advantages- it is usually high above the ground where farm animals can't damage the panels or grass grow up and shade them. The height also reduces the likelihood of overshadowing by nearby obstacles. The cost of roof mount is generally low and installation/maintenance can be easy depending on access and roof pitch.
It may even be worthwhile building a shed to mount solar on when you consider the cost of the groundmount frame and foundations, stock exclusion fencing and weed control.
Cable can be run some distance from the array on a building to the pump- but ensure the cables are large enough to minimise voltage drop, we'll cover this in a subsequent step.
Groundmount
It is not common that a building is perfectly placed and so groundmounting is usually more common. The first two pictures in this step show typical commercial groundmounts. They are available as kits from a variety of vendors. The kits usually consist of galvanised steel screw anchors, tilt frames and heavy duty rails. The further apart the frames are, the more heavy duty the rails need to be. From a cost perspective it is a balancing act between the cost of the rails versus the number of foundations/frames and their cost.
Some things to note are:
- The grass around the groundmount needs to be maintained to stop it growing up and overshadowing- roadbase, mulch, herbicide, mowing and shotcrete are all options.
- If grazing animals are likely to damage the array then exclusion fencing is required and the arrays need to be above/back from the fence so that they are not overshadowed.
- If multiple arrays then the one in front needs to be far enough away from the one behind to prevent overshadowing during the times of operation you need. the below website calculates solar altitude and azimuth angles for any time and location:
https://www.esrl.noaa.gov/gmd/grad/solcalc/azel.ht...
Ground Mount manufacturers provide specifications and drawings for the assembly of their frames.
Step 16: Groundmount Foundations and Weed Management
I chose to build my own hybrid ground/roof mount. The commercial systems are designed to go on level or gently sloping land. To fit my 30 degree dam bank I would have had to modify them. They are also reasonably costly.
I'll cover my design in detail- the principles are very similar to commercial mounting systems and you may design your own like me or use the process to install a commercial system. My system is quite inexpensive as everything is recycled. I used both ground screw anchors and concrete foundations.
Basically I made steel frames that fitted the foundations (both concrete and ground screw). 100x50mm hardwood Timber purlins spanned between the steel frames. The size of the purlins governed the spacing between frames. Corrugated iron roof sheeting was installed over the purlins- this is to protect them from the weather. Then standard roof mount rails were installed on the sheeting before installation of the solar panels.
Foundations
The mass of the array is relatively small- panels, rails, frame and sheeting are about 25kg/m2. The wind had a bigger impact with wind loads being about 2-3x the mass (both lift and downward, depending on wind direction). Wind loads are highly site specific and if you are unsure you should consult a structural engineer.
So the foundations have to take forces in both compression (downward) and tension (upward). I used ground screw anchors for most of the foundations, but could not get enough as the ones I got were a project surplus so I also used concrete foundations. I have covered both so you can use either.
The attached document shows the layout of my foundations. The perimeter is the foundations for the fence and the 3583mm spaced piers are the array foundations. Having setup the timber profile and string lines in step 12 Solar Array Sizing and Location made it easy to measure out and mark the locations for each pier/footing.
The first 3 pictures in this step show the screw anchors (compared with star posts for scale) and their installation. In soft ground they will just screw in using a hydraulic auger motor on the front end loader of a tractor. I made a steel key that fitted the auger and the top of the ground screw. A helper is essential to position and guide your alignment. In harder ground a small pilot hole (about 100mm) will need to be be bored.
Screw anchors are near impossible to align perfectly. They wobble as they go in, hit stones and roots and deflect and you need to stop immediately that the height is right. It is not good practice to unscrew them to get them higher. So if using screw anchors allow for around +-100mm alignment to plan. You can see the big flange on top of the anchor- this is to help with misalignment by giving lots of room to align the structure on top. In my case I installed the ground screws before fabricating the frames, I measured the level and position of each screw set and adjusted my frames to fit.
Ground screws are fast and relatively simple, but being galvanised steel in ground they will corrode. This depends on the moisture and soil pH at your location. In my case I expect >60 years from them.
An alternative idea I have seen to overcome both corrosion alignment is to bore a larger hole of 200-300mm about 3/4 the depth of the screw. Then screw the anchor in and align it by pushing the top around (try and keep the top level- if you need to push it to far it will go out of level). Once aligned fill the hole with concrete. The same could be achieved using some similar length 80-100NB medium or heavy walled galvanised pipe with some cross members welded on to prevent pull out- just drive them in with a sledge hammer, align and concrete.
As I did not have enough ground screws I had to make some concrete footings. These have the benefit of being much longer lasting, but they are more time consuming and expensive to make. The next 3 photos show the reinforcing cage I made with anchor bolts welded to it.
A formwork is made around the footing hole and the cage suspended in it by the anchor bolts. A steel plate keeps the anchor bolts firmly in place. This plate was removed once the concrete was set and used as the baseplate for the frame. This is an approach to making cast in anchors. These are essential in foundation situations where there are large loads as retrofitted anchors (eg mechanical or chemical) often cannot handle the loads and/or trap moisture and corrode.
Weed Management
As I have grasses that could easily grow to a height that can overshadow a groundmount array, I decided to apply shotcrete around the array. The last 3 photos in this step show using a Render Sprayer. This is a device for spraying render onto walls- it uses compressed air. Simply connect the compressed air and dip the hopper in a wheelbarrow of mortar, aim and pull the trigger. As the mortar hits the surface at velocity air is forced out and the mortar is compacted.
The mortar mix I used was 5 coarse river sand (pebbles to about 4mm dia) to one cement with MP47 fibres (the coarse ones 47mm long) added at a rate of 30kg/m3 and the Micropoly fibres (fine ones) added at about half this rate. The fibres need to be added when the mix is nearly finished as they can "furball" in the mixer if left too long. There are longer fibres (65mm) but these will not pass through my small render sprayer. The longer fibres are used in commercial shotcreting.
The fibres act as reinforcement with the longer ones preventing macro cracks and the finer ones the micro cracks. They are perfect for a job like this on uneven ground where steel reinforcement can't be fitted. The finished surface is quite thin, about 30-40mm thick.
Outside the array fence is pasture grass. If this is not grazed then I need to run the tractor and topper through it to prevent it from overshadowing the array.
Step 17: Ground Mount Frames and Assembly
I made my frames using 32NB heavy walled galvanised pipe. I surveyed the location of each pair of footings and adjusted the frame fabrication to suit.
They cleats on the frame are spaced to suit the solar rails, for my panels that is 800mm apart. The top member is supported by knee braces back to the legs at these load positions. This reinforces the top member while also providing bracing in this plane.The final weld on the knee braces was made on site after fitting- this enabled a little bit of adjustment to fit the foundations.
Most of these frames I simply stood up on the ground screws, and with a helper aligning them to vertical with a spirit level, I welded in position, then welded off the knee brace.
The concrete footing I simply placed the baseplates on the footings and tightened the nuts, then welded the frame in place.
Following this the purlins were bolted in. For me they are hardwood 100x50mm. The static and dynamic (wind) loads in my case determined these were good for a 4m span. You can use timber or steel, the section size just needs to be adjusted for the loads and span. Blocking (or bridging) is fitted between the purlins to prevent them twisting out of plane under load. The deeper the purlin and higher the load the more rows of briding required. I just needed a single row mid span, but 2 or 3 rows is not uncommon.
Note the use of bracing. At each end of the array there is a bracing bay. It has hoop iron speed brace over the purlins and M12 threaded rod braces on the front and back walls. The bracing adds stability to the structure, removing flexibility. The structure must be stiff to prevent movement placing loads on the glass solar panels.
I fitted a sheet of stainless in one bay as a mount for the inverter and electrical gear. You could use mild steel or plywood. In all parts of the frame I simply used the materials I had available or could get cheaply from places such as the scrap metal dealer. In total the materials for the ground mount structure including ground screws and shotcreting cost $1845. Just to buy a groundmount frame for 10kw currently costs about $4,000 and does not include the ground screws- they are around $100-$200 each. So there is a significant saving to be made using your own labour and materials you can find around.
The final task in this step is to fit the roof sheeting. I sheeted both the roof and back wall. The back wall I did to reduce the uplift forces of the wind getting under the back of the array and to provide more shelter for the electrical equipment. The roof was sheeted to prevent rain from causing deterioration of my timber purlins. Sheeting of the structure is not essential depending on the materials you make your structure from.
Step 18: A Short Note on Fencing
You may be fortunate and not require fencing, for instance your array is high enough that animals cannot reach it or you don't have animals to contend with.
In my case I have the worst imaginable, cattle and the wife's horses to contend with. Both are curious and seem to develop itches in places that only sharp edges can scratch effectively. I am sure they would decide that the edges and corners of solar panels were made for their own private pleasure if they were ever allowed to experience them. Given the animals strength this would very quickly destroy all the panels of the array within scratching reach.
To avoid this I fenced my array out. It was quite a significant project cost at $5,386. The high value of the asset means it deserves high strength fencing- one animal getting through the fence on just one occasion would likely do tremendous damage. So a wire fence really is not strong enough, generally build the fence to a similar quality that you would build your animal yards.
I was pricing up cattle rails and panels when I came across used fence panels off a bridge. They were priced very attractively at AUD$130 each for 2.6m lengths. The material cost was about the same as buying the oval cattle rail and posts to fix it to or pre-fabricated cattle panels. They are perhaps excessive in strength for this job. It is worth hunting around scrap yards and the internet to try and find suitable materials to keep project costs down.
Again the relatively high cost of fencing makes it preferable to have a roof mount with the panels out of reach- perhaps a shelter shed for the animals to get in under, provided the posts will take the load of them rubbing against them.
The constraints around fencing are:
- Ensure that the fence height to the east, north and west is lower than the array to prevent overshadowing
- Ensure you have access between you fence and the array to maintain the array (more in maintenance)
- Ensure the fence will be adequate to keep the pest species you have away from your array.
As I have a full, heavy duty steel fence around my array I did one more thing with it. I earth bonded each fence panel together with copper busbar using stainless bolts tapped into the steel. The photo in the next step showing the earth rod also shows the busbar connection.
While this is not required under any standard, I live in an area that has a very high lightning intensity. The steel cage around my array makes a very attractive target and without earthing, lightning would likely arc from the fence to the earthed array and/or through the concrete footing to earth. By earthing the system I am providing some degree of area protection from lightning. This is covered more in Step 24 Risks.
Step 19: Installing Solar Rails and Panels
Solar rails come in all shapes, sizes and styles. Generally they can be divided into ground or roof mount types. Ground mount are heavy rails designed for long spans between supports. This is to minimise the number of supports required. These rails are quite costly and they are difficult to obtain second hand as there just are not the number of ground mount systems being replaced that there are roof mount.
Roof mount rails new are currently somewhere between AUD$5-$15/m. 2 Rails are needed per panel so for a 10kW system about 88m of rail is needed costing $440-$1320. They come in various lengths, typically 2.1, 3.15 and 4.2m, but can be easily cut to any length you need. Before buying new rails check the price of fittings as cheap rail may have expensive fittings. The following are needed:
Splices: Rails in a run need to be joined together with splices to give them strength and electrical continuity
Mounts: Come as metal roof or tile roof (roof hooks). They need to be spaced as per the rail manufacturers specification (typically 800-1200mm apart) and depends on your wind region ie cyclonic they have to be closer together again. Mounts usually come complete with roofing screw, rubber isolating foot and rail nut/bolt.
Grounding clip: This allows the rails to be electrically joined with earth cable and bonded to earth, ensuring that if there is a fault in the system that makes the panels and rails live, then it is grounded for safety. It also assists with reducing the impact of lightning strikes.
Panel clamps: End clamps are required at the ends to hold the panels down and mid clamps between panels. Make sure that the clamp size matches your panel thickness as there are different sizes eg 35mm, 40mm, etc.
I chose to use roof mount as I could get the rails and fittings extremely cheaply second hand- all the rails plus fittings cost AUD$434 (or $43.40/kW). In many cases I got given the rails and fittings when buying used panels. The biggest problem was that there was always some fittings missing and I had to figure out what type of rail I had and then seek out fittings to match. This takes a bit of time looking at the internet trying to match the shape of rail you have. Some rail I had to send to the scrap dealer as new fittings were just unavailable.
The first step in setting up rails is to work out the distance apart they need to be. As a general rule only one quarter of the panel should overhang the rail, so as panels are 1640 this means 410mm overhang and 820mm between rails. In my system I chose to mount the panels in "portrait", that is long edge parallel to slope. Your site may better suit "landscape" that is short edge parallel to slope. Check the panel manufacturer specification as they may require certain mounting widths.
Generally the rails run at 90 degrees to the long edge, so if you mount in landscape the rails will run parallel to the roof sheeting. This is the most efficient use of rails, but there is no rule about this. Panels can be mounted on their short ends, again allow no more than one quarter overhang.
The first picture in this step shows the finished rails. I used 2 different types. As there is no splice between the different rail types I have put roof mounts at the adjoining ends. The second picture shows this.The rails were connected electrically using cable and clamps.
To install the rails put the end roof mount brackets up. Then stretch a stringline taunt between them. Mark out the distance between supports and screw down each mount using the screw type recommended by the rail system manufacturer. You don't need to worry about rail lengths as splices will provide a structural join between rails. However if you can't splice rails as per when rails change types, then ensure you have a mount at the end.
Next fit the rail to the mount. In most systems the nut turns sideways and you can slip the rail over the nut. Turn the nut 90 degrees and start tightening the bolt. This step is where the string line is handy for level. The roof will vary a little in height. Each mount has adjustment in it, so first do one end and then the other, adjusting them to string line height, then tighten the nuts through the centre. Continue with each rail- first splicing the end, leveling the other and tightening off through the centre. It pays to look along the rail from one end to make sure you don't have a sag in the centre due to the stringline not being tight enough. If so tighten it and adjust the centre rails up.
A very important step is earth bonding. This needs to be to standards AS/NZS 5033:2014 Installation and safety requirements for photovoltaic (PV) arrays.
This will change over time as new versions are issued and will be different in different countries. They key principles are:
- The earth system is continuous- that is any one part of the system is bonded to any other so that if a fault occurs all parts are at the same voltage (equipotential). A good example here is that as I have two rail systems and they are not spliced together mechanically I electrically bonded them using grounding clips and cable.
- The earth system is grounded at one point- this ensures that if the ground potential is different between two points, then the roof system is earthed at one and the same as the earth at that point.
There are many lesser rules which need to be followed such as the use of stainless steel connectors, etc.
One of the pictures in this step shows the central earth for this system, this is a 1440mm long copper clad steel rod driven into the ground. The ground should be damp, if the ground is dry the rod must be longer. In my case this is a very damp location at the foot of the dam- almost a swamp. All the system earth cables are tied to this, even the steel fence surrounding the array. More on that later in Step 24 Risks.
Once the earthing of the system is complete, the panels can be installed. The rails should be straight so you can measure off the rail to get the panel positioned correctly. I find a stringline just gets in the way- the panels are heavy and large (awkward). A helper or two is invaluable here to take panels from a stack and hand them to someone who is clamping them down and on steeper angles holding the panel in place until it is clamped.
Install the bottom row first, this can support the upper rows and stop them sliding down the array.
Start with end clamps at one end- clamp in your first panel leaving the leads sticking out the sides. I have not found a system yet that will reliably hold a panel at 30 degrees slope with just clamps on one side. So while holding this panel in position, slide the next one close. Join the cables (+ positive to - negative). Fit the mid clamps and push the panels tight together. Now while holding both panels, tighten the mid clamp. This first panel is now secure and the second can be supported while the third is installed. Repeat until all panels are installed.
There may be systems out there that reliably hold on a pair of clamps, or your array may be on less slope and you don't have the problem. But keep in mind the last thing you want is a panel sliding off and breaking.
The next step covers wiring up the system.
Step 20: Wiring the System
At this point you have an array with positive and negative cables from each end. Onto a spare length of rail (about 300mm) at one end fit an array isolator. This is a switch that turns the power of the array off. There are brackets available with these switches to allow you to fit them to rails.
From the array isolator the cables need to run to the fuses. The cable length governs the size of the cable required. Generally for array's 4mm2 DC solar wire is used and is commonly available. 6mm2 is also easily available but more costly.
Checking the calculation:
4mm2 copper resistance = 5.6 ohms/km (data from cable suppliers, sometimes stamped on the cable sheath)
for 56m R= 56/1000 x 5.6 = 0.31 ohms (this is the length through the solar panels that are 4mm2 cable and back to the fuse)
Current I =7.65A
Ohms law: Resistance R = Voltage V/ Current I
0.31 = V / 7.65
V= 2.4V
With a system voltage of 647.7V this is a loss of just 2.4 / 647.7 x 100 = 0.37% so insignificant compared with losses due to temperature effects.
Note that all electrical work must be done in accordance with Australian Standards AS/NZS 3000:2018 Electrical Installations or similar for different countries. If you are not competent with electrical work(competent being defined as properly accredited in your jurisdiction), then utilise a licensed electrician. In many locations around the world electrical work may only be done by licensed tradespeople (eg NSW, Australia this applies). For NSW rules see:
https://www.fairtrading.nsw.gov.au/housing-and-pro...
The electrical schematic in this step displays in simple form how the system is wired up, from the array through to the pump motor. The first photo also shows the major electrical components- they don't look like much, just a a series of cabinets. Each component is described in detail below:
- HRC Fuses- (High Rupturing Capacity). These are a cartridge type fuse. Fuses are a much better choice than circuit breakers as they are more sensitive and will trip faster preventing damage to equipment more than circuit breakers will. They need to be sized according to the panel and inverter requirements. In this case they are 16A, 500V. (A very close match for the 15A maximum required by the panels). These came with the inverter system and if they fail I will replace them with 15A fuses. The 1A difference is probably not significant in this case. Fuses work by limiting the current, we know that the current in this system is normally 7.65A but may rise towards 10A in short circuit, 16A should only occur if the two arrays combine or there is some electromagnetic pulse (EMP) such as a lightning strike. The voltage rating is simply the voltage the fuse will withstand without arcing after failure. In this system 1000V fuses would probably be a better choice.
- Combiner - after the fuses the power from both arrays is combined. This is simply a terminal block that takes 2 inputs and combines them to one, 2 positives together, 2 negatives together. The effect of this is to double the current but voltage stays the same.
- Surge Diverters- It is advisable to have surge diverters on every electrical cable around valuable electronic gear. These protect the equipment from EMP. EMP is a very high voltage but for an extremely short duration pulse. They occur as a result of lightning, solar flares and high altitude nuclear blasts. The last is very hard to protect against due to the nature of the pulse, but hopefully never an issue. The first 2 are a reasonable risk and for me lightning especially. Lightning does not need to actually strike the array to generate a pulse, a nearby strike will cause a pulse and the array and all cables can act as an antenna. Think of surge diverters as a "pressure relief" they connect the system to earth when the voltage is too high and drain it to earth. They come in different ratings, these ones are 1100V, ie they will allow 1100V to pass but any voltage above that they will drain to earth.
- Earth- There should be one main earth stake, it's length needs to be adequate to at all times be well embedded in damp ground (ie the dryer the ground, the longer the stake) Multiple stakes may be used but they must be bonded (ie joined by conductors) to each other. Generally each earth wire is run to a linkage terminal block and from that block a cable is run to the earth stake. All metallic components should be bonded to the earth system- this ensures that in the event of a fault all parts are earthed and at the same potential. It is very dangerous not to have a proper earth system or some parts earthed and others not as this causes a potential difference between these elements that may cause electric shock, fire or damage due to discharge arcing betwenn components.
- Main Switch- This switch simply isolates the inverter and downstream.
- Inverter- This converts the direct current (DC) input to three phase alternating current (AC) output. (Other systems use a DC to DC converter that takes the varying current and voltage of the array and converts it to a controlled DC output). The inverter also carries the system smarts- that is it does power management and controls the system. The inverter I have responds to diminishing solar input by lowering the output frequency from 50Hz standard- as the frequency reduces the motor turns slower (pumping less) and its power requirement reduces to match the available power. There are also low voltage control signals to the inverter from devices such as pressure and flow switches which I will cover in Step 21 Control System and Valving.
- Shielded cable- The AC cable connecting the inverter and the sine wave filter is shielded. The primary reason for this is that the inverter output is "noisy", it is not a smooth sine wave like what is available from electricity supply, it is more a square wave with lots of spikes on it. These spikes generate electromagnetic waves (EMP in miniature) which disturb electronic equipment, and the inverter is electronic equipment. So a feedback loop could develop and the power form continue to degrade. Shielded cable simply has a metal braid around it which is earthed, so the generated waves are earthed and cannot radiate to interfere with equipment.
- Sine Wave Filter- This takes the noisy signal from the inverter and "cleans it up" producing a much neater and controlled sine wave. This reduces electromagnetic interference from the output cable. More importantly it provides a steady, smooth frequency wave for the 3 phase pump motor. While the motor will operate on a noisy wave, it will be constantly accelerating and slowing in response to the input signal and can be expected to have a shorter life (as well as make more noise). For more information about Sine Wave Filters see:
- http://files.danfoss.com/download/Drives/DKDDPFO61...
- Output RCD (residual current device)- , this is required by AS/NZS 3000. These use a core balance transformer so if there is any current imbalance (ie leakage of current) the device trips and cuts off supply. Leakage means leakage to earth- this could be say a damaged wire and this is a shock hazard for anyone touching it. As such the RCD provides excellent personal protection. In this 3 phase system (no neutral) all phases must balance, otherwise the core balance transformer will trip to RCD. Care must be taken in choosing the RCD for this type of system (no neutral) as the test button must be wired between phases and not phase to neutral. If the RCD test button is wired between phase and neutral it will require a resistor installed between the neutral and a different active phase to prevent failure of the test system. (If your system has a neutral this is not an issue).
https://controllogic.com.au/blog/post/how-to-wire-an-rcd-with-no-neutral-line provides more detail.
- Output surge diverter- While this is on the output of the Sine Wave Filter, it is not to protect the equipment further down the line from solar output. It is to protect the sine wave filter and inverter from an electromagnetic pulse (lightning strike) traveling back along the cable from the pump. Cables buried in the ground are sensitive to EMP, a nearby lightning strike will induce a voltage in the line. Given the sensitive nature of the sine wave filter and inverter (and high cost) I have elected to provide some degree of protection, these ones are rated at 380V. You can also install surge diversion at the pump motor to protect it. In my case I have 3 locations that would require protection and the cost is not worth it, the pump motor is fairly hardy, well insulated and relatively low cost to replace. For better protection HRC fuses should also be installed after the surge diverter.
The best option for lightning protection on these cables is to use shielded cable, it has the reverse effect to containing signal noise in the cable, it prevents external EMP from entering the cable. Basically it makes the shielded contents "invisible" to EMP. It is however 2-3 times more expensive than regular cable. If your system is in an area of higher lightning activity (wet tropics, escarpment, etc) then shielded cable is probably well worth the expense. I'll cover more on lighting risk in step 24.
I have 3 switched outlets in my system, one close by at the dam, one a little further away at the bore and the last and furthest away is at the creek. One of the pictures in this step shows the riser at the creek- the power outlet as well as pump delivery hose and the creek flow switch.
Sizing the cable from the sine wave filter to the pump is based on designing for the allowable voltage drop- just like water losing pressure due to friction flowing in pipes, electricity drops voltage. This depends on the length of the cables and cross sectional area of the conductor. The calculation is covered in AS/NZS3008:2017 Electrical Installations. The simple online calculator below is very good, it also has a more detailed calculator for AS/NZS3008:
https://www.jcalc.net/voltage-drop-calculator-as30...
Note that some pump suppliers provide their own tool for cable sizing. The allowable voltage drop for the motor I used is 3%, the longest length of cable from the sine wave filter to the pump is 100m. The pump voltage is 380V and current 5.7A. Using the calculator at the link above it recommends 2.5mm2 cable giving a 2.34% (8.9V) drop. So the specification for my cable is 2.5mm2 , 3 core and earth PVC double insulated cable. This cable needs to be installed in conduit to protect it from crush damage. You can get armoured cable for direct burial but it is more difficult to handle and more expensive.
The last picture in this section shows the trenches excavated for the cables and pipe. Australian Standards require normal burial of electrical cable to be 600mm deep, but under ploughed ground this is to be increased to 1000mm. My trenches are 1000mm deep and the power plus control cables (both in separate conduit) are buried at this depth. The trench was backfilled to 600mm deep and the water pipe buried. I personally don't like water pipe too deep as it becomes too hard to access for any future repairs.
The next step covers the design of the control circuits.
Step 21: Control System and Valving
Every system is different in what controls are required. This step discusses what controls I used as they are standard and probably of use in the majority of systems.
Electrical Logic Controls
The first activity to do is to work out operating modes:
Mode 1: Irrigation from creek or dam- constant flow at 76m head 1.54L/s
Mode 2: Transfer from Creek to Dam, constant flow at 50m head and 2.5L/s
Mode 3: Stock watering from creek, bore or dam, intermittent flow (on demand) at maximum 60m head (to protect old pipes with 600kPa pressure limit)
The next activity is to determine what pump protection is required, This can include overcurrent, over temperature, excessive starts, run dry, water level switches, etc amongst many. The largest risk I consider is run dry protection. Pumps can run dry if the water source dries up, the pump suction is blocked or an outlet valve is closed (in which case the pump will heat the water inside until it evaporates/boils and then run dry). There are sensors that can be installed on the pump for this, but I prefer flow switches. They are simply a little metal reed placed in the pipe and water moving past them pushes them and activates a switch. When the flow stops the switch changes state.
From these requirements it is clear that I need:
A) Pressure switch control to turn pump on when stock are drinking and off when system pressure returns to maximum 60m. The pressure switch is variable using a screw and spring system to adjust the cut in and out pressures.
B) Flow switch control to ensure that water is flowing from the pump (Note that flow switches only work in one direction). The flow switches are adjustable using a screw and spring to adjust the amount of flow necessary to activate them.
The first diagram shows the logic control. A single pressure switch and two flow switches are wired into the digital inputs of the inverter. Digital inputs simply work between two states High=1 and Low =0, With my system 0 to 5V registers as Low and 18-30V registers as high. While the schematic shows a single line between the inverter and switch, there is in reality two wires. One wire provides the signal (24V DC) and the second return wire from the switch to complete the circuit.
So if the pressure/flow switch is closed then the signal is High and switch open, signal is low.
As I have multiple supply points I need multiple flow switches. I can use one to detect flow from the bore or dam, but need a second to detect flow from the creek. So I have an external changeover switch to select which sensor is used at any given time.
Cable sizing for sensors uses the same calculator as in the previous step, except now the input is 24VDC, 0.02A. The voltage drop is not as critical as there is a very wide band so say 5%. Over 100m of cable length it recommends 1mm2 cable, this has a 0.1V (0.42%) drop which is negligible. This is small because the current is tiny. Generally 1mm2 cable is the minimum used in electrical wiring- below this is electronics. I used 1.5mm2, simply because I had a lot of it available, just twin and earth double insulated wire used for lighting circuits.
It is buried in conduit and placed as far from the power cable as possible. The reason for this is that the AC current in the power cable can induce current in the signal cable (another reason to use shielded drive cable). This is not likely to cause a problem in this system as the digital inputs have a very wide tolerance of 5-18V to change signal state. This can be a problem in long runs with power and signal cables close (in the same conduit) and in particular with analog inputs.
I have not used any analog inputs, but they in this system would be 0-10V and could be used for say an external speed input controlling pump speed. This would be easily interfered with by induced current from the power cable so large cable separation or use of shielded drive cable or signal cable would be essential.
The buried cables of the control system are just as vulnerable to the EMP of a lightning strike as the power cables. To mitigate this I have installed surge diverters (30V nominal) just before they enter the inverter.
Valving
Just as important as the electrical logic control is the valving, these two work together. The second diagram is a P&ID or process and instrumentation diagram. It shows where each valve fits in relation to the logic controls.
To explain this I'll work through from left to right:
- First valve from the dam is a non return valve. I use these wherever the pump connects (Dam, Bore and Creek) the reason for it is that I have had a bad experience of line pressure turning a pump impeller backwards when it had stopped due to leakage through the footvalve. The impeller unscrewed the nut holding it in place, fell off and ruined the pump. So now to prevent backflow from the system I use a non return valve where the pump connects.
- I also use an isolation valve at each outlet so that when it is not in use it can be properly shutoff. Non return valves have the problem that when the system drops pressure they can be easily opened. Objects can get in and then cause problems in the system or cause the non return valve to fail. I had one fail once due to a large frog being trapped in the flap of the valve and wedging it open.
- The next valve is return to dam. This is a globe valve, this is simply a large version of a garden tap with a washer that lifts proportional to the number of turns you open the handle. It is used to regulate pressure return to the dam and ensure that the system pressure remains around 50m at maximum flow- the minimum the pump I have should run is 40m, below this the impellers can lift and damage the pump.
- Branching off after this is a line to a pressure tank. It has ball valves both sides, this enables it to be drained and the air pressure tested without draining the system. The pressure tank takes shocks out of the system and also stops pressure oscillation- for instance if the irrigator has reached end of run and shutoff but has some leakage then the pressure switch control will rapidly turn the pump on and off. The pressure tank slows this down from every few seconds to around every 1.25 minutes.Check with your pump supplier the maximum number of permissible pump starts per hour.
- The vacuum relief valve is intended to break siphon when irrigating from the dam. If the irrigator ends the day halfway across a run then without this valve water will siphon out of the dam and create an enormous puddle overnight. The vacuum relief valve opens when pressure drops and lets air into the system. It must be above the dam water level and ideally on the highest point in the system.(eg top of the dam bank)
- The pressure gauge is installed next to the pressure switch and very close to the inverter. This enables manual reading of pressure for setting the pressure switch cut in and out as well as globe valve at the dam.
- At the bore there is a manifold of valves that allows for flow of water in from the bore or dam to trigger the flow switch, but as flow switches can be damaged by operating in reverse (bends the steel reed) there is a bypass circuit to enable water from the creek to the dam to go around the flow switch.
- This system then tees into the existing irrigation system which is isolated with a valve to enable filling of the dam from the creek.
- The next valves separate the stock watering system.
- The last in this system is the creek manifold consisting of an isolation valve , the creek flow switch, another pressure gauge and non return valve. This pressure gauge is simply to provide remote monitoring of the pump when installed in the creek- to check for changes which could indicate partial suction blockage, delivery hose damage, etc.
This step completes all the major steps for building your system. The next step discusses testing and commissioning your system.
Step 22: Testing and Commissioning
This is quite a complex system with lots of individual parts, so testing and commissioning to make sure it all works is essential. It is much easier to break this down into individual parts or sub-assemblies such as Array, electrical logic controls, Inverter and valving/pipe system.
Array Testing
With new panels array testing is probably redundant. There is extremely high confidence leaving the factory that they will work and simply testing open circuit voltage and short circuit current is adequate. However with used panels this may be more important.
The easiest way to test the array is connect it directly to a purely resistive load, Large resistors can be purchased, but they are expensive an old stove element or electric heater element is a reasonable substitute. They are cheap (free even), simple and no concern if you burn them out, and available in ratings close to what is needed for measuring strings.Note that this test, like all electrical work, is only to be conducted by a competent person (as previously defined). Whilst an electric shock cannot be obtained from the elements the exposed uninsulated connections are live, a complete stove top with the connections enclosed is better than the singular elements used in the photo shown here. In this test the necessary current and voltage measurements were taken several meters away from the elements. The elements themselves were barricaded off and personel excluded from the area so that the exposed terminals could not be touched by anyone. All connection and disconnection was performed after the system had been fully isolated. The photo was taken immediately after power had been isolated.
A load must be used to test current and voltage, short circuit and open circuit tests are not truly indicative of how the system performs when a load is applied. Inductive loads such as motors are challenging as a test load because their voltage and current changes with the applied load.
From previous steps we know that each of my arrays have Vmpp= 647.7V, Impp= 7.65A, String Power = 4955W at 1kW/m2 Irradiance. Using Ohms law the size of resistance that will match the Maximum Power Point is R=V / I = 647.7 / 7.65 = 84 ohms. This is called the Characteristic Resistance (Rch) of the array, applying this resistance will result in the system working at its' maximum power point.
I managed to find two hotplates of 1250W each rated 240V, Power = V x I so I = P / V = 5.2A. Resistance = V / I so R= 240 / 5.2 = 46.1 ohm.
Using these two in series (one after the other) the Resistance = 46.1 + 46.1 = 92.3 ohm, This is close to the optimal 84 ohms for testing of a single array at 1kW/m2 Irradiance. They can also be used singly or in parallel. In Parallel the Resistance is 1 / R = 1 /4 6.1 + 1 / 46.1 so R= 23.1 ohms.
The first photo shows hotplates during testing. They have been earthed in case any part of their metal support frame becomes live- the earth connection will safely ground them. Most importantly keep well clear of the live connections. After this test I started using bricks under them to avoid setting fire to the insulating block of timber supporting them.
The results measured using a clamp meter and based on one array at 11am on the 29th April were:
Array Voltage 600VDC
Array Current 6.85A
Looking at the solar insolation for that time (1:00 am UTC), it is about 0.8kW/m2. I don't have an I-V curve for my strings as they are made of 3 different panel types.
This step would be easy if they were all the same, we would simply divide 600 by the number of array panels (21) = 600 / 21 = 28.5V and then compare how close 28.5V and 7A is to the maximum power point on the 0.8kw/m2 curve or NOCT conditions.
The method for an array of mixed panels is a little more convoluted, from Step 14 Designing Strings of Panels we know:
String efficiency 15.7%
Pmpp = 4955W string (236W per panel in 21 panel string)
Vmpp = 647.7V
Impp = 7.65A
and from above Rch = 84 ohms at 1kW/m2
Calculating the maximum power point at 0.8 kw/m2 P = string area x irraidance x efficiency = 21 panels x 1.5m2 module area per panel x 0.8 x 0.157 = 4.0kw
Typically reducing irradiance from 1kW/m2 to 0.8kW/m2 reduces panel voltage by around 2V, this is just an estimate that we'll apply here:
0.8kW/m2 Vmpp = 647.7 string voltage / 21 panels - 2V = 28.8V per panel Or for the string = 28.8 x 21 = 606V.
With power at 4kW for 0.8kW/m2 then current should be Power = Volts x Current so 4000 = 606 x I, I = 4000 / 606 = 6.6A
0.8kW/m2 Rch = 606/6.6 = 91 ohms so the test load of 92.3 ohms is very close to the estimated ideal load at 0.8kW/m2 irradiance. As a result the measured V and I should be close:
Measured V = 600V, Measured I = 6.85A
The measured and theoretical values are very close- within a few percent, a slight error in my assumption regarding Vmpp at 0.8kW/m2 could easily alter the theoretical result. As such it is reasonable to accept that these panels are working to specification at 0.8kW/m2.
Given the age of some of the panels I had anticipated a result that was more like 7-10% different from the calculated- allowing for the deterioration of cell output through life.
If your test result indicates that the panels are performing significantly worse than expected given their age then it indicates there is some fault, most faults will be picked up by testing Voc and Isc of each panel and inspection as per Step 13, section "Used Panels". If this has not identified poorly performing individual panels then the most likely fault a single panel or a connection.
A good check test is to test each string and compare them all- they should all be the same, it is very unlikely but possible that each string would have the same identical fault.
Firstly make sure there is no dirt or overshadowing on any part of the string and that it is a perfectly clear day. Make sure all your connections are clean and firm. Make sure you have calculated irradiance correctly for the array tilt, orientation and time of day.
If you confirm the above and the fault is not located then test each panel individually. This is a slow and painstaking process. You will need a test load resistance for each different panel type (I would need 3 test loads). The test load is the Rch at the irradiance, eg for the example BP solar panel earlier in Step 13 NOCT (0.8kw/m2) Vmpp = 31.5V and Impp = 4.41, Rch 0.8kW/m2 = 31.5 / 4.41 = 7 ohms. This has to take around 126W, so it is a large resistor, not one of the little ones that handle 5W from an elctronics store. They cost around $30-$50 each. You may be able find old incandescent light bulbs that are suitable. It must be a purely resistive load so LED and compact fluorescent lamps are no good.
Doing this test enables you to find the defective panel that fails under load, remove it from the string and replace.
This test is useful to perform at any time throughout your array life- if you suspect any string, group of panels or panel then you can apply a test load to check their performance. Use the approach above for calculating resistance in series and parallel to establish a test load as close to the mpp at the appropriate irradiance of the group of panels you are testing, and if possible do the test at midday to avoid having to adjust too much for different irradiance.
Wiring Continuity
It is good practice to check all connections and cable terminations and with your multimeter check continuity. While the system is not energised (Note that solar systems are up to 1000V and the risk of electric shock exists), use one probe to inject a small current and the other to receive and signal continuity- usually a beep and a reading of low resistance. If there is no beep or the resistance is high when it shouldn't be then there is a termination fault or some part is open circuit.
Generally you can only test small parts of the circuit, across fuses, through combiner boxes and switches. The more complex components such as the inverter and sine wave filter cannot be tested this way. Surge diverters should be open circuit as they only close when there is a surge.
Megger Test (Insulation Test)
For this test a Megger Insulation Tester is required, most electricians have one of these as it is a required test under Australian Standards for testing installations.
his test applies a voltage to a cable and leakage of voltage from that cable to earth is checked (also phase to phase in 3 phase systems). Supply voltage is not applied during this test- only the voltage applied by the Megger test unit. The test should come back with very high resistance in the Millions of Ohms (ie Mega Ohms). If this is not the case there is a short circuit - note though that in 3 phase motors there is connection between phases, so resistance across the windings of a 3 phase motor will be low.
For my motor phase to phase measures 9.4 ohms and each phase to earth 50 mega (million) ohms. Earth continuity was near perfect, virtually 0 ohms, ie no resiatance to any fault current flowing to earth.
The earth system is also checked to ensure good connection through the system to the earth stake- the resistance to earth should be extremely low as above. High resistance in this means open circuit (no earth continuity) and a dangerous circuit. Resistance in this circuit can result in failure of the earth circuit when a fault is applied- this is dangerous as an electric shock can result, but also arcing and fire can occur.
Just a little note on terminology, I should refer to impedance instead of resistance when discussing AC circuits, but for the sake of simplicity given these systems have both DC and AC I'll use the generic term of resistance.
Supply Voltage
Test using your multimeter that the supply voltage at the pump location is as per expected, that is the design voltage less any cable losses, for my system that is 380V (measured phase to phase rather than phase to earth) less 8.9V cable losses. With no load applied the voltage should be close to 380V, only dropping when the pump is running to around 371V. On my system these were measured at 380V no load and 368V under load which is quite acceptable being only 3% voltage drop. If the actual voltage drop is significantly greater than design (or exceeds 5%) it indicates a problem such as a bad termination (high resistance) or damaged cable (broken cores).
Pump Direction
3 phase AC motors can run in both clockwise and counterclockwise directions. To change rotation direction simply swap any 2 of the phase conductors. Eg if Red wire in L1, White wire in L2 and Blue wire in L3 and the motor runs clockwise, just swap L1 with any other eg White in L1, Red in L2 and Blue in L3 and the motor will run counterclockwise.
DC permanent magnet motors can usually simply be reversed simply by swapping positive and negative wires. Other types of DC motors can be reversed, but you need to follow the manufacturers directions as they are more complex and can be damaged by simply swapping polarity.
If the pump shaft is visible and there is a direction of turn arrow on the casing or in the specifications then momentarily turn the motor on and see that it turns the right way (Note: Most pumps can be run like this momentarily, some pumps should never be run dry- if in doubt check with the manufacturer) Adjust direction using wiring modifications as necessary.
If the pump shaft is not visible, install the pump in water and run briefly- check pressure and flow and record. Use a bucket and time how long it takes to fill the bucket. Reverse the pump and repeat the test. Whichever test gave the higher pressure and flow is the correct rotation direction.
Setting Controls
The inverter or controller will likely need some setting up, this depends on the system you have so follow the manufacturers directions, typically: Maximum motor current, power factor, minimum and maximum frequency, motor speed, ramp up and down times, solar panel power (or voltage). These enable one controller to be customised for a range of different pumps.
The system controls such as flow switches, level switches and pressure switches all need to be adjusted to work properly. Firstly most of these devices can operate as normally open (open circuit) or normally closed (short circuit) think of them as a switch between allowing a signal through so logic is high or "1" or not allowing a signal through, logic is low or "0" . While the device may be like a switch high being on and low being off, logic controllers need to be told what high and low actually means.
Either high or low can be programmed in a controller to mean start or stop. It is handy but not essential to follow a convention such as high means on/run and low means stop. This way helps avoid confusion with different devices.
As I have 2 flow switches and 1 pressure switch I used this system to mean that low from the flow switch meant no flow, so stop. Low from the pressure switch means pressure has reached high setpoint so stop. High in both instances means run. Usually these devices are extra low voltage (24 or 12V DC) so they are quite safe to work with.
Devices need some adjustment to operate properly:
- Flow switch- these are usually a stainless steel "reed" in the pipe, water moving past them in one driection only moves the reed and activates the switch. There is a spring that returns the reed to the no flow position when flow stops. The spring tension needs to be set by adjusting a screw to make it firmer or looser- generally aim for it to activate at the lowest flow you need and deactivate below this. I find they need to be monitored for a little while after installation and need further adjustments.
- Pressure switch- These use a plunger working against a spring. Tightening the spring increases the pressure required to activate the switch. Usually there are two settings maximum and minimum pressure and there is a maximum they can be apart eg 300kPa differential would mean that if the upper is set at 600kPa then the minimum can be no lower than 300kPa. Having a pressure gauge nearby when setting this device is essential- you need to be able to observe the pressure and hear the unit "click"on or off at the desired pressure.
- There are other common sensors such as float switches and level probes- these work on similar principles.
Again a multimeter using continuity mode is useful for commissioning these devices, you can probe the switch and have a helper turn the system on and then adjust the screws until the switch changes state and the multimeter beeps. This is particuallry useful for control devices that are some distance from the control unit and/or those that are silent in operation, and for those of us that are hard of hearing.
Check that the controller receives the signals and does what is required eg stop the pump on no flow, high pressure, tank full, well low, etc. Adjust the logic and or controller until the desired control is achieved.
System Monitoring and final adjustment
The attached document shows some data that I captured at the end of January on a fine clear day (note daylight saving time was active so subtract 1 hour for real time). The output in pressure and irrigator operation is an excellent match to the solar insolation. Given I am using about 10kW of panels for 2.7kW of pump there is maximum response from 9am to about 6pm (8-5 standard time). The shoulders either side of that ramp down due to inadequate insolation to provide maximum power. This is a feature of the Inverter in this Grundfos system- when the solar insolation is inadequate it slows the pump down by reducing frequency and as such extends the time the system is operational, giving around 20 to 30 minutes extra operation in each shoulder period as well as extra operation during cloudy periods.
Analysing some of the data from the commissioning notes, keeping in mind that Vmpp=647.7V for this system (ie it deliveres maximum power when voltage is at or above this figure):
- 6:50pm, 280kPa, 36.3Hz, 1.13kW, VDC = 616V - the system is running below Vmpp but still functioning, albeit poorly for irrigation.
- 6:30pm , 390kPa, 42.3Hz, 1.74kW, VDC = 615V - the system is still below Vmpp but the motor is running faster and using 1.74 - 1.13 = 0.61kW more power ie the controller is trying to keep VDC around 615-620V by increasing or decreasing the load power.
- 9:56am, 560kPa, 50Hz, 2.78kW, VDC = 681V - the panels are still cool and producing far more power than the pump needs and it is running at the maximum power and frequency.
- 8:23am, 380kPa, 39.9Hz, 1.47kW and I'd estimate VDC around 615V
Using the arbitrary orientation and tilt calculator we can see that 8:23am on the 21 January 2020 (7:23 in standard time due to daylight saving or 21:23UTC) Smodule = 0.2105 kW/m2. So an array of area 42 panels x 1.5m2 per panel = 63m2 is receiving 0.2105 x 63 = 13.26kW of irradiance that is being converted at 15.7% efficiency so P output = 13.26 x 0.157 = 2.08kW. This calculation is some 0.61kW greater than what is being recorded at the inverter, however other factors impact this:
- Solar panels usually have lower efficiency at low irradiance, also early in the morning there is likely to be dew that will reflect some of the incoming light- probably atound 2% efficiency reduction to 13.7%
- There are inefficiencies (losses) in the inverter and sine wave filter probably around 5% and 3% respectively and cabling losses (cable + fuses + switches + terminations) of about 2% (10% all up combined)
- It is a time of very rapidly changing irradiance and a small time measurement error on my part (incorrect watch time- usually a few minutes fast) can be a significant error in Irradiance eg 5 min time difference makes 0.018kW/m2 difference or 0.178kW measured power (8.5%) output difference.
So applying 1 and 2, Power at the panels = 0.137 x 13.26 = 1.82kW from the panels, less 10% for system losses P= 1.63kW. This is very close (within 10%) of the reported value, and acceptable given my time inaccuracies.
This test tells me that the system is working correctly, the input power is slightly higher than the pump power and the difference is reasonable given the inefficiencies and uncertainties above. Any result that is this close is a good result.
Further information from this data shows that when the frequency drops below 40Hz the pressure drops below 350kPa. This results in poor irrigator performance, but also the pressure at the pump is around 400kPa (40.7m) at this time- that is 350kPa at the gauge plus another 50kPa in height and friction back to the pump. Given my pump has a lower limit of 40m head, I raised the minimum frequency to 40Hz. This ensured that the pump shuts off before the duty point pressure drops below the rating of the pump.
The minimum frequency will change with task as the pressure in the system changes. In stock watering I can work with a minimum frequency of 35Hz and still achieve 400kPa at the pump. It also changes depending on if the pump is in the bore, creek or dam- in the bore there is a higher static lift - typically 6m versus 4 so the pressure at the gauge can be 2m lower and 40m head is still achieved at the pump.
Ongoing
It is worthwhile to record the settings you have in commissioning. When you change a component in the future it is useful to be able to come back and refer to it later. You can also recheck for changes in system performance that may indicate deterioration of some element or that maintenance is needed.
This step ends the formal part of design and construction of the solar pumping system. The subsequent steps are more general in nature and cover topics such as some ideas on how to launch your pump in a creek or dam, costs and benefits, system maintenance, risks and environmental benefits.
Attachments
Step 23: Pontoons, Jetties and Flying Foxes- Getting Your Pump in the Water.
The best and easiest method of connecting a pump to a water body is a flooded suction- such as an outlet valve from a water tank straight into the pump suction.
This is rare for irrigation on farms, usually the pump will need to draw from a dam, creek or bore. Installing a pump in a bore is very well covered elsewhere and will not be covered here- after all there are very few ways of getting a pump in and out of a bore!
Open water bodies are more challenging, creeks flood and wash away infrastructure, dams usually have very slow tapering bottoms and the pump suction needs to be quite some way out into the dam.
For non submersible pumps the solution is usually a long suction line of heavy walled poly pipe or spiral wound suction hose with a foot valve, strainer and float. These are usually held in position with guy wires or an anchor. In creeks and rivers they are removable but dams are usually permanent.
Submersible pumps are more challenging. The whole pump has to be placed in the water body and usually submersed at least 1m deep, some must be installed vertically or very close to and others allow from vertical to horizontal (but not below, ie upside down) insertion. Any pump type can be a solar pump, but the manufacturers so far have concentrated on multistage submersible pumps as the main market has been for remote water bores. Other types are available but the range is limited at the moment.
For this solar pump project I built a pontoon jetty using recycled floats and catamarans to place and retrieve the pump in the dam and a flying fox to place/retrieve the pump from the creek.
While the dam was near empty during the 2019 drought I also installed a permanent piled jetty at the existing mains electric pump, this carries the suction hose 25m out to the float and makes foot valve maintenance a breeze. Really though, it was something I promised myself that I would do when the dam dried up. Primarily so that when it is full again we can go down there and have a bit of fun swimming in the dam without having to wade through calf deep mud. Also it was a great way to turn a negative into a positive; as our dam dried up and the water level fell I was able to dig more footings in the floor of the dam. So what would normally depress me- the fact we were running out of water for our stock, was no longer such a concern, I could build further out into the dam. A bit of psychological relief for the farmer in drought.
As it was I installed the last footing just as the drought broke and was battling the water flooding my holes while we skidded down the muddy dam bank with barrows of concrete!
So this step will also provide some suggestions on building piled jetties.
Pontoons
A pontoon is a floating structure, it rises and falls with the water level. As such they are a flexible structure and are ideal for dams where there are no currents or waves to deal with. The pontoons that are common around Marina's are generally designed as a large float platform connected by a hinged ramp to an anchor point, piles in the water or concrete on shore. The platform is either guyed by wire rope back to shore or restrained by piles. As marina channels they are installed into tend to have steep sides, they usually only extend out from shore a maximum of 10-15m. They are also designed for attaching vessels to so tend to have a long side parallel to the shore being "T" shaped.
Farm dams often have very flat bottoms and gradually deepen. In my dam I need to get out 25m to ensure I am in the deepest part. As all I am doing is launching a pump I don't need a "T"shape, just a long narrow access walkway to get the pump out and suspended in the water.
The first photo shows the pontoon jetty I built to get the submersible solar pump in the dam. This was built for AUD$3,556 using mostly recycled components. I think a commercially supplied and installed jetty like this would cost around $15,000. So a huge DIY saving.
Starting with the anchor, I built a concrete slab into the dam bank above the high water level of the dam. Into this I fitted M20 stainless cast in anchor bolts to connect the first span of the jetty back to the anchor. These need to be strong as the jetty hinges vertically on them but also any lateral (sideways) forces are taken at this point. Sideways forces occur due to wind, animals rubbing on the jetty, movement on the jetty, etc.
I had to hunt around for a while but found 3 old pontoon floats as well as 3 old catamarans. I have used the pontoon floats in close to the concrete anchor for two reasons:
- 1) They are the hardiest when the dam is empty so are least likely to be damaged sitting on firm ground
- 2) They are not very wide so the jetty will tend to "twist" when walked on over these, the anchor is the firmest place to resist this twist.
The catamarans came as just hulls and needed a bit of work, especially after the horses stomped on them during storage. The holes had to be patched with fibreglass and all joints, the storage lids and even the bungs were all siliconed up to prevent water ingress. Tiny holes (1.5mm dia) were drilled just under the joint of each hull up near the bow to allow them to "breath", and prevent air from expanding and contracting inside and "flexing" the hulls.
The pontoon floats had holes from past impacts in them too and were missing caps. These were all repaired and the caps had little holes in them to let the floats "breath".
In the pictures of this step there is a pair of scrap stainless pipe posts about 15m out from the anchor. As this jetty is 25m long and 1m wide (walkway), it would experience large sideways bending forces if unsupported. These two posts provide lateral support to reduce these stresses. There is still a large load at the anchor but far less than would be without this additional support.
An alternative to posts would be to use guy wires and run them from the farthest pontoon back to the dam bank about 10m either side of the anchor point. This is the only economic approach if your dam is full when constructing your pontoon. The only problem is this impacts more of the dam bank and provides cables that livestock can get tangled in.
As we were in drought (2019) when this was built and the dam almost dry I elected to keep the structure more contained and use these posts instead of guy wires. I put the posts as far out as I could (the further the better) but this was as far as our dam water level fell.
The key to successfully installing posts in dams is the foundation. Far too often people underestimate just how little bearing capacity a dam floor has when submerged. A jetty built during a drought or when the dam is new collapses in the years after the dam fills as the dam floor liquefies from solid ground to soft mud.
Geo-technically a dam floor is one of the worst bases to build upon. The first layer is organic mud- generally black and a very fine silt. This has zero practical bearing capacity as it is fully liquefied sludge when wet. Step one is to excavate this out of the way and expose the clay of the dam floor.
The clay at the surface also has very little bearing capacity when flooded- it swells with moisture and acts as a seal to keep water in the dam.Water penetrates into the clay but as it goes deeper it has less effect on the bearing capacity. That is the deeper the footing is dug the firmer the ground supporting it will be.
Regardless, even damp clay has a very low bearing capacity. I work with 20kPa (kN/m2), this is just a estimate and probably conservative. If your application is critical there are tests that can be performed, but these need to be done in situ (ie flooded dam) rather than dry hole. 20kPa is an extremely low soil bearing capacity, for normal construction soil capacities are greater than 100kPa.
20kPa simply means 20kN/m2 or kilo newtons per square meter. A kilo newton is 1000 newtons which is really just 100kg (approximately) so 20kPa is 20x100= 2000kg/m2 or 2 tonnes per square meter. In simple terms if a load of more than 2 tonnes is applied to an area of 1 square meter, then it will sink into the clay.
The footing I used for the posts is shown in the second picture. The stainless posts pass right through the footing into the clay beneath (for lightning earthing) and have reo bars welded to them to bind them into the concrete and stop them "slipping" through the slab.
The footing is 3.4m long by 0.6m wide so has an area of 2.04m2. It is 0.9m deep at the ends and 0.7m deep through the centre. It has a volume of 1.6m3, concrete has a density of about 2300kg/m3 and so the concrete mass is 3680kg. The pressure exerted by the footing on the dam floor is 36.8kN / 2.04m2 = 18 kPa.
Simply digging or driving the posts into the dam floor while the dam is dry would have resulted in them moving later- slipping deeper into the floor and being pushed sideways by the pressure of the pontoon against it.
Each float of the pontoon is joined using aluminium from the local scrap yard. There was no significant engineering design in this. I simply got what I could and it ranged from 100mm universal beams out of a truck tray to tubes ranging from 50mm nominal bore (NB) to 100mm NB. Span testing was done by laying a pair of members on blocks 1m apart between supports and putting a ply wood deck on top then standing on it to feel how much it deflected. This simulated the pontoon walkway. I adjusted the span length until I was satisfied with deflection- typically I wanted less than 5mm deflection under the weight of me carrying a pump and tools, say 100-150kg all up.
This resulted in spans being made from 2.4m to 3m depending on the aluminium section used.
Aluminium was used for both its corrosion resistance and being lightweight. A pontoon jetty can only carry as much weight as the volume of water displaced by the floats. These small 14'-16' catamarans were only ever designed for around 100-150kg. So the weight of the structure has to be minimised in order to allow one large farmer and pump to walk across it.
As the whole structure has to flex in the vertical direction to accommodate changes in dam level, little waves, etc. I joined floats rigidly in pairs and then hinged them at the ends so that each pair was linked to the next pair with beams that hinged on a single bolt.
This connection experiences a lot of wear at the bolt hole as it is constantly moving. So ensure you use thick plate (I used 13mm aluminium plate for each side of the hinge) or line the hole with pipe to increase the bearing area. Larger bolts are better as again they have a large bearing area minimizing bearing pressure. I used M12 stainless bolts with Nyloc nuts. Locking nuts must be used as the motion will undo regular nuts.
While the main members are directly under the walkway, you can see in the photo additional members about 500mm either side of the walkway. These are in the areas with the largest lateral bending and are there to assist in reducing the bending stresses at these locations.
Before decking the structure was braced. I did this using 3.2mm stainless wire rope tensioned diagonally in an "X" between each float. An eye nut was fitted after the nylocnut on each hinge bolt, into this was fitted a turnbuckle that allowed the wire to be tensioned.
Bracing takes the "slop" out of the structure and makes it all move together so it shares the loads over all the joints rather than the tightest joints taking all the load. It adds strength to the structure by transforming it from simple beams into a horizontal "truss".
The deck was built using fibreglass enviro grate offcuts. I ran out of these and ripped the toungue and groove off some old hardwood floorboards to finish the deck. All were screwed down using stainless hex head screws. The fibreglass is a little on the heavy side and has been used where the large floats are near the concrete anchor. Aluminium decking would be good, but I could not get it in scrap. The timber will require maintenance and replacement over time.
At the far end of the jetty aluminium lugs were built into the catamaran frame to enable the pump to be suspended on floats in the dam. The floats are to keep the weight of the pump independent from the jetty and allow slack wire joining the two to prevent vibrations from the pump transferring into the jetty structure.
Piled Jetty
The piled jetty is perhaps easier to make than a pontoon, but requires access to the dam floor all the way to the end. In my case I was not worried if I got all the way or not as it was just something to do during the drought. As it was I achieved the full 25m needed. The photo showing my old Land Rover parked next to the jetty on the dam floor provides a good sense of the access needed.
The key to footing design is discussed above in the pontoon jetty posts- design for ultra low bearing capacity soils. The footing in this jetty is the same as the pontoon, except smaller being 2m long by 0.5m wide. It is only 500mm thick at the top but penetrates into the clay 500mm at either end. There is about 1300kg of concrete in each footing resulting in a bearing pressure of 13kPa from self weight.
The dimensions of this footing are also to give stability- the jetty is about 3m high and 1m wide so the 2m wide footing provides lateral support- as does the 500mm deep "pile".
The only other difference is that this footing is designed with cast in anchors rather than the stainless pipe passing through it. This was done to enable fabrication of each jetty pier in my workshop and then site fitting to the cast in M20 stainless anchor bolts.
One downside of this is that when the piers are exposed above water level they are at risk of lightning damage, this is discussed in the risks step.
The piers were all made using 100NB scrap stainless pipe with a baseplate welded on and a cross member at the top to keep them spaced. 10mm stainless round bar cross bracing was welded in on site once the piers were installed.
Recycled 250x50mm hardwood beams spanned each frame (the first two spans are 7.5m and the next two are 5.5m). The spans are based on the used timber I had available to me. These were simply lifted into position with the tractor and bolted off to the piers. This structure was engineered to the Australian Timber Structures code AS1720.1.
100x50 blocking (or bridging) was installed between the beams- 2 places in the short spans and 3 places in the long spans to prevent them twisting out of plane. When a load is applied on the top of a deep beam it tends to twist the beam around. By installing diagonal blocks from the top of one beam to the bottom of the other every few meters it makes the pair of beams act as a single large beam.
Recycled fibreglass enviro grate was installed with stainless screws on this jetty over the top of a rubber strip that protects the timber from water pooling on it.
The weight of materials is not so critical in this jetty, but all up the total weight per span of materials and people is not to exceed the allowable soil bearing capacity of 20kPa. In this case as there is 13kPa from self weight the allowable structure and "live" loads is 7kPa, that is 700kg. The structure mass worked out at around 400kg per pier leaving 300kg for the live loads ie people.
Flying Fox
Installing a submersible pump in a creek that floods is somewhat more challenging than installation in a bore or a dam. Some options are:
- Stillage tube: A tube that can be installed into the creek at an angle and allow the pump to slide down the inside into the water. The tube is anchored on land and cantilevered out into the water. On my site the tube would need to be around 10m long, anchoring was a challenge as was the weight of the tube to remove prior to a flood. Also ensuring the pump stayed below water level as the creek level dropped was challenging.
- Well: It is possible to construct a well adjacent to the creek and connect it with a pipe below the creek floor into the creek. This is a good design and fairly robust. But in my situation would require extensive excavation of a creek edge prone to erosion and would probably not be permitted by the authorities.
- Anchor: An anchor such as a block of concrete or steel can be placed in the creek with a buoy to attach the pump to. This works well provided the depth and diameter of the hole keeps the pump in the water as the creek level falls and the buoy drifts downstream from the buoy. There is also the problem of getting the pump to and from the buoy. Wading out may be OK or a boat. Finally the assembly is likely to get washed away in a flood.
- Guy wires: If access can be gained from all sides of the creek then guy wire anchors can be installed about 120 degrees apart on land above the flood zone. A wire from each of the anchors is run to the pump location and a buoy placed there. The pump is attached to the buoy. The system rises and falls with the creek level and remains in the same position. It can be tensioned up to lift above flood level when a flood is coming.
- Ramp: These are traditionally used with non submersible pumps and lower them closer to the water level on a winched carriage, the same can be done with a submersible pump into the water. But these structures are very invasive on the creek bank, prone to damage from floods and may not be permitted by authorities.
Issues with the options above led to my use of a flying fox. My site suits this as the deep hole I pump from is on a bend in the creek, I own one side only- the outside of the bend. So I installed 100x10mm angle galvanised steel posts well out of the flood zone and back from the creek edge. On one end I mounted two boat trailer winches and the other anchor points for the cables.
A 5mm stainless steel cable was run from one winch to the anchor at the other post. A polyester rope passes from the other winch to a pulley at the far anchor and back to another pulley at the winch- forming a continuous loop. The rope is used to pull the pump suspended from the stainless cable into position and back again. Polyester is used as it is far more resistant to degradation by Ultraviolet (UV) light from the sun than other synthetic ropes. It is the type of rope commonly used for boat moorings, look for it in marine stores rather than hardware shops which mostly have polypropylene rope- this degrades in UV light.
A carrier for the pump was made using a light stainless tube and some Dee shackles allowing the assembly to slide on the 5mm cable. The pump is suspended from this with floats. A picture in this step shows the pump just after insertion in the creek. There are a range of commercial "Zip line" systems that are designed for playgrounds and could be adapted to this use instead of making it yourself.
Another photo shows the assembly of the pump and floats before insertion. Firstly the pump is fitted into a sleeve that has been modified with a screen at one end to filter out algae, etc from the creek. It also has a mount for the stainless wire rope made to fit it. The sleeve ensures water flow past the pump motor to keep it cool.
The floats are old 20L plastic drums that have been very well washed and filled with expanding foam (they do leak water slowly past the lid). The floats need to at least equal the pumps mass in displaced water ie my pump is 30kg so I need at least 30L of displaced water- 2x20L drums = 40kg capacity (less a few kilos for the weight of the foam filled drums.
Submersible pumps also must be installed on an angle between vertical and horizontal and never below horizontal. Check with your pump manufacturer what the flatest angle they can be installed at- my Grundfoss is able to go to horizontal. So the floats are setup on different line lengths to maintain the required angle.
The pump suction must also be a minimum level under water to prevent it from sucking air from the surface. For mine this is 1m below water level. The floats achieve the right angle and maintains the depth regardless of creek water level.
Launching and retrieving the pump is simple. Just attach the pump and float assembly to the carrier, the layflat hose and cable to the pump, adjust the winches to have the cable moderately taunt and then start pulling the rope to the right position. This changes every flood with logs and debris being shifted around. Once above the correct position, release the winches until the pump is suspended in the water by the floats.
The embedded videos in this step show the process better than I can describe it.
The benefits of this system are:
- The pump can be easily installed and removed (prior to flood) without getting your feet wet.
- The pump can be positioned anywhere along the catenary of the flying fox to adjust for underwater snags.
- The pump is retained in position and cannot drift off from where it was installed.
- The pump is free to rise and fall with the creek water level.
- All parts of the system are well away from creek edges and out of the flood zone.
The risks are:
- Tree branches falling from overhead and damaging the lines
- Lightning strike and falling overhead powerlines (these go over my site)
- Not lifting the assembly out prior to a flood
The first is managed by maintaining the flying fox catenary as slack as possible for as much of the time as possible. Tension in a wire is proportional to the weight on the wire and the tension pulled into it. This system will take about 1000kg before being damaged, when the stainless wire is tensioned up to be above the flood level its tension will be around 600 kg so it only has an additional capacity of 400kg to absorb falling objects.
I welded stainless 10mm rods to the bottom of the posts before installing them in concrete. That penetrates further into the ground and acts as an earth rod at each of the flying fox posts. This should prevent damage from falling electrical cables or lightning as the system is well earthed.
The final risk is for me to be vigilant and ensure I go down to the creek whenever heavy rains are forecast and extract the pump.
Step 24: Risks: Fire, Flood, Lightning and What Can Go Wrong
A key question before building anything is "What can go Wrong?", after all you don't want to see your investment destroyed or damaged by a predictable event. This section covers the risks that I considered in designing and constructing the solar pump system. You may have other risks on your site to consider.
Fire
We live in a bushfire prone area, last year saw the worst fires on record here. The area where all my equipment is installed is in pasture, so the worst fire it can be threatened with is grass fire. To mitigate this risk I designed as much of the system to be non combustible as possible, the only flammable component is the timber roof purlins and plastic conduit and cables.
The area around the array was coated with spraycrete to suppress weeds and under the array is kept bare earth. So any grass fire cannot get close enough to ignite any of the array materials. The timber purlins are well flashed with metal to prevent wind blown embers getting to them.
Where poly pipes or conduit rise from the ground, concrete has been placed around them to keep grass and flames back.
Fire generated by electrical fault is possible, so cables are in conduit and all equipment is fully enclosed in metal cabinets, so if one part fails eg a fuse blows, it cannot start a fire in nearby grass. Good earthing reduces the risk of electrical arcing causing a fire during an electrical fault.
While this system is not fireproof it is most likely to survive ember attack followed by a grass fire.
Grazing Animals
Large herbivores like cattle and horses get itchy and love to scratch. They also get through wire fences and if contained in a small area such as an array and can't get out may panic and cause damage to the array. I decided to make high pressure fences that the animals could not get through, far enough away from the array that they can't reach the panels to rub or chew on. These fences require no maintenance.
Flood
The creek I am on floods, it has the potential to flood to around the height of the base of the array fence. This is another reason to make the fence surrounding the array and the bore strong, so that any debris such as logs brought down in a flood can't damage the structure. As much infrastructure as possible has been placed above the flood level. In particular all electronic equipment is well out of reach of flood waters.
The main risk is the pump being in the creek- It has to be lifted out using the flying fox prior to the flood and the flying fox tensioned to remain above flood level.
Also the dam level rises up to 500mm above the spillway in extreme floods (eg February 2013). The piled jetty has been built to keep the timber structure out of the water and the stainless piles of the pontoon jetty are high enough to prevent the pontoon floating above and off the piles.
Rain, moisture, dust and insects
Moisture, dust and insect ingress into electronics will destroy them. All electronics should be well sealed against water with IP (Ingress Protection) ratings of at least IP54, IP65 or 66 is better. This means that the equipment is well sealed against moisture and dust. The main cabinets are under shelter of the solar array roof, enhancing their moisture resistance. They have breather holes in the base and these I glued in a fine mesh to keep insects such as ants and wasps out while still allowing air circulation.
Lightning
This is a significant risk. Given every part of the system is electrical the EMP (electromagnetic pulse) of a nearby strike let alone a direct one can do a lot of damage. The risk of lightning depends on where you are located, see the map at the link below:
http://www.lightningsafety.com/nlsi_info/lightning...
I am located on the edge of the 40 days of thunderstorms per year zone of NSW, the highest risk area of Southern Australia. The photo in this step shows the hole from a strike in my paddock about 50m from my house. I witnessed it occur during a thunderstorm on the 16 January 2020. There have been many strikes around and near my farm.
The principles of lightning likelihood are as follows:
- Geographic location, some areas experience more lightning storms than others, the greater the number of storms, the higher the risk
- Site location, the tops of hills are far more at risk than the bottom of valleys
- Structure height relative to nearby objects- the higher the structure relative to objects around it such as buildings and trees, the higher the risk. So an array structure in the middle of a flat paddock is the highest structure and more likely to be struck. Given arrays need to be clear of objects to the north that block sun, they are very likely highly exposed and at risk of lightning strike.
Lightning causes damage in 2 ways, direct strike and EMP. Lightning can best be described as "capricious", there is no way to tell exactly where it will strike. The path it takes varies depending on conditions at any given time. The best protection against a direct strike is good earthing.
Think of lightning as being like the arc in an electric arc welder. When the rod is too close to the job, it sticks and current flows but there is no heat and no arc. When there is a small gap between the electrode and the job the electricity arcs across the gap melting the metal. If the gap is too big the electricity in a welder is insufficient to bridge it.
Lightning is up to 260,000 Volts, so it will bridge any gap or insulation. It is not practical to try and protect from lightning by insulating. Trees are routinely blown apart as they have high resistance but the effect is that the moisture in the tree spontaneously boils to steam and the tree blows itself to pieces.
The best approach is like the "stuck" electrode. Bond everything with equipotential bonding and earth it. A massive voltage can then be transferred to earth safely without damage caused by arcing at high resistance joints. In Step 19 Installing Panels and Rails the last picture shows the bonding of the fence panels using copper busbar and bonding them to the earth stake using 35mm2 copper cable.
As a rule of thumb use bonding materials that have at least 35mm2 of cross sectional area- copper busbar is excellent, cable is good too. Make sure there is excellent contact at joints and no corrosion can get in- eg clean before assembly and then spray zinc rich paint over it. Make sure contact areas are large- if possible 35mm2. Make sure that all metal is connected together in one system so that if lightning strikes one part, then every part is raised to the same potential voltage.
This is like a "bird on a wire" while it sits on a conductor that is all at the same voltage it is safe, once it bridges 2 conductors of different potential then current can flow and it is shocked. The same as the structure- if all parts are at the same potential (voltage) then arcing cannot occur.
Nothing should have a high resistance or a gap that can cause arcing, this will result in significant damage. Like trees concrete is a poor conductor, but lightning is so powerful that if it strikes a structure sitting on concrete it is likely to crack (shatter) the concrete much like it shatters trees. It is worthwhile to ensure that metal structures on concrete are bonded into the earth system. This can even be done in each footing with an earth stake under the footing bonded to the reinforcement mesh and steel structure above.
The posts for the pontoon jetty and flying fox all project through the concrete into wet ground so they can easily earth a strike. The piled jetty however is not earthed, it relies on dam water being around the piles to conduct lightning away. While pure fresh water is an excellent insulator, most water will have some dissolved ions in it, my dam water has a conductivity of only 92uS/cm, so it is not a great earthing system. Had I thought about it I probably would have put an earth stake under each footing and connected an earth cable through the slab to the anchor bolts.
EMP is harder to protect against. Think of EMP as a strong radio wave and every bit of metal an antenna, the longer the bit of metal (eg a wire) the larger the antenna and the more voltage an EMP can induce in the metal. Short runs of cable a meter or two long are not at great risk of lightning induced EMP, but longer lengths such as the field wiring out to the pump or control devices are. Lightning generates EMP whenever it strikes, this EMP can result in voltages high enough to damage electronic equipment even if the strike is some distance from a buried or aerial cable.
The best defence in this case is surge arrestors (or diverters). These are a device like pressure relief valves in hydraulics. Under normal circumstances they are closed, but when the voltage exceeds a certain level (marked on them) they drain the surplus to ground, protecting devices on the other side of them from the high voltage. Generally they are use once only and need to be replaced, they have a colour window on them green "ok" red "replace". They should be used on all cables coming to and from expensive electronic gear like the inverter/controller. Further protection can be achieved with HRC fuses between the surge arrestors and prtotected equipment.
There are no guarantees with lightning, there are just good practices and lack of them. Using good practice reduces the risk of damage, but does not eliminate them.
Hail
Unfortunately not much can be done to protect solar panels from hail. They are made exceptionally tough and properly installed (no more than 1/4 overhang or as directed by the manufacturer) then they will resist most events. Typically they are designed to take a direct blow from 25mm hail traveling at 80kph, given the angle of the array the blow is likely to be glancing and so slightly larger hail may not damage the array in this instance.
However hail has been known to be as big as 150mm in diameter, and nothing practical can be done to protect an array from these bigger events, the chances however are very small.
Other Risks
The above covers the major "natural" risks, this section discusses risks that are man made.
Impact or collision: Farm machinery and the use of implements like slashers, mowers, toppers and pasture mulchers all present the risk of flying stones or machinery impact with the structure or array. Again a good solid fence can stop things like nudges from manouvering. In my case I have soft ground and no rocks so flung objects are unlikely.
Pump Failure: All pumps wear and without maintenance of bearings and seals will eventually fail. Follow the manufacturers recommendations for maintenance of your pump. In particular prevent the pump and motor from dry running and/or overheating. These will destroy a pump very quickly. Things such as loss of suction (water level too low) suction strainer blockage, impeller blockage should all be managed by monitoring and maintenance. Devices such as well level probes, pump temperature probes and flow switches are good insurance to stop the pump if these situations occur.
Solar panel output decay: All panels age, typically they lose on average 0.8% of their output per year. Nothing can be done to prevent this.
Failure of electronic equipment (Inverter, controller, sine wave filter, etc): These should be protected against surges with surge arrestors and overvoltage with HRC fuses. However like all electronics they have a certain life before replacement is necessary. The best approach is to buy equipment from a reputable supplier who offers a long warranty. Note that the warranty is only as good as the vendor, a small vendor may have a great warranty, but if they cease to operate in Australia, then the warranty is worthless. Generally provide the best environment for your electronic gear- dry and dust free, exclude insects and keep it as cool as possible.
The most significant risks with solar are natural, but they can be manged to some extent. Generally solar systems are extremely reliable with a very small number of failures.
Step 25: System Operation and Maintenance
Operation
Operation of the system is simple, basically it should run itself with occasional supervision to make sure pressures and flows are as expected. When there is adequate solar insolation the system operates and then shuts down when inadequate. The Grundfos system I installed ramps up and down dropping to about 40% of full pump output capacity in low light conditions.
The main complexities arise if, like my system, it is to do a range of tasks. For irrigation I need to increase the pressure cutout to 760kPa from the dam filling 450-500kPa or the stock watering 575kPa. I need to switchover flow sensors when moving the pump from the creek to the bore or the dam and I need to adjust valves based on the operation I am doing.
Maintenance
The solar array needs a clean from time to time. The main picture of this step shows cleaning after a few days of dust storms during the 2019 drought. Having a garden tap near your array is very handy and a long handled windscreen cleaner like used on trucks is excellent. Ensure you leave room around your array to do these cleaning tasks.
My array is a high point at the dam and birds enjoyed perching along it and of course pooping on it. This led me to install bird spikes (shown in last picture) along the top (southern) edge. This has largely eliminated the problem, there is the occasional bomb from a low flying duck though.
The array will also grow mould over time, so even if it is otherwise clean, allow to give it a good scrub at least once a year to keep it in top operation.
Rats, mice, possums and pigeons have been known to nest under solar panels. Keep an eye ope for this and remove them.
The grass around the array needs to be slashed down so that it does not overshadow the array (I have summer active grasses which include Setaria).
The electrical gear is generally maintenance free other than replace the HRC fuses if they blow and the surge arrestors if they change from green to red.
The pump is the only other component that needs maintenance and that depends on the advice of your supplier. Mine recommends:
- Replace seals every 5 years
- Replace impellers and bearings every 10 years
Step 26: Costs and Benefits
Costs
Attached to this step are breakdowns of the costs to construct and operate the solar pump system. The first document Project Construction costs outlines the cost for every element of the project. The complete installed system cost AUD$28,989. This is a very low cost for 10kW of solar providing power to a 2.2kW pump system. I used a lot of second hand materials and there is no charge on my labour, I estimate about 400 hours of my time in this system.
If I was to engage contractors and outsource everything then I would allow say $30,000 for the panels, groundmount, inverter and pump just for supply and delivery.
High pressure fencing would cost around the same at $5000.
There would still be around $2,500 in balance of system electrical equipment- eg cable, conduit, J Boxes, etc
Pipe fittings would be in the order of $1600
Installation labour would be around $15,000, bringing the project total to $54,100 prior to having a structure to install the pump in the dam or creek. A pontoon or solid jetty would likely add about $15,000, whereas a commercially built flying fox may be around $4,000. My system has both so total cost with pontoon and flying fox would then be $73,100.
So by doing it myself and using recycled materials I saved $44,111 or 60% of the cost of buying all new and paying others to do it for me.
Your system is likely to be a different size to mine, upscaling costs is not always reliable but we will go through the general principles to at least let you get an initial estimate.
Fencing- Generally as it is rectangular the perimeter length increases by 1.7 times each time the area doubles. The cost of fencing is driven by length. I used extremely heavy duty fencing, but it worked out about the same price as purchasing premade cattle panels. My price of $5386 for fencing supply plus say $2500 labour for 10kW of panel area is probably reasonable for supply and install of a standard duty commercial system. So for example cost to fence 40kW (2 area doublings 10kw-20kw-40kw) of panel would be 1.7x1.7x $7886= $22,790. There are significant savings if fencing is not required.
Spray Crete- This was very labour intensive given I have a very small render sprayer, for a larger system a contractor would be used. This would be about say $40/m2, the area doubles as the array area doubles so for example a 40kW array would be 60m2 x 4 x 55 = $9,600. Reasonable savings are possible here if it can be avoided.
Ground Mount- These have a fixed cost per panel of about $250 per panel including foundations and installation. So a 40kW installation comprising 160 panels would be around 160 x $250= $40,000
Solar Array- New panels qualify for REC's, assuming new panels currently allow $0.50/W for panels so a 40kW system would be 40,000 x $0.50 = $20,000 after RECs to supply. Installation of panels allow about $15 per panel for delivery and installation and if roof mounting about another $35 per panel for the roof mount rail system- delivered and installed. So installed costs for a 40kw System of 160 panels would be $22,400 + 160 x $15 = $24,800. If a roof mount system is instead of a ground mount then it would be an additional 160 x 35= $5600. This 40kW example is indicating the benefit of a high roof mount such as a shed- The savings are fence $22,790 + Spray Crete $9,600 + Ground Mount $40,000 = $72,390 for an additional cost of $5600 in roof mount rails. This would be around enough to purchase and erect a kit shed of suitable size (160 x 1.6= 256m2)
Pump, Electrical and Inverter- These components don't quite double in cost with capacity, typically like the fence they increase around 1.7 times per doubling of capacity so an 8.8kw pump system (good match for 40kW solar) would likely cost $9056 x 1.7 x 1.7= $26,172.
Pipe and fittings- There is a step change in these as I am using the largest of the Rural class B, to go up in size is a shift to metric and usually a heavier wall so the cost does double with capacity. So again in this example of 8.8kW pump and 40kw array the pipe cost would be around 2 x 2 x $1644 = $6576 supply and a rough estimate for installation in this case is to double the amount to allow for labour and machinery so 6576x 2= $13,152 fully installed.
Pontoon/Jetty- The cost of the pontoon would not change as it would be the same length and weight capacity, so say $15,000 for this structure pretty much regardless of pump size (up to a limit of what weight pump can be carried by hand).
So all up a 40kw array and 8.8kw pump system erected on either a ground mount or a new building with jetty to the dam would cost around $145,000 built entirely by contractors or just double the estimated contracted cost of my system but it is 4x the scale and capacity.
You can use the above as a guide to estimate the cost of a system of any reasonable farm scale you are contemplating constructing.
Operational Costs
The next 2 files in this step present operating costs with comparison with diesel pumping and electric mains pumping. These are based on my current system- the diesel pump being replaced by the solar pump and an equivalent mains powered pump that was my alternative to the solar pump.
While the energy for the solar pump is free, I have amortised (written off) the solar and electric capital costs at 5% and the diesel pump is written off over 10,000 hours as that is the assumed life when it will require complete replacement (It may need to be replaced well before this but I am allowing for good machine maintenance as per the manual).
I have used the actual cost that my system was of AUD$28,989 and will review the operational cost of a fully new contractor installed system a little later.
Solar has limited hours per year and it makes sense to operate it as much as possible, While I have a potential of 2200 operating hours cloud free (ignoring the shoulder period at reduced pressure and flow) I have allowed for 1883 hours per year this accounts for maintenance, inability to pump (eg stop irrigation order or extreme drought) and water not being needed.
The cost comparison of the 3 options are:
- Solar $1,793 per year
- Diesel $5,458 per year
- Mains Electric $5,359 per year
The solar works out about one third the cost of the alternatives. This is site specific, especially for mains electric. If my site had mains electric available where the pump needs to go then the mains electric annual cost would drop to around $4,000 per year or a bit over double to cost of the solar.
Allowing for full cost of my system using new parts and contract labour ($73,100) then the operating cost increases to $4000 per year, still cheaper than diesel and mains electric on my site, but comparable to installing a mains electric pump if power was available on site.
The return on solar is very dependent on operating hours. The last file attached is the same analysis but with just 500 hours of irrigation per year.
In this case solar is only marginally better than diesel, but is still better than mains electric on my site. However if I had to cover the full cost of installation ($73,100) then the annual solar cost would be $3653 and the system would definitely be uneconomic.
Cost/Benefit Summary
Solar pumping for irrigation only is currently not justified unless your irrigation needs are significant. Around 1000 hours per year of pumping is the breakeven point where solar may be economic if your project is completely outsourced.
If, like me, you are willing to scrimp and save and invest your own time in the project to halve the capital costs then 500 hours per year of irrigation makes solar economic. This is highly site specific though, for instance having power at the pumping location favours mains electric, having a large shed, but power a long way away favours solar.
Consider your natural advantages and challenges and use my pricing as a guide to help you make your decision.
The "X" factor in this project for me has been the ability to do something that was previously unimaginable- pump 12ML of water into my dam during high flow events. The total cost for this and 500 hours of irrigation per year is just $300 more than running my diesel pump for irrigation only.
It is not conceivable using diesel power to pump water to storage and then diesel to pump it out again. This double handling is definitely uneconomic, the more you use diesel, the more it costs. Solar however "changes the game" , the more you use it, the cheaper it becomes.
As a farmer it is hard to express the benefit of an extra 12ML of water stored each year. In the recent drought (2017-2020) my 25ML dam dropped from full to about 300mm water and 200mm of mud, getting close to unusable. I doubt I would have been able to pump 12ML every year through the drought but I would have been able to keep the dam full in 2017 and add perhaps 8ML in 2018 so by the end of 2019 it would have had more like 1 to 1.5m of water in it.
Having stored water is like having silage or hay in the shed. The solar pump just keeps putting water to storage, day after day improving my resistance to the next drought.
Step 27: Environmental Benefits
The solar pump is just a pleasure to have around and be around. The operation is so quiet that one can hardly hear it working. There is the faintest hum from the pump and the inverter. Both of which are inaudible from more than 10m away. This has completely removed a source of tension with neighbours as we no longer generate diesel pump noise pollution.
The silence is also good for wildlife, it has been shown in numerous studies that noise on creek lines and rivers disturbs aquatic life as well as native animals that hunt on or drink from the water, in particular the echo location of Bats.
Another major improvement has been that we have been able to rejuvenate the damage done to the creek bank back in the 1970's. The side was cut out to enable the installation of the diesel pump. This has been eroding badly as it is on the outside bend of the creek and also had a head cut draining the paddock above entering it. We have stabilised the headcut with boulders and started to repair the lost soil in the access ramp using timber pin retards. The photos in this step show before and after images.
The solar pump also reduces CO2 emissions- diesel consumption emits 2.64kg CO2/ litre so for my pump that is 2.6T CO2 per 1000 hours of operation. Even a mains electic pump has emissions based on the grid average which in Australia is about 0.8kg CO2/ kWh or around 2T CO2 per 1000 hours of pumping. These are small savings in my system, but increase as pump size and hours of operation increase.
Finally there is the benefit of not having the service and fuel the diesel pump. I look back through our incident register and there are a number of times that we have had a diesel or oil spill into the creek, for instance:
- Sight glass on fuel tank broke and diesel tank leaked out
- Slipped in mud while changing the oil and upended the dirty oil can
- Main diesel tank cap vibrated loose and secondary diesel tank overflowed through main tank
By eliminating the diesel pump we have eliminated the risk of polluting the creek as well as having saved ourselves the work of regulalry starting and stopping the pump, filling up diesel, servicing the engine, etc.
It is just so much easier having this silent worker, one that the more work it does, the less it costs. Working away not only to irrigate but to better secure our water supply in an envrionment that seems to be becoming more extreme. It brings a certain peace of mind.
Step 28: Field Day Invite
The creation of this Instructable has been made possible by the National Landcare Program: Agriculture Smart Farms Grants – an Australian Government initiative, who paid for its creation (I paid for the solar pump system). As part of this program a field day is being held once we are in safer times with COVID-19. This is expected to be on 19th August 2021 and held on my farm near Port Macquarie, NSW, Australia.
Coming to the field day will let you inspect the system I have built personally and ask questions that I will endeavour to answer. As you can see from the attached pic- a bit of cloud cover won't stop the irrigation, or the field day (a benefit of having 10kW of panels feeding just 2.78kW of demand).
If you are interested in this event, please contact Hastings Landcare:
office@hastingslandcare.org.au
I hope you can make use of this body of work and I look forward to meeting you.
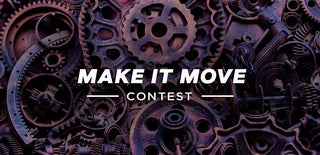
Participated in the
Make it Move Contest 2020