Introduction: Bye Bye French Doors
We purchased our first home in the fall of last year and I have been doing work on the garage since to convert it into my ideal workshop. The previous home owner had installed french doors in the side of the garage to provide an entry way into an office that was in the back half of the garage. Thankfully the dividing wall had been removed and the only things remaining of the previous office were the french doors and some old paneling on the walls. I already removed the paneling and replaced it with OSB which will be topped with a bead board plywood for a more finished and seamless look.
As I was removing the old paneling, I noticed some water and rot damage to the plywood surrounding the french doors. After tearing the inside down to the studs, I was able to inspect the french doors and it was clear that they were not installed well and the years of neglect meant they were close to falling apart. So I had to decide if I wanted to replace them with another set of doors or remove them completely. Removing them was the best choice. It gives me more security for my shop by removing an easy point of entry, and it gains me tons of storage space for my setup.
After discussing the options with my wife, we decided that I had the go ahead to start construction and that it should not be too hard to knock it out in a few weekends working a few hours here and there by myself.
Lets get started
Tools Used:
Pry Bar
Nail Puller
Hammer
Tape Measure
Utility Knife
Circular Saw with a special made siding blade
Air Compressor
Framing Nailer with galvanized nails
Finish Nailer
Level
Paint Supplies
Cordless Impact Driver
Cordless Hammer Drill with Masonry Bit
Ratchet with appropriate socket size
Jigsaw
Reciprocating Saw
Framing Square
Sharpie and Pencil
Materials Purchased:
Hardi Plank Siding to match existing siding
Galvanized Framing Nails
Screws
Circular Saw blade made for cutting Hardi Siding
Caulk
1 8 foot pressure treated 2x4
6 8 foot framing 2 x 4
Concrete Anchors
Pre-cut insulation
Tar Paper
Appropriate Nails for tar paper
Step 1: Remove the Old Doors
My first step was to inspect the outside trim pieces to determine the logical steps for removing the doors. I carefully removed a small piece of trim with my pry bar to test it and got a feel for how easy (or hard) it would be to remove the rest.
Next I removed the doors from the frame with my screw gun. This was easy to do with one person. I removed the top and bottom hinges first and left the middle hinge for last so the weight of the doors would not try to break the top or bottom hinge as the door started to fall away from the frame. After the doors were removed I noticed the door was only installed with 3 long screws through the hinges and into the frame of the door opening.
After removing all screws, I carefully removed the rest of the outside trim and with a few yanks of the pry bar, the whole frame peeled away in pieces. It was in worse condition than I thought. In about 15 minutes, I had the french doors completely removed. I would have had a second person on hand if I felt like the frame was more substantial and would be hard for me to handle it on my own. In my case, it practically fell apart so it was very easy to do by myself.
Step 2: Framing the Opening
My next step was to frame the opening for the new wall. I measured and cut the pressure treated 2 x 4 to go against the concrete. You want to use treated lumber because concrete wicks moisture so if the boards are not treated, they will soon rot with the damp conditions. I drilled several holes for concrete anchors and followed the instructions for installation. The process was simple, drill a pilot hole through the sill board the appropriate depth for the anchors, use a hammer to tap the anchors into the hole, and then use a ratchet with the correct size socket to tighten the sill board to the concrete.
I measured and marked the center lines on the top and bottom for my studs at 16 inches on center. This dimension is common for construction and matches the pre-cut insulation I purchased. I then measured and cut the studs to length and installed them with the aid of a level using my center marks as guides. A framing nailer made this process fast but it could be done with a simple hammer and nails too. I used galvanized nails as recommended to use with pressure treated lumber even though the only piece of pressure treated wood was the sill plate.
After the studs went up, I measured the opening and cut some OSB to close it off. I used a jig saw to cut the OSB since it had to be a weird shape to fit the opening. Some people use sheetrock, but I chose OSB because I plan on hanging things off the wall and want a wood product to screw into where studs are not located. I am installing a bead board plywood on top of the OSB for a cleaner look and to add more "wood" for a sturdy backing. The total thickness with the OSB and bead board plywood comes out to nearly 3/4" which should work nicely for my purposes.
Step 3: Time to Work on the Outside
Now comes the tricky part. I needed to remove the old siding around the door frame without damaging the siding I wanted to keep. This took a while to carefully pry the siding up just enough to loosen the nails so I could get a nail puller on them. Some nails were not visible to get the nail puller on so I had to pry just enough to get the blade of the reciprocating saw in order to cut the nails to remove the siding. Overall I was able to remove all the old siding pieces without any major damage to the pieces I wanted to keep!
The next step was to measure, cut, and hang the tar paper which is a moisture barrier to go under the siding for a water proof wall. I used 1" roofing nails specially made for tar paper for the installation. The heads of the nails are larger diameter to help hold the paper down without tearing it.
I called Dad to help me hang the new pieces of siding because they are 12 foot long and are flexible and nearly impossible to wrangle by yourself. Hardi plank siding is a concrete product so it is very resistant to rot, but is easy to break if too much stress is put on a single point. I purchased a saw blade to use with my circular saw that is recommended to use with Hardi products. It really cuts through the boards like butter. Normal carbide tipped blades will work, but this stuff is so abrasive that they were wear down quickly. I was able to find a blade for less than $20 so it did not break the bank.
The longest piece I needed was 143 7/8 inches so I was able to install them all with a single board because they come in 144 inch lengths!!!! I made it by 1/8" which was very lucky. It made for a seamless look. I was careful to orient the pattern of the wood grain texture so it matched the existing siding. Hardi is best applied with a framing nailer and galvanized nails. I did a few test shots to make sure the nail gun was set to shoot nails at the appropriate depth so it would not split the siding. The manufacturer recommends installing a thin strip of siding at the bottom on the sill plate and then installing full sheets starting from the bottom going up. The bottom thin strip is used to angle the bottom of the siding away from the wall to get the appropriate look and allow rain to roll off the bottom of the plank.
The installation is simple, measure, cut (I used a circular saw with a framing square to get square cuts), slide the old pieces into place, and nail to each stud. It is best to place your nails towards the top of the pieces so the piece above overlaps and hides the nails. Each piece of siding already has primer on it so all it takes is a coat or two of paint and it looks great.
Step 4: Time to Finish the Inside
Almost finished. Insulation is a breeze with the pre-cut pieces you can find at the hardware store. All I had to do was measure the length and use a straight edge and utility knife to cut to the appropriate length. I overlapped the paper tab strips and stapled them to the studs to keep everything in place when I put up the OSB panels that were cut earlier in the steps.
The final step was to install the bead board plywood with construction adhesive and brad nails. You can no longer tell that there was a door in the first place.
I am happy with how it turned out. The project was not difficult and could be done mostly with one person with the exception of the siding. I used a lot of power tools and specialty tools, but it could just as easily been done with simpler hand tools, it just might have taken longer. Opening up and patching walls seems very scary but if you plan it out ahead of time and have a good understanding of the steps, it is very manageable.
Hope this helps anyone on the fence about this kind of project. Thanks for reading.
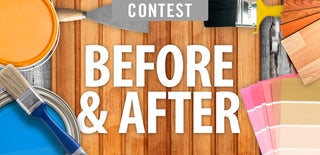
Participated in the
Before and After Contest 2016
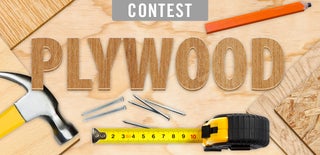
Participated in the
Plywood Contest