Introduction: CNC Leather Wallet
My trusty wallet has a lot of miles on it. It came as part of another wallet I bought years ago. I haven't been able to find another like it since.
I used my desktop CNC router to cut out leather panels. Then, I hand stitched it.
This is an entry in the CNC CONTEST. Hope to get your vote, Brent.
Step 1: Design on Fusion 360
This project is easily designed in Fusion 360.
I measured the dimensions of my wallet as I moved along the design process.
First I used my calipers to measure my old wallet's overall length and width. I also measured:
The card panels dimensions
The stitching offset
Distance per stitch
How deep of an arc to cut away in the card panels.
I started out in Fusion 360 by laying out boxes with the line tool.
Then, I used the 3 point arc tool to lay out the arc reveal.
I offset the box lines toward the inside to lay out the stitching.
I used copy and paste to lay out repeating circles for the stitching holes.
Once all the layout was done, I extruded the faces to match the thickness of the leather.
Finally, I exported the sketch as a .DXF, so I could run it through Carbide Create for my Shapeoko CNC.
Attachments
Step 2: Thin Out the Leather
This leather is 5/6 ounce from Tandy Leather. The finish is called "Kodiak". It's way too thick compared to my old wallet, so I had to thin it out. I improvised with my block plane and a parallel clamp.
I clamped down one edge of the leather and planed it down until I liked the thickness. I measured my progress by simply crumpling the leather within my fingers. How pliable the leather was showed me where I had to make more passes.
Make sure to start with a sharp blade on your block plane. Once one side was done, I flipped it around and did the other.
Step 3: Set Up Work Holding
I used a piece of poplar for my waste board. Since wood is often cupped or bowed, I did a leveling pass to flatten out the surface. Here I used a 1/4" end mill. The board itself was held down with screws on the outside edges.
Double sided carpet tape held the leather in place during the cutting process.
Step 4: CNC Your Leather
I placed the leather on the double stick tape, then pressed it down with a nylon roller.
I installed a 30 degree, 1/8" engraving bit (2 flute) and set the zero for the X, Y, and Z axis.
First, I cut out one long panel and two card panels. The second long panel was cut separate.
Step 5: Stitch Your Wallet
I used a simple back and forth stitch to bring everything together. All the holes were cut through the entire thickness of the leather. This made it easy to sew. It did help to push the needle through each hole on the front side to help locate the holes on the back side. I also started stitching at the corners to make sure everything lined up.
I am using 80lb sport fishing line for my thread. I melted the end of the thread so it would not pull out while I stitched.
Step 6: Burnish the Edges
I used candle wax to burnish the edges. First I applied melted wax to the edges with a paint brush. Then, I lightly went over it with a flame. This helped the leather absorb the wax.
I filed a notch in wooden dowel while it was in my mini lathe. I rubbed the edges against dowel to burnish everything.
Step 7: Stretch the Leather
To give the wallet its shape, I used blocks of oak cut to size. First, I soaked the leather in water. Then I placed one block into each card pocket. I flattened the wallet using the opposing force of the blocks. A clamp kept it in place while it dried to form.
I stamped it with an American flag for the finishing touch.
Step 8: Debut Your Wallet
This wallet turned out great. I'm sure it will last me for years to come. I was happy at how well it cut on my desktop CNC, and I'm excited to cut more leather.
Thanks for reading. Brent
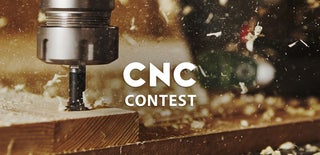
Runner Up in the
CNC Contest 2020