Introduction: CNC Puzzle
My middle-school students love doing projects with our CNC machine. We do many different projects where students design and engrave different parts of their projects. They love to engrave their names or pictures onto wood. But one of the more powerful uses of CNC technology is the ability to mass produce parts, or to accurately repeat processes, where many components can be reproduced exactly every time. Our small puzzle project demonstrates this concept.
Step 1: Create the Digital Image
The project starts as a digital image. I use ArtCAM software which is a powerful graphics program that allows us to use existing images, text, and pictures or to start from scratch and produce our own original artwork. The software creates the tool paths and the code that works with many CNC machines. Accuracy is very important at this stage. We use 3/8" Baltic Birch plywood for our puzzles, so the openings in each piece need to be machined just slightly larger than that, allowing for what I like to call a "sticky" fit. Ultimately, the parts should fit together with a little friction, even after some light hand sanding.
Step 2: Harness the Power of Software!
Once we've made sure that our design works (especially the tolerances) for one puzzle, the design can be copied and pasted any number of times. Our CNC machine allows for a working area of 20" X 24" so we produce a digital image that matches the size of the piece of Baltic Birch that we will use. On one piece we produce 12 complete puzzles (36 pieces in total).
Step 3: Create Toolpaths and Code
Once our design is complete, we create the toolpaths and code that works with our CNC machine. Our software allows us to machine each piece accurately with a 3mm End Mill. Some of the vectors (the digital lines) are machined outside the vectors while others are machined inside the vectors. Our software also allows for tabs to be created around the perimeter of each shape, so that during machining, pieces aren't completely separated from the main piece of plywood, the tabs are small enough to hold pieces in place, yet thin enough to snap easily once all the machining is complete.
Step 4: Machine the Project
With a 3mm End Mill chucked up in our spindle, we machine the project. This is the part where kids are mesmerized by the humming and the up/down, side-to-side movements of the CNC machine. We secure the Baltic Birch on a sacrificial piece of plywood using screws. The depth of cut was previously set to just slightly more than 3/8", so eventually, the sacrificial board gets chewed up and needs to be replaced.
Step 5: Finishing and Assembly
Once the machining is complete (our project takes just under an hour to machine), the pieces can be snapped off and worked on. Once they have been sanded and splinters and sharp edges have been removed, students can attempt to solve it!
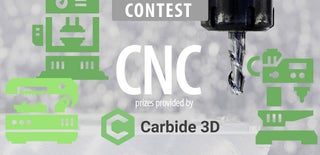
Participated in the
CNC Contest 2016