Introduction: COAT STAND With Kreg R3 Pocket Hole Jig
Don't you just hate it...your kids come in and dump their school stuff on the floor!
Over the summer holiday, I helped my son make a cool coat stand to hang up their coats and rucksacks, just in time for starting back to school..
I was also super keen to use my prize from the Outdoors Structures Contest of a fantastic Kreg R3 pocket hole jig...
...big big thanks for all of you who voted for my Bike Shed project
Step 1: We Want It to Be Cool!
The idea was to make a coat stand that doesn't look like a coat stand!
It has to look good in the day when the kids are at school and it is devoid of stuff.
And it has to be a super simple project for my son to make.
The idea we came up with is to have four poles sticking up from a heavy base board to allow the coat stand to be self supporting...
...the coats and bike helmets can hang on the poles...
...the rucksacks can sit on the base board.
To give the design a little more interest we would set the poles at differing angles to give it a more sculptural feel...
...and I wanted to use my new Kreg jig...though not in the usual way!
Step 2: Get the Bits Together!
MATERIALS
1600mm x 38x220mm softwood boards - this makes a base board of finished size 430x750mm
2no. 20mm x 2400mm long pine dowel - cut in half to make four 1200mm coat poles
1no. 9mm x 2400mm long pine dowel - to cut up to stitch the boards together
PVA wood glue
Some abrasive paper
TOOLS
20mm auger bit
Drill/cordless
Sander of choice - we used a belt sander
Thicknesser helps if the boards require dimensioning
General wood working tools
Step 3: Prepare the Timber
First prepare the base board.
We required it to be approx 430mm wide and 750mm long to fit the space we have.
The board needs to be heavy to self support the coat stand when loaded up with coats.
I had some unused rough sawn scaffold boards from my current project 'The Scaffold Board Shed' in the workshop...perfect.
The timber was 1600mm in length and so only needed to be cut in half.
We then put it through the thicknesser to plane them flat as they were slightly cupped.
By hand we trued up an edge on both boards to make a nice tight joint.
This could have been done on the planner as easily though there is nothing better than learning to use hand tools.
Step 4: Stitch It Together
I came up with this idea of using the Kreg pocket hole jig to stitch the boards together.
Clamp the Kreg jig to one of the boards planed edges and drill a pocket right through to the edge.
We did another three along this board.
Mark off on the opposing board in-between the holes and drill some more pocket holes.
We also turned the boards over and added some to the underneath for added strength.
Normal methods for jointing boards will work with a glued in tongue, biscuit joints, dowels or even a plain glue joint, check out Popular Mechanics Instructable for some of these methods
Step 5: Use Some Sticky Stuff
Glue up the meeting edges with PVA wood glue...
...and cramp tightly together.
Take the auger from the Kreg R3 jig kit and drill all the pocket holes deeper into the opposing board.
Cut some lengths of the 9mm dowel and glue them into the pocket holes, use a small hammer to knock them fully home.
Leave to dry.
When fully dried remove the cramps and cut off the protruding dowels flush with the board.
Its all stitched together and I really like the elongated dowel ends that add an interest to the surface of the base board.
Step 6: Shake + Sand
When cutting the ends of the base board to length a shake opened up...[shake - a split within timber]
...the Kregs jig came to the rescue!
As the shake was within the width of the board we needed to remove the plastic side tabs of the Kreg jig.
The process was the same as before...
...clamp the jig in position, drill a pocket hole, repeat a couple more times, remove the jig and drill a bit deeper with the auger, cut dowel,cramp tight across the board, glue in dowels and cut off flush...we were also able to squirt a little glue into the shake.
Sand the faces of the base board flat, we used a belt sander, ideal for this wide board though an orbital sander would work well.
Give the edges a sand and finish off the arris's [corners] by hand to give it a nice tactile finish.
Step 7: Mega Pocket Hole Jig!
Now for the coat poles.
These are made from 20mm pine dowel and we needed some pocket holes drilled into the base board to hold them in position.
Even though the Kreg jig has been fantastic up to this point, this would need something bigger...
...we need to make a MEGA pocket hole jig!
We wanted the poles to be angled towards the front of the stand and to have two differing angles to add interest to the stand.
For accuracy a big jig needed to be made.
Take an off cut of scaffold board timber.
Mark in the distance that the poles would be from the edge of the base board, we chose 75mm, and mark a pencil line.
Using a sliding bevel and the coat dowels work out the angles required.
Mark the two differing angles, one on each end of the block. Make sure it is angled in the correct direction, to point towards the front of the stand.
Extend the lines to the top of the block.
With the 20mm auger drill through the block at the desired position and angle.
Divide the base board length by the amount of poles required marking with a pencil tick.
Line the mega jig up with the first position and clamp in place.
We wanted stopped pocket holes and so worked out the depth needed and marked this on the auger with some tape.
Drill the pocket hole to the marked depth.
Move the jig up to the next mark, remembering to use the second angled hole.
Continue with the further holes.
Step 8: Coat Poles
Cut the 20mm dowel in half.
Sand one end to a nice rounded shape, give each pole a quick rub down with abrasive paper if needed.
Glue the dowels into the pocket holes.
That is it...all done.
Step 9: All Done
This is really a very simple wood working project that makes for a really funky object that not only works well, but also...
...looks cool...
...and was great to make with my son.
This project was inspired by the Kreg jig and I am impressed with it...
...really well made and cuts accurately...
...that is exactly what is needed in a quality tool.
Big thanks for all who enabled me to win it...
...Instructables...
...Kreg...
...and all of the Instructable members who voted for my bike wardrobe.
If you like this project then I would really appreciate your vote in the Wood Competition. Thanks.
This project is part of my YouTube series where I try to make cool and interesting projects.
Please check out my channel if you want to see more of the projects, if not there will be more coming to Instructables soon.
Why not check out what I am up to with pricklysauce.com
And also catch me on Facebook + Twitter
Just started on Instagram!
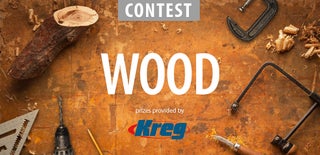
Participated in the
Wood Contest 2016